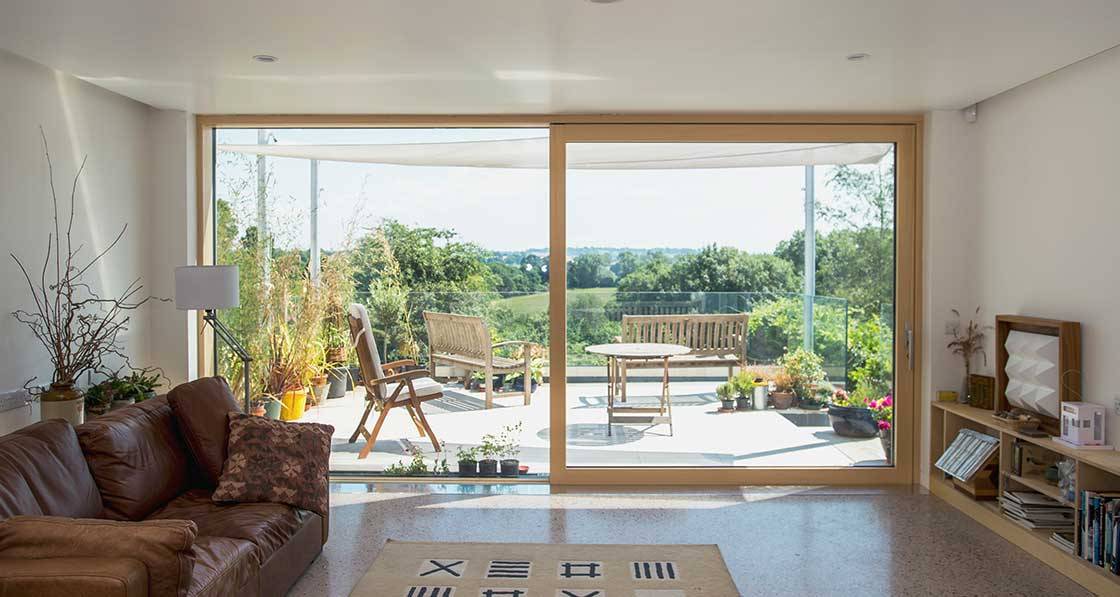
- New build
- Posted
Site specific - Somerset passive house adapts to tight plot
The best architecture responds skilfully and sensitively to its surroundings, so when a long and narrow plot beside a busy road became available in the Somerset village of Chew Magna, architect David Hayhow set out to design a passive house, inspired by nearby farm buildings, that would be both private yet filled with light — quite the challenge given the site’s tight restraints.
Click here for project specs and suppliers
Building: Detached timber frame passive house
Completed: January 2018
Location: Chew Magna, Somerset
Budget: £420,000
Standard: Uncertified passive house
£200 profit per year (with renewable feed-in tariff)
For once, estate agents are not exaggerating when they describe the Somerset village of Chew Magna as “well sought after”. Handily placed near Bristol, the ancient city of Bath and the Mendip Hills, house prices here are not for the fainthearted.
Local architect David Hayhow and his wife Rosemarie had lived for years in the village when they decided they wanted to build a passive house. The problem was, as David says, “hens’ teeth are more common” than finding a good location in Chew Magna.
They just don’t turn up. People have to buy land with houses on and knock them down and start again. But most plots cost £750,000 before you even start demolishing. And we’re not in that price league. We know people who took a big risk, buying and hoping to knock the house down, then they couldn’t get planning permission,” he says.
This article was originally published in issue 30 of Passive House Plus magazine. Want immediate access to all back issues and exclusive extra content? Click here to subscribe for as little as €10, or click here to receive the next issue free of charge
Eight years ago, the couple finally found a desirable site at auction. The existing building had originally been constructed as a garage workshop but was being used as an office by an estate agent. The price was affordable, perhaps because there were still five years left on the lease.
Planning permission had already been granted for a house, but David and Rosemarie wanted to proceed with a different design more suited to meeting the passive house standard.
