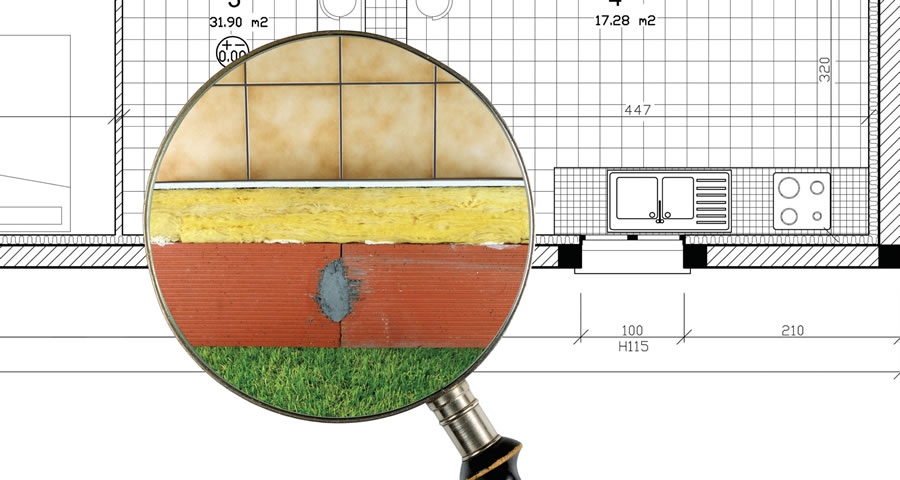
- Insight
- Posted
Material impacts
For decades now, European countries have been regulating the amount of energy new buildings can consume for heating and electricity. But as these standards get ever tighter, is time to start controlling the embodied energy and wider environmental impact of building materials — and what’s the best way to do it?
As building regulations tighten and sustainable building moves further into the mainstream, the building materials sector has been in a frenzy to get on the bandwagon. Greenwashing has of course been with us for years, and takes many forms.
Prefixes like ‘eco’ and ‘enviro’ pop up behind established brands, while promotional literature moves away from product imagery to generic shots of blue skies and rolling hills. Advertising copy gets selective — the Forest Stewardship Council (FSC) certification might only apply to the veneer, and not the core timber, while what has always been standard practice can suddenly get pushed out into the limelight, re-invented as a green innovation. You get vague, unverifiable claims, while the world ‘natural’ pops up everywhere, as if naturally occurring substances (eg asbestos, formaldehyde and arsenic) are universally good.
Despite the introduction of a raft of advertising standards across jurisdictions in order to try and combat the spin and encourage the science, the central problem here is that the main source of information on most of the building materials that we use are the companies that make them – meaning the companies promoting genuinely greener materials can get lost in the marketing noise.
Dr Craig Jones is director of Bristol-based consultancy Circular Ecology. He says: “You see them when you walk around the large trade shows. I won’t name any names but everyone knows who the large ones are. Every product, every material seems to be billed as sustainable. As a sustainability professional, it gets a bit tiring because not everything is sustainable in construction at the moment. Most things are quite far off and yet the word ‘sustainability’ gets bandied around all the time.”
In this part of the world, there are almost no statutory obligations to monitor, let alone curtail the environmental impact of the building materials we use. Regulation has concentrated on the energy needed to run the building rather than the energy needed to build it, and there were good reasons for that. Our building stock could only be made habitable by burning a lot of fuel.
Now however, as the regulations tighten and the process of breaking the fossil fuel habit becomes entrenched, the embodied energy in our buildings [ie all of the energy associated with the manufacture of the building materials and construction of the building] has come into sharp focus. Looking at Part L of the Irish building regulations and taking the 2005 regulations as a baseline, the first wave of reform saw a 40% reduction in operational energy [the energy used for heating, cooling and electricity] in 2008, followed by a 60% reduction from that same baseline in 2011. Changes to the energy performance standards in the UK (under separate versions of Part L in England and Wales, Part F in Northern Ireland and Section 3 in Scotland) have so far been less dramatic, but profound change is coming: under the EU’s energy performance of buildings directive, all new buildings must be nearly zero-energy by 2021.
Presentation of Environmental Product Declaration certificates to a number of prominent European construction product manufacturers at an October 2014 Eco Platform event. Photo: Triptyque
Dr Jamie Goggins is a senior lecturer in civil engineering at the National University of Ireland, Galway. “There are lots of ways to achieve the reduction in operational energy,” he says, “but one of the key things is obviously to make the building fabric more thermally efficient, and one way of doing that is to add more insulation to it. That means there’s an increase in material used in the building envelope. The more material you have, the more you drive up the embodied carbon and energy.”
