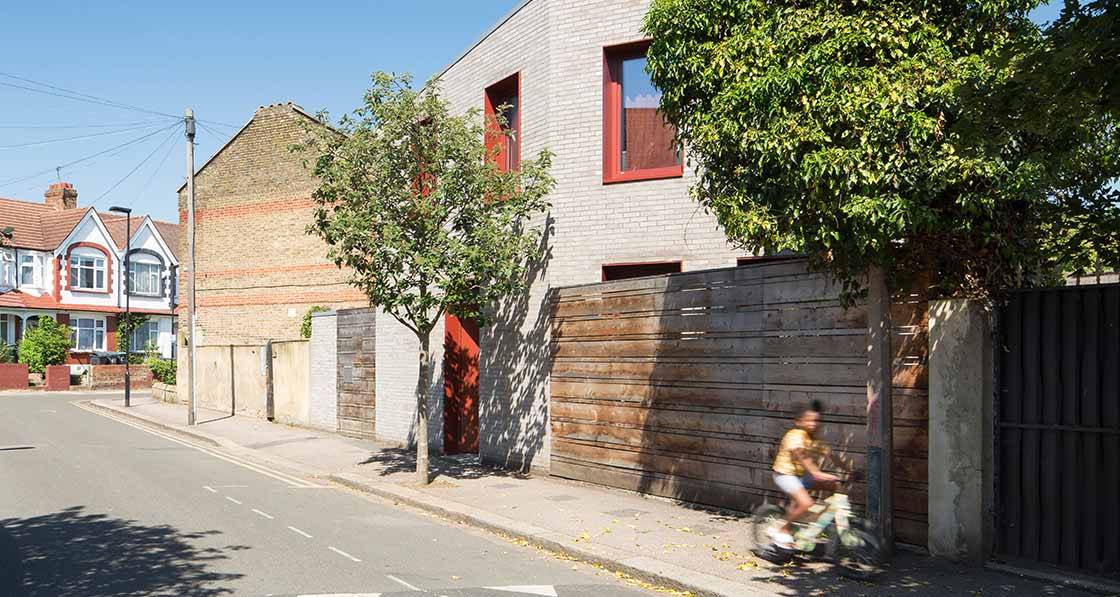
- New build
- Posted
Playing all the angles
Angle House in north London is a wonderful example of sustainable urban housing: modest in scale and built on a run-down site in the heart of north London, it boasts a passive approach to energy efficiency and some beautiful design touches.
Building: 110 m2 detached home and office
Build method: Brick & clay block cavity wall with timber frame elements
Site & location: Urban infill site, Tottenham, London
Standard: Fabric-first low energy dwelling (no specific standard)
Budget: £325,000 (build costs)
ENERGY BILLS £35 PER MONTH FOR ALL HEATING & ELECTRICITY (includes feed-in-tari", see ‘In detail’ for more)
The award-winning Angle House is a low energy dwelling sandwiched between Victorian terraces on a previously neglected site in Tottenham. The two-bedroom home and office was co-designed by Italian architect Andrea Carbogno and his partner, French architect Sophia Ceneda.
Although the couple now live there contentedly, transforming the original run-down plot into a comfortable home took longer than expected and provoked much stress. Not only did the narrow site present design constraints, but there were long delays, and the build stretched the project out.
“There were times when it was one of the most stressful experiences I’ve ever had. We were so invested in it as our personal project. But now it is all over living in the house is great,” says Andrea.
“The interiors are modern and it’s very functional. Everything is open space, and all the transition spaces are made use of, and are user-friendly. It’s big enough for large gatherings of family and friends, but not too big for two of us. We’ve designed it with lots of natural light and it’s tightly enclosed. But there are views out to back gardens on one side and at the front there’s a little courtyard with greenery.”
This article was originally published in issue 37 of Passive House Plus magazine. Want immediate access to all back issues and exclusive extra content? Click here to subscribe for as little as €10, or click here to receive the next issue free of charge
Both Sophia and Andrea had always wanted to build their own home. In part this was to take advantage of their skills, but it was also for cultural reasons. “I’m French, but my family is all from Italy, where it’s a longstanding tradition to build your own house,” says Sophia. “My grandfather built an incredible house in France and I always thought I’d build my own home. I just never thought it would be in Tottenham!”
Neither Andrea nor Sophia began their working lives as architects. Andrea studied accountancy in Italy, before leaving the picturesque Dolomites for London in 2000. For a couple of years, he worked in bars and restaurants.
Then, in 2003, he enrolled at the School of Architecture at London Met, where Sophia was taking the same course. She had arrived in London with a background in geopolitical studies and worked for human rights groups. But like Andrea, she found herself drawn to architecture, especially sustainable design.
The house was the winner of the dwelling prize at the 2020 New London Awards.
