- Design Approaches
- Posted
Dream factory
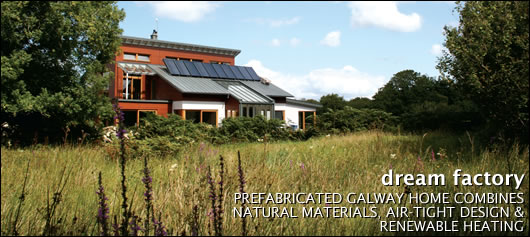
The rapid emergence of sustainable building in Ireland has been heavily influenced by the techniques of early-adopters extending from Scandinavia, to Canada, to Germany and Austria. John Hearne visited a recently completed timber home in Galway which uses Austrian know-how to couple air-tightness, high levels of insulation and healthy materials with a sustainable approach to heating and ventilation
One thing Josef Steiner is keen to emphasise is that his house in Na Forbacha in Galway is not a passive house. While he could, without much additional difficulty or expense, have adapted his design to passive house standards, to do so would, in his view, have been wasteful. Instead, he created a low energy home specifically adapted to his lifestyle.
“In designing the house, I looked at my whole life; as part of my business, I generate waste timber. I have waste timber for free as a by-product of what I do, so I burn it, I create energy. Everybody has to live according to their lifestyle, and it has to make sense energy wise.” So, though he could have designed out the kachelofen which acts as the house’s primary heat source, to do so would have been a major loss both to aesthetics and engineering. Common in central and eastern Europe, a kachelofen is a ceramic tiled woodstove which generates a low-intensity radiant heat. It lies at the heart of the house, at the junction between the three distinct living spaces, and overlooked by a mezzanine which is itself a secondary living room.
The sophisticated boiler at its centre is surrounded by a superstructure which acts as a large thermal store, from which the house draws heat long after the fires themselves have burned out. This is clad in tiles designed and fitted by ceramicist Ulrike Bernhard from attelier Bernhard und Mikula. Their fibrous detail, combined with the way the oven presents different faces to different living spaces, gives it an organic feel, as if it’s a living thing growing up through the house. Here too, there’s an elegant symbiosis between the engineering and the aesthetics. The water tank in the boiler house acts as a centralised thermal hub, fed by the oven and the roof mounted solar array. These combine through the control system to optimise water and space heating.
The building itself is a highly insulated, air-tight envelope, manufactured off-site and delivered from Austria on the back of a truck. Built in six days, and entirely complete in four months, the large south-facing window elements and overhead glazing enhance the passive solar energy gain, which is sustained by the heat recovery ventilation system, making the house extremely efficient to heat. Using the Passive House Planning Package (PHPP) methodology, total heating requirements come in at 28kWh/m2/a. “In Austria,” says Steiner, “we’d call it a three litre house. It would take just three litres of oil per square metre to heat it for the year.” Using a combination of waste timber from his business and wood pellets, he estimates that combined annual space heating and domestic hot water costs will come in at around e400.
The kachelofen, Steiner explains, is a custom-made, hybrid version of a technology that dates back thousands of years. “In Austria, old houses were built around this. The stove and the fireplace had a central function in the house…There were lots of variations, they had a fire here and then the gases would go up and heat a box on the first floor. The Romans used similar ideas; they used the heat stack effect inside a closed system to heat elements of the building. This is the same concept, except I used the most up-to-date technology available.”
Dried logs can be fed manually into the firebox, though the system has also been fitted with an automated pellet feed for greater versatility. It’s a closed system, Steiner explains, drawing an external air supply. “The whole thing is designed to take maximum energy out of the wood. By measuring the exhaust quality, it decides on how to supply the air into the fire chambers, plus it’s got a secondary firing as well. First the wood is gasified, then the gasses get burned again on a higher level.” There’s a high level of controllability built into the system. “If I say I want priority on water, it waits until the temperature in the stove goes up to 450 degrees. Up until that point, it brings the gasses through a series of closely packed, criss-crossing pipework underneath the ceramics…The heat will last until the evening, it will radiate all the way through the day.”
On hot water priority, once the temperature in the system reaches the desired level, water is sent through the heat exchanger – or back boiler – sited above the fire chamber, which is then piped to the centralised heat store. You can alternatively choose to send a proportion of the heat to the water and to retain a proportion within the oven.
