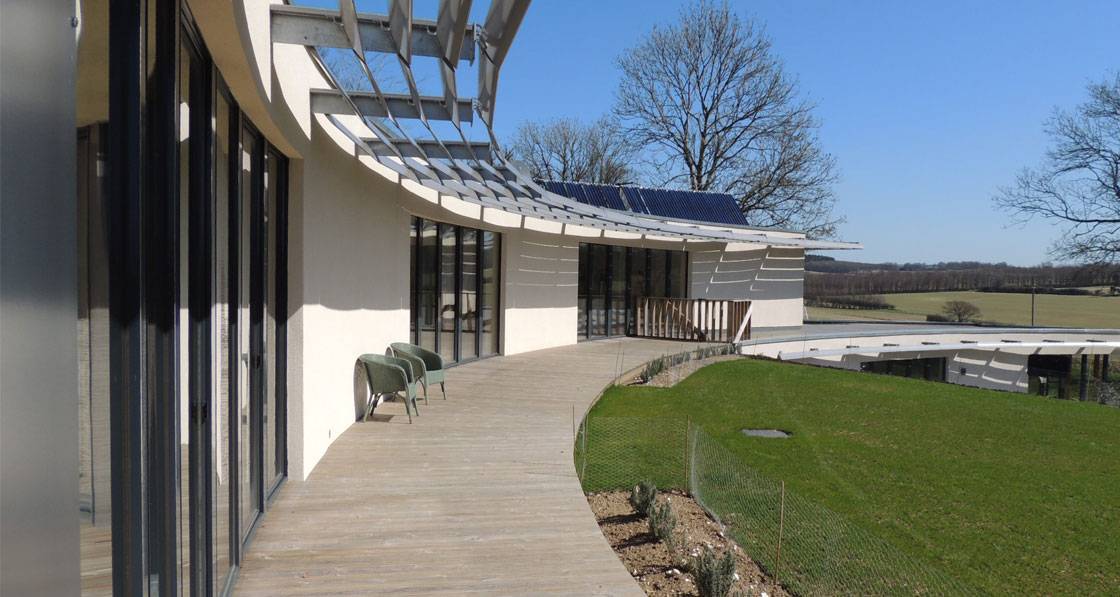
- Guides
- Posted
The PH+ guide to insulating concrete formwork
As demand for super-insulated and airtight building structures grows, insulating concrete formwork (ICF) is rapidly gaining popularity as a method of construction. But what exactly is ICF, what are its key advantages, and why is it so well suited to passive house and low energy construction?
This article was originally published in issue 25 of Passive House Plus magazine. Want immediate access to all back issues and exclusive extra content? Click here to subscribe for as little as €10, or click here to receive the next issue free of charge
Insulated concrete formwork is a method of building construction using lightweight and hollow insulation forms that fit together and are then filled with concrete. Once set, the concrete becomes a high-strength structure and the formwork remains in place as thermal insulation.
It’s actually been around since the 1970s in some countries, but in the intervening decades it has largely remained a niche choice, perhaps suffering from conservative tendencies in a sector reluctant to move away from traditional cavity wall construction, and from regulations which have placed little emphasis on superinsulation, airtightness and thermal bridging. ICF has tended to be the preserve of customers who want a high-quality construction with low running costs and aren’t just thinking about building as cheaply as possible.
But, of course, thanks to the demand for greater new-build energy efficiency, ICF has come much more into focus within the construction industry in recent years, including in the passive house sector. This is because by definition it offers excellent insulation and airtightness performance. There are several suppliers now established in Ireland and the UK.
Pros
ICF is certainly finding its advocates among energy-conscious architects and designers thanks to certain advantages that enhance its thermal performance, including inherent airtightness, the virtual elimination of thermal bridging and the fact that its advertised U-values are reliably achieved. There’s a simple logic behind this: when the insulation is serving as formwork for a concrete pour, the insulation has to be unbroken, or the formwork simply won’t hold the concrete. But it’s not just the presence of the insulation: it’s the fact that the concrete sets in direct contact with the insulation, and therefore delivers both airtightness and prevents thermal looping from undermining insulation performance.
Insulating concrete formwork involves a structural shell of insulation, usually polystyrene, into which concrete is then poured. Seen here are systems from Econekt (left) and Integraspec (right) under construction.
The significance of this can’t be overstated.
Studies have shown that gaps in insulation can dramatically undermine U-values. Insulation testing of a cavity wall with 50mm of XPS insulation in the cavity – with a 10mm gap to the inner leaf and 40mm gap to the outer leaf – showed that a 3mm gap between the insulation boards increased the U-value from 0.34 to 0.54 W/m2K, whereas a 10mm gap increased it to 0.65 W/m2K, as the thermal performance was undermined by natural convection.
In contacting most of the ICF suppliers in the Irish and UK markets for this article, it became quickly apparent that most companies were able to reel off projects showing remarkably low heating costs, even in some instances in spite of relatively modest U-values — as the mini case studies alongside this guide demonstrate.
