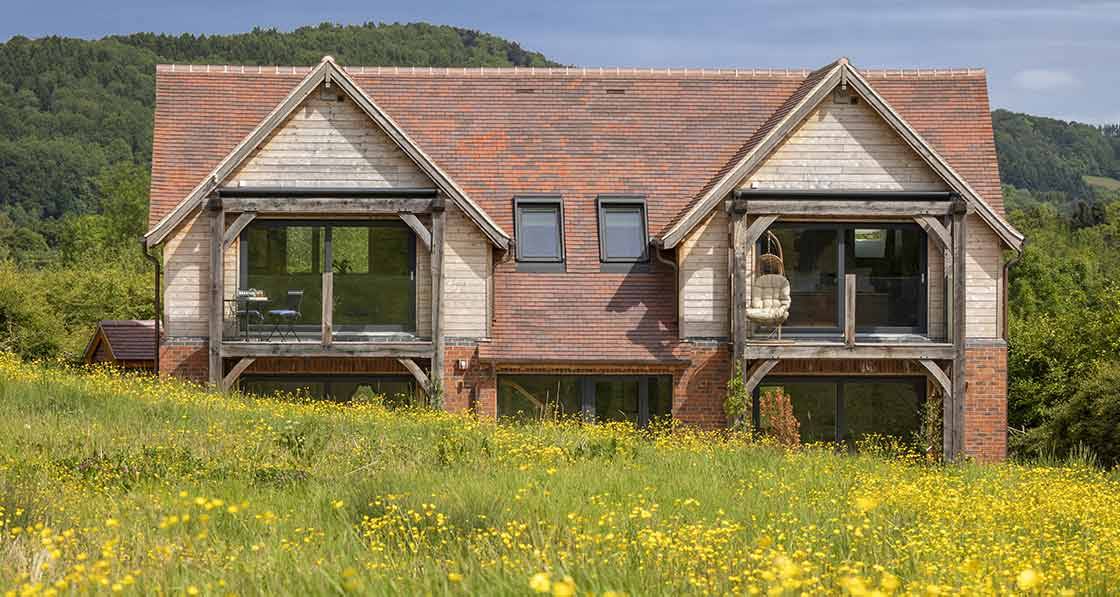
- New build
- Posted
Heart of oak
A striking new oak-framed passive house in an area of outstanding natural beauty in the English countryside has just opened its doors to the public, and already there has been a flood of guests seeking to experience life in a passive house.
Click here for project specs and suppliers
Building: 182 m2 detached B&B
Method: Oak frame
Location: Malvern, Worcestershire, England
Standard: Passive house classic certified
Energy bills: £25 per month for heating, hot water & cooling (see ‘In detail’ for more)
Andrew and Linda Burnett have been on quite a journey.
When they began looking for a retirement home near Malvern, in Worcestershire, back in 2013, their aim was simply to purchase a house in the area that they could convert into a bed and breakfast. But they ended up opting to self-build the first oak-framed passive house B&B in the UK. An eight-acre field with 700 pear trees, 75 plum trees and seven beehives was not part of the original plan either.
“When we set out we’d not thought about building an environmentally friendly house and we hadn’t even heard of passive houses,” says Andrew. “But we’ve shifted the whole idea of our bed and breakfast now. All but two of the guests staying since we opened at the beginning of July have done so to experience staying in a passive house, and to ask us about our experiences of self-build.”
As for the land attached to their house, it has brought about a complete change in lifestyle. “Our old house in Kent had a third of an acre with one plum tree and I said to Linda, ‘this grass cutting is getting a bit much at weekends, let’s look for something smaller’. And we ended up buying part of a former fruit farm with two orchards, which we’re now restoring,” says Andrew.
“We’re also turning a four-acre field into a wildflower meadow and we’ve planted new hedges. I’ve learned to use a chainsaw, and I own a compact tractor and gigantic lawnmower. A beekeeper comes to look after the bees, and we get annual rent of two jars per hive. We’re making plum and damson jams and more things with pears than you can throw a stick at.”
When their search began for a new home, the couple were living in a village in Kent. To make it easier, they relocated to a rented bungalow near the spa town of Malvern, in Worcestershire, where Linda grew up.
This article was originally published in issue 39 of Passive House Plus magazine. Want immediate access to all back issues and exclusive extra content? Click here to subscribe for as little as €10, or click here to receive the next issue free of charge
The couple visited a few barn conversions and liked the idea of a house with exposed wooden beams. But no suitable property was available and the idea of a self-build became more attractive. In 2015, Andrew and Linda visited a self-build exhibition at the NEC in Birmingham, where they came across Oakwrights, a Herefordshire-based oak frame design-and-build practice. There were three specialist providers of oak-framed houses available, but Oakwrights was the only one offering their own insulation and encapsulation system as well.
