- Case Studies
- Posted
End result
In light of the current economic conditions, an increasing number of Irish people are turning away from buying new homes, instead deciding to make the most of what they’ve got by extending and refurbishing. Lenny Antonelli visited one such house nearing completion in Glasnevin that uses a combination of materials and techniques to aim for highly sustainable results
Gerard and Ellen Menezes had little choice but to renovate the end-of-terrace Glasnevin home they bought in 2003. “For our first winter here we had all single-glazed aluminium windows and there was no insulation at all,” Ellen Menezes says. “You could see your breath it was so cold. We’d have the heating going full belt, and our bills were huge.”
Space was also an issue for the Menezes’s and their two young children. “The house came with planning permission to extend and we wouldn’t have bought it otherwise. It’s not that big, it was only 78 square metres.”
The couple are nearing completion of a refurb and extension that has boosted the building energy rating (BER) of the house from a D2 to B1. They received three offers for the upgrade, with the mid-priced and winning tender coming from green builders Viking House, who insulated the house externally and added a 65 square metre closed-panel timber frame extension. Viking House’s Seamus O’Loughlin is keen to stress that green extensions needn’t be prohibitively expensive. “For the price of a normal extension, you can get a factory-built passive extension, lifted over with a crane, that can be finished in a few weeks,” he says.
Other bidders offered more conventional upgrades, but for Ellen Menezes the intention was always to go green. “That was always the plan,” she says. “It’s just what’s important to us. My sister is a sustainable architect. (My interest) probably comes from as far back as when my father did building, and we got to see some of the building materials and how they perform.”
Having previously dry-lined parts of their sitting room and kitchen, the Menezes’s had witnessed builders struggle with green building materials. “When we got the Homatherm (a wood-fibre insulation product from Ecological Building Systems) before, our previous builder looked at us and presumed it must have been for the attic. But we said no, it’s for the walls. He hadn’t worked with the materials. So this time we said we wanted to work with somebody who knew how to use them.”
Limerick-based insulation specialists Aerobord supplied the 100mm of expanded polystyrene (EPS) insulation added externally to the front and back of the house, originally built from pre-cast concrete. “We used polystyrene because the walls weren’t breathable anyway,” O’Loughlin says. Ellen Menezes admits she wasn’t aware of external insulation before Viking House recommended it. “When Seamus mentioned that we could clad on the outside, it seemed like a brilliant option because the house is so small.”
Externally, the EPS 100 was finished with a fibreglass-reinforced cementitious plaster from Weber. The refurbished walls were brought up to a U-value of 0.22 W/m2K. An air gap between the polystyrene insulation and original wall allows moisture to dry out. “It allows any moisture that's built up to be redistributed to areas which are drier. If there's a damp patch it'll spread it over a big surface area,” O'Loughlin says. The old attic was insulated with cellulose to an average depth of about 400mm, boosting the U-value from 0.35W/m2K to 0.2W/m2K.
Viking House installed a new boiler too – a 90 per cent efficient Ravenheat modulating condensing gas combination boiler. Unlike conventional boilers, combination boilers heat water on demand, so they don’t need storage tanks and consume less energy, though they sometimes have a lower flow rate. Underfloor heating is installed downstairs in the new extension and in the new ensuite upstairs, while radiators heat the original house.
