- Passive Housing
- Posted
Forward pass
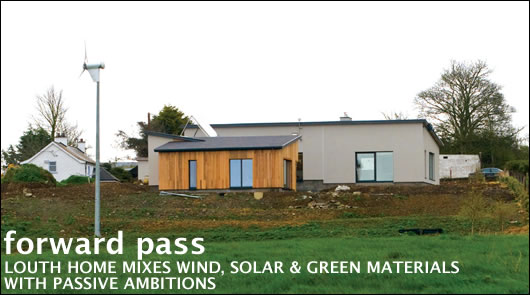
As interest in sustainable building continues to escalate, Construct Ireland is increasingly unearthing buildings that betray an ambition to break new ground under a plethora of green criteria. John Hearne visited one such house in County Louth, and found a project driven by passive house and BER scale-topping ambitions combined with on-site energy and water supply strategies and a commitment to the use of green materials
A new house in Collon, County Louth marries passive house principles with an aesthetic that sacrifices nothing to low energy design. Superinsulation, a very high level of air-tightness and a selection of renewable technologies facilitate a dispersed, tiered layout that works perfectly with the site and the surrounding countryside. “The house itself came from the topography of the site,” says Stephen Young of Young Design Build, the home’s designer and owner. “Because of its height and the location, the site didn’t lend itself to two storeys or anything of that type, which would have been more suitable for passive house.”
The passive house standard, as with all low energy design, is predicated on simplicity. Complex architectural shapes that are difficult to heat or compromise air-tightness are out. But by taking an innovative approach to construction and making maximum use of orientation, Stephen Young has effectively delivered a passive house with a twist. “We ended up using the tiers on the site and came up with three different blocks, separating our living areas from our sleeping quarters with a corridor in between, to give us a U-shaped block with a courtyard to the centre.”
Because of that dispersed footprint, achieving low energy consumption was a bit more challenging, admits young. It was achieved primarily by reducing heat transfer through the building fabric – surpassing even passive house criteria. “We went from the standard 0.15 W/m2K down to 0.12 W/m2K” he says. “0.15 W/m2K would be an average requirement for the whole envelope, so we got 0.10 on the floors and 0.12 on the walls and the roof.” In addition, glazing on the northern façade was kept to an absolute minimum while maximum advantage was taken of the southern aspect. Using smoked glass panels in conjunction with the U-shape, even bedrooms with a northern aspect enjoy considerable passive solar gains. In fact, the bathroom and the utility room are the only rooms in the house that don’t get any southern light.
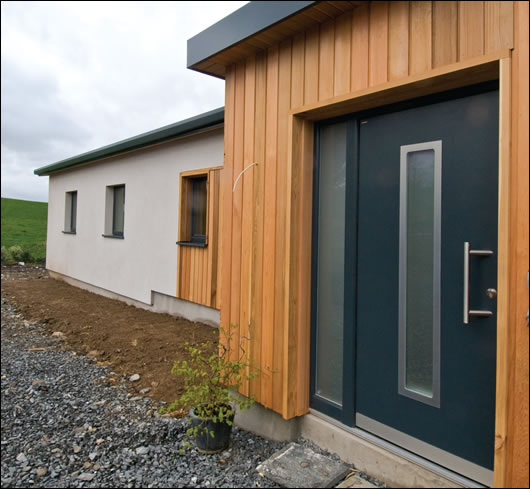
The cedar clad front of the newly-built house
“We used strip foundations because of the change in levels between the different blocks. The site or the design didn’t lend itself to an insulated raft slab, so we went with strip foundations and used Quinn-lite block work for all the rising walls. It’s an aerated block, so it’s got better thermal efficiency than a standard block. It’s a structural block as well; very light and easy to work with.”
One of the stand-out elements of the build was the innovative I-joist timber frame. Typically only used for structural purposes on long spans, Young came up with this solution in order to achieve a deeper structure and thereby facilitate a greater volume of insulation. “We looked at lots of different methods of construction to achieve high U-values with reduced depths, so I could have a timber structure that had less of a thermal bridge from the inside to the outside, which meant we could use less insulation. We used two elements of soft wood, internally and externally, which are connected by a plywood web.” The plywood webbing, from outside to inside, reduces from a width of 50mm down to 9mm, thereby drastically reducing the heat transfer.