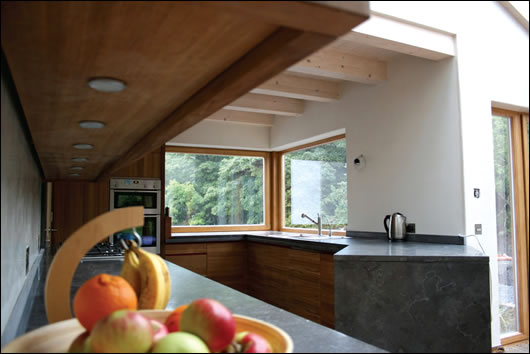
Open plan design and glazing bring natural light into the kitchen
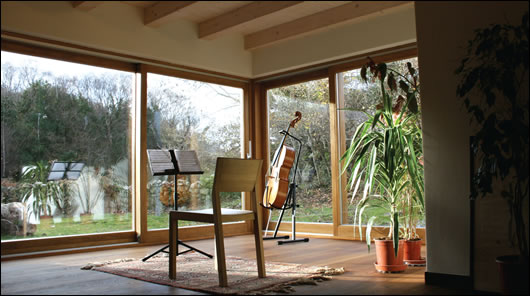
The music room faces south-west to maximise passive solar energy gain
The masonry mass which retains the heat is firebrick, overlaid with a thin (2mm) lime render. Lime is used extensively though the house – in fact the design team sought to ensure that natural materials were used throughout and that manmade fibres were kept to a minimum. The music room, at the house’s south western corner, lies directly behind the oven. The wall which backs onto the heat source is constructed from a fireclay called schamotte. “It’s got a high air content inside the granules,” says Steiner, “and it keeps the heat very well.”
The pellet module is housed in a unit in this room, drawing pellets through a vacuum system from a silo adjoining the western façade. “The system recognises which fuel is being used. It’s automated to pellets, so if I decide I want to switch to logs, even when the pellets are running, I just open the door and it recognises that logs are coming and it sets its processes to that.” Steiner’s company, Structural Timber Systems, built the house, and Steiner uses waste material such as off-cuts from batons from the onsite erection process to provide the fuel for his system. He stresses that all timber the company uses originates in sustainably managed forests.
Apart from underfloor heating in the bathroom and trench heaters sited at the base of some of the glazed elements, there’s no conventional heat distribution system in the house. “I’ve got the heat recovery ventilation, so the temperature created here gets evenly distributed and because the design of the house is open plan, the volume heats, then you leave the doors open in the bedrooms so they benefit. I put in floor channel radiators because the windows are the weakest link. In the cold spells, the heaters counteract the falling down-draft from the glass.”
The heat recovery ventilation (HRV) unit was provided by MTD Solutions Ltd. “It’s the MTD-ERV 350.” Mark Turner of the company explains. “It’s manufactured in Holland but was designed and developed here.” With a fan power of 0.67W/L, the system was designed specifically for Irish conditions. “A lot of the units out there,” says Turner, “they’re good, but the problem is they aren’t designed for the climate, the humidity and the cost of electricity over here.”
He maintains that units designed for, say, French conditions, where nuclear power makes electricity cheaper, have oversized motors that are costly to run, and which are heavily penalised in DEAP – the Irish software for calculating Building Energy Ratings – and can therefore wreck an otherwise healthy rating. Units designed for dry Scandinavian air conditions may be calibrated to reintroduce moisture to the structure to maintain the health of the timber elements. In Irish conditions, Steiner asserts that this facility can drive moisture to unacceptable levels within the house.
Noise – which can be an issue with mechanical ventilation – isn’t a problem here, according to Steiner. “I have it permanently on at the lowest setting.” he says. “You can do a rapid ventilation as well, but I don’t really need to use it. The air quality has been really good. It’s very good in terms of noise, you wouldn’t hear it, even lying in bed at night.”
MTD’s ducting apparently reduces noise by designing micro perforations into its internal core, thereby absorbing the noise-producing friction that typically occurs when air passes through a pipe. The fan itself won’t be heard at the lowest setting, but will at the high. “But there’s absolutely no need for it to be up high.” says Mark Turner. “If you set it at one, the lowest setting, that’s enough for it to do everything it needs to do. If you have steam in a bathroom, setting one will take a little longer to get rid of it than setting three. That’s all.”
There’s also an automatic summer bypass which kicks in when the external temperature rises above the internal temperature, while the F7 filters are fine enough to remove pollen, dust mites and even dust mite excreta from incoming air. The controls monitor temperature and humidity and how and when air is returned to the house. Incorporated at design stage, all pipe runs were pre-cut in the factory, streamlining onsite installation.
