- Case Studies
- Posted
Daintree
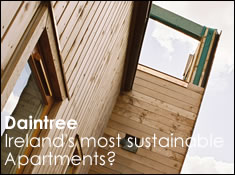
The Daintree Building is a mixed-use, sustainable urban building on Pleasant’s Place, just off Camden St. Dublin , writes Brian O’Brien of Solearth Architects. Conceived in 1999 it has been a long development process—but by late September Daintree should be open for business and the ever innovative Daintree (Paper Co) Ltd will have a new home, one appropriate to the delightfulness of their products and their focus on nature’s generosity for their raw materials.
Containing 7 apartments, commercial and craft space, a retail shop and a café as well as ancillary ‘green’ elements like bicycle cabins, recycling areas and composting units the project is very much an urban ‘poly-culture’, in terms of usage, function and metabolism.
Urbanistically the building is a four storey over basement, L shape, block, folded to maximise south facing area while respecting the building line, facing east, of the street. A masonry base supports a 3 storey timber frame superstructure, finished in render and timber and topped by a curved green (sedum) roof. Its design integrates garden terraces and solar panels into the upper reaches of the building. One of the three backland plots runs through to include a three storey building on Camden Street which was regenerated over the last few years by Kevin Quinn, Solearth and Daintree Ltd.
Energetically the building makes a large contribution to its own space and water heating needs. Space heating is generated by ground source heat pumps from three closed loop (200m deep) boreholes. The heat pump is (very conservatively) rated at a COP of 3 which means that for every unit of electricity in we will get 3 units of heat energy out—which is actually up to 10 times more efficient than electrical heating (the norm in most commercial apartments) when power station and transmission inefficiencies are taken into consideration. Ultimately the heat pump will be powered by renewable electricity, bought through the national grid. Six solar thermal panels (17.5sqm) integrated onto the building’s elevations and terraces will contribute to meeting the hot water needs. A gas fired high efficiency boiler provides back-up to both the heat pump and the solar hot water systems. While the solar thermal panels will meet up to 60% of hot water needs over the year, there may well be more hot water than required in summer.
Heat was to be distributed in under-floor heating but this was excised in a value engineering exercise which, with hindsight, has not been economically justified.
Most of the apartments in Daintree are designed to make use of heat gains from sunlight through classic passive solar design approaches; larger windows to the south, less glazing to the north and so on. This aspect should allow a large proportion of the space heating to be met passively in those areas. In the commercial parts of the building servicing is largely passive also; natural day-lighting is the objective in the large ground floor workshop and display area, which benefits from high floor to ceiling heights with clerestory and roof windows ‘stealing’ daylight as often as possible. Ventilation relies on natural buoyancy with fresh air being fed in through the basement, and drawn out at high level through fenestration (extract in the basement only is also mechanical).
Constructionally, the building is a combination of masonry and timber frame, the masonry being to basement and ground floor. In the upper three floors the building’s fabric is highly efficient, particularly utilising the full benefits of the timber frame construction method. Here 140mm timber studs filled with sheep’s-wool insulation are supplemented by an additional 38mm of wood fibre insulation (doubling as a service cavity) to lead to a heat retention of 33% better than building regulations (0.19W/msqK). The timber construction also of course allows us create a breathing wall, which allows vapour and humidity from both inside the wall and inside the space to diffuse outwards while preventing air leakage. This ‘breathability’ is critical in green buildings as part of the initiative to create healthy interiors now that the full impact of indoor air quality problems borne of pollutants in construction generally, paintwork and furniture, not to mention conditions like asthma, sick building syndrome and so on become more and more evident. Internal walls and floors are insulated with cellulose insulation and acoustically isolated using rubber-cork based matting.
The walls, structure and cladding make primary use of Irish (as a preference), or FSC certified, timber and use ‘panelvent’ sheeting as their outside layer, protected by a ventilated cavity, finished either in Irish cedar or in lime render on a Heraklith wood-wool slab system, as weather skin.
Preferences among the design team for low energy and sustainable materials were pressurised by value engineering and criteria had to be modified from a policy of eliminating problematic materials to minimising them. PVC has been avoided (it is used in wiring/conduits and some pipe work only), formaldehyde glues have been reduced and high-energy materials like aluminium and stainless steel designed out. The project involved 4 major concrete pours, one of which used ‘eco-cem’ a cement that displaces climate changing, C02 heavy Portland Cement with ‘ground granulated blast furnace slag’ (GGBS), a by-product of steel production. Most of the render used was lime based, again to improve flexibility over the timber frame and to reduce the building’s C02 debt. In fact the only high-energy material used is copper for copings and rainwater goods. This has been done quite intentionally because copper is one of the few materials that is both easy to re-use without down-cycling it and accessible in a salvage operation, and the economic incentive to re-use it increases with time. Also it adds just a touch of texture and delight.
