International Selections
Newly inaugurated RIAI president Paul Keogh argues that sustainable building is as much about site location and density as the minutiae of green materials and technologies. Keogh – who will select exemplars from further afield in a later edition of Construct Ireland – has chosen four diverse UK projects that integrate sustainability without compromising on design.
Maggie's Centre, Rogers Stirk Harbour + Partners
Paul Keogh: Maggie’s Centre sits on the grounds of Charing Cross hospital. In a fairly inhospitable environment it manages to make a building which is an oasis of calm and tranquility. It's a day-care centre – a drop in centre for people suffering from cancer, and provides social and therapeutic services within the city.
The floating roof and courtyard gardens are very distinctive. Environmentally its credentials are fairly impeccable – the building is entirely naturally lit. It's naturally ventilated too because all of the rooms open onto individual courtyard gardens, showing that even in difficult urban settings buildings can be naturally ventilated. The building uses cross ventilation and the courtyard form of the building to create through cross ventilation.
The choice of materials is impeccable – for example all timbers have been sustainably sourced. Insulation is all mineral fibre, the glass is low e argon-filled. Rainwater is recycled for landscaping and irrigation.
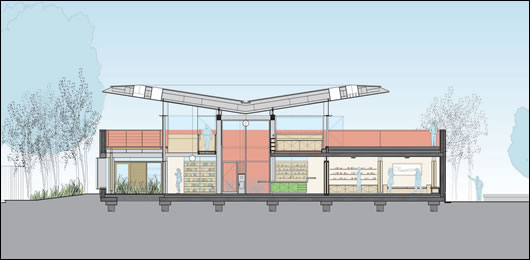
The floating roof uses unglazed rooflights to shelter external spaces and obscure views of the adjacent hospital
Project overview
The winner of the 2009 Stirling Prize, Maggie’s Centre is located on a difficult corner site in the grounds of Charing Cross Hospital, adjacent to a busy road.
The structure uses high embodied energy materials: concrete frame with a floating roof formed from a steel dia-grid supported by a concrete portal frame. The floating roof uses unglazed roof lights to shelter external spaces and obscure views of the adjacent hospital. This contributes to the shading strategy and helps to signal the idea of the centre as a marker or gatehouse for the main hospital building.
Emphasis was placed on selecting FSC-certified timbers from sustainable sources, using softwoods such as Siberian larch and birch-faced ply. Hardwoods such as European oak have only been used where hard wearing timber is absolutely necessary, for example for the thresholds. The majority of surfaces are naturally finished, removing the need for paint.
Mineral wool insulation is installed throughout walls, roof and roof terraces. The centre’s Schueco glazing system has thermally broken frames, low-e argon-filled glass and a centre pane U-value of 1.2 W/m2K. Designed to be air-tight, blower door tests on the centre are ongoing.
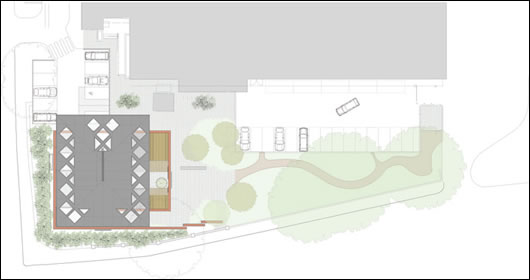
The ventilation is passive throughout – using cross ventilation – by the use of internal gardens and roof gardens. Each room opens onto an internal garden space.
A high efficiency domestic gas condensing boiler provides heating – through underfloor heating, supplemented by trench heaters built into the furniture on the first floor – and hot water. Zoned heating controls are installed with internal and external temperature sensors.
Energy efficient light fittings are used where possible. Low ambient lighting levels are used throughout with task-lighting used where greater lux levels are required. All external landscape lighting is on a solar clock.
Rainwater is harvested from the roof and used to irrigate the gardens and external landscaping. Dual flush toilets are incorporated.
High external walls and fast-growing birch trees planted along the edges of the centre protect the inner space from relentless daytime noise and visual distractions of the adjacent road on the ground and mezzanine levels.
