- Large Buildings
- Posted
Graham Group's green HQ
Completed in December 2009, Graham Group’s new headquarters reveal the construction and asset management company’s commitment to green building. The project’s sustainability adviser, Chris Croly of BDP describes an innovative design that pushes the boundaries of natural ventilation and takes a thoughtful approach to materials and buildings services to ensure a minimal environmental impact.
What must a new generation sustainable office provide? It goes without saying that it should have an excellent energy performance, and the new office for Graham Group has achieved an A rated Energy Performance Certificate (EPC). However, excellent energy efficiency is just not enough these days, and this building has achieved a Breeam rating of Excellent for its holistic approach to sustainability. In addition, the people working in the building must know that they are working in a sustainable building; they must feel the difference as they work.
It used to be said that the most important thing to provide in an office building was user control. If the office staff could sit near a window and open it when they got hot, or could pull a blind to reduce glare, then they would feel like they had control over their local environment and would perceive the office environment to be comfortable. While this is partly true, it fails to address two important issues: the boiling frog phenomenon and people’s inability to notice changes in carbon dioxide levels.
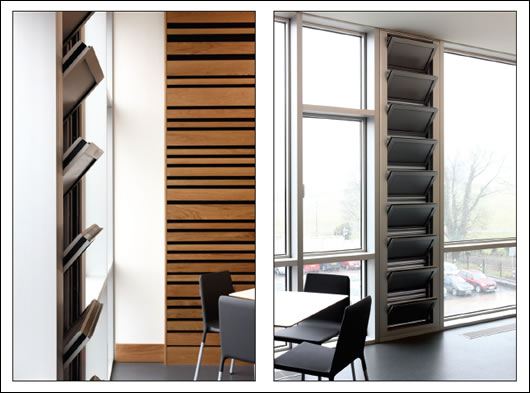
The building’s main natural ventilation system combines advanced floor to ceiling motorized louvres with manual window openings
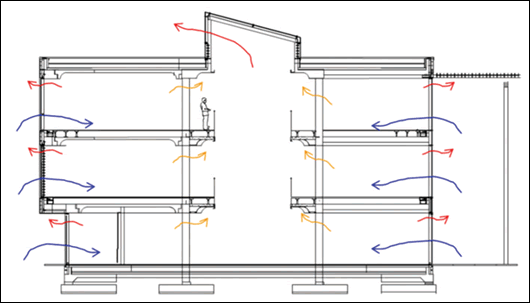
Have you ever walked into a room and noticed that it is hot and stuffy but no-one in the room has noticed, and all the windows have been left closed? This is the boiling frog phenomenon. Those of you who were concentrating in the more interesting moments of biology class may remember the theory that it is possible to boil a frog in a beaker of water without it jumping out, but only if you very gradually raise the temperature (0.002C per second to be precise). I doubt this experiment would work with humans (and can’t locate any research papers on the topic) but something similar does happen in an office where office workers don’t perceive air quality to be getting worse if the air quality changes gradually. Plenty of research has been done on this topic.
Humans are also particularly bad at detecting oxygen deficiency in the air and naturally ventilated offices regularly have carbon dioxide readings that rise above 6,000ppm where the recommended maximum is 1,500ppm before workers begin to dose off. To compound the situation, as we design buildings that are more airtight, the problem gets dramatically worse. One of our recent research projects demonstrated that new airtightness standards have doubled peak carbon dioxide concentrations requiring a new approach to design. A new generation office must therefore combine the best of the natural and automated approaches – a hybrid approach that was used in the new Graham building.
New innovation
The new three-storey Graham building offers a particularly interesting case study because it contains some new concepts that have not previously been used in office buildings. The first is the use of natural ventilation for the main IT server room. Server rooms in large offices are invariably air conditioned all year round despite the outside temperature in Ireland being below 15C for over 85% of the year, offering a source of free cooling. Computer experts often argue that a server requires the close control of temperature, humidity, and dust by an energy-hungry air conditioning system to operate correctly, but is this actually true? Why is the computer under my desk happy to operate for years in a naturally ventilated room but the server (which is just a very busy computer) requires such a special environment? When BDP proposed a natural ventilation solution for Graham, their IT staff were extremely forward thinking and approved the concept. The natural ventilation works by locating the server room on the north façade of the ground floor and using a vertical stack that runs up through the buildings three floors to generate a natural ventilation driving force. Intake air is provided through a carefully controlled wall louvre that adjusts dynamically to suit the room’s cooling load. There is a back-up cooling system provided for extreme weather, but it is almost never required.
