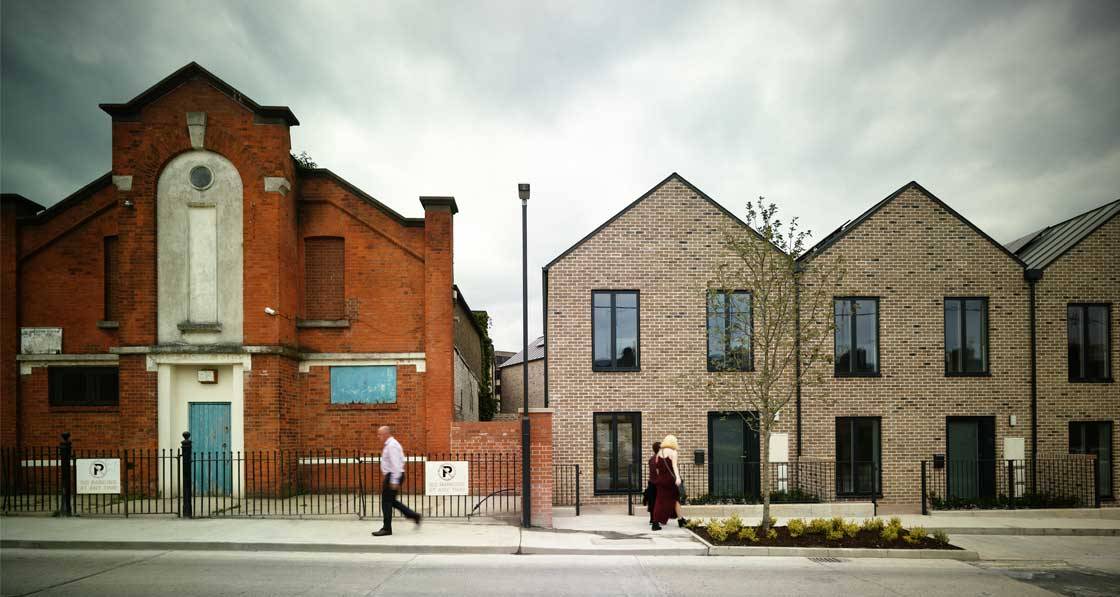
- Feature
- Posted
Social skills - The A1 rapid build council homes that are sustainability all-rounders
In the midst of a national housing crisis, this new development in Dún Laoghaire sets a hopeful and inspiring example: high quality, high density, rapid build social housing that needs almost no energy to heat and is within walking distance of shops, services and the seafront. No wonder it was one of the first projects to be certified to a rigorous new sustainability standard.
Click here for project specs and suppliers
Building: Scheme of 12 x 85 sqm social houses Location: Dún Laoghaire, Dublin Completed: 2018 Budget: €2.57m (ex VAT) Standard: Nearly zero energy buildings (NZEBs)
Up to €155 per year for space & water heating (estimate, see ‘In Detail’ for more)
Dún Laoghaire-Rathdown County Council’s recent development of twelve social housing units at George’s Place in Dún Laoghaire is just around the corner from the waterfront. It also lies at the intersection of a long list of diverse objectives, some of which give every appearance of being contradictory.
The houses are rapid build yet sufficiently well-built to have achieved an A1 BER.
They are high-density yet each retains its own front door and avoids overlooking its neighbour. The site itself is a brownfield site and came with a list of conditions that had to be carefully negotiated before the first sod was turned. The design and build team, led by Dún Laoghaire-Rathdown’s architects department, manoeuvred their way through a maze of restrictions and criteria to deliver exemplar houses in record time.
Schools, healthcare, parks, shops, amenities and public transport are all close at hand.
Susan Corcoran and her two sons moved into their new home in George’s Place in June, just twenty-one months after the planning phase began. “We had a cottage in Dalkey that was over a hundred years old,” says Corcoran. “You walked in the front door and you were in the main living areas. It was cold and it was drafty.”
“What I love about our new home is that as well as being warm, there are no drafts.” She also loves the fact that despite the fact that it is a relatively compact two-bedroom unit, her house feels bigger. “The windows are huge,” she says, “we get brilliant light.”
The best thing about her house, however, is the location. Everything is a walk away. Bob Hannan, senior architect with Dún Laoghaire-Rathdown County Council explains that a variety of factors led to the designation of the George’s Place site for social housing.