Recycled and salvaged materials in Daintree include floor finishes which are of salvaged pine. Also balustrades will be clad in re-used bamboo, acquired after the Nissan Art Project (‘Bamboo Support’ by artist Dan Shipsides) on the old Carlton Cinema in 2000.
In terms of health, all internal finishes will be organic paints, and breathable waxes. Daylight reaches all habitable spaces while some internal bathrooms are day-lit using solar tubes from roofs up to 3 meters above. Kitchens in the apartments include special recycling cabinets which will integrate with the various recycling areas in the courtyard outside.
Green roofs, being usually reliant on PVC or petro-chemical based membranes, have dubious claim to being green in and of themselves. However in the city where habitat is scarce, heat island effect is perceptible, and water runoff is a problem—green roofs hold and re-emit through evaporating 70% of incident rainwater—they can be seen to be an ecological benefit and Daintree’s roofs and terraces do not use PVC based membranes. The green roof had to optimise between a high arch facilitating an efficient load path, to enclose as much space as possible, and flatness, as green roofs cannot easily be used over 60 degrees. The specification selected used a green mat which was rolled down the slope/ curve and which at the time of writing is largely successful. The hot summer has probably stressed the plants but re-planting in a few small areas will rectify this.
Water conservation in Daintree is first addressed by minimisation; using concealed cistern dual flush toilets to reduce demand. Most of the rainwater collected on the terraces and courtyard, as well as any runoff that comes from the green roof, will flow along a sculptural gutter designed to edge the solar terrace and be stored in a ‘green’ water tank for use in the buildings WCs and gardens. On site treatment of black (faecal) water was originally proposed but for budgetary reasons was not constructed.
The courtyard in Daintree is edged to the south by an element known as the ‘green gantry’ which houses 21 individual bicycle ‘cabins’, and at an upper level a gantry for plants where species that encourage birds and insects will be cultivated. More of the bamboo will be used here. The landscape plan also includes a number of areas for composting of organic waste.
Daintree has a simple BMS system. All heat and water services to different parts of the building are grouped and metered for accurate charging, though the exact nature of how this will work depends on the composition of a management committee once the building opens.
The client chose to work with the Premier Guarantee insurance scheme instead of Homebond as it was felt that Premier’s openness to look at original and bespoke technical details and specifications was more suited to an architect designed, site specific building.
A number of elements that would have made the building even more innovative were dropped over the development period. It had been proposed to use an eaves mounted heliostat (sun tracking mirror) to bring south light into the north facing light-well of the workshop, but this was abandoned. Early research on creating a radiant earth floor with pre-cast earth panels (moulded with grooves for underfloor heating tubes) sourced in Germany also proved prohibitively expensive.
The intention to treat black water on site was always an ambitious one, and though included in the planning application (and crucially granted planning), research during detail design showed that that the only approach that was suitable, a system known as a ‘Living Machine’ ™ would work most economically at a larger scale. As envisaged it would have provided full on-site treatment to all the grey water (sinks and showers) and black water (toilets) on a higher storey of the green gantry.
Original hopes that the salvaged bamboo could be used as load bearing structure suffered from lack of information as extensive research failed to reveal the species of the bamboo plant, precluding professional load calculations and durability predictions.
In terms of services the problems of meeting regulations whereby any cavity containing a gas pipe must be ventilated would have meant threatening the building’s insulation and acoustic integrity and so gas supply for cooking was reluctantly dropped. A simpler layout where kitchens are always positioned on vertical service risers would have eliminated this problem.
The most nerve wracking part of the job was the question of dimensional co-ordination between the timber frame template and the first floor slab (the base for the frame). Site dimensions would normally be taken before such a critical element goes into production but of course the whole idea of timber frame construction is that the timber frame is ready to erect once the concrete sets, and so it must begin fabrication long before the slab is even poured. Little tolerance is possible and breath was held as the first parts were assembled on site. Hindsight might also suggest that the intricate and complex nature of the design was not an ideal layout for timber frame but this was driven by the requirement to maximise site development and timber frame has huge advantages in terms of insulation and healthful construction so the marriage, though ‘forced’, will hopefully be fruitful.