Before striking out on his own, Andrea worked for a decade for a London firm designing high-end residential homes. Then in 2014, the couple founded Carbogno Ceneda Architects, in Tottenham. Sophia still works full time as architect and sustainability lead at Glenn Howells Architects, but helps Andrea with business development and some design.
Angle House was the first time they designed a house together.
The couple began to look for a site to develop eight years ago while they were living in Sophia’s Tottenham flat. Her rule of thumb was that the combined cost of the land and the build should be “no higher than it would cost to purchase and refurbish a house in the same area”. Based on these parameters, they needed to find a bargain, but Tottenham was gentrifying fast and prices were escalating. The best site they could find for £100,000 was a section of the garden at the end of a row of terraces. It required a lot of imagination to see beyond the debris. “It had been sold 14 years earlier to a man from Birmingham doing shop-front glass glazing. There was a massive prefab concrete structure wrapping around a caravan, where he slept when he came down to work. There were lumps of concrete strewn on the floor,” says Andrea.
The site had a poor history in planning terms, and it became clear that it would be a challenge to get planning permission even for a modest two-storey structure. In 2013, the couple submitted a simple design that focused on massing, layout and orientation for outline planning permission. There was an agonising wait for planning, and once it was granted, the sale was rushed through.
Andrea and Sophia spent the next six months refining the original design in their spare time. In general, there was a lot of harmony between their ideas, and few disagreements. However, Sophia insisted on a staircase in the middle of the dwelling and Andrea refused to have any corridors. Sophia took charge of the sustainable elements. Having taken courses at the Centre for Alternative Technology (CAT) in Wales, she was cognisant of passive house principles.
Sophia opted for a zinc roof, although it was more expensive, and a smaller 20 square metre green roof at the back which is made of fibreglass and will eventually be covered in wildflowers. The couple opted for a hybrid construction, with a brick-and-clay block full-fill cavity wall on the ground floor, and on the first floor, a mix of this build-up plus timber frame wherever the footprint is set back from the ground floor wall. The house also achieved airtightness of 1.87 m3/m2/yr, though this was prior to completion, and it has not yet been retested.
All of these measures raised the energy performance to near the passive house standard.
It’s possible to deliver low-energy buildings without relying overmuch on technology.
“We aimed for passive house space heating at 15 kWh/m2/yr, and we ended up slightly above it at 27, which is 85 per cent less than a standard UK house,” Sophia says.
The tightness of the site demanded some ingenuity.
The road is L-shaped, and the house lies at the short end. It’s the only home on that side fronting the street. Immediately to the left, there is a terraced house, and to the right, there is a row of houses. The planners wanted the couple to set the front of the house back from the road, but they saw this as being against urban design principles, and during a redesign they had to negotiate the extent of this setback. “It’s like extending the street of terraced houses by adding a new unit at the end, however the unit is pushed back due to the triangulated shape of the site, because it’s too narrow at the front. We replicated the gable wall geometry of the end terrace to our street elevation, so there’s continuity to the sequence of angled roofs. Our house is subservient to the terrace which, as a design strategy, helps comply with planning guidelines,” says Andrea.
Most of the neighbours were excited when the two architects presented their plans. One of the neighbours said it was like watching an episode of Grand Designs right on their doorsteps.
One woman whose garden overlooked the new house was a bit concerned about light.
“But when she checked the design on the planning portal, she could see how the green roof would be set back from the rear elevation so it wouldn’t block out the light. Her response was ‘it will be much nicer than overlooking a dump yard’.”
In June 2014, the couple submitted their revised plan and received approval 12 weeks later. However, work did not begin on the development until October 2015. The initial expectation was that the build would take between 12 and 18 months. In the event, it went on for two-and-a-half-years and the couple didn’t move in until June 2018. “It was another stressful period. As architects, you are in control until a certain point, then you hand over the execution and so many points of conflict can erupt,” says Sophia.
We’ve designed it with lots of natural light and it’s tightly enclosed.
The main contractor for the structural works hired a team of builders based in Reading, over fifty miles from Tottenham. This restricted their time on site, and the truncated days meant the build dragged on. Sophia praises the contractor for executing the works well, “despite the builders being out of their comfort zone with a fabric first design like this”. There were also some delays due to a series of misunderstandings, such as when the builders assumed the ground floor slab was ground-bearing, when it was in fact suspended.
As planned another contractor was brought on to carry out the M&E works and internal finishes including the stunning staircase, but there were further delays. Sophia believes contractors in London often stretch themselves thin across multiple jobs, which can lead to delays. “These were the only times Andrea and I had arguments as we didn’t always have the same strategy for dealing with the contractors. However, on the whole the works carried out was well executed.”
