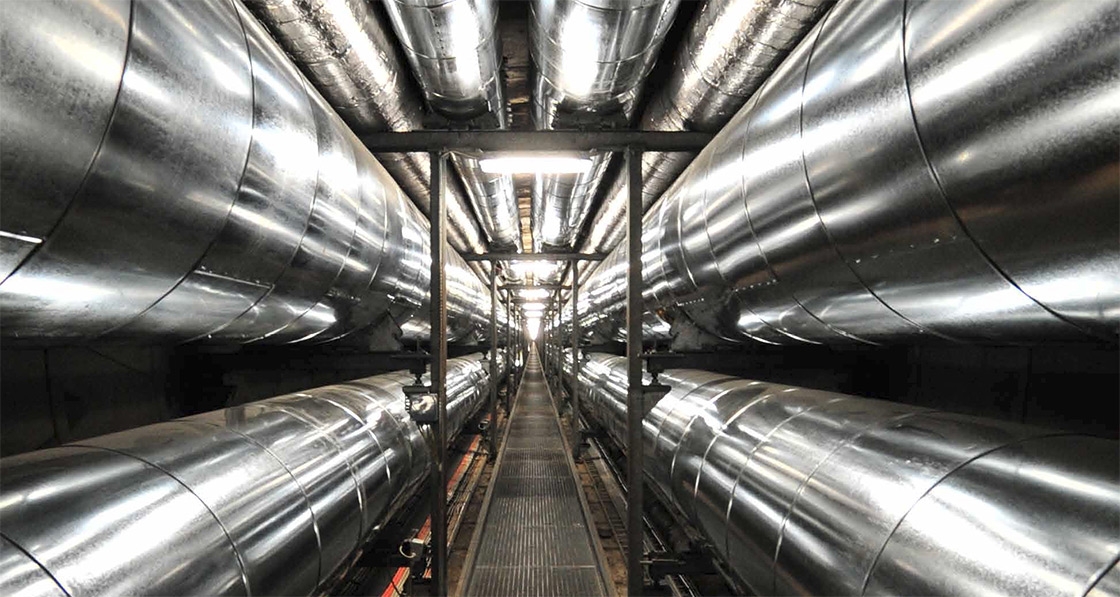
- Insight
- Posted
District heating and passive house - are they compatible?
Thanks to fabric-first energy performance approaches such as passive house, heating demand is collapsing. So how does district heating stack up in buildings which need such little heat?
This article was originally published in issue 15 of Passive House Plus magazine. Want immediate access to all back issues and exclusive extra content? Click here to subscribe for as little as €10, or click here to receive the next issue free of charge
As residential passive house in the UK and Ireland is moving up in scale from small developments to major projects involving hundreds of dwellings, communal heating in passive house is now on the agenda.Communal heating (piped hot water supplying heat to all the occupants of a development) is common in large blocks of flats: individual gas supplies are subject to complicated safety measures in tall buildings; direct electric heating is the alternative, but is considered expensive and high-carbon.
In recent years the desire to use low carbon energy sources such as large heat pumps, combined heat and power, and biomass has also driven interest in district heating – district heating here being the supply of heat from outside the building.
There is a common view that networked heat is “more energy efficient, delivers carbon savings, and can reduce consumer bills.” Networked heat is therefore seen as having an important role in future decarbonisation.
Cities, with their high density of heat consumers, are the most efficient market for heat, offering the highest ratio of heat sold to heat lost through distribution.
The two biomass boilers (with chimneys) and the wood chip store (red building) supply heat to the low density development at Cloughjordan Eco-Village
Some planning authorities now require new developments to be ‘district heating ready’ – even if there is not as yet a local supply of low carbon heat. The Mayor of London has “committed to generating 25% of London’s energy requirements” through the use of local, decentralised energy by 2025. In Ireland, too, district heating, particularly when fired by biomass, is promoted as “low carbon”.
Energy efficiency, reduced emissions and low bills are exactly the aims of low energy building – so you might think that networked heat would be a natural partner with passive house. However, the two approaches can sometimes work against each other in practice, and there are also theoretical reasons why the two approaches might not be a good match.
Is district heating efficient?
Heat sources for a single-building communal system may be a plant room containing a conventional boiler, or a heat pump — plant efficiencies should be similar to individual sources. For a wider district heating system, a variety of technologies may be employed, for example gas powered CHP, biomass, “energy from waste” (burning garbage) and occasionally, industrial waste heat or geothermal energy.
The idea is that supplying a heat network from these large-scale sources will be more efficient and hopefully lower carbon, than individual or single-building heat generation. Unfortunately, evidence to date in the UK suggests the opposite. Inefficient distribution, and/or plant that fails to perform as intended, has resulted in schemes that are not efficient or low carbon at all.