The system also includes a 2kW radiator to provide a temperature boost to incoming air if it’s needed. These have become a common add-on to HRV systems in low energy houses, but because they’re usually electrical, they can have a significant impact on heating costs and because of the inefficiency of Irish electricity generation and transmission, also on the energy rating. In Steiner’s house however, the radiator is plumbed, and when required, draws heat from that centralised buffer vessel.
Air-tightness is central to the effective operation of the HRV system. Structural Timber Systems’ highly insulated envelope achieves an astonishing 0.54m3/hr/m2 at 50Pa. “It’s a closed panel system that’s used in Austria.” says Steiner. “We put in all the windows, all the doors; whatever can be done in the factory is done in the factory, then we bring the full elements to site, and the only things done on site are the internal finishing and the external render.”
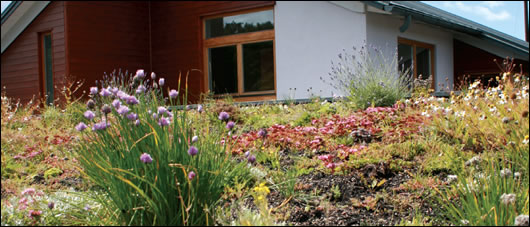
The master bedroom looks out onto this sedum roof which creates a visual link between the house and its surroundings
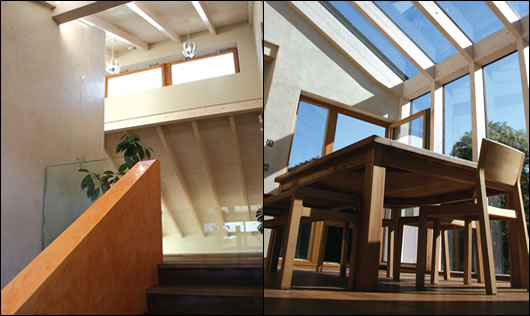
(left) glass balustrades help to make the most of light entering the house through clerestory windows; (right) the extensively glazed dining area adjacent to the kitchen
The super insulated wall components are composed as follows: inside to outside 12.5mm gypsum fibre board, 12mm OSB board as vapour control layer and for structural stiffness, 240mm timber framework, 240mm mineral wool as thermal insulation, 16mm DWD wood fibre board, Tyvek breathable membrane as second rain screen and air-tightness control and 30mm pressure treated timber battens to form a ventilated cavity. Externally, the house is finished with a silicon-based Sto render, while the aforementioned lime render is used throughout the internal surfaces. Altogether, the wall delivers a U-value of 0.16 W/m2K.
From bottom up, the floor is composed of exposed glue-laminated timber beams with a water-based white stain to stop darkening, 40mm engineered three-layer board in exposed quality (T&G) and the Fermacell Maxi floor system (40mm T&G Fermacell floor slabs on adjustable pedestals every 500mm centres). Those pedestals are 160mm high and the cavity is insulated with rockwool, while the floor finish is glued to Fermacell slabs. “The great advantage of the system,” says Steiner, “is that the ducts for the heat recovery system could be run freely between the pedestals and also, the system is completely dry. There was no time wasted waiting for wet screeds to dry.” The Maxi floor system was also used on top of the raft foundation on the ground floor. Taken together, this gives a floor U-value of 0.2 W/m2K.
From bottom to top, the roof components consist of 80/160 mm exposed glue-laminated timber beams at 800mm centres, 20mm engineered 3-layer board in exposed quality (T&G) with water-based white stain to stop darkening, 20mm service layer insulated with rockwool, 12mm OSB board, 260mm rafters, a cavity insulated with 260mm of Rockwool, 16mm DwD board, Tyvek breathable membrane, 50/60mm counter battens, 20mm rough sawn timber decking, underlay membrane for the metal roof and a patinated zinc roof finish with standing seams. The U-value in the roof is 0.15 W/m2K.
Runs for all circuitry and pipework are pre-planned and cut in the factory. Steiner asserts that the selection of timbers used for internal and external finishes – Framire in window sections, European larch in external cladding and oak throughout – all originate from sustainable sources. In the internal walls, two 12.5mm gypsum fibre boards sandwich 12mm of OSB board, the 100mm timber framework, 100mm of rock wool for sound insulation and another 12mm of OSB.