“One of the high-level themes of the Dún Laoghaire-Rathdown urban framework plan centres on connecting the town centre to the waterfront. Dún Laoghaire has that dichotomy between a main street which has underperformed and a waterfront which is buzzing with people. One of our strategies is to create as many links as possible between the two.”
This article was originally published in issue 29 of Passive House Plus magazine. Want immediate access to all back issues and exclusive extra content? Click here to subscribe for as little as €10, or click here to receive the next issue free of charge
A second ‘high-level theme’ in the plan promotes the idea that increasing the residential population of the town is the best way to boost its vitality and economic performance.
With these themes guiding developments in the area since 2004, individual site strategies were drawn up to unlock their potential, while remaining within the parameters of the framework plan.
The next challenge was to find a way to deliver own-door, high-density urban dwellings in keeping with the character of the area. Bob Hannan puts it like this: “If you’re going to create family housing, how are you going to do it in the most efficient way possible using precious urban land?”
The shallow, railed-front gardens so prevalent in the area offered a neat example of how to limit each house’s external footprint, as did the small courtyard back garden. Splayed windows at the first floor also minimise direct overlooking of neighbours.
Surprisingly, each house even manages to get its own car-parking space, and there are what the architects describe as ‘home zones’ – informal play and amenity areas – which are passively overlooked by the houses themselves.
Hannan says that while the houses were still in the planning stage, the local authority received an invitation from the government to submit developments to its rapid delivery programme. George’s Place became the council’s response to that call.
Planning permission for the twelve houses was submitted to the local authority’s internal planning process in September 2016. The project went out to tender the following February and contracts were signed in October 2017. Susan Corcoran and her family, along with all of the other tenants, moved in last June.
“We wanted to unravel the idea that rapid build is lower quality,” says Hannan, explaining that the decision was taken to move large elements of the construction offsite not alone to speed things up but also to ensure higher standards.
“With a traditional build, you’d have a guy on a wet November night trying to cut insulation. It’s dark and raining, and he’s freezing. It’s very hard to keep high quality in something like that."
Increasing the residential population of the town is the best way to boost its vitality.
Manufacturing in factory conditions, by contrast, ticks two boxes – speed and quality. To further facilitate offsite construction, the designs of the two types of houses deployed were kept simple. Both are two-bedroom; one narrow fronted with double aspect front and back, the other a wide-fronted shallow unit. To the same end, the design team restricted itself to a small palette of good quality, robust and easily maintained construction materials.
Though rapid build methods may be comparatively new to the construction industry, at George’s Place they were delivered by Sisk Living, a new division of John Sisk & Son – one the oldest and most trusted builders in Ireland.
The Home Performance Index: measuring sustainability in Irish housing
Words by Pat Barry, Irish Green Building Council CEO
Why do we need new a sustainability rating system with the advent, across Europe, of the new nearly zero energy building (NZEB) standard? NZEB for dwellings requires an improvement from an A3 to an A2 BER rating. This represents an overall carbon saving of about 300kg per annum for a sensibly-sized 80 square metre house, or half a tonne for a bigger three-bed home. This is a start but needs to be seen in the context of the total carbon emissions associated with how we design and where we place our homes.Ireland’s per capita carbon emissions are way out of line with the rest of Europe at nearly 13 tonnes per capita versus just over eight tonnes for the European average. It’s not just down to seven million belching cattle, but to the massive resource consumption associated with our legacy of laissez faire planning. The Home Performance Index sets out to capture and reduce these impacts for new home development.
What does it measure?
The Home Performance Index was designed to be easy to apply and fully integrated with Irish building regulations. It is divided into five categories: environment, health and wellbeing, economic, quality assurance and sustainable location, each containing a set of indicators.
It starts with the site. Inefficient land use for home construction leads directly to habitat degradation and fragmentation, pollution, and soil sealing, which increases the risk of flooding and negates the ability of soil to sequester carbon. A typical oneoff home on a quarter hectare is a missed opportunity to sequester, through forestry, 800kg of carbon per annum, or improve to biodiversity.