“Stephen came to us asking if we’d be able to make walls out of I-Joists,” says Conor Doherty of A-Frame Energy Efficient Homes. “We looked at his floor plan, got our engineer to review it and said basically, yes, we could do it…Your standard walls are 140mm, and you just pack in the insulation. With the I-joists, you can go as wide as 400mm, and joists you can get spans of 6m and 7m long.” Young also points out that by achieving a high thermal performance in that one single solution – wider walls – you’re reducing construction time and expense. There’s no need for additional thermal measures, either outside or inside. The frame also comes pre-fitted with a Solitex external breather membrane from Ecological Building Systems to protect against moisture ingress. In all, the timber frame took two and a half days to go up.
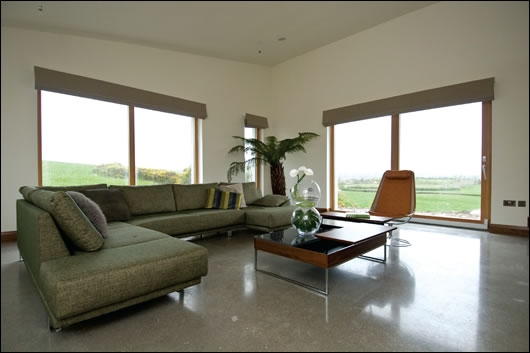
The southern aspect of the house utilises extensive glazing to maximise passive solar gains
Next came the air-tightness membrane. Here, Young chose Siga’s Majpell breathable vapour control barrier, used in conjunction with Siga’s range of tapes and adhesives. Andreas Schmidt of Siga is keen to point out that achieving air-tightness is as much about process as product. Training is crucial in securing the exacting air-tightness standards required when building to the passive house standard. To that end, Siga run a one-day training course for customers, then back this up with advice and site visits as required. “Our products are very good, but without good workmanship, they’re worth nothing, so you need that kind of training and advice onsite.” In conventional builds, the membrane is typically stapled on. In passive construction however, it’s recommended that tapes are used to reduce penetrations through the membrane. “Quality control was also a big aspect.” says Stephen Young. All trades onsite were taken through the air-tightness process to drive home the importance of keeping it in-tact throughout the build. The wall build-up also included a service cavity through which cabling and plumbing were routed, again in order to keep services away from the membrane. According to Young, air-tightness tests recorded an astonishingly low 0.235 air changes per hour at 50 Pascals, substantially better than the passive house 0.6 requirement.
Into the frame went no less than five tonnes of Warmcell 500, supplied by Ian Fox of Collon Eco Insulation. “We were given an approximate start date.” says Fox, “but unusually for this business, the Youngs were ready ahead of time by roughly two weeks. We were able to work to the new dates and found the site meticulously prepared. All of the breathable membrane was erected without any creases or sagging.”
Internally, Young considered standard plasterboard but opted in the end for Fermacell building board, primarily because the product removes the need for skim coat. A conventional plaster finish introduces a substantial amount of water into the build, leading to the likelihood of cracking as the finish dries out. Fermacell is however finished with FST, a light, trowel-on finish that can be painted within half an hour of treatment. “It’s a fibre board as opposed to a plaster board.” says Paul Callan of Richmond Building Products, who supplied the product. Manufactured from water, recycled paper and recycled gypsum, its high density gives it high fire and acoustic ratings. “For example, 12.5mm board on either side of a 75mm metal stud, with a rockwool infill, can give you up to 54db sound reduction, and that outperforms 9 inch blockwork.” Fermacell also substantially outperforms plasterboard on racking strength. Equivalent to 9mm plywood, the board can take up to 50Kg from a single point loading. It’s also moisture resistant and can be used in bathroom and kitchen areas.
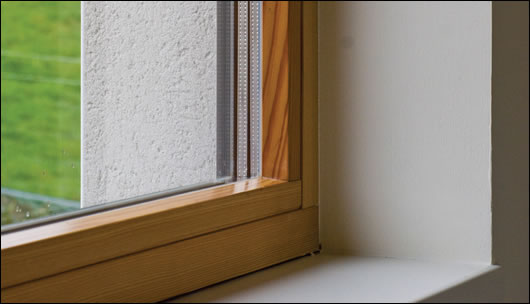
High performance triple glazed windows sit in a substantially thick wall
The full wall build-up is as follows: Fermacell, a battened service cavity, the air-tightness membrane, the timber frame with cellulose insulation, an external racking board, breather membrane and external battening. For outside finishes, Young chose a mix of render finish and cedar cladding, delivering an immensely impressive total wall U-value of 0.12 W/m2K.
