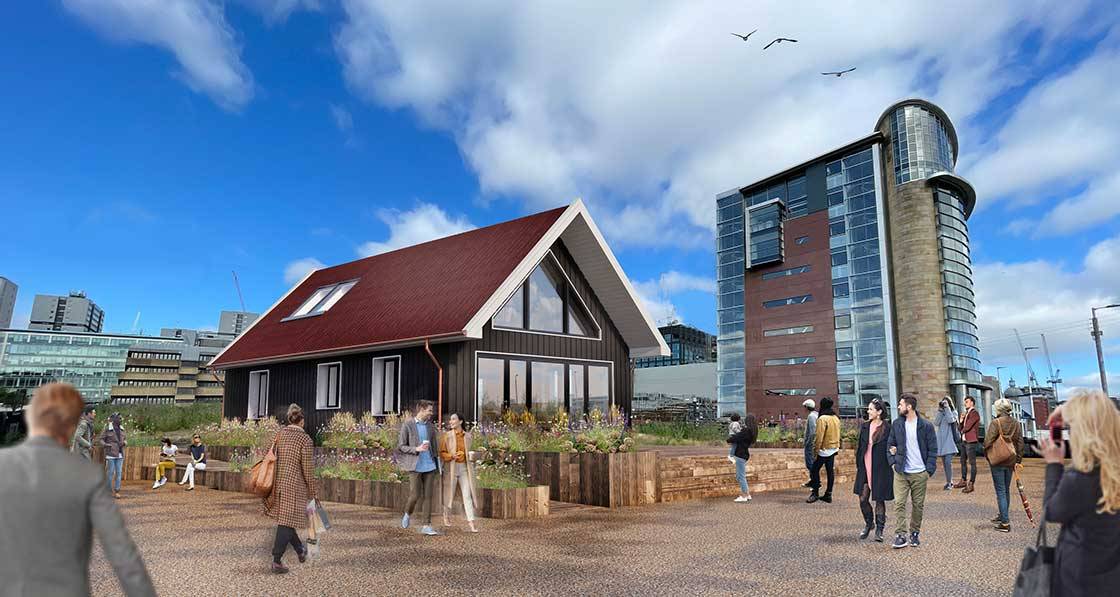
- Events
- Posted
COP26 house to showcase fabric first, low carbon build methods
This article was originally published in issue 39 of Passive House Plus magazine. Want immediate access to all back issues and exclusive extra content? Click here to subscribe for as little as €10, or click here to receive the next issue free of charge
The timber frame house is being constructed by Beyond Zero Homes, a coalition of organisations aiming to demonstrate how “beautiful, affordable, healthy and comfortable homes can be developed with minimal impact on the environment, throughout their lifecycle”.
The group is led by architect Peter Smith of Roderick James Architects, and includes leading manufacturers and suppliers in the sustainable building sector such as Ecomerchant, Medite SmartPly, NorDan, Steico, Fakro, and Paul Heat Recovery Scotland, as well as Home Grown Homes, the forestry company BSW, and contractor Robertson.
After COP26, the house will be dismantled into its original 1.2 metre-wide panels and be transported in its entirety to its new home near Aviemore, where it will form one of a scheme of 12 affordable houses.
The 65 square metre house has been designed to minimise embodied carbon, using local timber and natural, sustainable materials. According to a provisional life cycle analysis carried out by Circular Ecology, the house has an embodied carbon of 374.4 kg of carbon dioxide equivalent per square metre (kgCO2e/m2) during building life cycle stages A1 to A5 (raw material supply through to construction), but sequesters more than double that amount (815.2 kgCO2e/m2) in wood-based products during the same period. This carbon will be kept out of the atmosphere so long as these wood products remain used in this or any other structure into future.
For life cycle stages A1 to A5, B4 (refurbishment) and C1 to C4 (end of life), the total embodied carbon is 515 kg/m2/yr, well inside the RIBA 2030 Challenge target of 625 kg/m2/yr (though the RIBA challenge also includes other B stages). For a small, detached house, especially with a double height space, achieving the RIBA operational energy target of 35 kWh/m2/year has been more of a challenge. “Whilst the RIBA target is extremely difficult to achieve for this particular house design, we like a challenge and are investigating a variety of different ways of heating the building to ensure we meet the target,” said architect Peter Smith. “For larger houses using this same build system, the target is significantly easier to achieve.”
The house, which was largely built off-site, was specifically designed to use homegrown C16 spruce to avoid the need for imported timber. The timber frame walls also feature SmartPly Propassiv, an airtight OSB certified by the Passive House Institute, as well as Steico wood fibre insulation both externally and between the studs.
“We have made conscious, informed choices about every material in the house to minimise embodied carbon,” said architect Peter Smith. “In particular, responsibly sourced timber and natural materials are used as much as possible in the structure, with reduced reliance on concrete and steel.”
He added: “All timber elements, which make up the vast majority of the structure, can be re-used or recycled at end of life, as the house has been designed to be easily dismantled.” All fittings, external cladding, and windows have been screwed in place rather than nailed or glued so that everything can be easily removed, repaired or replaced.
While not aiming to achieve the passive house standard, passive house design principles have been applied, including an airtightness target of 0.6 air changes per hour, minimisation of thermal bridging, and heat recovery ventilation. Walls, roof, and floor are designed to U-values of 0.13 to 0.14. The house has a space heating demand of approximately 25 kWh/m2 per year, with this demand provided by an infrared heating system.
Meanwhile all windows are triple glazed, and while there is plentiful glazing, the use of large roof overhangs and eaves were designed to avoid overheating. In addition, the wood fibre provides protection from temperature peaks due to the combination of low thermal conductivity, high specific heat capacity and high density.
“Here is one example of a building that exceeds our 2030 targets for embodied carbon and dramatically reduces operating energy compared to current benchmarks, using existing products, existing suppliers and existing skills. It shows just what we can achieve with new build right now,” said Will Kirkman of project sponsor Ecomerchant.