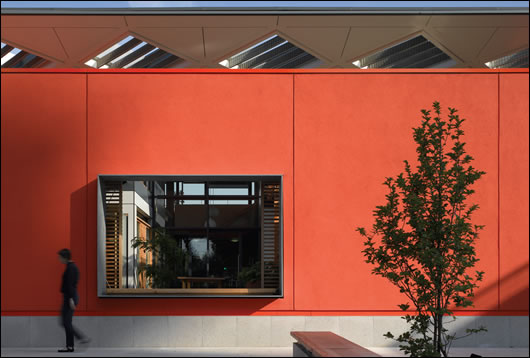
The use of courtyard gardens help to naturally ventilate the building and provide a tranquil setting
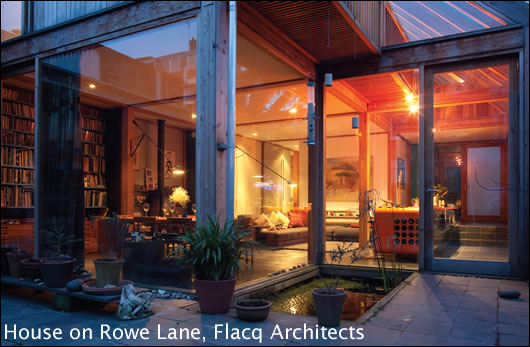
House on Rowe Lane, Flacq Architects
Paul Keogh: Flacq is a young practice which evolved out of the Richard Rogers office, and has a good track record in sustainable projects. For a one off house Rowe Lane is interesting because it's in a brownfield former industrial site in Hackney – a very constrained site. It uses its form fairly ingeniously to maximise the amount of daylight coming into the house and the relationship between internal and external spaces.
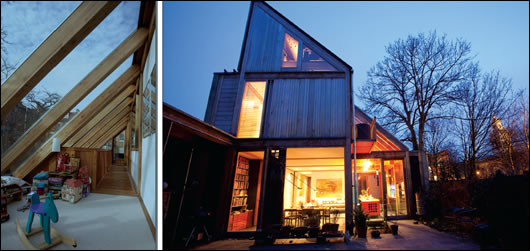
High levels of glazing maximise the daylight entering the house and the relationship between internal and external spaces
It’s built from a sustainably sourced prefabricated timber system – a post and beam structure which goes together ingeniously with metal connector plates. It’s effectively a terraced house, and on its two side boundaries it has diaphragm walls which stabilise the timber structure. It has a very highly insulated fabric.
For its heating system it uses a biomass boiler and wood burning stoves for local heat, but it has none of the obvious appearance of an eco house – it's urban and smart. It doesn't look like you’d need to wear sandals and make your own yogurt to live there.
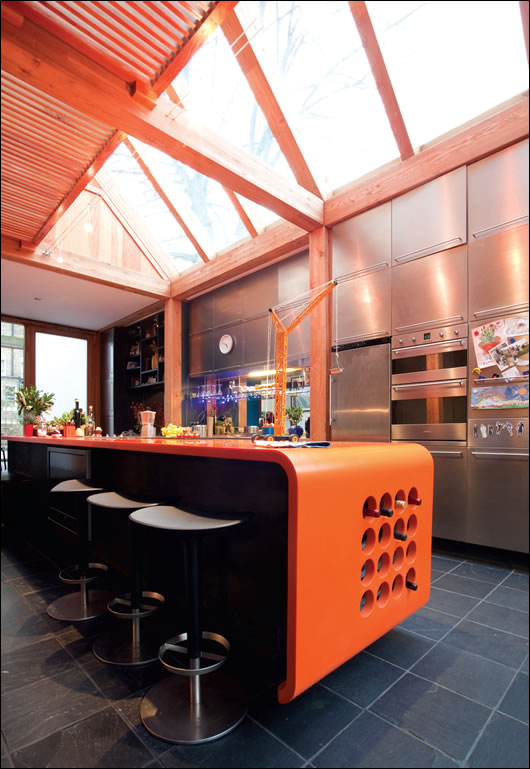
Project overview
Winner in 2009 of a London regional RIBA award and a 2006 Hackney Design Award, the house on Rowe Lane is sited on a difficult former industrial site. Seeing the opportunity afforded by external planting for shading, the design responds to an existing sycamore tree to the west – the foliage of the deciduous tree provides shading in summer, and the bare branches enable passive solar gain at winter.