I-joist construction with a cellulose infill was also used in the roof, maintaining that same U-value. Though Young had intended finishing the roof in zinc, the planners insisted on slate. This presented a particular problem because of the low pitch of the roof. The plan specified a 10 degree pitch, but slate can’t be relied upon to withstand wind-driven rain when the pitch drops below 20 degrees. The choice was then either to increase the pitch, or find another way to weather-proof. Young chose the latter. Above the breather membrane, he battened and counterbattened, then installed a Kingspan insulation panel, but for more than its thermal properties. The panel provides protection against the elements, while the air cavity underneath prevents condensation build up. A Nu-Lok slate system, also provided by Richmond Building Products, was then fitted to the top of the panel. “By using the Nu-Lok system,” Declan Green of Richmond explains, “you set out your battens at 307mm apart, and there’s a linking channel for every tile. You fit 8.1 tiles per square metre. Because the link channel works as an overlapping system, you don’t have to use as many tiles per square metre.” In addition to the cost saving and environmental benefit – simply by reducing the usage of materials – you’re also placing less stress on the timber frame and the foundations. “It’s a more secure way of fixing your roof and it’s a quick and easy way to work. It cuts down on labour and you’re not nailing the tiles because you’re just clipping them into the link channel.”
To complete the envelope, Young installed 200mm of Xtratherm rigid polystyrene in the floor, underneath a 150mm floor slab. Then, instead of additional interior finishes, he polished the concrete slab. “There were two reasons for that.” He says. “We really liked the finish when we saw it elsewhere. It’s a hard, durable surface that you’ve no worries about maintaining; it’s like one big floor tile really, and the pure look contrasts well with the white walls. Plus we wanted to maintain that heat sink as well.”
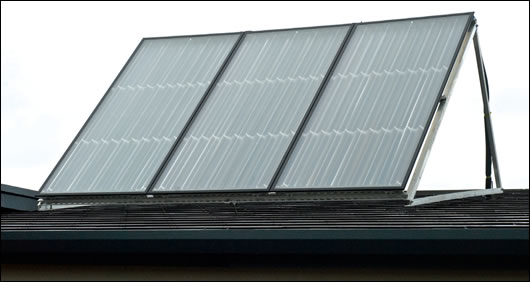
Three solar panels are mounted on the roof
The triple-glazed, aluclad doors and windows are the Edition range from Internorm, supplied by Ecoglaze. “When we first went looking at windows, we found that some companies had great U-values on their windows but they wouldn’t do a complementary door or a complementary sliding window. We wanted everything to tie in together; that was one benefit of the Ecoglaze range. And the external window sills came as part of the system – they clicked in underneath.” Each window incorporates three 4mm glass panes with argon fills and aluminium spacer bars, while the energy performance is further enhanced by the thermal break that the external cladding provides. The total U-value in the window comes in at 0.86 W/m2K. This falls short of the passive house target of 0.8 W/m2K, but because walls and roof outperform the criteria, the overall envelope remains within the specified limits. “The door that Stephen went for in the front of his house is a passive house standard door.” says Matt Jordan of Ecoglaze. “It’s got a total U-value of 0.79 W/m2K. It’s such a big unit, it feels like a safe when you open and close it.” Does the size and weight of these units, and the chunkiness of the profile ever put people off? “The only problem,” he says “is you’re restricted to certain designs and they’re fairly European designs, so for the passive house door you wouldn’t get the likes of Georgian doors in Dublin.”
One of the key advantages of the Ecoglaze patio doors is that they ‘tilt and turn’, facilitating summer ventilation. Young also hopes to deal with any overheating issues with planting. “I didn’t really like the idea of integrating louvers or anything like that into the building, I don’t think they look residential, and given the size of the house, large overhangs wouldn’t have worked either, so we’re looking at integrating natural solar shading by planting a lot of trees.”