Oakwrights’ founder Tim Crump brought up the idea of passive house construction.
Andrew and Linda liked the idea and began to do some research. Initially the appeal was the promise of exceptionally low heating bills during their retirement. The next step was to visit and stay in Oakwrights’ show home in Herefordshire. “After we stayed in The Woodhouse, we both said, ‘that’s it, that’s what we want!’” says Linda.
The show-house gave the couple a clear direction forward. They liked its oak framed gable ends and traditional tiled roof. They decided they wanted a brick finish on the ground floor and timber cladding above, which would fit in with the barn conversions in the local area. But they still needed to find a plot within a ten-mile radius of Malvern, and that did not prove easy.
Andrew was working outside the area as a public health consultant, so Linda took charge of finding a site. It was practically a full-time job. She spent a year trawling through websites for hours every day. Finally, after a couple of near misses, she spotted a large plot in an area of outstanding natural beauty (AONB) between the Malvern and Suckley hills. The picturesque site with its panoramic views and tranquility won them over and their offer was accepted in October 2016.
The site had existing planning permission for a smaller two-storey dwelling and the previous owner had begun excavating part of the valley in preparation for that build. But the design for the new oak frame passive house was substantially different, and a new application had to be submitted.
Based on Andrew and Linda’s wishes, Oakwrights’ in-house architectural team designed the house with the living space upstairs to offer panoramic views. Their en-suite master bedroom is also upstairs and has a walk-in dressing room. Meanwhile, the two en-suite guest bedrooms are downstairs, along with a home office and the large hallway. There is space to install a lift one day too, if necessary.
The Burnetts originally wanted to build a four-bedroom home, but later opted to reduce it to three, which allowed Oakwrights to design larger bedrooms and left space for a double-height hallway with a “bit of a wow factor”.
Oakwrights also included two south-facing gables and a rustic tiled roof, which helps the home to blend into its setting. “There are also an east-facing and a west-facing gable ends, the four gables creating an intriguing roof externally and substantially adding to the attractiveness of the high ceilings in the upstairs rooms,” Andrew says.
The south elevation has four large, tripled- glazed lift and slide doors alongside a triple-glazed front door and two roof lights. The emphasis was on positioning windows, doors and balconies to take advantage of the views of the hills and garden.
Construction in progress
https://mail.passivehouseplus.co.uk/magazine/new-build/heart-of-oak#sigProId5dbb6f671c
“There’s an Oakwrights vernacular running through all our designs. It uses areas of oak outside, as well as large and well-proportioned windows,” says Oakwrights architect Craig Alexander.
While the dwelling that was originally intended for the site had a north-south axis, with large east and west facing facades, this would have presented an overheating risk from low-angle morning or evening sun. So Oakwrights’ design flipped the main axis to east-west, giving the house a large south-facing façade (within 30 degrees of due south is considered ideal for a passive house). “We balanced potential summer heat grains through the south-facing windows with the introduction of shading from the balcony structures, with integrated blinds above,” Craig says.
Planning permission for the build was achieved without any issues even though the use of cellulose insulation to achieve onerous U-values meant having thick wall and roof build-ups, and consequently, increasing the overall size of the house so as not lose internal floor space. Legal complexities held the project up and it was not until April 2018 that the first spade went into the ground.
Andrew and Linda chose a young and enthusiastic firm of builders called Furber Young, which turned out to be one of the best decisions they made.
“While Andrew was away I came to sit in the field and watched the build almost every day. It was wonderful to see the oak frame being pulled into place by the crane. You could see the markings on the beams showing where they needed to go. It’s a shame Andrew couldn’t watch, but I filmed it for him,” Linda says. “When I came down I would bring cake and everyone was friendly and welcoming. The builders had all been at school and college together. They were great friends and there were a few stag-dos during the build. They even came across at weekends specially to show Andrew what they’d done.”
Andrew and Linda had planned the build meticulously together with Furber Young, Oakwrights and Green Building Store, who provided the mechanical ventilation with heat recovery system (MVHR) and the triple- glazed doors and windows. As a result, everything went smoothly and the house was completed a week early in just 11 months.
The work also came in on budget. Project costs were £699,000, added to the land costs of £413,00, so around £1.1 million in total. Andrew and Linda moved in on 5 March 2018. At first, they could barely believe they owned such a property. “For weeks it felt like we were on holiday. It seemed so fantastic, we thought the house was not really ours and any minute we’d have to pack up and leave,” says Linda.
The MVHR system keeps the house feeling fresh. Meanwhile, a ground source heat pump takes heat from the field to warm up the hot water and the underfloor heating in the hallway and bathrooms. Oakwrights also designed an enhanced version of their WrightWall Natural and WrightRoof Natural encapsulation system to seamlessly wrap around their frame, which is prefabricated in their Herefordshire workshops and includes recycled paper cellulose insulation.