The HPI measures a site’s accessibility to a range of transport options: walking, cycling, public transport and carsharing. We can’t fix bad sites with electrical vehicles, but we’ll make much faster progress if we only build homes where citizens can live free of the need to own cars altogether. Mandatory requirements are also set in the most important areas, such as water efficiency, ventilation, thermal bridging, and enhanced airtightness. For example, we set a maximum air infiltration level of 3 m3hr/sqm/50pa, as opposed to 7 in the current building regulations. But we also insist that a properly designed and commissioned ventilation system is installed too. The HPI also sets a maximum annual heat demand, encouraging builders to provide the most efficient building fabric-first, rather than achieving a higher rating through renewables.
Water efficiency is now a key part of achieving NZEB with data from SEAI showing that hot water accounts for over 70% of regulated energy in NZEB apartments. The HPI links into existing databases and calculators for water efficiency provided by the European Water Label to help designers design for efficiency.
Embodied carbon
The HPI encourages compact home design and measurement of the embodied carbon of a build. An NZEB home has operational regulated emissions of about 8kg per square metre per annum, but we lack good figures for Ireland for embodied carbon. Figures from other countries suggest between 600kg and 900kg per square metre of floor area. So excess home size can send carbon emissions through the roof.
Figures for 2016 showed that the average new build detached house in Ireland had an average floor area of a whopping 241 square meters, an increase of 60% since 2000, thus wiping out the 60% improvement in energy efficiency in the same period.
Common sense could achieve greater carbon savings than technology. To support the HPI, the IGBC is developing the infrastructure for measuring the embodied carbon of buildings, establishing an environmental product declaration programme (www.EPDIreland.org) to provide the data for calculation. This has been very successful, Irish manufacturers have reacted quickly, and we have already verified 16 EPDs covering over 40 products for Quinn Building Products, Kore, Ecocem, Medite SmartPly, and Munster Joinery. We have also provided training in life cycle assessment and embodied carbon to seed knowledge into the industry.
This year will now see many large developments certified by the HPI including the Cherrywood development of 1,269 homes in south Dublin by Hines, plus at least 12 social housing schemes. The HPI is also now specified as standard in tenders by Dublin City Council.
Green mortgages
A key purpose of the HPI is to define for banks, investors, pension funds, developers and government a robust way of defining what type of development can be considered sustainable, and therefore what should be financed.
IGBC has been working with the World GBC and the European Mortgage Federation on the development of energy efficient mortgages, which are now being piloted by 40 banks across Europe. IGBC is also starting a new initiative with 16 other international partners later this year, which aims to further develop green mortgage programmes and expand them beyond just simplistic energy efficiency. Denmark Technical University will carry out detailed research on the total monthly costs of homes, providing real data that support banks in offering discounted interests on mortgages for greener homes, based on their lower default risk.
For more information on HPI certification, and the full technical manual, see www.homeperformanceindex.ie
More on the Irish Green Building Council at www.igbc.ie.
1 Two courses of Quinn Lite AAC blocks used in subfloors at perimeters and party walls to reduce thermal bridges; 2 the ground floor also features 150mm XT Xtratherm insulation and a radon control membrane; 3 panels being lifted into place for the timber frame structure; 4, 5 & 6 the Kingspan Century Ultima wall system takes only between three and four days to erect once it arrives onsite, and delivers high levels of thermal performance and airtightness; 7 Airtight Pro SCL membrane on the internal side of ceiling; 8 Kingspan PIR insulation to the inside of the roof construction; 9 windows & doors in place, and work begins on fitting the external brickwork over a Protect TF200 Thermo breather membrane.
John Sisk & Son CEO Stephen Bowcott spoke to Passive House Plus about the company’s motivation: “For generations Sisk have been at the centre of house building in Ireland and particularly at times of social need. With the onset of the housing crisis and in support of Rebuilding Ireland, we set up Sisk Living as a specialist residential building division with a clear vision: to become the premier house building contractor in Ireland in terms of size, speed and quality with the lowest possible cost to the end user. George’s Place was one of our earliest projects and we are very proud of our achievement in delivering it.”
According to Sisk Living director of housing, Norman Higgins, the project was a perfect fit for them. “With near zero energy building (NZEB) soon becoming mandatory for all new housing stock, we wanted to test ourselves to deliver this standard as early as possible. George’s Place was a very attractive proposition for us, not only because of the NZEB factor, but also because it was an extremely fast build on a technically challenging city centre site which allowed us to bring our expertise to bear.”
It may sound contradictory but while this was a busy city centre location, it was also, a quiet and thriving residential area. Poor relationships can develop quite quickly between a very busy contractor and neighbours in a location such as this. Managing this aspect of construction was about the smaller things like keeping neighbours informed of what was happening and reacting to any query promptly and respectfully.