The couple finally moved their belongings across to Angle House in the summer of 2018. After a few days sleeping on Sophia’s floor while the electricity supply was connected, they were finally able to sleep in their new 110 square metre home. The more spacious ground level is 75 square metres and would work as a self-contained one-bedroom flat. “An elderly couple could easily live downstairs as there’s a bedroom, bathroom and wheelchair access,” said Andrea. Upstairs there is a further 35 square metres of space, which is enough for a second bedroom with a bathroom and an office space that is separated from the stairs by timber slats. It could also be transformed into a third bedroom. “It’s not a large house, but it uses the space effiiently,” he says.
Sophia’s awareness of passive house principles paid dividends. Even when temperatures fell to zero in January this year, the couple only needed to switch the heating on for a couple of hours a day, and their annual bill for gas and electricity is a modest £400, excluding charges. The couple very rarely use the bathroom radiator upstairs, or the portable electric radiator they bought for the office. Though Sophia took the lead in developing the low energy aspects, Andrea is also passionate about sustainability. He recently took his exams as a passive house designer and intends to take his tutors’ advice to test the house using PHPP software against the Passive House Institute’s low energy building standard (a less onerous alternative to the classic passive house standard). “I’m hoping the course will set me up to expand the services we can offer.
I was drawn to passive house because it’s possible to deliver low energy buildings without relying overmuch on technology. But I’ve got a lot more detailed knowledge now,” he says.
The house was the winner of the dwelling prize at the 2020 New London Awards, and was shortlisted for small project of the year at the Building Awards last year too. The couple also achieved Sophia’s goal of not spending more than they would retrofitting a property.
The overall cost was £425,000, including a £325,000 mortgage in addition to the £100,000 cost of the yard. In 2018 the house was valued at £650,000. “We’ve proved you can still do something really nice in London for under £500,000, and the house is a case study demonstrating our skills as sustainable designers too,” says Sophia.
1 The run-down plot had an existing prefab structure and other debris which had to be disposed of; 2 Coredesk Cellcore Plus insulation1 The run-down plot had an existing prefab structure and other debris which had to be disposed of; 2 Coredesk Cellcore Plus insulationwas installed under the ground floor; 3 wall build-up showing 90 mm bricks externally, 200 mm Knauf Earthwool insulation, and 100 mmPorotherm clay blocks; 4 the use of low thermal conductivity Teplo-L-Wall ties minimises thermal bridging; 5 the first floor timber frame withan opening for a roof window; 6 insulated cavity closer; 7 175 mm Knauf Earthwool rafter roll within roof rafters; 8 & 9 airtightness measuresincluding Intello membrane and taping around windows.
Selected project details
Clients: Sophia Ceneda & Andrea Carbogno
Architect: Carbogno Ceneda
Structural engineer: engineersHRW
MVHR (design & supply): Green Building Store
Energy consultant: Fenton Energy Consultants
Airtightness consultant: Alex Whitcroft
Clay blocks: Porotherm
Wall, roof & floor insulation: Knauf
Thermal blocks: Marmox
Airtightness products: Ecological Building Systems
Windows & entrance doors: Internorm
Roof windows: Abbey Glass
Joinery: Thorsen Joinery
Sustainable drainage systems: Aco Drain
Finance: Ecology Building Society
Gas boiler: Valliant
Underfloor heating: Wavin
Solar PV: Athena Electrical
Lighting: Delta Lighting
Heating controls: Heatmiser
Lighting controls: Schneider Electric
Water conserving fittings: Aston Matther
Sanitaryware: Catalano
Brick: Bespoke Brick Company
Paints: Dulux
In detail
Building type: 110 m2 detached two-storey masonry & timber frame house.
Location: Tottenham, London.
Completion date: Summer 2018.
Budget: £325,000 excluding site, landscaping & joinery.
Passive house certification: Not assessed.
Space heating demand (Measured): 27 kWh/ m2/yr (Figure derived from actual gas bills from January 2019 to January 2020, considering boiler efficiency of 89.6 per cent and excluding estimated 10 KWh/m2 for domestic hot water).
Overheating: Less than 2 per cent of the time recorded with temperature above 25C. On very hot days, overheating is averted with the help of cross-ventilation.
Number of occupants: 2
Environmental assessment method: House designed to be aligned with Code for Sustainable Homes level four, passive house principles in terms of fabric efficiency and heating requirements, and Lifetime Homes criteria.
Airtightness (at 50 Pascals): 1.87 m3/m2/yr one year prior to completion on 15/08/2017 (note: as this result passed building regulations the airtightness was not re-assessed post completion).
Energy performance certificate (EPC): A 92 Measured energy consumption: 50 KWh/ m2/yr (5 Dec 2018 to 4 Dec 2019) based on actual energy bills for electricity and gas & considering boiler efficiency of 89.6 per cent (actual KWh/m2/yr usage as shown in bills is 54.3 KWh/m2/yr). Similar values were reported for previous year.