The building – a Glulam Siberian larch post-and-beam timber structure laminated in Denmark, selected for durability and strength – is designed to be adaptable and deconstructable. Sustainably sourced timber is used throughout, including western red cedar hardwoods and douglas fir. Natural materials are used wherever possible, including slate flooring, lime plaster, and lime-based NBT paints.
Well-insulated 250mm deep breathable walls and roof combine NBT’s Pavitherm, flax and lime-based breathable plasters. Windows are cedar framed with fixed low-e argon-filled double glazing. The glazing fraction was increased to include top lighting – the extra heat loss is traded off against a reduced electrical light requirement. Conceived in 2003, the house was not specifically designed with air-tightness in mind.
Heating is provided by a 2.5kW wood pellet Baxi boiler and a multi-fuel Rais stove. Underfloor heating in installed throughout – embedded in a screed on the ground floor, and in a plywood board on the first floor. The installation of solar thermal to provide summer hot water is currently being planned.
Cross ventilation was designed using fixed glazing units combined with coloured ventilation flaps – effectively enlarged, manually openable trickle vents.
Rainwater is recycled from the roof for gardening uses. Other water conserving features include low flow taps and a dual flush toilet.
The Wembley primary school, Walters and Cohen Architects
Paul Keogh: One of the things I want to champion in my presidency is the establishment of joint committees with the Department of Education and the RIAI – as well as a similar committee with the Department of Health. The aim is to ensure that in the roll out of programmes the physical infrastructure is designed and built to the highest standards. There will be a conference later in the year – a first national schools conference – in this regard. According to the departments’ website, 1,100 schools are currently seeking major capital works, but only 52 are at detailed planning and construction. With pupil numbers set to rise by 30% in the next 20 years, we’ll need a further 5,000 places each year, on top of the retrofitting of the existing stock, not to mention removal of our disgraceful pre-fabs.
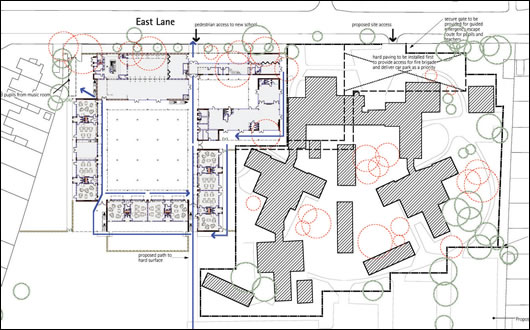
The school’s structure is reinforced concrete frame, using recycled coarse aggregates and high percentages of GGBS
The Wembley school is not particularly novel but it uses historic precedents to make a very beautiful place for learning. Principally it’s designed around two courtyards which create a very interesting microclimate and external spaces. All of the circulation is external. Each classroom is entered directly from the courtyard. It's that old cliché that the school is a microcosm of the city – the courtyard becomes like a town square. With the doors opening to the external fresh air is introduced when the u classes change.
It’s a fairly conventional structure – full-fill cavity wall and aluminium windows. However the school uses innovative radical energy technologies – fresh air is preheated or cooled via ground-coupled earth pipes to the main school hall.
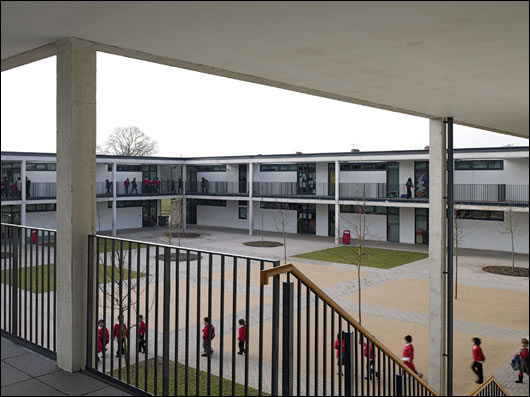
The school is principally designed around two courtyards which the classrooms open onto, creating an interesting microclimate
Project overview
Wembley Primary School is built on the playing fields of the existing school site. The original building was demolished and landscaped. The school achieved a Very Good Breeam rating – the UK environmental assessment tool for non-domestic buildings – with a score of 55.37%.