One significant sustainability initiative that Sisk Living brought to the project was to register it with the Irish Green Building Council’s (IGBC), Home Performance Index (HPI). Sisk Living then made continuous submissions to HPI through construction and last May, George’s Place was awarded a silver certification under the exacting scheme. The HPI label was developed by the IGBC to encourage excellence in the development of new homes. In addition to the sustainability of a dwelling, HPI assesses its impacts on wellbeing and the costs associated with living in these homes. Drilling down through the HPI documentation, you uncover some interesting results. For example: George’s Place received the highest ever score for ‘walkability’. Schools, healthcare, parks, shops, amenities and public transport are all close at hand, reducing car dependency and boosting the health and financial wellbeing of those who live there.
Dún Laoghaire-Rathdown County Council architects appointed A2 Architects as ‘enabling architects’ to undertake the detailed tender package after planning had been approved and to manage the project during the construction phase.
Peter Carroll of A2 says that the site itself was very challenging.
“You wouldn’t think that it would lend itself to rapid delivery construction,” he says. “We had difficulties with Japanese knotweed, there were more than a dozen boundary conditions, and we had to deal with existing buildings onsite that had to be remediated to hold onto their integrity.”
The build team also had to take into account the fact that they were surrounded by busy roads, and that the site lay at the centre of a thriving residential area.
“We had to ensure that our tender drawings and detailed design were as accurate as possible, and as specific as possible. This was a government contract that didn’t allow any slack.”
Everything, from the pressings of the sills to the ridge details, railings and hard landscaping were closely specified by A2 in collaboration with Dún Laoghaire-Rathdown architects well in advance. Having said that, Carroll notes that a number of tolerances were built into the tender to allow participating parties to suggest rapid delivery systems. Sisk Living selected the Kingspan Century Homes rapid build timber frame system, which takes between three and four days to erect once it arrives onsite.
It was originally envisaged that the houses would be certified passive, and while they don’t quite meet certification thresholds, passive principles are embedded in the design.
What I love about our new home is that as well as being warm, there are no drafts.
As Bob Hannan asserts, Dún Laoghaire- Rathdown is one of the most progressive local authorities in the country when it comes to energy standards.
“It may not be certified but it does have fabric-first principles – very high levels of insulation and airtightness, combined with mechanical heat recovery ventilation. The development is an exemplar in terms of pushing high performance building to its limit, and that is driven by the council itself, and our department in particular.”
For the record, air permeability tests report values of between 1.24 and 3.2 m3/hr/ m2 at 50 Pa, with all bar two units clocking scores of under 2.0 – while U-values are within passive house ranges, as are thermal bridging details. The units also blitzes Ireland’s new nearly zero energy building standard (NZEB), which only came into force at the start of this year.
Peter Carroll says that during the tendering process, the passive house strategy was retained in order to attract like-minded contractors who would not be intimated by exacting standards. And that explains how the development secured such a high score in the Irish Green Building Council’s HPI scheme.
The fact that these houses were built for €249,000 (incl. VAT) each also gives the lie to the idea that a fabric-first, low energy build is an expensive build. And because each house carries an A1 BER, running costs for the tenants should not exceed €200 per year. Susan Corcoran points out that because we’ve had such a mild winter – so far at least – her house has not been seriously tested by the elements. Indoor air temperature over the last eight months has remained steady, warm and comfortable. She likes the fact that she has constant hot water, that yearly maintenance of the system is built into her rent and that the controls for the Nilan Compact P combined heat pump and ventilation system are so easy to use.
“It’s a touch screen with an up and a down arrow,” she says. “Couldn’t be easier.”