“We took a gamble on being able to build the house we wanted,” says David. The couple left their project in limbo for several years before applying for planning permission, which was granted subject to a few changes. The build took a year after work began in January 2017. An important early decision was taken to re-use the existing strip foundations, which extended two metres under the ground. This was one of the project’s greenest elements as it negated the need for lots of new concrete.
We took a gamble on being able to build the house we wanted.
The long and narrow shape of the site had a great influence on the design, which took its inspiration from a nearby cottage and barn that had once been part of a farm. These two-storey structures had gables facing the high street, and steep, pitched roofs. But David’s passive house was rendered, rather than stone clad, and he opted to place slates on the roof as they blended with the black solar panels.
Getting enough light into the Pump House was challenging. David decided not to put many windows on the east and west elevations, which overlooked neighbouring homes. This made it essential to maximise the light coming from the two gable ends.
“One end was facing south, so it was simply a question of putting in lots of glass. But it wasn’t easy to get light into the middle of the building,” says he says. “We managed it by introducing a double-height area of roof glazing, which we dubbed the Wintergarden. It provides lots of light for both the ground floor and the north-facing study we share on the first floor. It makes it a lovely space to be in even when the skies are grey outside.”
1 Laying of the concrete slab which was installed over 300mm of Dow Floormate XPS insulation; 2 erection of the closed-panel timber frame system; 3 installation of the Internorm windows on the tight site required a crane; 4 I-rafters in the roof which were then filled with 300mm Earthwool insulation; 5 Smartply ProPassiv airtight OSB to the inside of the roof construction, with airtight taping at junctions and joist ends; 6 the outside of the roof build-up with battening over woodfibre insulation; 7 outside this again was the breathable sarking and the mounting system for the solar PV array, with was installed flush with the roof slates; 8 detail at the wall roof junction with Diffutherm woodfibre wall insulation rising up under the eaves to meet the roof insulation; 9 internal service cavity insulated with Rockwool.
The Hayhows have been monitoring heat performance since moving into the house in January 2018. Temperatures are consistently around 19C or 20C, but David says it feels slightly warmer than that. In March last year, during freezing weather, temperatures only dropped below 18C on two mornings before rising above 20C during the day. Two months later, an early heat wave pushed temperatures inside above 25C, principally because of the large glazed area.
David has since found ways to rectify the overheating issue. He has installed two motorised opening lights to the roof windows, and a small opening in the external wall just above the ground floor which, when activated at night, provide cooling ready for the next day.
Meanwhile, the south-facing bedroom windows have been fitted with external Venetian blinds inside a fourth layer of glazing, and the sliding doors to the living area are protected by a shade-sail supported on steel posts. David is also planning to add internal shading to the roof glazing.
It is full of light and interesting use of materials.
In the first year the couple used 3,480kWh from their renewable electricity supplier, but with their 6kWP solar photovoltaic array, generated 5,270kWh in the same period. David says he and Rosemarie love the feel of their passive house. “The house is great to live in. Each space has a particular character and offers small delights at every turn. It is full of light and interesting use of materials.”
He continues: “The study has a high sloping ceiling and looks north onto the High Street. We are aware of the traffic, but it is subdued by the triple glazing. The study is not as gloomy as north-facing rooms usually are as it gets light from the south through the winter garden roof. We’re also aware of the path of the sun as it travels through the day.”