Another original idea had been to ‘dump’ the excess summer hot water from the solar panels into a communal hot tub for residents on a shared -but secluded! – terrace, which would certainly have shown that sustainability doesn’t have to mean ascetic, however concerns about Legionella prevented this.
Once on site, the building process has been remarkably smooth due mostly to the can-do attitude of the general contractors Cunnane and Donaghey. Below ground works were uncomplicated (for a city centre site) and the timber frame was erected rapidly justifying the effort that went in to pre-fabricating it on speed as well as ecological grounds. Cunnane and Donaghey have been both co-operative and creative in overcoming problems the design team and client foresaw, and in pointing out and solving ones they didn’t!
Economically the project makes sense. While the refusal of the original design’s fourth floor knocked 4 apartments out, stressing the economies of scale the project is turning out to be as commercially viable as a comparable conventional development. It might be even more viable depending on the sales strategy and the relevance buyers place on ‘buying out’ the risk of future fossil fuel price rises. Important ecological innovations such as reduction of problematic materials and use of recycled and organic finishes were shown to have a marginal affect on cost.
Sustainable Energy Ireland (SEI) provided €5,000 per apartment as part of their House of Tomorrow grant and the finished construction cost of the project will be in the region of €2180 per sqm (ex vat and based on gross floor area). This actually shows that the commonly held assumption that there is a large premium on ecological innovations in building is somewhat false. The marginal extra cost of the advanced construction techniques and technologies chosen will be far outweighed by the benefits to health, running costs, asset security and well-being and I’m confident that the units in Daintree will be as sought after, and will change hands as rarely, as those in the Green Building, Temple Bar.
The project’s long incubation period, going back to 1996, was born of multiple feasibility studies for different sites, a long period of brief development (by design!), multiple planning applications and an appeal, a long- and ultimately fruitless- search for a development partner, and of course the involved process of technical research and solutions translation, one would expect, but it’s been worth it all.
Daintree falls somewhere in the middle of a spectrum that stretches from the non-green but nonetheless high design of recent high-end housing to the green buildings of the future—what we here in Solearth call ecological or ‘vital’ buildings that are restorative to ecology instead of being simply ‘less bad’ to it. And while Daintree only provides some of it’s own energy and water needs and so on, whereas vital buildings would actually create more energy, heat, water and air (and treat more than their own waste/ wastewater) it is probably the greenest housing in the country, and more than that will in all likelihood be a joy to live and work in. We’re thankful to everyone who helped.
Apartments in Daintree will be on sale by estate agent Felicity Fox from October.
Project Team:
Architects:
Solearth Ecological Architecture: Mike Haslam, Brian O Brien, Katie Elmore, Eoghan O’Shea, Ruth Fortune, Ruth Kealy, Esteban Diaz de La Vega, John Quinn
Architectural Consultants (2000-2002):
Adrian Joyce Architects
M&E:
Buro Happold; Susan Cormican, John Connolly.
Structural/Civil:
Buro Happold; Chris Bakkala, Bilal Aboujahja
Quantity Surveyors:
Gardiner and Theobald; Kevin James, Peter Devcich
Main Contractor:
Cunnane and Donaghey; Jack Cunnane, Greg Donaghhey, Barry MaCormac, Gabriel Seery, Sean Haberlin
Selected sub-contractors and suppliers
Mechanical sub-contractors:
McGratten Kenny
Electrical sub contractors:
This email address is being protected from spambots. You need JavaScript enabled to view it.
Timber frame:
Riverview
Green Roof:
Bauder
Insulations and membranes:
Ecological Building Systems
Sheep wool Insulation:
Ochre wool
Cellulose insulation:
Polypearl
GGBS cement for concrete:
EcoCem
Solar Thermal Panels:
Veissman by Precision Heating
Heat Pump:
Unipipe
- Articles
- Case Studies
- Daintree
- sustainable design
- Dublin
- green roofs
- timber frame
- passive solar design
- heat pump
- Solearth
Related items
-
Up to 11
-
It's a lovely house to live in now
-
We Build Eco flat pack timber frame partnership gathers pace
-
Mass timber masterwork
-
AECB conference to showcase timber innovation
-
Heart of oak
-
Welsh social housing to embrace passive house, timber & life cycle assessment
-
Cambridge chooses passive house comfort for Kings’ College students
-
Pitch perfect - Beguiling Dundee passive house puts wood into woodland
-
Above the curve - Limerick passive house showcases precision timber engineering
-
COP26 house to showcase fabric first, low carbon build methods
-
Boxing clever