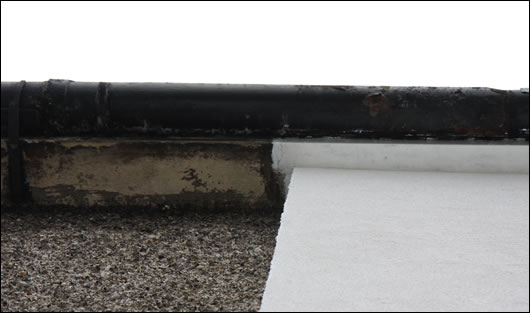
100mm of expanded polystyrene (EPS) insulation was installed externally on the front and back of the end-of-terrace house, giving the refurbished walls a U-value of 0.22 W/m2K. The EPS was finished externally with a fibreglass-reinforced cementitious render from Weber
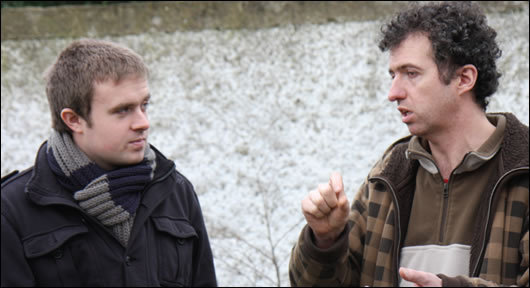
Construct Ireland journalist Lenny Antonelli (left) speaks to Viking House’s Seamus O’Loughlin (right) on site in Glasnevin
In partnership with Viking House, MBC Timberframe manufacture the closed-panel timber frame system used for the Menezes extension in Cahir, County Tipperary. From the inside out, the wall build up includes 13mm of Fermacell, a 70mm service cavity insulated with blown cellulose, OSB board (taped for air-tightness), 150mm timber studding with more cellulose insulation, 80mm of wood-fibre board, and a breathable mineral plaster supported by fibreglass mesh. It boasts a U-value of 0.13W/m2K. Electrical conduits, windows and doors are all fitted in the factory, and the house arrives ready for painting.
The roof of the extension has a similar build-up: 100mm of wood-fibre board on the outside, OSB on the inside and 250mm of cellulose in between, resulting in a U-value of 0.12W/m2K.
O'Loughlin stresses that various factors effect the performance of insulation. “Heat is lost through insulation in three ways – through conductivity, which is measured by the lambda value of the insulation, through the insulation density, which is the amount of heat stored within the insulation to be given back to the house later, and through decrement delay, or phase delay, which is the ability of dense insulation to slow down heat loss and gain.”
O'Loughlin says Viking House's combination of wood fibreboard and cellulose offers a decrement delay of more than twelve hours. “This allows midday heat back into the building twelve or more hours later, and dramatically slows down heat loss. The dense insulation also acts as a buffer to balance out heat fluctuation,” he says.
O'Loughlin refers to study from Delft University of Technology in the Netherlands that examined two similar houses, each with a roof U-value of 0.21W/m2K – one insulated with lightweight fibreglass and the other with denser cellulose. Both were oriented to the south and remained unheated during the study period, throughout which outdoor temperatures fluctuated by 25oC. While the temperature in the fibreglass-insulated house varied by 13oC, it fluctuated by just 3oC in the cellulose-insulated house. When the temperature outside dropped to 10oC, the inside of the fiberglass-insulated house measured 14oC, yet it was 18oC inside the cellulose-insulated house.
“So the dense insulation kept the house four degrees warmer than the lightweight insulation with a similar U-value,” O'Loughlin says. “If you wanted to get the temperature fluctuation similar in both houses then all you would have to do is put a 50mm layer of wood fibreboard on top of the 200mm of fibreglass. Every 10mm of wood fibreboard gives you an hour extra of decrement delay.”
O'Loughlin offers an anecdote to illustrate the importance of dense insulation materials. “My friend stays in his log cabin in Sweden for a few weeks every winter. He heats the house with a log stove that tends to go out at about 2am. Often it gets as cold as minus 20-25oC at night, but the log cabin loses heat relatively slowly and it's typically 10-12oC inside the cabin in the morning, 15-20oC warmer than outside. First thing in the morning, he lights the stove again.”
O’Loughlin continues: “While he was telling me this story I was thinking of the winter nights I spent in a caravan in Ireland with a gas heater. The temperature inside the caravan would reach the external temperature of maybe 8-10oC in under an hour after the stove was put out, even though when you calculate it, the caravan has a better U-value.” He concludes: “In order to buffer temperature fluctuation materials need to be heavy and have a good U-value. Wood-fibre, poroton, aerated concrete blocks and timber are all good products for this.” O’Loughlin is keen to stress another advantage materials like timber and poroton have over concrete. “Because they have a good U-value, the heat doesn't transmit through the material, so the outer layer stays warm. If your wall is 15oC you'll need to heat the room to 25oC to feel comfortable, but if the wall surface is 19oC, you'll only need to heat the room to 20oC.”