Selected project details
Design architect: Dún Laoghaire-Rathdown County Council architects department
Enabling architect: A2 Architects
Contractor’s architect: O’Mahony Pike
Project management: A2 Architects
Main contractor: Sisk Living
Timber frame: Kingspan Century
Client’s M&E engineer: Delap & Waller
Contractor’s M&E engineer: Johnson Reid & Associates
Client’s civil / structural engineer: Punch Consulting
Contractor’s civil / structural engineer: DBFL
Contractor’s energy consultant: Johnson Reid & Associates
Electrical subcontractor: Drysdale Mechanical & Electrical Services
Mechanical subcontractor: Gaffney Mechanical
Client’s quantity surveyor: Nolan Construction Consultants
Airtightness tester: Energy First Services
Windows: Velfac, via Novus Windows
Solar PV: PV Green
Insulation contractor: Baker & Co
Airtightness products: Dupont Tyvek / Airtight Pro / Ecological Building Systems
Zinc roofing: Copeland Coppersmiths Ltd
GGBS: Ecocem
Flooring: Forbo
Wall board: Gyproc
Floor insulation: Unilin, formerly known as Xtratherm
Mineral wool insulation: Knauf
Fire breaks: Rockwool
Thermal blocks: Quinn Building Products
Radon barrier: Radon Ireland
Breather membrane: Protect
Flooring particleboard: Norbord
Zinc roof: Rheinzink
Attenuation tank: Microstrain
Bricks: Ibstock
Render & white mortars: Kilsaran
In detail
Building type: 12 x 85 square metre timber frame town houses
Location: Dún Laoghaire, Co Dublin
Completion date: May 2018
Budget: €2.57m + VAT @13.5%
Passive house certification: Not assessed in PHPP
Primary energy demand (DEAP): 18 to 23 kWh/m2/yr (range of all 12 units)
Heat loss form factor (DEAP): 2.77 to 2.90
Energy performance coefficient (EPC): 0.123 to 0.137 (range of all 12 units)
Carbon performance coefficient (CPC): 0.117 to 0.132 (range of all 12 units)
BER: A1 rated (all units, as per DEAP primary energy demand above)
Environmental assessment method: IGBC
Home Performance Index Silver Certified
Measured energy consumption: N/A
Airtightness (at 50Pa): 1.24 to 3.2 m3/hr/m2 (range of all 12 units; note all but two units scored under 2.0 m3/hr/m2)
Thermal bridging: Kingspan Ultima wall system designed to minimise thermal bridging. Two courses of Quinn Lite AAC blocks used in subfloors at perimeters and party walls. Y-values of between 0.0119 and 0.0307.
Energy bills (estimated): €15.36 annually for space heating & €125.45 for hot water for dwelling type one; €30.36 for space heating & €124.66 for hot water for dwelling type two. Figures calculated based on DEAP energy consumption projections for HPI assessment.
Ground floor: 225mm insitu concrete floor slab followed below by 1000-gauge polythene separating layer, 150mm XT Xtratherm insulation, radon control membrane, 50mm sand binding, compacted hardcore. U-value: 0.12 W/m2K
Walls: Outer leaf – ten units with Ivanhoe Cream Dark End brick, two units with 20mm Kilsaran GP Render externally followed inside by 100mm blockwork external leaf – 50mm cavity, Kingspan Ultima 185 timber frame consisting of breather membrane, 9mm OSB, 89mm studs with PIR insulation, airtightness/vapour control membrane, 50mm PIR insulation, 35mm timber battens to create service cavity, 12.5mm plasterboard and skim finish. U-value: 0.12 W/m2K
Roof: Zinc roof externally, followed beneath by 7mm double standing roof seam, on vapour-permeable separating layer/ underlay, on 18/22mm marine ply deck fixed to timber roof joists. Min 50mm proprietary eaves ventilation try. Roof insulated at ceiling level with 150mm Knauf Earthwool insulation above and between joists, followed beneath by airtightness/vapour control membrane, 30mm Kingspan PIR insulation, 30mm service void and 12.5mm plasterboard/skim finish to all ceilings. U-value: 0.12 W/m2K
Windows: Velfac V200 Energy triple glazed, argon-filled timber aluclad windows. Overall U-value: 0.82 W/m2K
Heating & ventilation: Nilan Compact P combined heat recovery ventilation / exhaust air heat pump system providing balanced whole-house heat recovery along with all space heating & domestic hot water requirements.
Electricity: 4 x 290W solar photovoltaic panels per dwelling.
Green materials: Many specified construction products had high sustainability ratings quantified in Environmental Product Declarations (EPDs) including Forbo marmoleum flooring, Ecocem GGBS, Dulux Vinyl Matt paint & Gyproc wallboard.
https://mail.passivehouseplus.co.uk/magazine/feature/social-skills-the-a1-rapid-build-council-homes-that-are-sustianability-all-rounders#sigProId2b45acb82a
- Issue 29
- social housing
- social architecture
- Housing crisis
- high density
- rapid build
- dun laoghaire rathdown