- New Build
- Posted
EPA HQ
A new extension to the EPA's headquarters in Wexford lives up to the organisation's aim of environmental protection, boasting passive ventilation and lighting, a host of green technologies and a sustainable approach to landscaping.
If you expect any organisation to build green, it’s the Environmental Protection Agency. The new 2,800 square metre extension to the EPA's Wexford headquarters features solar PV, rainwater harvesting and wood chip heating. But perhaps its most outstanding green credential is that ventilation and lighting – typically two of the biggest electricity hoggers in office buildings – are largely provided passively.
Designed by an Office of Public Works team of architects led by Stephen Kane, the extension's slender design is pivotal to its passive energy strategies. At only 14m wide natural light can fill the office space, which is mostly open-plan. The extension's designers followed a simple principle: measure the height of your windows and double it – any surface within twice that distance from the glazing will generally receive sufficient daylight for working. With a tall glazed facade running down both sides of the extension, new workspaces are largely passively lit.
The slim design is equally essential for passive ventilation – open-plan areas benefit from cross ventilation, while closed offices are clustered separately as not to impede this. Before construction the designers simulated the effect of different glazing and shading options on internal temperatures using modelling software from Integrated Environmental Solutions. The goal was to ensure the building would meet the OPW’s key rule for natural ventilation to be viable: that the indoor temperature would only rise above 25C 5% of the time, and would never go over 27C.
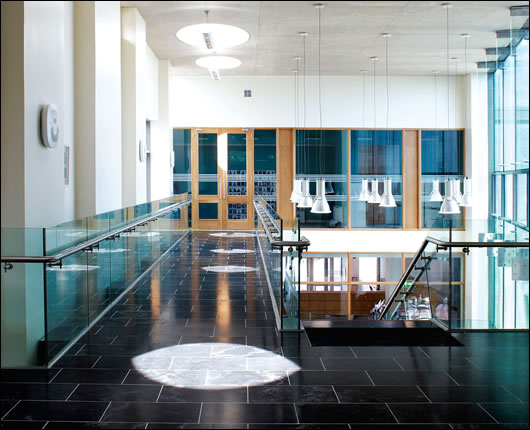
Artificial light will only switch on if natural light cannot meet the required demand. Occupancy sensors have also been installed and staff can dim lights manually
The OPW chose a combination of solar shading externally with automated high windows for day and night cooling – according to the modelling this should ensure the temperature rises above 25C less than 0.5% of the time in the open plan areas, and less than 1% of the time in the cellular offices.
The orientation – the main facades face north and south – is a key part of the cooling strategy. If the facades faced east and west, the sun would hit the east facade in the morning and west facade later in the day. But because they face north and south, potential overheating is only an issue on the south side, where vertical shading devices were installed outside the glazed-facade. "You only have to address the south facade, so management of your solar gains is much easier," says Jason Smith of Noel Lawler Consulting Engineers, mechanical and electrical engineers on the project. “Horizontal shading would have been ineffective against the low angle winter sun, and there’s no adjacent buildings to give you local shading either."
Staff can open low-level windows for simple cross-ventilation in the open plan offices, but u the glazed facade is automated too – high-level windows open at night to purge the building of excess heat if temperatures inside get too hot. The automated facade is also designed to interact with the building management system. “That’s so that you don't have a scenario where you heat the building and the automated facade is trying to extensively ventilate the building,” Smith says.
Cellular offices feature manually openable and automated windows too, while a passive stack effect ventilates the atrium – when it gets too hot a low-level vent on one side of the space and a high-level vent on the other open, drawing cool fresh air in at the bottom and pushing warm air out the top as the heat rises.
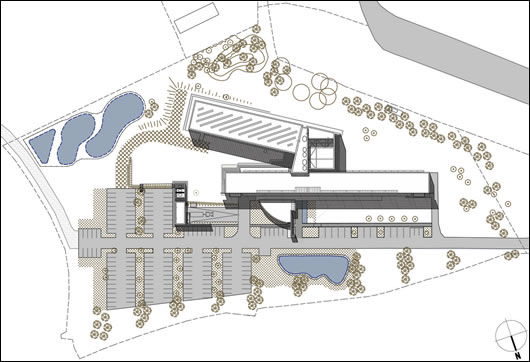
Passive ventilation and lighting may dominate, but active mechanical and electrical systems feature too. A digital addressable lighting interface (Dali) is used throughout the extension in conjunction with efficient T5 fluorescent lamps. The system is programmed to maintain a certain light level, and artificial light will only switch on if natural light alone can’t meet this. Occupancy sensors have been installed, and staff can dim lights manually. Lighting outside the building also features daylight and motion sensors. Overall, the energy efficient lighting is expected to save almost six tonnes of carbon a year.