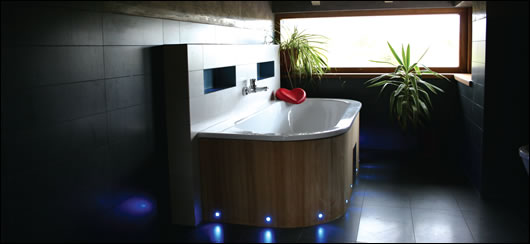
two rooms in one: LED lights transform the bathroom at night
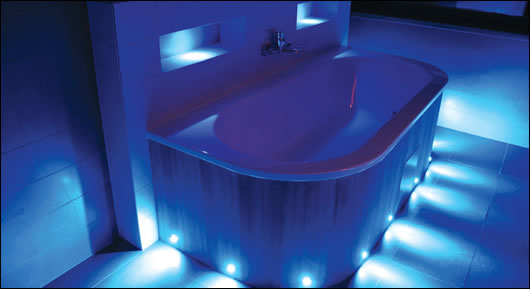

Trench heaters were sited at the base of some windows
The internal doors, pre-hung in the factory, incorporate draft stripping. “The construction of the house took six days.” says Steiner. “After six days, the crane left, and then there was probably another six days just to finish all the bits and pieces. When you join the panels you need to do certain completion works on site. You need to wrap the Tyvek, tape it and so on…That took another six days, and then after ten days, the first-fix plumbing and the roof racks and the external render started. After twenty-one days the superstructure was complete.”
Josef Steiner has been bringing these houses to Ireland for the past twelve years, and last year, his company Structural Timber Systems, in partnership with Factum GmbH in Austria and CLG Developments extended their business into public procurement. “The government went out to tender for a system-built, fast track building process for schools in rapidly growing areas, which we won, so we built one in Portlaoise and two in Gorey.”
Factory building brings a range of advantages, not least the high degree of planning it engenders. As a result, glitches, hitches and unforeseen problems don’t tend to occur “There’s a detailed drawing of each wall, so I know, I can define everything down to the last millimetre of every single wall, and every element that’s produced. I know where the studs are, where the boards meet. Everything.” The only issue that arose in Na Forbacha was when preparing the site, it was discovered that the ground was softer than had been thought, which led to a lot more preparation and quarry run than had been envisaged. Building costs worked out at e180 per square foot, giving a total project value of e600,000.
Steiner’s site itself is low lying, and well sheltered by forestation to the south, east and west. The trees are however sufficiently far from the house to allow extensive passive solar gains even during the winter months. Large glazed sections maximise these passive returns. “The idea,” says Steiner, “was basically to design a house using passive-house principals and technology. I could have gone for triple glazed windows but I didn’t because I felt that the extra investment wasn’t justified. I wanted a house where I could use the fire system that I had in mind, so triple glazing wasn’t really required, plus I just felt that the window profiles, they get so big and chunky, I would have lost on the aesthetic that I wanted to achieve. And the glass is the most efficient double glazed unit that was available at the time. The glass itself has a U-value of 0.9 W/m2K, and the whole unit is 1.1 W/m2K.”
The range of issues that typically arise with large glazed sections are very neatly dealt with here. Winter heat-losses are counteracted with the aforementioned trench heaters. These sections also incorporate no less than three patio type doors – a common feature of Irish homes, and a common weakness for draughts and fabric losses. The factory engineering however ensures a high level of draught sealing. Again, that air permeability rate came in at 0.54.
Nor is there a problem with summer overheating. During warmer months, ventilation and cooling happens through a passive stack system. In a fully automated system, the tilt and turn doors allow fresh air in, while the clerestory windows are opened to allow hot stale air to escape. When the temperature reaches a pre-set level, motorised windows open to vent the warm air. “It’s perfect, it’s fantastic, if you open the doors and windows downstairs, you can tilt them and you open the top, and immediately the temperature goes down.”
The patio doors themselves are not used during the winter, leaving all the ventilation to the HRV system, while the main entrances are enclosed by draft lobbies, and are both found on the north side of the building. Adjoining the main house, the separate office and artist’s studio lie along a north south axis, giving the office high-quality northern light and the studio, plenty of southern light. High level glazing in the house – both from those window sections in the living space and the clerestory windows – has the added advantage of providing increased levels of daylight into the building, reducing dependence on artificial light.