While working at home during the second Covid-19 lockdown, Andrew enjoyed walking barefoot on the warm tiles.
The house was certified to the passive house classic standard in September 2019. According to Andrew, the house is performing better than predicted in PHPP, the passive house design software, for both electricity consumption and overheating. “PHPP stipulates that overheating must not exceed 25C for more than 10 per cent of the time. Our estimation was for 1.9 per cent, but we’ve had data loggers measuring internal and external temperatures every 30 minutes and our overheating over 12 months was 0.57 per cent, which is absolutely brilliant,” he says. “And also, for electricity the PHPP predicted 98 kWh per square metre for everything, whereas our level was 61.65 kWh.”
The Burnett’s current ‘green’ electricity supplier predicts their annual electricity bill will be £1,560, which covers all their energy costs.
Any other energy required to heat the house comes from the sun, people in the house, the heat output from household devices, and recovery of heat from air removed in winter.
Back in 2014, in the couple’s Kent house, which was about 140 square metres rather than the current 200 square metre house, they paid more than £3,500 for energy. But their oak-framed house is as much an aesthetic experience as it is thermally efficient.
Andrew and Linda particularly enjoy having two balconies at the front. “They provide shading from the summer sun, but they make the house look more interesting. We frequently eat on one balcony and we’ve put comfortable chairs on the other one. It’s idyllic sitting there with a single malt enjoying the views across the fields,” says Andrew.
“The wildlife is also incredible. There are birds of prey and swallows in the sky and we see deer coming out of the woods. A family of badgers arrives every night and we have visits from a little fox. All of that is easy to see from the house, especially in the living room with the windows that go right down to the floor. But the views are incredible everywhere.”
Embodied carbon
Oakwrights commissioned John Butler Sustainable Building Consultancy to analyse the embodied carbon of the house, using PHribbon. The analysis included the substructure, the superstructure (excluding stairs), internal walls and intermediate floor, wall and ceiling finishes (but not floor finishes) and building services. The services included the ground source heat pump, heating and hot water pipes, underfloor heating system, but not the external collectors, or the associated excavation. The MVHR system is included, along with the stainless-steel ductwork. Electrics were not included.
Internal doors, baths, and sinks were also included, but the kitchen fit out wasn’t included. The building’s timber windows and MVHR system were assumed to need one replacement each within the 60-year time period for the LCA, though it was assumed that the ductwork would last for 60 years. The heat pump was assumed to need two replacements. All other components were assumed to last for 60 years or more.
Based on these assumptions, the building achieved a cradle to grave score of 71.1 kg of CO2e, or 339 kg CO2e/m2 GIA, comfortably beating the revised RIBA 2030 Climate Challenge target of 625 kg CO2e/m2. The figure for module A alone – which deals with emissions up to the point of practical completion of the building – is 274 kg CO2e/m2 GIA, with a further 270 kg CO2e/m2 GIA sequestered in the building’s timber, meaning that if it was permitted to engage in carbon accountancy sleight of hand and net sequestered emissions off against upfront emissions, the two figures would almost cancel each other out. Instead, it is considered that the sequestered CO2 is released into the atmosphere at the building’s end of life. Even if the CO2 sequestering products were assumed to be reused or recycled, the amounts sequestered would pass on to that future use, meaning that in the context of this building’s LCA, it’s effectively no different to the products being incinerated at their end of life.
The A1-A3 emissions (the materials, from cradle to factory gate) for the as built external walls comes out at 10.8 tonnes of embodied CO2e – compared to 21.7 t for a rendered cavity wall alternative of the same walls.
Selected project details
Clients: Andrew & Linda Burnett
Architecture & passive house design: Oakwrights
Civil & structural engineer: J Turner & Associates
Main contractor: Furber Young Developments
Airtightness testing: db Air Tightness Testing
Build system supplier: Oakwrights
Airtightness tapes, membranes & wood fibre insulation: Ecological Building Systems
Airtight OSB: Medite Smartply
Additional airtightness tapes: Siga
Wall & roof insulation (cellulose): Isofloc LM, via Oakwrights
Insulated foundations: Isoquick
Windows, doors & MVHR: Green Building Store
Roof lights: Velux
Shading: Solihull Blinds Ltd
Ground source heat pump, DHW tank, underfloor heating: Energy Zone
Lighting: Mr Resistor
Wastewater treatment: Conder sewage treatment unit, via Furber Young Developments
Mortgage: Ecology Building Society Self-build site insurance and structural warrantee: Protek
In detail
Building type: 182 m2 (treated floor area) detached, oak-frame, certified passive house Location: Storridge, Malvern (Malvern Hills Area of Outstanding Natural Beauty)
Completion date: March 2019
Cost: £1.106m (£699,000 for the build, £413,000 for the site)
Passive house certification: Certified
Space heating demand (PHPP): 13 kWh/m2/yr
Heat load (PHPP): 10 W/m2
Primary energy demand (PHPP): 108 kWh/m2/yr
Heat loss form factor (PHPP): 3.06
Overheating: 1.9 per cent of the year >25C (projected in PHPP); 0.57 per cent (measured) Number of occupants: 2 + B&B guests (PHPP completed based on 4 occupants)
Airtightness (at 50 Pascals): 0.57 m3/hr/m2 Energy performance certificate (EPC): B (89) Total electricity consumption: 8,366 KWh per year for all energy (29 Oct 2019 - 30 Sept 2020), equates to 45.93 kWh per m2 treated floor area.