The server room ventilation system is also designed to be able to recover heat from the servers during the winter through a connection to the building’s heat recovery system at the top of the natural stack.
The computer room has also been designed to be future-proofed and is sized to accommodate a potential change in computing technology to thin client computing. Thin client computing removes all of the computing power from the office spaces and places it in the central computer room. This strategy shares computing resources and therefore reduces computing energy dramatically. The natural ventilation has been designed to work with this future system.
The building’s main natural ventilation system is also unique and combines advanced floor to ceiling motorized louvres with manual windows.
The manual windows allow staff to adjust their local environment and the silent, fully adjustable, motorized louvres perform a series of functions as follows:
• Night cooling
In Ireland the outside temperatures during the night in summertime are considerably lower than daytime temperatures and opening the louvres at night, in conjunction with the vents at the top of the atrium, draws a significant amount of air through the building, cooling the building’s exposed concrete surfaces, and offering free cooling the following day. The building’s concrete ceilings are curved to maximise the area for heat transfer.
• Daytime temperature control
If an area of the office becomes too hot during the day, and staff have not automatically opened their windows, the louvres take over and gradually and silently open. Because the louvres are fully modulating, they can open to exactly the right proportion and this prevents unwanted draughts.
• Daytime air quality control
Many research studies have shown that people provided with opening windows in airtight buildings will not receive adequate levels of fresh air, particularly during cooler weather, as they tend to keep windows closed under the perception that it is not warm enough to need a window open. However, this then causes the carbon dioxide levels in the building to rise above recommended levels which could affect human performance. To counteract this, the building contains carbon dioxide sensors in each office zone and the louvres automatically open to maintain an optimum air quality.
• Airtight support
While the building regulations support the use of airtight buildings, they also require holes (permanent vents) to be provided in airtight buildings. Whilst the permanent vents normally have a manually adjustable cover, in practice such vents are never adjusted. This is a contradictory requirement because the permanent vents allow air leakage when the office is unoccupied and fresh air is not required. The use of motorized louvres overcomes the building regulation anomaly as permanent vents are not required in addition to the motorized louvres, which open only when actually required.
Motorized louvre vents were selected rather than motorized windows as they offer a much more subtle method of automated ventilation control. When opening to their minimum setting it is almost unperceivable that they have opened. The louvres also offer an improved control of outside noise relative to windows which was important as the building is located close to the M1.
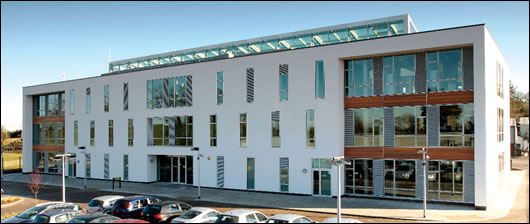
The more modestly glazed northwest façade
When designing the building, BDP approached a number of louvre suppliers and it quickly became clear that there were no identifiable louvres on the market with an acceptable air leakage performance. The company that provided the final louvres for the building was however open to development and modified their standard product to achieve the air leakage level set out by BDP, proving the advancement through independent lab tests. We are pleased that since the completion of the building, the suppliers are continuing to develop their products based on their findings from these lab tests. The environmental performance of products will often only be improved when designers and consumers challenge suppliers, so it is vital to continuously put pressure on the industry and demand product enhancements.
Advanced natural ventilation schemes should not rely on a single driving force and should work successfully in all weather conditions. Graham’s offices are largely open plan and are set around a central atrium offering several forces to drive the ventilation. The pressure difference across the building generated by wind draws air through the building’s plan, while the central atrium stack uses the building’s height to draw air through the building. In addition, the office spaces are provided with openings that have the largest possible height difference, with louvres reaching from floor to ceiling level, maximising the driving force for natural ventilation even when cross and stack ventilation are not in use.