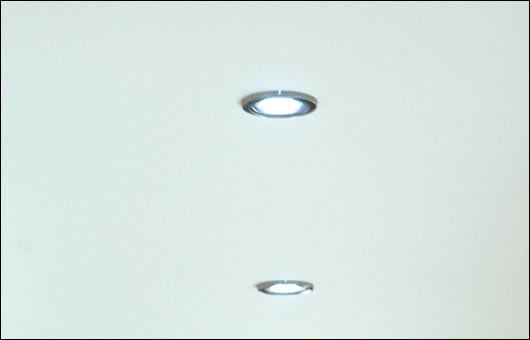
LEDs are fitted in the hall
In keeping with the best low energy design principals, the three bedrooms on the house’s northern elevation have small windows. However, they still manage to benefit from considerable solar gain. All three open onto the hallway which connects the house’s two tiered blocks, which is itself south-facing and features large glazed sections. Smoked glass panels fitted alongside bedroom doors conduct much of that passive heat into bedrooms.
The house’s sole space heating source, a Kal-Fire wood fire, was imported direct from the manufacturer in Holland. It’s a partially sealed unit, fronted by a glass panel, which, crucially, has its own air supply ducted directly to the fire from the outside. The amount of air going in can be adjusted to temper combustion intensity. “Because it’s glass enclosed,” says Young, “it’s far more efficient, so it burns more slowly. It’s a smart unit in that once you have it burning, it’s got its air supply to the underside which it distributes in two ways. First into the combustion area, then the other air supply goes around the casing of the fireplace. That heated air is then conducted into the living space through vents on either side of the fireplace.”
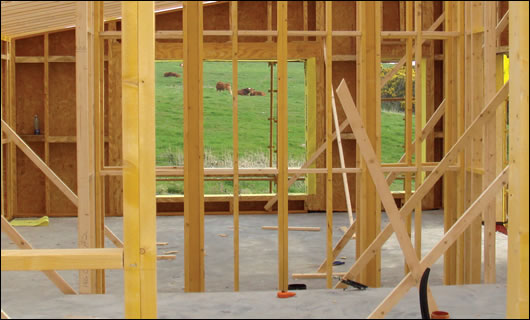
The innovative I-joist timber frame system went up in just two and a half days with Solitex membrane’s to protect against moisture ingress
The one disadvantage arising from the combination of wood fire and the low air change rate is that you cannot use the extractor fan over the cooker while the fire is burning. The kitchen/dining/living room comprises a single volume of air. If the extractor fan runs at the same time as the fire, it will depressurise the room and begin sucking smoke from the fire. “In some installations you can get an auto bypass, so when you switch on an extractor hood, you might have another fan in place that will boost the extraction from a fireplace. Otherwise, you could just open a window.”
Young considered routing the warm air from the fire directly into the ducting of the heat recovery ventilation system, but decided against it because of the high temperature of the air. In any case, the warm air from the fire is being discharged into the open plan living/kitchen area and is then distributed through the house by the HRV system, a Maico WS 250 provided by Irish Fan Distributors in Waterford. A compact ventilation system certified by the Passivhaus Institut in Darmstadt, the system also incorporates a geothermal brine loop. “It’s actually using the heat of the ground to temper the fresh air coming in.” says Billy Wright of Irish Fan Distributors. “You have a constant temperature in the ground of between 7 and 10 degrees. The loop allows you to use that temperature to pre-heat the air in winter and pre-cool it in summer.” The 50m loop runs along the northern and western sides of the house. Because of the prevalence of rock onsite, a long mound had to be created to achieve the 1.5m depth required to take advantage of the constant soil temperatures. The HRV system also incorporates a post-air heater, which is run via a heat exchanger linked into the hot water system and controlled by a single room thermostat in the utility room.
