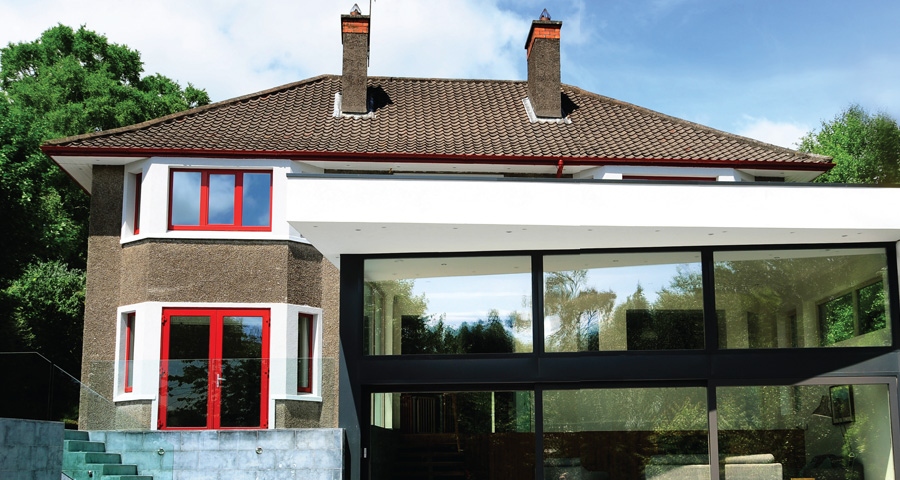
- Upgrade
- Posted
Cork home hits 94 percent heat reduction with Enerphit
The vast majority of energy upgrade projects aim for low hanging fruit measures, and risk locking buildings and their occupants into needlessly high energy usage, environmental impact and discomfort. This recent home upgrade on the outskirts of Cork City shows what truly deep retrofit looks like.
Prior to Elite Architect’s renovation of a 1950s house in Co Cork, architect Andrew Shorten used passive house software to estimate its annual heating bills. When the figure came in at a staggering €5,500, he did a double-take.
“It sounded a lot,” says Shorten, “but when I thought about it, my own rule of thumb for a ten-year old house built to building regulations is that it costs about a Euro per square foot per year to heat, and this house is 1950s, single glazed with zero insulation and 2,500 sq feet. That €5,500 mightn’t be far off.”
When Shorten performed the calculations again after the renovation, he found that the cost of heating the house had fallen to just 6% of the original figure.
The drive for Enerphit, the Passive House Institute’s standard for renovations, came from Elite. Shorten says that he simply recommended that approach for the job and the client agreed. “At the time they were renting an old house in Blackrock in Cork. I was talking about an airtight house, and they had drafts coming up from under the floorboards, so they were able to contrast what we were aiming for with the wrong end of the spectrum.”
While Enerphit standards are not as exacting as passive house, design professionals will tell you that achieving those standards can actually be more challenging. A new build offers a wider choice of design and construction options. When you have to work with and retain large sections of what’s already there, it frequently requires more imagination and a more exacting spec to hit the targets.
“There was a rustic character to the house, particularly as you approach from the road, and we felt we didn’t want to lose that character,” says Shorten. “It hadn’t been touched in years, so it needed a significant overhaul in terms of performance, electrics, plumbing, heating, insulation and aesthetics, and we also needed to transform it into a tasty house to live in. In fact, it was kind of obvious what the brief was.”
One thing the project had in its favour was orientation. The living areas of the house already faced south, benefiting from passive solar gains. To increase those thermal gains still further, an extensively glazed one room extension was added. A sloped garden facilitated dropping the floor level here, allowing the design team to create a four metre high living space surrounded by a double-height glazed wall. In order to both connect outside and inside, and to provide summer shading, an overhang was created at this elevation.
Contractor the Green Build Centre had worked on passive house projects before, but this was u their first Enerphit renovation. “We were very lucky to be honest,” says project manager Mark Higgins, “because basically the house was stripped back bare. In that respect we had a blank canvas to work with. We stripped out the whole building, ceilings – the lot.”
Retaining the external look of the house meant ruling out one approach that tends to feature prominently in Enerphit projects: external insulation. But because it was such a big, boxy house, there was sufficient room to accommodate additional insulation internally.
The team then turned its attention to eliminating cold bridges and achieving airtightness. Andrew Shorten points out that external insulation, in addition to affecting the house’s character, can add a further challenge in a retrofit situation. “With external insulation, there’s now a huge gap between that insulation and the insulation under the floor.”
Shorten argues that insulating internally put him in a better position when it came to designing away cold bridges. Cutting away all floors and ceilings allowed the contractor to completely dryline internal walls. Installing new insulation beneath the floors and in the roof then allowed the team to effectively create a continuous, almost unbroken layer of insulation inside the house.
“If you draw a section through the house,” Shorten explains, “floor meets wall perfectly, wall goes through first floor perfectly, bar timber joists bridging, which isn’t a major deal. Then it goes up and meets the 450mm of attic insulation.
“All of the internal walls meet the external walls, creating a break in the insulation but we pumped the cavity with 100mm of bead, so that thermal bridge was nullified by the fact that there was more insulation out beyond it. It meant the compromise there was really minor.”
Airtightness was then achieved through a combination of OSB board and Siga tape. As has become increasingly common now, the build contract was subject to a substantial retention – in this case €30,000 – on achieving airtightness.
“We have a system where one person is in charge of the airtightness from start to finish on the project,” says Mark Higgins. “That one person is basically onsite all the time. He’s project leader.”