During very cold weather (less than 5C outside) the mechanical ventilation system starts up as more energy is saved by recovering heat than is used by fans driving the ventilation at this temperature. When operating in mechanical mode the carbon dioxide levels in each area of the building are carefully monitored and air flows are carefully adjusted to the minimum levels required, minimising the energy use of the variable speed fans.
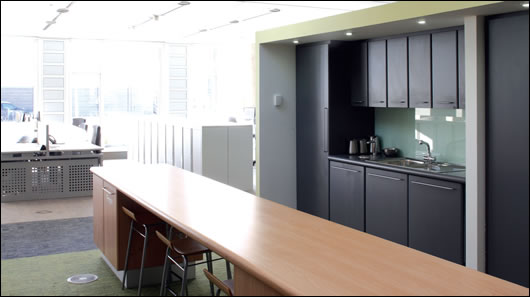
Each room in the building is fitted with daylight sensors. All lights turn themselves off
Integrated design
The building was recently described in Perspective Magazine as “an unassertive venture into the orthodoxies of mature modernism – clear and lucid in its plan and in its spatial organisation. A flagship building and a manifesto of the firm’s commitment to sustainable design.”
The building’s natural approach to sustainability comes from the embedding of sustainable consideration into every aspect of its design. The building’s location on the site, its orientation, the layout of the plans and the arrangement of glazing were all driven by the desire to reduce the building’s energy consumption passively.
The building faces south east to take advantage of morning sun in winter to passively heat the building. The south east façade is highly glazed to maximise useful solar gain and all other façades receive a lighter glazing treatment. Spaces that do not benefit from large amounts of natural light and do not require as much u heating such as toilets, stores, and plant are located on the north west side of the building, with the south east dedicated to office accommodation.
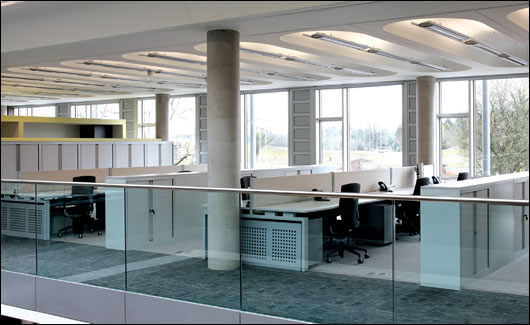
Perimeter lights remain off till daylight lux levels reduce
While solar gain is encouraged during the winter, in summertime it is blocked from the main façade by solar shading to the upper floor. Horizontal solar shading prevents high angle summer sun but allows low winter sunlight to enter the building. It is no coincidence that this shading is only applied to the top floor as the thermal modelling showed that the top floor is more susceptible to overheating than the other floors, due partly to heat gain through the roof and partly to rising hot air from the lower floors via the atrium. Solar shading can also block light and it is therefore not applied to the lower floors which receive less light from the atrium than the top floor.
Daylight
The amount of daylight received by an office space can be expressed by the term “daylight factor” which indicates the percentage of daylight outside that makes it into the building. Daylight factor levels of 2% are often considered to be adequate for office buildings but in fact offer a relatively poor level of daylight. In contrast, this building achieves an excellent daylight factor of 5% at the lowest floor, rising to over 8% at the top floor.
Quality daylight is vital for the generation of a sense of wellbeing in the offices but can also dramatically reduce an office’s electrical energy usage. Each room in the building is fitted with an occupancy sensor and the larger open plan offices are divided into zones, each with their own sensor. If the sensor detects that the room or zone is unoccupied, the lights automatically turn off. Each row of lighting is also u fitted with light level sensors that dim the lights in each row to exactly the required level. It can clearly be seen when visiting the building that the rows of lights closest to the windows are almost turned off while rows deeper into the office are normally dimmed to approximately 50% of their maximum output.
Heating
The building is heated almost entirely by a wood pellet boiler and pellets are sourced locally, minimising transport distances and supporting local industry. The biomass boiler is supported by a small backup oil fired boiler which is required for less than 5% of the time but allows the biomass boiler size to be reduced notably, reducing its standby losses. Hot water is also provided from the biomass boiler offering an almost zero carbon heating and hot water supply for the offices.