Energy bills (measured): Gas and electricity energy bills from January to December 2019 inclusive, totaled £578.80 (or £397.70 excluding VAT & standing charge). Subtracting the £150 solar PV feed-in-tariff gives an annual bill of approx. £429, or £35 per month. Based on the estimated space heating demand above, USwitch.com suggests a cheapest available gas bill for space heating only at this address of £94 annually, before standing charges and VAT are added, and not including the feed-in-tariff (£195 total for space heating with charges).
Thermal bridging: Use of low thermal conductivity Ancon Teplo-L-Ties wall ties, thermally broken window frames, Marmox thermal blocks. Y-value: 0.0776 calculation based on construction details and ACDs.
Ground floor: Concrete pile foundations (2,000 mm), hardcore on existing clay soil, 50 mm sand blinding, followed above by 160 mm Cellcore Plus 7/10 insulation, damp proof membrane, 200 mm reinforced concrete slab, self-adhesive membrane by Visqueen (to guarantee against any DPM damage during construction), 200 mm thick Knauf Polyfoam Eco floorboard, 70 mm sand and cement screed with underfloor heating pipes, Ditra matting, 11 mm thick ceramic tiles on adhesive. U-value: 0.13 W/m2K
WALLS
Ground floor (typical): 90 mm bricks externally, followed inside by Ancon basalt resin Teplo-L-Tie wall ties, 200 mm Knauf Earthwool DriTherm 32 slab insulation, 100 mm Porotherm clay blocks, 3 mm Porotherm Ecoparge, 2 x 12.5 mm plasterboards on dabs internally. U-value: 0.15 W/m2K
First floor part masonry (as above) and part timber frame as follows, from outside in: 90 mm bricks externally, 30 mm airgap, Ancon basalt resin Teplo-L-Tie wall ties, 100 mm Knauf Earthwool DriTherm 34 slab insulation, Tyvek SUPRO breather membrane, 15 mm PEFC plywood Sheathing Board, 90 mm Knauf Earthwool FrameTherm 35 slab between 50 x 90 treated timber studs, pro clima Intello Plus airtight vapour control barrier and tape adhesive, 2 x 12.5 mm plasterboard internally. Timber frame U-value: 0.16 W/m2K
Note: Wherever electrical services were needed on an external wall, the wall build-up includes a 50 mm service cavity to prevent any puncture in external fabric.
Main roof: Standing seam zinc roof externally, followed underneath by weatherproof roof membrane, 22 mm softwood sheathing boards, 50 mm ventilation gap with 50 mm x 50 mm purlins, 175 mm Knauf Earthwool rafter roll within rafters, 75 mm Knauf PIR laminate, 12.5 mm plasterboard to ceiling. U-value: 0.13 W/m2K
Flat green roof: Wildflower blanket externally, followed underneath by 100 mm growing medium, filter fleece, reservoir board, Ecomat, PE foil, waterproofing, 5 mm fiberglass, 18 mm PEFC marine ply, 160 mm Kingspan Styrozone insulation H350 R, 18 mm PEFC plywood, 50 x 200 mm deep timber joist. U-value: 0.13 W/m2K
Windows & external doors: Internorm triple glazed low emissivity, thermally broken, powder coated aluminium / timber windows and doors (to garden/courtyard). Internorm timber aluminium Passive House Institute certified entrance door (model HT400). U-values of 0.5 to 0.67 W/m2K for windows; 0.58 W/m2K for entrance door.
Roof windows: Abbey Glass triple glazed low emissivity broken powder coated aluminium perimeter frames: U-value: 0.75 W/m2K & 1.0 W/m2K.
Heating system: Vaillant ecoTEC pro28 condensing gas boiler supplying underfloor heating (GF) and hot water. Time and temperature zone controls with delayed start thermostat. Electric wall radiators for bathrooms installed but rarely used, provision for future radiator connections on first floor.
Ventilation: Paul Focus F200 heat recovery ventilation system. Passive House Institute certified heat recovery rate of 91 per cent / EN 308 certified efficiency of 93 to 95 per cent.
Water: Rainwater harvesting (for plant watering), low flow fixtures. Actual consumption pre-Covid-19 (Mar 19 to Mar 20) 80 litres per person/day (post Covid approx 95 litres/p/day).
Electricity: 8 m2 solar photovoltaic array (2.12 kW power) with average annual output of 1,988 KWh. Annual feed-in-tari" income £150. Green materials: Timber frame (first floor), clay Porotherm blocks, PEFC certified plywood, Scottish larch (sarking, landscaping and fencing).
Image gallery
https://mail.passivehouseplus.co.uk/magazine/new-build/playing-all-the-angles-fabric-first-london-infill-uses-smart-decision-on-a-tricky-site#sigProIdc96335ed2a