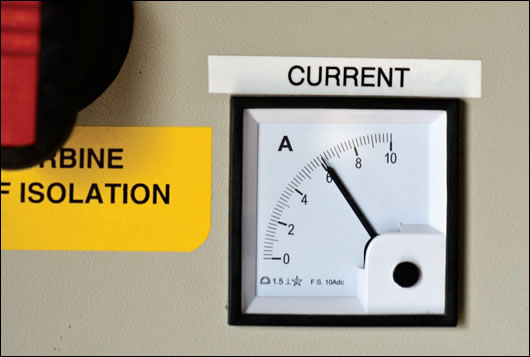
Live data on the performance of the Proven wind turbine
The solar panels are Solarfocus CPC collectors supplied by Renewable Energy Systems and fitted by Penarch in Monaghan. These hybrid panels are guaranteed against condensation and the effects of corrosive air. “If you take flat plates,” says Paul Carberry of Renewable Energy Systems, “they’re vented top and bottom and most have 30mm of insulation at the back. CPC doesn’t, which is a big advantage in Irish weather conditions. We suffer hugely from condensation, which they don’t have in mainland Europe where most of these products come from. Through the changing of the seasons, particularly the fluctuations in temperature, the collector never condensates internally…Condensation causes problems by rotting the insulation at the back. So with conventional flat plate, the efficiency ratings you had quoted at the start, may, in three or four years mean nothing.” The parabolic tray incorporated in CPC panels also facilitates the collection of sunlight up to fifty degrees west and east of south, thereby allowing greater flexibility in panel placement. Because of the low pitched roof, the three panels – fully 7.2m2 – had to be mounted on an A-frame on the roof to achieve the optimal 45 degree angle. The panels feed directly to the hot water tank, with any excess going to a buffer tank for use via the heat exchanger in the HRV system.
Since moving into the house, the Young family have found that between the post-heater in the HRV and basic hot water requirements, they rely on the back up immersion far more than had been anticipated. To mitigate this power requirement, and the impact it has on the BER, Young is now looking at adding an air-to-water heat pump.
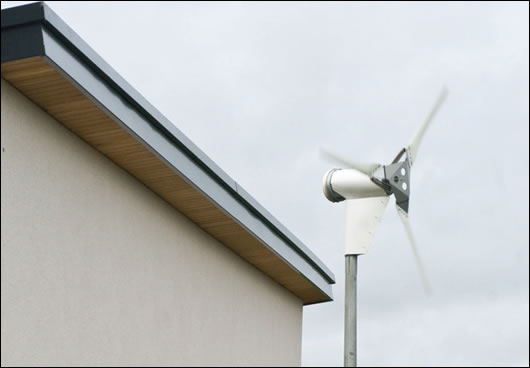
The 2.8 kW wind turbine provides a sizeable part of the house’s electricity requirements
In the meantime, the Proven 2.8kW wind turbine is providing a substantial chunk of the house’s electricity requirements. Also supplied by Renewable Energy Systems and fitted by Penarch, Paul Carberry says the 2.8kW machine is perfectly sized: “You’re not exporting a huge amount of power, and what you do export to the grid, you’ll get the full benefit of.” The combination of feed-in tariff arrangements recently announced by ESB and Eamon Ryan will allow the exportation of 3,000 kilowatt hours onto the grid per year for a combined tariff of 19c per KWh. Any electricity over that limit will earn the lower rate of 10c.
“We went with the Proven turbine,” says Stephen Young, “because they’ve been used for a long time in rugged terrain and on sites in the ocean, so they last. Many of the cheaper turbines we looked at would cut out in high windspeeds and stop generating, whereas the Proven turbine, the blades come in on themselves during high winds, so they still rotate and won’t cut out. When you have wind, you want to keep using it.” The system requires maintenance annually, which can be completed in half a day, without the use of any heavy machinery.
Tommy Kelly of Penarch, who installed the turbine, says that Young’s site was good without being exceptional. A clear, unobstructed view of the southwest – from which we get 90 per cent of our wind – is the prime consideration. “Your first job is site location. You have to analyse the site and find the best position for the turbine within the constraints of planning and boundaries, then you mark where your foundations are going, you dig them out and pour them. That’s basically phase one.” Two separate sets of foundations are required. The tower foundation, in which the baseplate for the tower is mounted, measures 3m by 3m by 1.2m deep, while the foundation for the winch pin, which facilitates raising and lowering of the turbine itself, measures a metre squared. “Phase two, you leave it two to three weeks to cure the concrete, then you can mount your tower and put your turbine on that…Once you get your foundations right, everything else falls into place.” Since it was installed, the turbine has drawn huge interest from passers-by. Young says at least two people every weekend ring the bell to ask about it.