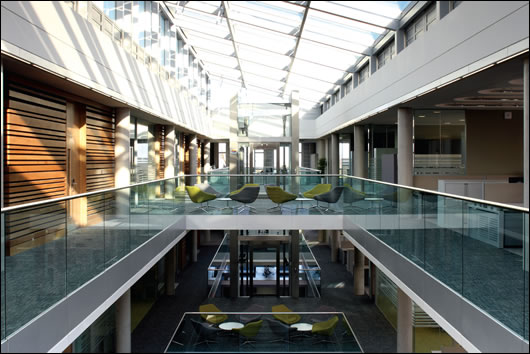
The offices are set around a large central atrium which aids ventilation and greatly increases natural light, with the added benefit of glazed balustrades
Water usage
The building’s low water consumption fittings are supported by a rainwater collection system that dramatically reduces the building’s water demand. The building’s discharge of surface water to the drainage network is also significantly reduced by the use of permeable paving, that allows rainwater to percolate gradually into the ground rather than diverting it to the surface water drainage system. u
Wider aspects of sustainability
The Breeam method is an international rating system that is often used to judge a building’s overall commitment to sustainability. The method examines every aspect of the building’s environmental impact from waste management and material selection through to management decisions. The building achieved a score of Excellent under the certification system – the highest result possible under the method at the time. The building was one of the first in Northern Ireland to use the scheme as a method of controlling the wider methods of its sustainability. As such, the building addressed the wider aspects of sustainability in a number of ways.
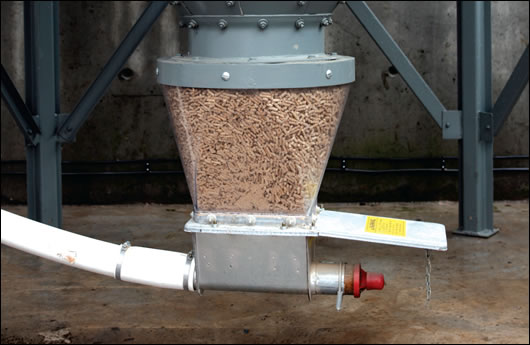
(above & below) The building’s heating and hot water is supplied almost entirely by a biomass boiler with the pellet storage area and plant room located in the roof
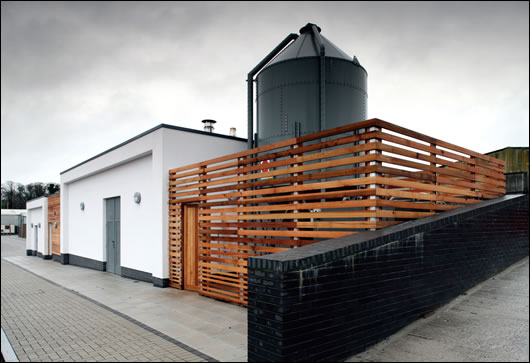
The existing site contained a disused fertiliser factory and the existing structures were crushed and used as building materials for the new building. Where new concrete was used, it contained 50% ground granulated blast-furnace slag (GGBS) to reduce its carbon impact.
Materials were selected with reference to the BRE Green Guide to Specification in order to ensure their environmental integrity. Low embodied energy materials were chosen. Timber – both in the building and for construction activities – was all certified as being sourced from an ethical source, long life building components were used, and consideration was given to the dismantling and recycling of materials at the end of the building’s useful life.
Low toxicity materials were used in construction with a detailed volatile organic compound (VOC) study undertaken, particularly when selecting internal finishes and furniture.
Internal acoustic baffles and some of the building’s furniture were made using sheep’s wool in order to support the use of natural materials.
A qualified ecologist was employed to advise the design team on the best form of landscaping to support local wildlife. In addition to planting, nest boxes, bat boxes, and butterfly nectar feeding stations were added to the site. A moth lodge was installed and a bat-friendly security lighting system was used.