The structure is reinforced concrete frame – chosen for thermal mass – using recycled coarse aggregates with mass fraction of 66 to 80% combination of GGBS conforming to BS 6699.
All timber is FSC or PEFC certified. Junckers sustainably sourced sprung timber floor was selected for the hall, studio and circulation area.
The envelope is modestly insulated, including full-fill cavity wall insulation. The U-values are 0.35 W/m2K for walls, 0.20 W/m2K for the roof, 2.20 W/m2K for roof lights and 2.0 W/m2K for windows and doors. Room two of the school achieved a modest air-tightness result of 7.91m3/h/m2 at 50Pa.
Ventilation is mostly designed passive, with mechanical ventilation – and some heat recovery – in deep plan, toilet and changing areas. High and low level openings in classrooms induce buoyancy driven airflow in summer time, with manually controllable trickle vents and operable windows.
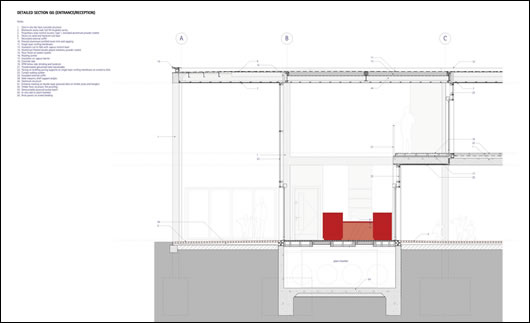
A section of the entrance/reception reveals the plant chamber containing the ground-coupled earth pipes
Heating and hot water is provided by three 150kW high efficiency gas boilers, with less than 20mg/kWh NOx emissions. Multi-zone heating controls with local sensors are used. The hall and the resource space are zoned separately from the rest of the school. A combination of perimeter/trench heating, built-in convectors and low surface temperature radiators distribute heat. The flow temperature is controlled by the outside air temperature and average indoor air temperature for each zone.
Ground-coupled earth pipes buried 1.5 to 2m beneath the courtyard pre-warm/cool the ventilation air before it enters the hall and resource area. This reduces the gas heating load considerably during the winter and provides cooling to internal spaces in the summer.
Lighting controls with presence and daylight sensors feature in the classroom and office area suspended lighting installations. Integrated photocells dim lighting output to complement natural daylight levels. Toilet lights are controlled by presence only.
Rainwater is recycled for flushing the WCs. The taps in the WC areas are non-concussive.
Accordia housing, Feilden Clegg Bradley Studios
Paul Keogh: Accordia is a multi-unit private and affordable housing development outside Cambridge. It’s high density, mostly consisting of houses. The urban master plan for Accordia is based on high density urban living, and proves that you can go high density without going high rise. The ten hectare site – with three hectares of open space – has an overall density of 40 houses per hectare, rising to 65 in the dwelling section. It has attractive pedestrian-friendly streets and open spaces, and the houses themselves are generously sized. There's a low parking ratio. Cars aren't all parked near the housing.
The houses are innovatively planned with internal courtyards and terraces instead of large back gardens. Spaces between the buildings are quite tight. We're crippled in Ireland by this rule that you must have 25m between opposing living rooms, and this – along with outdated road standards – is the reason suburbia here looks as boring as it does. Accordia is a high density urban housing model which, if applied here, would be immediately attractive to your normal middle class family. It isn't designed around the car – it's designed around attractive networks of pedestrian and cycle-oriented streets and spaces. It uses inherently environmentally sound terraced house types.