Air conditioning is used to cool a communications room in the extension. While it’s usually u frowned upon by green-minded architects and engineers, the air conditioning system here has been designed with efficiency in mind – the heat it dissipates is recovered and used to pre-heat domestic hot water to 40C. Surplus heat is then directed to a firefighting pond outside, providing a passive source of cooling for the system and minimising its electricity consumption. Recovering heat from the air conditioning system is projected to save over half a tonne of carbon a year. High efficiency thermal wheel heat recovery ventilation features in the conference centre, library and toilet blocks.
A 400kW KOB Pyrot wood chip boiler, supplied by Clearpower, meets the building’s space heating and hot water needs. It features an automated rotary arm delivery system, and Clearpower’s Mike Shelley says it has an efficiency of 90 to 92%. The OPW chose wood chip over pellet primarily because of its lower carbon footprint – pellets are processed more – and because chips can be sourced locally. Using wood chip as a fuel rather than LPG (liquified petroleum gas) is projected to save 89 tonnes of a carbon a year.
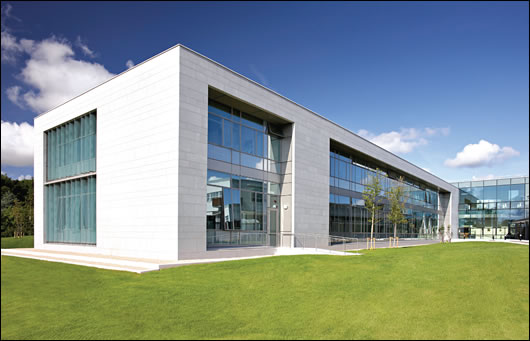
The full-height double-glazed facade comprises most of the walls of the extension
An LPG boiler acts as a back-up heating source, but the wood chip boiler should meet 90% of the building's heating needs. Heat is distributed throughout the buildings by standard radiators, though some fan assisted rads are used in the atrium where a higher output is needed to heat the large space.
The roof of the new extension features an extensive array of solar PV panels – estimates suggest it will generate almost 27,000kWh of electricity a year. Supplied by Coolpower, the panels face due south and are angled at 40 degrees from horizontal. The DC (direct current) generated by the PV array is converted into AC (alternating current) by an inverter/controller, which is then supplied to the building's electrical circuit. The PV panels are projected to save 10 tonnes of CO2 a year by displacing electricity that would otherwise be imported from the grid.
The full-height glazed facade comprises most of the walls of the extension – it’s double-glazed with low-e coatings and has an average U-value of 1.7 W/m2K. Opaque elements of the glazed facade have a U-value of 0.27 W/m2K, while mass concrete columns comprise the non-glazed parts of the extension – these are insulated externally to a U-value of 0.27 W/m2K, and clad with granite. Concrete is intentionally left exposed in many areas inside to provide thermal mass. All concrete – except for the concrete columns – contain’s Ecocem’s GGBS, a low-carbon alternative to Portland cement. Both the roof and ground floor are insulated to a U-value of 0.2 W/m2K.
A blower door test produced an air-tightness result of 2.98m3/m2/hr – Jason Smith says that keeping the building shape simple was crucial to achieving this, as was the attention to detail during the design and construction stages.
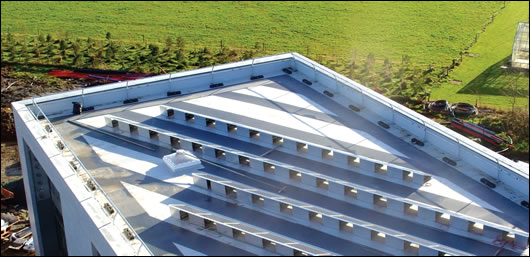
The roof of the extension features an extensive array of solar PV panels, supplied by Coolpower
The building features a rainwater harvesting system too, which collects rainwater from roof gutters and permeable paving, filters it and delivers it for use in non-potable applications such as toilets, wash basins and landscaping – and the firefighting pond that is used to cool the air conditioning system in the communications room. The rainwater storage tank can store sufficient water for 20 days use, while a borehole provides a back-up source of non-potable water during extended dry periods.
While the new extension is the most striking element of the project, the OPW also carried out refurbishment work on part of the existing building – about half the top floor – to test design strategies ahead of the main project. New higher spec windows were installed with both manually openable and motorised sections for ventilation, some cellular offices were removed to encourage passive ventilation and lighting, a brise soleil was installed to prevent glare and extra insulation was added around window openings.