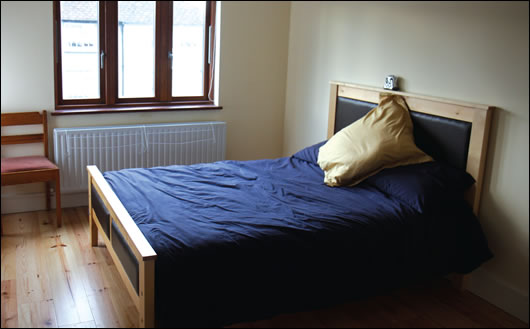
The closed-panel timber frame extension houses a new en suite bedroom upstairs
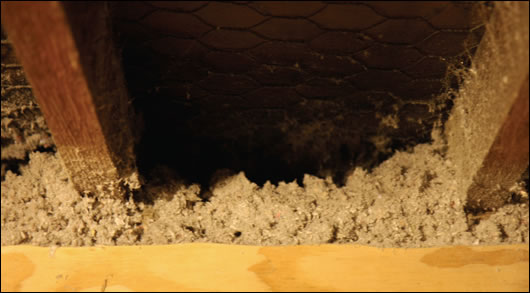
Cellulose insulation was installed in the original attic to an average depth of 400mm
The extension at Glasnevin also features Viking House’s patented foundation system, which includes three layers of EPS 100 insulation (300 mm altogether). O’Loughlin says the foundation needs less than a third of the concrete of conventional build, and requires just one pour. “The foundation system eliminates the cold bridge between the wall and the floor,” he says, referring to the cold bridge in most foundations where the walls cut through the floor insulation and meet the foundation.
The foundation system boasts a U-value of 0.107 W/m2K, and Viking House claim it reduces to 16 per cent the amount of heat lost to the ground from an underfloor heating system, as opposed to a figure of 65 per cent which Viking House claim is typical for conventional Irish build.
Rationel Vinduer Ltd supplied the extension’s double-glazed windows – the same units installed in the original house prior to Viking House coming on site. O’Loughlin would have preferred triple glazing in the extension, but the Menezes’s were keen for it to retain the same look as the rest of the house.
A blower door test in the extension produced a result of 0.75 air changes per hour (ACH) – slightly short of the 0.6ACH passive house standard. “We just built it the way we always do, and we were expecting a good result,” O’Loughlin says. “We put the OSB board on the inside and taped all the joints with Siga tapes, and taped up the inside of the roof. When you do that, it’s easy to get close to passive air-tightness levels.”
The original blower door test produced a result of 0.9ACH. “There was some taping done at the floor junction and some services were taped up after that,” says Archie O’Donnell of Integrated Energy, who tested the house. Integrated Energy offer a range of low energy and passive planning & design services. “We want to get down to 0.6 and we’re confident we can do that.” The older part of the building scored 1.8ACH, and further sealing work is planned there.
O’Donnell also tested the house using the Passive House Planning Package (PHPP) software. Even when not building to passive standards, O’Donnell sees PHPP as a useful design tool. “It’s an excellent package to use as a designer. It doesn’t cost you a penny extra to turn your house towards the sun, and to open up the southern windows,” he says. “It can be more useful as a design tool because of how it deals with issues like shading from trees and neighbouring buildings. And it’s much more detailed in terms of windows and window frames. If you’re looking for a low energy building it’s the tool to use.”
O’Donnell says he gets regular enquiries from self-builders with planning permission who are keen to go passive, but stresses that it’s more expensive to reach the passive standard if it wasn’t planned in the original design. “It’s very expensive and difficult to bolt on solutions.”
