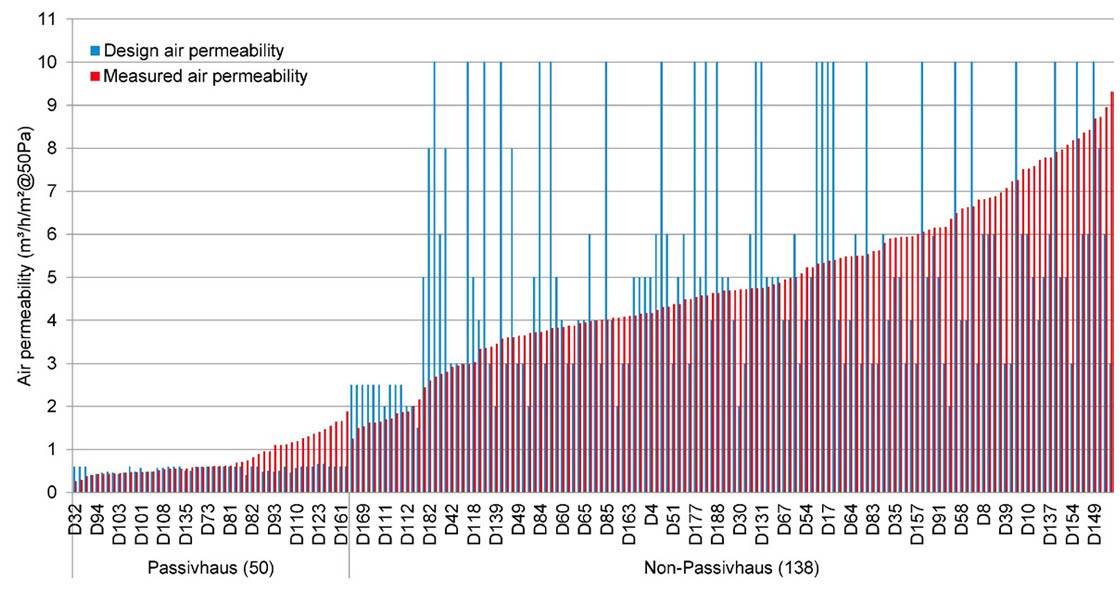
- Design Approaches
- Posted
Performance gap much smaller for passive homes, research finds
This article was originally published in issue 26 of Passive House Plus magazine. Want immediate access to all back issues and exclusive extra content? Click here to subscribe for as little as €10, or click here to receive the next issue free of charge
A detailed study of test results from almost 200 low energy homes in the UK suggests that while gaps between designed and real-world energy performance are ubiquitous, these gaps are much smaller in dwellings built to the passive house standard.
Professor Rajat Gupta and Dr Alkis Kotopouleases at Oxford Brookes University, analysed data from the UK’s National Building Performance Evaluation programme (begun in 2010 by the then Technology Strategy Board). The 188 homes, comprising 50 passive and 138 non-passive dwellings, were built with a range of construction systems and to various performance targets.
The team analysed the results of air leakage tests, in-situ U-value measurements of walls and roofs, and whole house heat loss.
The biggest set of data was for air permeability.
The non-passive homes had a range of air permeability targets, from 1.5 m3/h/m2 (at 50 Pascals of pressure, normal test conditions) right up 10 m3/h/m2 (the legal maximum).
But the actual results did not have much relationship to the targets, with nearly half of the homes being leakier than the targets, which were often unambitious in the first place. The average air permeability ‘overshoot’ was almost 2 m3/h/m2.
Most of the homes were fitted with mechanical ventilation with heat recovery (MVHR) systems, which would not have been performing efficiently in the 81% of non-passive homes with leakiness worse than 3.0 m3/h/m2, the recommended air permeability limit for installing MVHR, the authors point out.
A small number of homes used mechanical extract or ‘natural’ ventilation. Their permeability targets averaged at 8.5 m3/h/m2, but on average these homes actually had better infiltration rates than designed: for in the ‘naturally ventilated’ homes it was 40% better on average (5 m3/h/m2).
While this could offer energy and comfort advantages, if the ventilation strategy was dependent on air infiltration through the building structure, there could have been implications for indoor air quality. Air quality measurements were not within the scope of this meta-study, though they will be the subject of future research by the same team.
Overall there was barely any relationship between design and delivered air permeability for non-passive dwellings, which suggests that “design air permeability” means nothing in practice, unless the result is tested and enforced, as it is on certified passive house builds.
Meanwhile, just over half the passive dwellings also showed airtightness performance gaps, with worse fabric permeability than target, but in these instances the average gap was only 0.5 m3/h/m2, 75% less of a gap than in the non-passive homes. The widest gap was 1.3 m3/h/m2 among passive dwellings, and 6.3 m3/h/m2 among non-passive dwellings.
U-values & heat loss
In-situ U-values were measured in 20 of the dwellings and these too showed regular discrepancies between targets and measured results, under-performing in three quarters of those measured. The passive house walls measured on average 0.03 W/m2K higher than target, with non-passive dwellings averaging 0.07 W/ m2K higher. In ten cases, the wall U-value was worse than that allowed in the building regulations.
Roof U-values also missed their targets, with passive house roofs measuring 44% worse than target on average, and non-passive dwellings 71% worse.
For 29 of the dwellings the whole house heat loss had also been measured, via co-heating tests. Most of the passive dwellings underperformed slightly – these generally showed an ‘overspend’ of about 4.5 W/K (an overshoot of around 10%).
Whole house heat loss in the non-passive dwellings was much more variable, with some even doing better than designed.
However of those non-passive dwellings which underperformed, the gap was much bigger than with the passive dwellings – ten times as big in fact, at an average of 42 W/K, a 30-50% overshoot for many.
As the authors wrote: “the magnitude of underperformance was much less in PH dwellings ... a comparison between the non PH and PH developments [using thermal imaging] revealed a significantly lower frequency of defects amongst the latter, highlighting the importance of attention to detail that is integral in a PH approach.”
“Despite the small sample of PH dwellings with a complete set of fabric performance data, it is evident that PH dwellings perform well across all the three in-situ tests, indicating the robustness of the PH standard.”
The study also identified a difference between masonry and timber construction.
“The fabric performance gap was consistently larger for dwellings with masonry construction. Compared to their timber counterpart, masonry builds were found to be leakier and have higher external wall thermal transmittance and whole house heat loss,” the authors wrote.
Although numbers were small, masonry builds had a 20 W/K higher heat loss coefficient on average than the timberframed dwellings, which averaged very little performance gap.
But the results for passive dwellings showed much smaller deviations from design targets for both masonry and timber construction, “indicating that the quality of detailing and workmanship is more important than the type of construction,” the authors wrote.