“When a trade finishes he’ll inspect, and he’ll advise before the trade starts as well. When you tell people that airtightness can cost anything between €5,000 and €10,000 they really don’t understand why – sure it’s only tapes and plastic. They don’t understand the amount of labour that goes into achieving it.”
He adds that he treats airtightness as a process, and that he doesn’t tend to make any money on that aspect of the build. The first and only airtightness test recorded 0.9 ACH, comfortably within the Enerphit limit of 1 ACH.
Heat now comes from a gas boiler, while a heater battery in the mechanical heat recovery ventilation system provides backup. “Because the extension is virtually all glazed apart from one wall,” says Shorten, “there was a risk of it being vulnerable to cold in the winter because of excessive heat loss, so that area has a separate zone heated by underfloor heating. We’ve found that that works perfectly.”
The new triple-glazed windows from Slowinscy deliver overall U-values of 0.7, while a bespoke rooflight over the office area, put together onsite by the contractor, was also designed to meet a 0.7 U-value.
Despite achieving Enerphit standards, so far neither client nor architect have opted to seek certification from the Passive House Institute. “It wasn’t high on our priority list.” Shorten admits. “But it’s at the standard. While we may go for it in the future, we haven’t pushed our client to get certification because it’s an expensive process.”
The clients are now in the house for seven months. There has been the usual adjustment period as they get used to how a passive space works. “I think it takes a little getting used to from a client’s point of view. We’ve experienced that with other clients as well. Once they’re in the house six months and they understand things, they get happy with it.”
“The whole project went quite smoothly,” says Mark Higgins. “The architects were onsite every week which is very important. If you have a problem, it can be dealt with quickly. The biggest watch-out factor is that everyone is talking all the time, and everyone understands what’s happening next.”
Selected project details
Clients: Anonymous
Architect/passive house consultant: Elite Architects
Engineer: Foundation & Design
Main contractor: Green Build Centre
Energy rating assessment: Brian Ronayne
Heat recovery ventilation:
ProAir Systems, installed by Munster HRV
Insulation to floor and walls: Xtratherm
Cavity wall insulation:
Thermobead, installed by Dungarvan Insulation
Roof insulation: Knauf
Airtightness products: Siga
OSB: Medite Smartply
Breather membrane: Ecological Building Systems
Thermally broken cavity wall ties: Ancon
Windows & doors: Slowinscy
Roof windows: Cork Glass/Velux
Condensing boiler: Vokera
Kitchen/fitted furniture: Creative Designs
Additional info
Project overview:
Building type: renovation and extension to a 1950s detached house
Location: Cork
Completion date: December 2012
Budget: confidential
Enerphit certification: application has not yet been made.
BER (before): unknown
BER (after): B1 (92.68 kWh/m2/yr)
Space heating demand (PHPP)
Before: 226 kWh/m2/yr
After: 12 kWh/m2/yr
Heat load (PHPP)
Before: 103 W/m2
After: 11 W/m2
Airtightness (at 50 Pascals)
Before: Unknown
After: 0.92 ACH
Original walls
Before: blockwork with un-insulated cavity. U-value: 2.0
After: platinum EPS insulation to existing 80-90mm cavity; 100mm Xtratherm Thin-R PIR insulation internal drylining; Smartply OSB airtight/vapour control layer with all joints taped with Siga tapes; 38mm Xtratherm PIR insulation; plasterboard with skim finish. U-value: 0.11
Extension walls: blockwork with 100mm cavity pumped with full fill bead insulation, TeploTie low thermal conductivity wall ties; 100mm Xtratherm Thin-R PIR insulation internal drylining; OSB airtight/vapour control layer with all joints taped; 38mm Xtratherm Thin-R PIR insulation; plasterboard with skim finish. U-value: 0.11
Existing roof
Before: pitched, hipped A-frame roof to existing house with concrete roof tiles. U-value: 2.3 W/m2K
After: PVC single ply roofing membrane; 300mm mineral wool insulation on the flat between existing roof joists vapour barrier; 50mm service cavity; plasterboard ceiling. U-value: 0.09
Extension roof: PVC single ply roofing membrane; single ply membrane finish; WBP plywood; 50x50 battens to create ventilated void; Pro Clima Solitex Plus breather membrane; Firring pieces to create falls; 425 mm Eco joists with 450mm Knauf Loft roll between joists; Siga Majpell vapour barrier and tapes; 50x50 battens to form service cavity; plasterboard with skim finish; U-value: 0.11
Floor: original suspended wood floor removed, roughly 400mm of 804 aggregate imported and compacted; radon barrier; 150mm of Xtratherm PIR insulation; 150mm concrete slab. U-value: 0.11.
Thermal breaks: 100mm wide strip of Xtratherm PIR fixed to the base of the external wall at 300mm beneath floor level, meeting 150mm of Xtratherm laid horizontally beneath 150mm of concrete – and used to level concrete pour.
Windows & doors
Before: single-glazed, aluminium windows.
After: new triple-glazed Slowinscy Thermax Ultra timber alu-clad windows. Overall U-value: 0.70
Roof windows: triple-glazed unit to flat roof from Cork Glass. U-value: 0.7. Velux triple-glazed rooflight. U-value: 1.0
Heating system
Before: existing boiler and radiators throughout entire building
After: Vokera Combi gas boiler, 97% efficiency, underfloor heating to extension only. Heating battery in ventilation unit, with heat distributed through HRV system to all rooms.
Ventilation
Before: no ventilation system. Reliant on infiltration, chimney and opening of windows for air changes.
After: ProAir PA 600 HRV with Sap Appendix Q rated efficiency of up to 94% and specific fan power down to 0.57 Ws/l, with in line heating battery fabricated by ProAir.