O’Donnell wonders if a separate passive standard should be introduced for the upgrade of existing buildings. “It really seems that to get an existing building down to passive house levels, you’d almost be as well to take it down and build again. There are some areas where you just won’t be able to get rid of the cold bridges.”
O’Donnell calculated the BER for the upgraded house as a B1 – 95 kWh/m2/yr specifically, and a vast improvement on the D2 (290 kWh/m2/yr) he estimates the original house as having. He stresses, however, that a difficulty in finding relevant information meant various assumptions had to be made about the house prior to upgrade.
While the results are clearly impressive, further work is planned that should get the house up to an A3. As Construct Ireland went to press, Viking House was set to install 15 square metres of solar panels on the south-facing roof of the extension with an accompanying 6,000 litre buffer tank in the garden. Why such a massive system? To satisfy most of the house’s hot water and space heating demand. O’Loughlin reckons that by combining an oversized array of evacuated tubes with a new low-temperature underfloor heating system in the old part of the house, he can significantly reduce the Menezes’ reliance on gas.
O’Loughlin will also install breathing windows – a type of local heat recovery ventilation (HRV) unit – in the kitchen and bathroom. The breathing window needs no air ducts, and features two fans that draw fresh air into the house while expelling stale air. The separated air streams are then guided through a heat exchanger and discharged (the stale air to the outside, the fresh air to the inside). The unit automatically switches on when CO2 or water vapour reach more than 500 parts per million. “It can even be washed in a dishwasher,” O’Loughlin says.
The internal kitchen wall that adjoins the neighbouring house – a major point of cold bridging – will be dry lined with 80mm of wood-fibre board, and the original doors will also be replaced with passive-standard German doors. “It would be silly not to do it (get new doors) because we’ve got a well insulated house and then this corridor of wind coming through the door,” Ellen Menezes says. 300mm of polystyrene insulation will also be added under the floor of the old house.
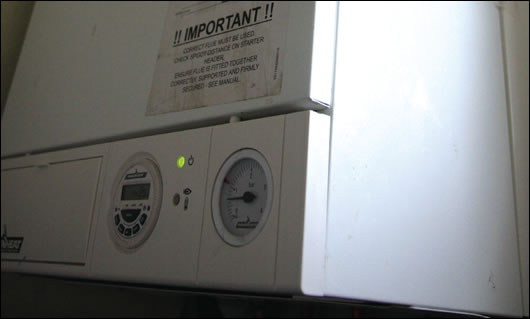
A 90 per cent efficient Ravenheat modulating condensing gas combi boiler was also installed
Seamus O’Loughlin expects the planned improvements to get the house comfortably into the A3 bracket, but Ellen Menezes is nonetheless happy as things stand. “The house is never chilly any more,” she says. “It’s comfortable all the time. My mum used to hate coming up here because it’s such a cold house. But after she saw the renovation she went back home and straight away found out about getting cavity wall insulation. She got the pearl beads done right away, and it’s made a difference in her house too.”
Selected project details
Clients: Gerard and Ellen Menezes
Main contractor: Viking House
Timber frame: MBC
Energy consultancy: Integrated Energy
External insulation: Aerobord
External render: Weber
Windows: Rationel
Air-tightness products: Siga
Combi boiler: Ravenheat
- Articles
- Case Studies
- End result
- refurbish
- renovation
- extension
- fermacell
- viking house
- breathing windows
Related items
-
It's a lovely house to live in now
-
How to scale up energy renovation
-
Woodland wonder
-
Holy Trinity
-
The stunning low energy seaside home that's built from clay
-
Mayo passive house makes you forget the weather
-
World class passive social housing
-
Life in an air-heated passive house - Five years on
-
Affordable homes scheme reflects rise of Norwich as a passive hub
-
Larch-clad passive house inspired by a venn diagram.
-
389 sqm home, €200 measured annual heating
-
SuperHomes retrofit scheme opens for 2017