Thermal bridging guru Andrew Lundberg of Passivate says that passive house designers are generally agnostic when it comes to construction types because the focus is primarily on energy conservation, but says that ICF performs particularly well for passive house applications because insulation continuity is guaranteed at all standard junctions, and at good thicknesses.
“Some system suppliers have also taken the positive step in having catalogues of standard details and related psi values and fRsi values developed for their systems as part of their Agrément cert applications, and that offers them currently a unique or rarely seen selling point, as well as demonstrating the performance of their systems and removing any guesswork. That also saves significant cost for people looking to build with those systems.”
Skills
ICF is a very different method from traditional masonry construction, with some saying the skill set required is more akin to carpentry than blocklaying. There may not be many experienced ICF builders around, but it may be inevitable that more builders incorporate the method into their skillsets given the combination of quick build speed and high performance it offers, in a market where energy performance standards are rising exponentially.
While the UK market has been served by an Insulation Concrete Formwork Association since 1992, in Ireland it’s another matter. The Irish Concrete Federation is in the throes of setting up a separate body within its organisation to better represent the views of the burgeoning ICF industry in Ireland, and to promote standards as well as selling its benefits. Part of this plan will include devising training and upskilling programmes for its members, according to its CEO, Gerry Farrell.
Raw materials
While ICF certainly has its advocates, others may baulk at the fact that it typically comprises two materials which can have comparatively high environmental impacts: ready-mixed concrete and polystyrene. Both materials have relatively high embodied carbon emissions, although the question of how green ICF is may need to be based on a systematic sustainability assessment of the whole construction.
Such an assessment could determine the embodied CO2 of a material, among other parameters, including a full life cycle analysis.
In its favour, ICF starts with the advantage of comprising fewer materials than other construction types, and there are various suppliers of both concrete and EPS who are manufacturing using recycled materials, including GGBS (ground granulated blast-furnace slag), a low carbon “green” cement derived from recycled steel industry waste.
Then there’s recyclability. The materials typically used to manufacture ICF – EPS, concrete, plastic ties and steel rebar – typically lend themselves to recycling once the building reaches its end of life, which was a significant factor in Irish firm Amvic Ireland gaining a BRE Green Guide rating of A+ on its system.
It’s also important to compare like with like.
While an ICF wall contains a relatively large amount of (typically polystyrene) insulation, a fair comparison would have to include other wall types achieving the same performance – which in terms of traditional construction, for instance, would involve similar quantities of insulation, plus thermal breaks and the materials to construct inner and outer leafs.
ICF systems under construction from (left to right) Amvic, Logix and Polarwall.
The vast majority of construction projects use significant elements of synthetic insulations which are oil-based or derivatives. Velox is one ICF manufacturer that normally eschews EPS in favour of a structural wood/ cement, but also offers versions with EPS or platimum EPS.
Polarwall uses exclusively XPS (extruded polystyrene), which it says has a better thermal performance than EPS and therefore reduces the overall wall thickness, helping to increase the internal living area.
North American manufacturer Nudura’s system offers credits under the USGBC’s LEED environmental rating system, scoring highly for energy performance, while also offering credits for its use of 100% recycled polypropylene and steel folding webs, which the company says enables the cavity in the formwork to be closed during transportation, enabling up to 40% more material to be transported.
Ultimately, if your main sustainability focus is energy consumption in use, then there is a wide range of construction types, including ICF, that would be perfectly suitable for low-energy, nZEB and passive house projects.
“If your main concern is sustainability, embodied energy and CO2, then you’re into a much narrower range of product which unfortunately comes at a price premium that the mass market aren’t currently interested in paying,” says Lundberg.
Compatibility
In terms of the compatibility of ICF construction with a variety of other building methods, a number of suppliers we spoke to say that there are no issues with using ICF in combination with strip or other insulated foundations.
“ICF works perfectly with any foundation system – be it strip, concrete raft or insulated raft, they provide no problems. Even in basements there is no problem as long as the tanking of raft and walls are properly addressed,” says Dony Kelly of Thermohouse.
ICF is also proving a solid option for hybrid constructions where it forms the basis for the ground floor – or basement – with a different structure on the top, such as timber frame. But it can also be used for buildings that go as high as 20 storeys, although some systems may have lower limits depending on a variety of factors.
Fire
Concrete is among the best performing materials in the event of fire, meaning the concrete structure of ICF lends the system inherent fire safety advantages. ICF systems typically offer between two and four hours of fire resistance, with greater resistance achieved by walls with wider concrete cores.
Meanwhile manufacturers point out that the insulation used in ICF is manufactured with flame retardant additives. ICF is also typically finished with cementitious renders externally – though a broad range of finishes are possible, including brick and stone slips from specialist suppliers such as Monolith, and rainscreen cladding – and plasterboard internally.
It’s understood that some multi-storey ICF constructions on the continent have been built with no firebreaks. Although this may raise some concerns for high rise applications given the scrutiny being applied to different construction approaches in response to the Grenfell tower disaster, the fire performance of an external insulation layer fully encased behind a cementitious render system can’t be compared to a ventilated rainscreen cladding system – let alone one with a polyethylene core.