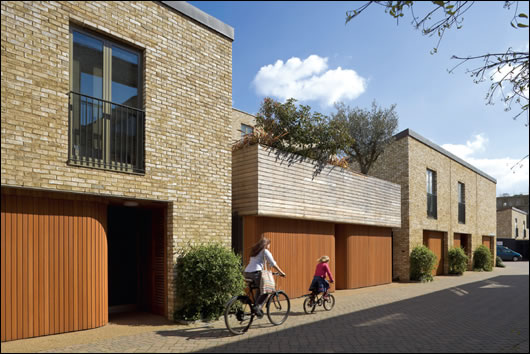
FCB appointed Alison Brooks Architects and MacCreanor Lavington Architects to design 10 and 25% of the housing respectively to bring variety
Project overview
A high density urban housing development, the first phase of Accordia was constructed between 2005 and 2006. Architects Feilden Clegg Bradley created a master plan based on access for pedestrians and cyclists rather than cars and designed most of the 212 houses and 166 apartments. FCB appointed Maccreanor Lavington and Alison Brooks Architects to design 25% and 10% of the housing, in order to bring variety to the scheme.
Accordia has picked up numerous awards, culminating in the 2008 Stirling Prize. An appraisal through Ecohomes – the UK’s environmental assessment tool for new housing prior to the introduction in 2007 of the Code for Sustainable Homes – gave the building a Very Good rating, scoring 64.9%.
The housing at Accordia is built from a combination of high embodied energy materials – prefabricated precast concrete, light gauge steel frame inner leafs and brick external wall, with some structural steel for apartment buildings.
UK sourced oak was used for balcony frames. All timbers used in kitchens and bathrooms, external cladding and internal joinery are FSC certified. Sustainably sourced timbers were selected for floors – with low VOC for kitchen and bathroom joinery.
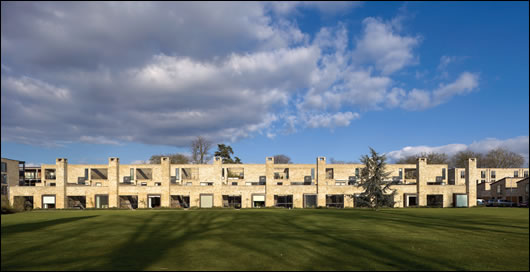
The development is set amidst large open areas and mature trees; UK-sourced Oak was used for balconies
Envelope U-values are over 30% higher than the requirements of 2002 UK Building Regulations, with walls at 0.27 W/m2K, roofs at 0.2 W/m2K and windows at 1.7 W/m2K. Pressure tests were carried out in accordance with the requirements of Ecohomes. FCB stress that the design included careful detailing to avoid cold bridging, with modifications to suit bespoke construction systems chosen by the contractor. The Ecohomes assessment lists the SAP u calculated CO2 emissions for the worst case of each dwelling type at less than 23.58kg/m2/yr.
The ventilation strategy generally relies on natural means via windows, with mechanical extract ventilation from bathrooms. The development’s compact urban form and mature trees reduce overheating problems.
90-95% efficient condensing gas boilers with less than 70mg/kWh NOx emissions were installed with underfloor heating and individual room temperature controls to main living and bedroom areas. Some residents have added solar thermal and PV systems.
Low energy CFL lighting was installed widely internally and externally, with daylight sensors controlling external lighting.
Water consumption is estimated to be less than 40m3 per bedroom per year, with low flow taps chosen for sinks and basins. The development uses sustainable drainage systems with ecological stormwater attenuation basins.
- Articles
- International green buildings
- Paul Keogh
- RIAI
- Stirling Prize
- Maggie's
- centre
- Argon
- Flacq
- condensing
- gas
- boilers
Related items
-
Big picture - Points of access to resilient living
-
Emma Stone show puts passive house up in lights
-
Big picture - Huff'n'Puff Haus - a straw bale passive house
-
Big picture - off grid passive house in British Columbia
-
EU proposes gas demand reduction plan till spring
-
International - Issue 39
-
Firebird rebrand emphasises sustainability & innovation
-
RIAI launches 2030 climate challenge
-
International - Issue 38
-
Grant invests in biofuel tech for oil boilers
-
International - Issue 36
-
International - Issue 35