As operational energy reduces, embodied energy — as a portion of the total energy the building will consume over a sixty year life — climbs steadily higher. Goggins and his team at NUI Galway have explored a wide range of local and international studies in their research. To make things simple, he zones in on one – a 110 square metre cavity wall house.
“If we take the 2005 [Irish] regs, the percentage of embodied to operational energy is about 20-80. Then under the 2008 regs, it’s 25-75. In the current regime, it’s about 40-60 and when it comes to nearly zero energy buildings, it will be about 50-50.”
There is, he points out, quite a bit of variation within these figures, depending on the sources of operational energy and the materials chosen in construction, but the trajectory is unambiguous. “The key message here is that as you move towards more energy efficient building in terms of operational energy, the percentage of embodied energy gets more significant,” he says.
The other point he makes is that there is a significant material difference between operational and embodied energy. “Embodied energy is all about the here and now,” he says. “These are the emissions being put into the atmosphere today, whereas operational energy emissions are spread over sixty years…Surely it’s a lot less onerous on the environment to deal with the operational side of things over the 60 years rather than sending it into the atmosphere all in one go, or at least over a short period of time.”
Moreover, these figures make some pessimistic assumptions about where the energy to heat and cool our buildings will come from over the next sixty years. As the grid decarbonises, the proportion of energy that comes from fossil fuels will continue to decline, thereby forcing up the relative proportion of energy expended in construction.
Goggins continues: “The greenhouse gasses that we’re giving off today in making the material and constructing the building, we can’t change that, we can’t roll that back, but the operational stuff we have 60 years to deal with.”
Against this backdrop, the case for regulating exactly what goes into the buildings we build becomes compelling. In the UK, the civil engineering sector has started to address the issue. Craig Jones of Circular Ecology says that all new water infrastructure must undergo a whole-life embodied carbon assessment, while new rail developments over a certain size must measure their embodied carbon impact.
There’s no equivalent in the buildings sector. Certification programmes like Breeam offer points for completing life cycle assessments and reducing the environmental impact of a building, but there is, as yet, no statutory requirement for such work.
Even the voluntary codes have drawn criticism from within the green building sector. The BRE Green Guide to Specification, which is used as a means of gaining credits under the Code for Sustainable Homes, has come in for a lot of negative attention. The Alliance for Sustainable Building Products (ASBP) in the UK has issued a lengthy critique of the guide, pointing to, among other things, its lack of transparency.
It says: ‘None of the data used to generate Green Guide ratings is open to public scrutiny. The principle of transparency is a central theme of international LCA standards [life cycle assessment] (ISO 14040). It is common practice to ‘black box’ sensitive information but not the entire data set. As the UKGBC [UK Green Building Council] Task Group have indicated, the principle of transparency is critical to foster trust and learning.’
At a European level, CEN/TC 350 is the committee responsible for developing standardised methods for the assessment of the sustainability aspects of buildings and civil engineering works. In recent years, it has put much work into developing assessment methods for construction materials, and in particular, developing core rules for the development of Environmental Product Declarations (EPDs) for construction products.
As far as the future of building materials is concerned, the EPD is set to become a very familiar term. Craig Jones says that EPDs offer something approaching a common standard. “Anyone measuring the environmental impact of construction would be recommended to use these standards because they are official EU-wide standards, applicable all around Europe. They’ve been out since 2011/12, and while it does unfortunately take a long time for standards to become influential, they do help to bring consistency across Europe.”
An EPD is essentially a standardised document which quantifies the life-cycle environmental impact of a particular product or system. Each one is independently verified and registered, and breaks down the impact of that product or system across a range of categories, including global warming potential, ozone depletion, acidification and eutrophication.
“An EPD is actually similar to the nutritional label that you would find on a box of Corn Flakes,” says Pieter Stadhouders of Netherlands-based consultancy EcoReview. “Similar in that you describe the characteristics of your product in a way that is easy to understand, consistent and that it complies to the environmental regulations.”
It’s important to say that having an EPD doesn’t mean that the product in question is in any way superior to its alternatives. Rather, it cuts a swathe through the greenwash and describes the environmental impact of that product in precise, scientific terms. Databases of EPDs are slowly becoming the gold standard in Europe, superseding earlier data sets which captured only the embodied energy and carbon of building products.