It’s also reassuring to know that most suppliers will happily engineer firebreaks in, horizontally between each floor and vertically within the exterior insulation. Dony Kelly of Thermohouse says it is crucial that firebreaks must be in contact with the concrete core, so the EPS must be removed before the firebreak is installed. Velox, however, says that there is no need for separate firebreaks with its system because the formwork is made out of fire resistant material, but can fit them if required.
In terms of size, ICF walls range in thickness from 120mm (the absolute minimum permitted by the Eurocode standards) to 300mm. In a nutshell, a standard wall will typically be 150mm thick, but 200mm or more is better to combat the shear forces, building loadings and wind forces associated with taller buildings.
Speed of construction
One of the advantages of ICF over block-building and other methods – as long as experienced builders are involved – is the speed of construction. A typical house can be built at a rate of a single storey per week.
Velox’s benchmark is eight working days with three men to build a two-storey 42 sqm detached council house from slab to wall plate, all concreted.
Naturally, others say that speed depends on a number of factors. Serge Mellieur, who heads Canadian ICF supplier Polycrete, said: “Normally if you have a good working team and good planning, our construction system is faster than anything else, because we cover the structure and the insulation at the same time with the same team of workers. But never forget that quality of construction has to be your first goal before speed.”
There are no reported issues with interstitial condensation which, given the claims for ICF regarding the elimination of thermal bridging, is as it should be. The key factors here include good airtightness, mechanical ventilation, and having the correct balance of insulation so that the dew point is kept towards the outside of the structure.
(left) Velox’s unusual spin on ICF, in this case with additional platinum EPS insulation fixed to the structural wood/cement formwork; (middle) the Polycrete ICF system – in another example of ICF being used below ground level; (right) the Nudura ICF system going up like Lego.
ICF and thermal mass
Suppliers and advocates also point to the benefit of a long ‘decrement delay’ with ICF — i.e. that it can slow temperature changes by absorbing and releasing heat slowly — because its concrete core offers high thermal mass.
The benefit of having a high thermal mass is that it can moderate internal temperatures and delay the time at which peak temperatures occur. In practical terms, the theory goes that this means that the building should have lower winter heating requirements, along with a lower risk of overheating and less demand for air conditioning in summer.
However, there are still some grey areas in terms of the understanding of thermal mass in general, and in the thermal mass properties of systems such as ICF, with some research that ICF’s thermal mass is high, and some suggesting it is relatively low.
But even if the thermal mass of ICF is low, it may not be a bad thing. In low energy buildings, both thermally massive and lightweight structures can be prone to overheating. If too much heat is allowed to accumulate into thermally massive materials, they may simply take too long to cool down.
But the thermal mass effects of ICF – like many other construction methods – depends on its exact configuration, including what materials are used internally and externally. The local climate is another factor, too.
The conventional wisdom is that thermal mass needs to be exposed to have an impact, which is why the likes of exposed concrete slabs have long been a common feature as a passive cooling strategy in office buildings. This effect is undermined somewhat if you apply plaster or plasterboard, and possibly even more so if insulation is placed between the room and the wall’s concrete structure.
When it comes to ICF, you will typically have a mix of very high-density concrete with very low-density expanded polystyrene.
“When low heat capacity materials [like polystyrene] are exposed to heat sources, whether it’s solar gain or internal heat sources, you will get a relatively significant increase in temperature in those materials for relatively little heat input,” says Andy Lundberg of Passivate.
So from a cool state, an ICF home will have a relatively rapid response time to indoor heating, compared to exposed heavyweight structures. This also means that solar gain on the external facade can heat up the outer EPS layer quite significantly — but the effect of this on the internal environment is diluted by the heavy thermal mass of the concrete core.
In solid constructions without cavities this balance can be very important in maintaining comfortable environments, Lundberg says. But these effects can be significantly altered by internal liners, eg skimmed & painted plasterboard on a service cavity, and external render systems, which can feature dark absorbent colours or highly reflective finishes.
“We are now at a point where each project should be examined in isolation to ensure that the wall build-ups, including external and internal finishes, work for the specific building in its location and environment. We have the knowledge to do this, and not an excuse in sight not to.”
“However, once these inner and outer layers are covered by either external renders, or ventilated cladding systems, or have an internal service cavity installed or even just plasterboard fixed directly to the system, everything changes,” says Lundberg, adding that this is equally true for a cavity wall construction.
“So the key point is, there is no right or wrong when it comes to thermal mass and what’s exposed and what’s not. Every building is different and will perform differently.”
So figuring out the best solution for each project would require focusing not just on calculating heat losses using steady-state U-values and looking at the overheating risk if needed, but also at the best use of thermal mass effects – including decrement delay – in order to bring out the best in the materials. Lundberg says: “On some projects that may involve exposing thermal mass, and on others may require burying it behind lighter materials. It all depends on what the specific project needs. “It’s the next step in trying to model buildings more accurately for the as-built condition, but we’re just not there yet.”
ICF examples
Please click to read
Three year old passive house, Dunmore East, Co. Waterford
Sleek Tipperary home with promising monitoring result