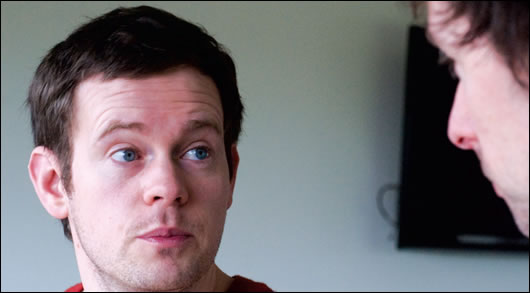
Stephen Young, of Young Design Build, talking to Construct Ireland journalist John Hearne
To further reduce electricity consumption, dimmable CFLs are used throughout, while LEDs are fitted in the hall. Each unit provides the equivalent of 50W of illumination, while consuming only 2W of power. “It’s not a huge abundance of light,” says Young, “but it’s sufficient for a corridor.”
The house also boasts a Bord Na Mona RainSava rainwater harvesting system. Using the roof as a collector, the water is conducted to the 4,000L underground tank via the gutters and downpipes. “Inside the tank,” Bord Na Mona’s Frank McKenna explains, “there’s a submersible pump. That’s directed to a control panel that can be placed in a utility room or the garage. That will service your washing machine, outside taps and toilets. Between 60 and 70 per cent of the water you use in the house will be fed by the RainSava tank.” The water is filtered in two stages. Initially, a vortex filter is fitted between the downpipes and the tank itself, while a second filter on the submersible pump provides an additional level of comfort. Because the house is located in a hard-water area, using rainwater in the washing machine prevents the lime-scale damage that would otherwise occur.
Using the passive house methodology, Stephen Young estimates that the house’s annual space heating requirement at 13kWh/m2/a. “From a BER rating point of view, it’s A2 with the turbine, but if we refine our cylinders and put in an extra heat source, preferably a heat pump, it will go up to A1.”
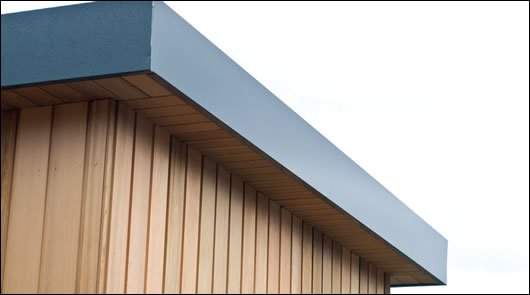
The roof is also of I-joist construction with a cellulose insulation fill
Passive house living does take a little getting used to, he says. “The first night we moved in, in November, the house was freezing…Sharon, my wife, thought the house just wasn’t working, it was so cold. It took the guts of a month and a half to warm up. With a passive house, I knew going into it that it would be different in its first year cycle, and once you get a summer over, that you’d build up a lot of heat into the slab. A year on after that, you’d expect it to be that little bit warmer coming into winter again. Right now, we have a comfortable 20 degrees throughout the living areas and a little less in the bedrooms.”
Selected project details
Client: Stephen & Sharon Young
Designer/contractor: Young Design Build
Timber frame: A-frame Energy Efficient Homes
Air-tightness: Siga and Ecological Building Systems
Cellulose insulation: Collon Eco Insulation
Windows and doors: Ecoglaze
Fermacell boards: Richmond Building Products
Heat recovery ventilation: Irish Fan Distributors
Solar thermal & wind turbine: Renewable Energy Systems
- Articles
- Passive Housing
- Forward pass
- BER
- water supply strategies
- Superinsulation
- Siga
- Majpell
- breathable vapour control barrier
Related items
-
Podcast: what we've learned from 20 years in green building mags
-
BERCerts.ie offering ventilation validation
-
BER data indicates national house building growth – except for Dublin
-
BER data: sick buildings risk while new build surges
-
G-rated Meath bungalow aims for A rating — without renewables
-
Is building life cycle assessment about to become easy?
-
Going A1-rated & certified passive lifts build costs by 0.1%
-
Analysis: 12,000+ homes built in 2017 – as energy standards marginally fall
-
New homes data reveals extent of Irish low energy revolution
-
Simple and stunning Highlands passive house merges old and new
-
SuperHomes scheme offers home retrofit support
-
IGBC launches Ireland’s sustainable homes label