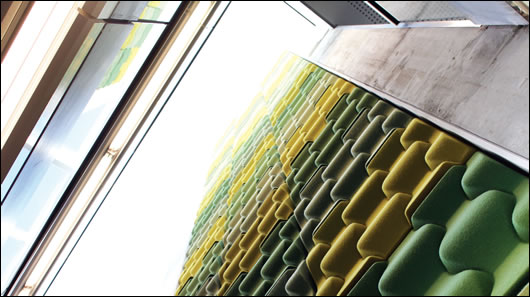
Internal acoustic baffles were made using sheep’s wool
The building is located at a key transport node, minimising transport to the various sites where the company work.
The building is future-proofed to allow ease of expansion without disruption to the building’s structure, and future-proofed against climate change by offering a natural ventilation solution that can deal with future outside temperatures that could be notably higher than those currently experienced.
The Considerate Constructors Scheme (CCS) – a scheme used to improve the image of construction - was implemented to ensure that the building was built in a way that minimised energy used for construction, and waste generated. The scheme also ensures consideration for the site’s neighbours during construction.
This approach is complimented by the work Graham does to reach out to the local community, providing employment and various u training opportunities locally.
End result
Due to the impressive carbon performance achieved by the building, and its attention to detail on every aspect of sustainability, the building is regarded by many as one of Ireland’s most sustainable workplaces. The levels of comfort offered by the advanced hybrid natural ventilation system make the building an essential case study for anyone who doubts the ability of naturally ventilated office buildings to produce a quality internal environment in Ireland. The use of the building not only as a functional office, but as a demonstration of the potential of sustainable office design, was one of the key goals set by Graham when procuring the building, and they have said of the completed building:
“BDP has managed to integrate sustainability into all aspects of the building design, enabling us to reduce our carbon footprint, lower our environmental impact and demonstrate the benefits of sustainable design techniques.
“We are absolutely delighted with our new premises, the new building and landscape not only looks good internally and externally, but is proving to be a very comfortable and pleasant office environment to work in – it is a resounding hit with our employees who love their new working environment.”

The new offices are proving to be a very comfortable and pleasant working environment for Graham’s employees
About Graham
Graham is a privately owned company operating in the construction, asset management and project investment sectors. Their new office is based in Hillsborough just outside Belfast, with their projects located throughout the UK and Ireland. It was important to Graham that their new office building was a visual demonstration of their commitment to sustainability both in the buildings they produce and in their own activities. It was however also important that the building could demonstrate that sustainability doesn’t bring a significant cost penalty and that it shouldn’t simply be attached to an otherwise badly performing building. Their new building was recently completed and was awarded the title of “Most Sustainable Building – Ireland 2009” by Action Renewables.
Selected project details
Architects/C&S/sustainability: BDP
M&E: Caldwell Consulting
QS: Bruce Shaw
Main contractor: Graham Construction
Fit-out/furniture: SPS (low VOC materials & sheep wool baffles)
Solar shading/glazing: McMullen Architectural Systems /Environmental fabrication
Vents: NACO
Boiler: Hoval
Air test specialist: Stroma Technology
Internal shades/blinds: Decor
Carpets: Milliken
Roofing: Grangers
Render: K-Rend
Rainwater harvesting: Rainharvesting Ireland
Drainage/permeable paving: Tobermore
Coffered slabs: Creagh Concrete
GGBS: Ecocem
BMS: Trend system installed by ATC
Trench Heating: Versatile Heating
- Articles
- Large Buildings
- Graham Groups green HQ
- natural ventilation
- Environmental Impact
- Night Cooling
- Airtight Support
- Louvre
- Mature Modernism
Related items
-
Campaign launched to tackle whole-life environmental impact of buildings
-
Why shading is a major issue in our hospitals
-
Ireland's new central bank hits nZEB & BREEAM outstanding eco rating
-
Ground-breaking housing scheme captures one developer’s journey to passive
-
Welsh school fuses passive & eco material innovation
-
Material impacts
-
East London passive school promotes active learning
-
Mechanical ventilation and IAQ - what the evidence reveals
-
International selection - issue 11
-
Hereford archive chooses passive preservation
-
Low energy Tipperary offices go for gold
-
Ireland's 1st hemp-built passive house