In some case studies recently collated by Innovate UK in the Building Data Exchange (buildingdataexchange.org.uk), monitored losses in district and communal heating systems equalled or exceeded 50% of all heat supplied. In one development, “the overall system efficiency stood at 40% and 46% for two successive years. Assuming the boilers performed at the quoted 90% efficiency, system losses will have accounted for 45-50% of all the energy consumed.”
Unfortunately this is not unusual. In an article on billing for district heating, Yan Evans of communal heating firm Switch2 wrote: “From our own experience and involvement in a significant number of community heating systems, including operating schemes as the ESCo, the overall efficiency of the heating system (fuel input through to delivered heat at the point of consumption) is typically between 50% and 60% once heat distribution losses have been taken into consideration.”
Oversizing
When designing a communal heating system, engineers have to estimate the maximum amount of heat that might be required at any one time – and system design tends to be driven by a fear of missing this target, as Gareth Jones of Fairheat explains.
“M&E designers take a conservative approach,” Jones says, and adds that professional indemnity insurance is one of the biggest drivers of this: “As one person put it, ‘no one ever got sued for delivering too much heat’.” Interestingly however, a Which? survey of customers of over 20 different district heating schemes found that too much heat was the most common complaint about system performance.
One social tenant observed: “The corridors in our building are unbearable in the summer. We complained about the pipes being hot even though the radiators aren’t on — it’s dangerous” and another: “The pipes are so hot [that] I leave the windows open, even when the radiators are off.”
In fact, traditional standards for calculating peak load overestimate what’s needed, even before you start adding extra to be on the safe side, as passive house building services engineer Alan Clarke points out: “The old UK BS 6700 (now obsolete but still sometimes used) is completely wrong and leads to massive oversizing. Current good practice is the Danish standard, but Danish researchers have looked at a range of standards and concluded they all over-estimate demand.”
Chipped offcuts from a sawmill supply heat and hot water to 55 dwellings via the village communal heating network
Oversizing leads to plant that is too big and too expensive — and ironically, less efficient, as many heat sources work a lot better under full than partial load. Pipes will be too large, and flow temperatures may be higher than needed, all of which serves to exacerbate heat loss.
It probably hasn’t helped that for domestic systems there has been no incentive in SAP to design networks to minimise losses. Pipe length and flow temperatures are not taken into account; instead SAP offers a blanket default external distribution efficiency of 95%.
Thus designers receive no feedback to show if a design is an efficient one, and no penalty if it isn’t. In one development evaluated by Innovate, recorded losses “were… eight times those assumed in the as-built SAP calculations”.
Passive house wants even less
Because the fabric of a passive house is so well-insulated, much of the space heat can be supplied by existing heat sources — occupants, their day-to-day activities, and sunlight. This way, a lot of energy is saved.
The corollary of this is that if too much heat gets into the building, it will not simply leak out, but needs to be removed, to prevent conditions getting too hot. Passive house designers therefore take care not to let too much heat into the building when it is not wanted — by adding summer shading, for example, and by ensuring hot water systems are well insulated.
Because district heating customers expect heat and hot water as instantaneously as if they had their own boiler, communal heating systems usually circulate hot water continuously. But continuous heat means continuous heat loss throughout the system.
Few studies of existing systems have given information about whether the losses occurred inside or outside the building envelope.
Losses within the buildings do not necessarily appear in calculations and models at all, because in winter they contribute to heating the building so are not necessarily seen as losses. But the complaints referenced above suggest that there certainly is an excessive heat loss within some communally heated buildings; and if it is too much in a conventional building, it would be disastrous in a passive house.
The authors of one of the Innovate studies made a rough estimate that the internal distribution losses in the study buildings might equate to around 300W unmetered extra heat per apartment in the winter, and 150W unwanted extra heat per apartment in the summer. These apartments were low energy but not passive house; as passive house designer and certifier Peter Warm observes, what a traditional engineer might dismiss as a few hundred watts “is enough to cook a passive house.”
Poor installation has clearly played a part in these poor efficiency figures, including into the buildings. In one of the Innovate case studies “the primary pipework [within the building] was insulated, but there were gaps at the back of the pipe… the valves and pipe connections were un-insulated due to the smallness of the gap between the wall and pipework, determined by the dimensions of pipe clips.” In another, so many valves and junctions were left uninsulated in the plant room its temperature was a stifling 35C.
New code of practice
In light of the poor performance of district heating in the UK, CIBSE and the ADE (Association for Decentralised Energy) have published a new voluntary code of practice for district heating.
Gareth Jones has already found the guidance helpful when working to improve potentially inefficient designs, because it frames efficient design as best practice, which counterbalances the tendency to oversize.