Partly for aesthetic reasons and partly to take advantage of is light-harvesting properties, Steiner faced extensive sections of the upper floor in ‘Spatula Stuhhi’, an Italian stucco product which combines marble dust and slaked lime with natural pigments to create a highly reflective marbled surface. LEDs on the stairs and in the bathrooms provide a low level ambient light which again, reduces the need for flicking switches. There was some compromise on general lighting. “It’s probably not as energy efficient as I’d like it to be. I’m waiting for the technology to catch up; at the moment you can’t get bulbs that are dimmable and low energy, but as soon as soon as they come on the market, I’ll get them.”
The master bedroom looks out on a sedum roof section, which, planted in April, was a riot of colour in November. This was a DIY job too. Most of the plants were harvested from the garden of his partner Ciara’s mother. “There were a lot of plants growing over the path, so we just transplanted them, then filled out the space with some additional plants that we bought, but very few. We didn’t spend e100 on plants.”
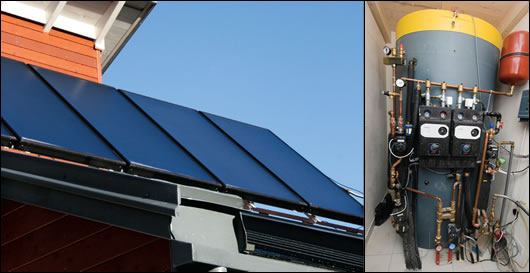
(left) The ten roof-mounted solar panels have been sited just above the main south-facing glazed sections and feed into a 1,500L buffer tank in the boiler room (right), which acts as the centralised heat store for the house
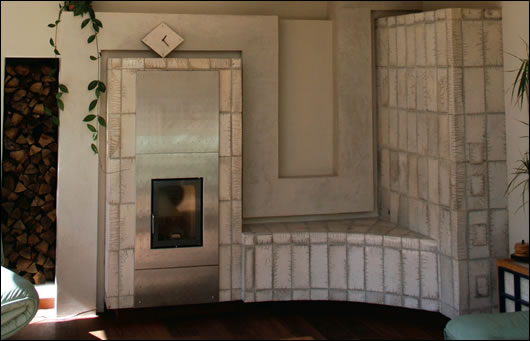
The kachelofen, which is common to central and eastern Europe, is a ceramic-tiled woodstove which generates a low-intensity radiant heat
Underneath, the build up begins with the waterproof EPDM membrane used on all flat roof sections, then a drainage mat. On top of that, there’s 30mm of gravel, a geotextile membrane, and the plants, which include a selection of taller herbs and flowers like lavender and thyme. The roof’s function, says Steiner, is purely aesthetic. “It’s to blend the building with the landscape, it binds the background to the building.” Though there are no water harvesting facilities in the house, low-flow taps and dual flush toilets reduce water consumption.
The lime render on internal surfaces leaves a much rougher, grainier finish than conventional renders. “I like the texture, I don’t like smooth finishes…I wanted to have it unpainted first but you could see the fibre board underneath, plus we didn’t want sand from the render falling down.” Instead, he used a Keim paint. Keim mineral paints are used extensively in restoration work, and were developed to reproduce the appearance of a lime fresco finish. It’s a liquid silicate paint which comprises a potassium silicate binder with inorganic fillers and natural earth oxide colour pigments. When applied onto a mineral substrate, the binder is absorbed and forms a micro-crystalline silicate structure. This crystalline structure allows the substrate to breathe.
Outside, the ten roof-mounted solar panels – fully 20m2 – have been sited just above the main south facing glazed sections. They were installed, along with much of the heating kit by Gerry Cunnane of Wind Water Solar Energy Systems Ltd. in Kerry. “They’re flat plate panels from IDM Energy Systems in Austria.” says Cunnane, “with a minimum energy collection of 525kWh/m2/a.” These feed into the 1,500L buffer tank in the boiler room, which is the nerve centre of the operation, housed in the studio adjoining the house. 20m2 of panels, not to mention a 1,500L tank, seems a lot for a structure of this size (3,300 square feet, including the studio).
Josef Steiner explains the thinking behind the spec. “With 20m2, you get a contribution to space heating as well.” he says. “For domestic hot water, a 300L tank would have been big enough, but that 1,500L storage capacity is there because of the stove.” Without adequate heat storage, there’s a danger that the oven might overheat the house; diverting excess heat to the tank – which is highly insulated and only loses a degree in 24 hours if untapped – prevents overheating without waste. “Once we have 1,500L of storage,” says Steiner, “you also want to install a solar system to fill that. It makes sense to size towards each other.”