We’re also seeing the beginnings of regulation around life-cycle energy, and here too, EPDs are playing a central role, particularly in the Netherlands, where a statutory framework for reducing the environmental impact of buildings is at a more advanced stage than anywhere else in Europe.
Pieter Stadhouders says that since 2012, to get a construction permit in the Netherlands for any building larger than 100 square metres, an environmental impact calculation of all the materials in the building is required. “The indicator which they use is called the Environmental Cost Indicator, or ECI, and that’s a summation of eleven different environmental impacts which are weighted to give one figure.”
This regime facilitates the accumulation of a wide range of data, which, it’s envisaged, will lead to the development of a series of ECI benchmarks for different categories of building. From there, it will then be possible to encode minimum values into the building regulations.
“Probably in the future there will be regulations on maximum ECI per square metre,” says Stadhouders, “or there will be some sort of penalty if you have a high ECI per square metre …It’s not yet determined on how this policy will work, but they’re saying, ‘ok we want to prepare the markets to calculate this and get a reference’.”
At a national level in the Netherlands, much of the work has centred on building the databases which will inform the design of whatever policy is eventually settled upon. Stadhouders explains that ‘category one’ data was essentially first generation data gleaned from work done by some sectors, including concrete, to measure the environmental impact of its products. This data, while it fell short of the standards set by EN 15804 – which governs the development of EPDs – provided the authorities with a baseline dataset with which to begin assessments.
“Then they asked different industries — wood, cement, gravel, glass and so on – to compile an EPD for the whole industry. This phase took about two years to complete, and gave the ‘category two’ data, which was validated data under the EN 15804 determination method, even though it was not producer specific.” The third and current phase comes with the publication of validated, product-specific EPDs. This is the most detailed dataset yet and comprises ‘category three’ data.
The authorities in the Netherlands are now in the process of phasing out that first database, by introducing incremental penalties for the use of category one data, thereby incentivising the industry to adopt a more scientific way of measuring the environmental impact of the materials it uses.
In Ireland and the UK, the political climate for improved environmental regulation may have soured in the last few months, with the scrapping of the zero carbon homes plan in the UK, while in Ireland, political pressure has been brought to bear on a local authority that has sought to make the passive house standard a minimum for new buildings. So there would seem to be little prospect here for improved regulation of embodied energy and carbon in buildings.
But while the regulatory environment may not be up to it, Pat Barry, executive director of the Irish Green Building Council, believes that the market may do a lot of the work that the government shies away from. “Manufacturers will only go and get an EPD if they know they’re better than the average,” he says, “so it encourages manufacturers who believe they have performed better and have made an effort to reduce their impacts to go off and get the verified data. Getting an EPD gives a competitive advantage.”
He also points out that Breeam and Leed, two of the leading green building certification programs, award credits just for having an EPD, creating further competitive pressure. Already, a broad number of product manufacturers – including many whose wares are advertised in these pages – have either acquired or are in the process of preparing EPDs for their products.
Barry believes that those competitive pressures will continue to push the sector in the right direction. “Pretty much any large office project will get some sort of certification so when an architect rings a manufacturer and says, ‘look we have to get this credit, we need an EPD, have you got an EPD? You don’t?’ If that happens with only 5% of specifiers, they start to see a change, and manufacturers start asking, ‘What’s an EPD? I suppose we better get one because we’re losing 5% of our market share if we don’t have one.’”
As EPDs become more common, he suggests, it will be easier for government to regulate. “You can’t regulate for something that is expensive and that is being done by very few people, but once it becomes mainstream, once it becomes common practice, then it makes it more feasible for local authorities and governments to regulate for it.”
Craig Jones in Bristol is a little less optimistic. He believes the virtuous cycle of competitive pressure leading to regulatory action is still a long way off. “I think there’s a bit of chicken and egg in the UK at the moment…There’s probably not enough activity from manufacturers and the government’s not regulating anything either.”
He points out however that the advent of building information modelling, or BIM, holds out the prospect of mitigating the administrative burden that a fresh layer of regulation would add to a sector that has had to deal with a lot of additional regulation over the past decade.
BIM is all about creating a comprehensive digital representation of a building. As EPD databases become more comprehensive and BIM software more powerful, it’s possible to envisage a time when making the calculations needed to establish the life cycle environmental impact of a building will become much simpler than they are today.
“If these assessments could be integrated into the tools that designers are already using,” says Jones, “it becomes a lot easier… Then hopefully – because it’s so much easier to do an assessment — government will get more comfortable about regulating.”