Selected project details
Clients: Rosemarie & David Hayhow
Architect: David Hayhow
Structural engineer: John Filor Consulting
Passive house consultant: Alex Duckworth
Passive house assessor: Warm
Sustainable drainage consultant: Clive Onions
Timber frame: All Timber Frames
Mechanical & solar PV installations: Green Flare
Electrical contractor: AJW Services
Airtightness test: Building Analysis & Testing
Wall insulation: Superglass, via All Timber Frames
External wall insulation & render: Baumit, via Back to Earth
Additional wall insulation: Rockwool, via Earthwise Construction
Roof insulation: Knauf
Additional roof insulation: Diffutherm, via Back to Earth
Floor insulation: Dow
Airtightness products: Ecological Building Systems, Back to Earth
Windows & doors: Ecohaus Internorm
Roof windows: LAMILUX UK Ltd
GGBS cement: Dors Building Services
MVHR installation: Earthwise Construction
Permeable paving blocks: Stonemarket
Sedum roof: Riefa Green Roof Solutions
Air source heat pump: Mitsubishi
MVHR: Green Building Store
Solar PV: LG
Clay paint: Mike Wye Ltd & Associates
Airtight OSB: Smartply
Airtight sealing foam: Illbruck
Ground slab: Dors Building Services
Fit-out contractor: Earthwise Construction
Rainwater harvesting: Rainwater Harvesting Ltd
In detail
Building type: Detached 202 sqm timber frame passive house
Location: Chew Magna, Somerset
Completion date: January 2018
Budget: £420,000
Passive house certification: Uncertified
Space heating demand (PHPP): 11 kWh/m2/yr
Heat load (PHPP): 9 W/m2
Primary energy demand (non-renewable, PHPP): 61 kWh/m2/yr
Primary energy demand (renewable): 27 kWh/m2/yr
Primary energy generated: 39 kWh/m2/yr
Heat loss form factor (PHPP): 3.35
Overheating (PHPP): 0%
Airtightness (at 50 Pascals): 0.39 ACH
Energy performance certificate (EPC): A (95)
Measured energy consumption: 3,480 kWh (mains electricity consumed in first year) Energy bills: £421 for electricity in first year (also covers space heating & hot water). However, renewable feed in tariff of £621 per year received, leaving a net energy profit of £200.
Thermal bridging: Additional external & internal insulation to walls & roof to reduce bridging; insulated fixings for woodfibre EWI; strip foundations w/ lightweight blocks insulated both sides. Guidance taken from ‘Passivhaus-Bauteilkatalog’ & Steico’s ‘Building System Details with Psi values’.
Ground floor: Existing strip footings raised by two courses in aircrete blocks w/ 450mm XPS insulation to inside & 650mm outside. 150mm concrete slab on 300mm Dow Floormate XPS insulation, on DPM, on sand binding, on existing slab. U value 0.107 W/m2K
Walls: Closed-panel timber frame walls; Baumit render externally followed inside by 60mm Diffutherm woodfibre insulation, breather membrane, 230mm timber studs insulated with glass fibre, 15mm OSB, Diffutherm Udisteam vapour barrier, 50mm Rockwool-insulated services zone, plasterboard. U-value: 0.120 W/m2K
Roof: Slates externally followed by battens, breathable sarking, counter battens, 35mm Diffutherm UdiTop woodfibre insulation, I-rafters filled with 300mm Earthwool insulation, 12mm OSB, 50mm Rockwoolinsulated services zone, plasterboard. U-value: 0.114 W/m2K
Windows: Internorm Studio timber/aluminium HF310 triple glazed windows, HS330 lift & slide door. Typical overall U-value: 0.8 W/m2K
Roof windows: Lamilux PR60 energy save fixed & motorised roof windows. Overall U-value: 0.9 W/m2K
Heating system: Mitsubishi Ecodan 4kW air source heat pump w/ thermal store. Supplies domestic hot water & heating to 3 x towel rails & one small radiator in drying cupboard. Ventilation: Paul Novus 300 mechanical ventilation w/ heat recovery. PHI certified heat recovery efficiency 93%. Purge ventilation by opening roof windows.
Water: Low flow taps and showerheads; rainwater harvested to 3,500L tank for use in WCs and garden. Calculated water use 29 litres per person per day from mains, plus rainwater use.
Electricity: 6kWp PV system on WSW facing roof, flush with the slate roofing. Produced 5,270 kWh in first 12 months.
Green materials: Reused materials existing foundations, timber and steel from existing site. FSC-certified timber throughout plus timber from our own sequoia. Woodfibre insulation, GGBS concrete, clay paints, Fermacell tile board. Riefa planting board made from flour and coir (coconut fibre).
Landscaping: Permeable block paving to the entrance and parking area. Sedum green roof to lobby area & wildflower meadow to bin store roof using Riefa system.
Image gallery
https://mail.passivehouseplus.co.uk/magazine/new-build/site-specific-somerset-passive-house-adapts-to-tight-plot#sigProIde151564243