This tank then is the centralised heat store. “It’s like a hub,” says Gerry Cunnane, “that all the inflows go into and all the outflows come from. It’s primary water in the tank, which circulates through the heating system, and the domestic hot water is generated indirectly using an external heat exchanger…That domestic hot water comes from the very top of the tank, the hottest part of the tank, then the heating circuits are fed from a point lower down. You have two distinct zones; you have underfloor heating which would run at a certain temperature, then you have the trench heaters and the little heating cassette that’s in the HRV.”
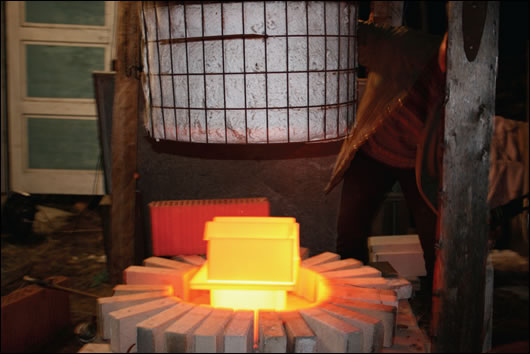
(above) the schamotte fire bricks of the kachelofen being fired; (below) the floor build up includes Fermacell slabs suspended on pedestals, and 160mm of Rockwool insulation
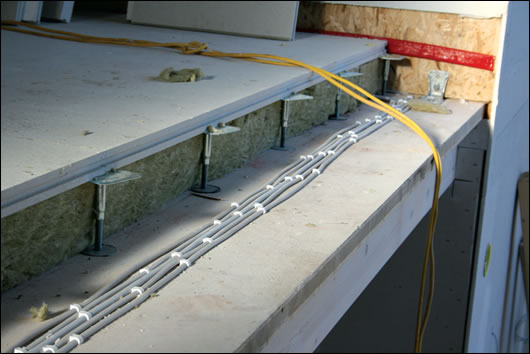
“The interesting thing about the system,” says Cunnane, “is rather than use a heat exchanger inside the tank to deliver up the solar heat, they use an external heat exchanger. When your solar panels get up above a certain size, it’s much better to use an external heat exchanger to load the solar heat into the tank, especially when you have a long pipe run…What you have basically is two pumps. The first pump comes on, circulates the solar heated water down as far as the heat exchanger which is on the tank, and once that heat has been there for ten or fifteen seconds, it then brings on the loading pump to strip that heat off and deliver it into the tank. In that way, you don’t get any initial cooling which you do get with a conventional heat exchanger, particularly if you’ve a long pipe run - you’ve all this dead water coming down that isn’t actually heated.”
The control system automatically favours solar energy. Once the temperature differential between the buffer vessel and the panels reaches ten degrees, the system comes on. The controls themselves provide for ample flexibility in programming between the different zones and balancing the heat inputs to optimise system efficiency. Also to that end, the weather compensating facility allows the system to regulate flow temperature lower or higher depending on external conditions.
Back inside the house on a dull November morning, you get a striking uniformity of air quality through the high, open plan structure. “It’s nice to get this connected volume,” says Steiner, “and because it’s well insulated you can afford to do it. Sometimes in an inefficient structure, you get cold spots because there’s such a large volume of air, but with the heat recovery ventilation, you get the warm air circulating all the time, so it’s always warm.”
Selected project details
Build system: Structural Timber Systems
Solar array: Wind Water Solar Energy Systems
HRV: MTD Solutions
- Articles
- Design Approaches
- Dream factory
- timber
- kachelofen
- woodstove
- firebrick
- lime
- MTD Solutions
- Structural Timber Systems
- sedum roof
Related items
-
Timber in construction group holds first meeting
-
Mass timber consultation: have your say by 21 April to change the rules
-
Seeing the wood for the trees - Placing ecology at the heart of construction
-
Boxing clever
-
TU Dublin launches timber technology degree
-
Scottish passive house built with an innovative local timber system
-
Towards greener homes — the role of green finance
-
Steeply sustainable - Low carbon passive design wonder on impossible Cork site
-
Timber frame & mass timber: the Passive House Plus guide to structural timber construction
-
Ecological brings Lime Green plasters to Ireland
-
Focus on whole build systems, not products - NBT
-
International - Issue 29