Energy bills (measured or estimated): From Oct 2019 to Sept 2020 Andrew and Linda paid £1,289 for the above quantity of energy (£107 per month), including all charges. The ground source heat pump consumed 1.489 kWh over 12 months up to 7 August 2021, so on the same tariff it would cost £300 (or £25 per month) to run the heat pump for space heating and cooling, and domestic hot water. Tariff rate of 19.943p per kWh inc VAT used.
Thermal bridging: Use of low thermal conductivity cavity wall ties, thermally broken window frames, insulated reveals. Thermal bridge Y-values (figures in W/mK): eaves: - 0.009; verge: - 0.043; valley: 0.034; base to wall: - 0.028; normal corner: - 0.049; wall to flat: - 0.029; pitch to flat: - 0.003; reverse verge 0.027; reverse pitch to flat: - 0.80
Ground floor: Isoquick insulated foundation system incorporating 250 mm BASF Peripor EPS insulation completely encasing 300 mm reinforced concrete slab (with 50 per cent GGBS). U-value: 0.127 W/m2K
Walls: 12.5 mm plasterboard internally, followed outside by 46 mm service void battens with mineral fibre insulation (0.039 W/mK), 12.5 mm Smartply Propassiv airtight OSB3 board, all joints taped, 300 mm JJI I-beam frame factory filled with Isofloc cellulose insulation (0.038 W/mK) to 72 kg/m3, 60 mm Gutex moisture resistant insulation board (0.039 W/mK), Solitex Fronta Humida breather membrane, ventilated cavity, rainscreen of either: 102.5 mm brickwork (ground floor) or horizontal timber boarding (first floor). U-value: 0.10 W/m2K.
Sloping ceiling: 12.5 mm plasterboard internally, followed outside by 46 mm service void battens/ mineral fibre insulation (0.039 W/mK), Novia airtightness membrane, 9 mm OSB, 300 mm JJI I-beam frame factory filled with Isofloc cellulose insulation (0.038 W/mK) to 72 kg/m3, 60 mm Gutex moisture resistant insulation board (0.042 W/mK), Solitex breather membrane, vented pitched roof with battens, counter battens and clay tiles. U-value: 0.10 W/m2K
Flat capped ceiling: 12.5 mm plasterboard internally, followed outside by 100 mm service void battens, 12.5 mm Smartply Propassiv airtight OSB/3 board, all joints taped,2 x 300 mm JJI I-beam frame factory filled with Isofloc cellulose insulation (0.038 W/mK) to 72 kg/m3, 60 mm Gutex moisture resistant insulation board (0.042 W/mK), Solitex breather membrane, vented pitched roof with battens, counter battens and clay tiles. U-value: 0.07 W/m2K.
Windows & external doors: Triple-glazed, argon-filled, wood-framed windows and doors from Green Building Store Ultra range. U-value: 0.75 W/m2K (based on whole window U-value for standard window 1,230 mm x 1,480 mm for this range). The windows and doors have insulated frames, with Swisspacer Ultimate edge spacers; 52 mm thick triple glazed units.
Roof windows: Four Velux GGU passive house certified roof windows. U-value (whole window): 0.51 W/m2K (EN ISO 12567-2)
Space heating & cooling: Ground source heat pump 3-8kW Mastertherm modulating unit with desuperheater (COP 4.5) for domestic hot water and underfloor heating in the three en-suite bathrooms, hall and boot room. There are also electric towel rails in the three bathrooms. The heat pump also has a cooler battery that can drop incoming air temperature 5 to 7 C during hot weather.
Domestic hot water: Ground source heat pump as above heating 400 litre unvented Tempest cylinder from Telford Stainless Steel Ltd with two probes and a switch to enable heating of upper 200 L or whole tank. Tank also fitted with an electric immersion heater controlled by a timer to ensure once-weekly Legionella pasteurisation heating to just above 60C.
Ventilation: Zehnder Comfoair Q MVHR; Passive House Institute certified efficiency 90 per cent. Water: Low flow fittings used.
Image gallery
https://mail.passivehouseplus.co.uk/magazine/new-build/heart-of-oak#sigProId71b41d05a1