Modelling suggests the extension will consume 52 kWh/m2/yr for heating and 54 kWh/m2 yr for electricity. Refurbishment of the existing building is expected to cut its heating demand from 89 kWh/m2/yr to 66 kWh/m2/yr. The new extension achieved an A3 Building Energy Rating, and it has projected carbon emissions – for space heating, hot water, ventilation and lighting – of 16 kgCO2/m2/yr, a carbon performance co-efficient of 0.23. The entire building scored a B1, with a projected carbon emissions of 31kg CO2/m2/yr and a carbon performance u co-efficient of 0.43.
The OPW embarked on an extensive consultation with EPA staff prior to finalising the design. The original building is a well-known symbol of the organisation, and the extension was designed to compliment both this and its surroundings – the Johnstown Castle demesne and gardens. A 400 acre estate of farmland, forestry, parkland and lake, the estate is home to Johnstown Castle, most of which was built in the early part of the 19th century. The estate is now the site of a Teagasc research facility, as well as the Irish Agricultural Museum.
In design terms, the building is similar to other OPW projects recently profiled by Construct Ireland such as the veterinary offices in Drumshanbo, Co Leitrim (volume 4, issue 9) and the Food Safety Authority building at Backweston, Co Kildare (volume 4, issue 5) – all are characterised by the slender design that facilitates passive ventilation and lighting. Extensive glazing at the EPA extension allows the office space to merge with the surrounding environment – the same effect is achieved by the transparent lift and glazing in the atrium.
The open courtyard between the new and old buildings was designed to embrace the surrounding landscape, creating views towards the old demesne woodland. As with the building, sustainable principles were applied on the surrounding 10 acre site, about 60% of which was landscaped. The OPW’s principle aims were to promote biodiversity and integrate the building into the rural landscape.
“The overall approach to the new planting was generally naturalistic further away from the building, with more rectilinear planting beds closer to the building,” says OPW landscape conservation architect Elizabeth Morgan.
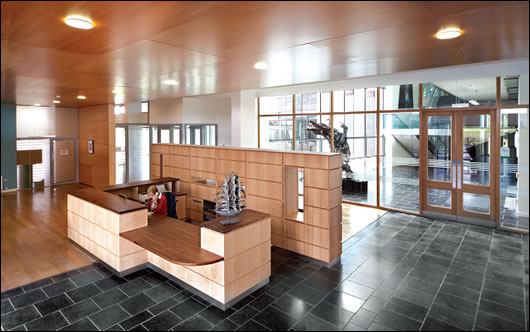
The open-plan office space maximisesnatural lighting through extensive use of internal glazing
Many existing trees in front of the building were in bad condition - these were re-located to other areas of the site. The courtyard was planted with birch, wild Irish cherry and a long perennial flower bed to enhance views towards the woodland. Clumps of native semi-mature trees such as hornbeam and scots pine were planted near the northern boundary to u provide screening of the building from a local road, while still allowing views out to the landscape.
A new mound was created on the southern boundary with the castle gardens – this was planted with semi-mature oaks and relocated ash trees to provide screening from a path in the gardens. The southern boundary was also planted with groups of native species such as alder, birch, oaks and hollies.
The area around the firefighting pond was planted with grasses and perennials such as miscanthus, molinias, panicums, iris and sedges. Further beds around the building and car park were planted with a variety of colourful flowering plants. In total 200 new indigenous semi-mature trees and large shrubs were planted, along with over 3,500 grasses and perennials and 8,000 daffodils.
Too often building in the Irish countryside has involved throwing up ugly, energy inefficient buildings that make no effort to fit with the surrounding landscape. But with detailed attention paid to landscaping, design quality, energy performance here at the EPA extension – and at their other recent projects in Drumshanbo and Backweston – the OPW continues to buck that trend.
Selected project details
Client: Environmental Protection Agency
Architects: OPW Architectural Services
Associate architects: Kavanagh Tuite Architects
Services engineers: Noel Lawler Consulting Engineers
Contractor: Mythen Construction Limited
Concrete / formwork: South East Formwork
Glazing: Architectural Aluminium Ltd / Kilkenny Aluminium
NV & window control: Windowmaster
Photovoltaics: Coolpower
Woodchip boiler: Clearpower
Landscaping: Tom Beckett Landscaping
- Articles
- New Build
- EPA HQ
- passive ventilation
- Office of Public Works
- environmental
- protection
- Agency
- Wexford
- Stephen Kane
Related items
-
Playing all the angles
-
Grant offers free home heating system design
-
Channel Islands gets its first passive house
-
Analysis: 12,000+ homes built in 2017 – as energy standards marginally fall
-
New homes data reveals extent of Irish low energy revolution
-
Ground-breaking housing scheme captures one developer’s journey to passive
-
BREEAM excellent building marries sustainability with world-class design
-
Our passive journey #3: Designing our family’s passive house
-
Our passive journey #2
-
One family's passive journey
-
Stunning Somerset passive house embraces wood and light
-
Low energy Tipperary offices go for gold