Crucially, the code calls for distribution losses to be calculated (not just taken from SAP). It suggests that networks should design for system losses of no more than 10% in the sections of the network outside the building.
It also encourages designers to consider the risk of overheating: “With appropriate design the heat loss within the building should be less than 15%”. However, questions remain about how the code, which is voluntary, could be enforced.
Will it work in passive house?
As we saw, losses from internal distribution are not ignored by building occupants – and they can’t be ignored in a passive house either. If communal heating is going to work in passive buildings, there needs to be a step change in both design and installation.
Can it be done? We’ll soon find out, as the first UK passive houses with communal heating are now emerging.
The Agar Grove development of 350 passive house dwellings in Camden, north London, will feature a communal heating system
Peter Warm has been involved with more than one of them. His overriding advice is: “If you have to do communal heating, absolutely the most important thing is to minimise the length of pipework.” This is the approach being planned for the development of 350 passive house dwellings in high and mid-rise blocks at Agar Grove in Camden, north London. As Bertie Dixon of building services consultancy Max Fordham explains, their design strategy has vertical pipe risers straight through stacked flats, which allows for much shorter pipe runs than the more standard horizontal approach.
Losses also depend on the temperature in the pipes. At a standard 80/70C flow and return, losses will be around double those in an identical system run at 55/35C. However in the UK even 70/40C is seen as low temperature – even though Scandinavian systems dropped below this 40 years ago.
4G networks
Much higher efficiencies than 50% have been achieved using lower temperatures. One scheme, at Lystrup in Denmark, achieved distribution losses of 17%, serving a low rise (and therefore relatively low density) development of low-energy houses (losses will always be higher in low density development because of proportionally greater lengths of pipe). This scheme was an example of ‘4th Generation’ or 4G district heating, where flow temperatures are very low compared to previous practice, at around 55C.
To minimise losses, return as well as supply temperatures should be as low as possible. High return temperatures add to distribution losses, and also impair the efficiency of the heating plant – condensing boilers can’t condense so well; CHP will also be less efficient, and parasitic loads from pumping will increase, as less heat is being removed per litre pumped.
The scheme at Lystrup above achieved return temperatures of around 34C – and the engineers realised that even this carefully designed system was in fact oversized, and return temperatures could have been lower still. Hot water temperatures were not much lower than the system temperature, thanks to highly efficient heat exchangers in each house.
One concern voiced when lowering network temperatures is legionella risk. Where hot water is stored in hot water tanks or long pipe runs, it must be brought above 55C periodically. However, it is widely accepted in mainland Europe that this does not need to apply where hot water is generated instantaneously, and downstream pipe volumes are small.
German regulations for example allow up to three litres of pipe volume downstream of an instant heater. As Marko Cosic of CoHeat points out, this is the same kind of arrangement that is taken to be safe downstream of every combi boiler.
In the UK and Ireland low temperature networks like this are rare, though one that appeared to work well for the users was installed at the demonstration “zero carbon” development at GreenWatt Way in Slough, UK. The small district heating system ran at 55C, with hot water taken off at 43C.
Return temperatures were between 30 and 35C, and engineer Martin Crane of Carbon Alternatives — who were responsible for the system — believes the latest equipment could lower them further. Legionella was not considered to be an issue: “There was only a very small volume of stored water, less than 1 litre,” Crane explained.
The system at Agar Grove was initially designed to work at 70/40C flow and return, but the contracting team is now aiming to reduce the temperatures to 55/25C. Low volume, small bore, hot water distribution in flats will enable pipe volume downstream of instantaneous water heater to come under the three litre limit.
Commissioning
While flow temperatures are set at the plant, low return temperatures are much more difficult for a system designer to secure. As well as getting the system sizing right, they depend on the performance of the building, the design of the building services, and the behaviour of the occupants. Furthermore, return temperatures are raised disproportionately by just a few components functioning sub-optimally, so careful commissioning is key.
If heat emitters (radiators) are too small or do not give off enough heat (because for example they are insulated with towels or laundry), return temperatures will be too high.
If controls do not work well – for example, bypass valves or ‘heat call’ valves open too often — hot water flows uselessly round the system, and return temperatures will be too high. (Bypass and/or heat call is needed to ensure the heat is always being brought near to the consumer, so they get ‘instant heat’)
At Agar Grove, a number of measures are being proposed to minimise return temperatures, including the smallest possible bypass, and thermostatic valves which slow down the heating flow if the water is coming back too warm. Pipe insulation will be carefully specified and, crucially, checked after installation with thermal imaging.
As the team at Agar Grove recognise, installation is as important as design — and designers need to play their part, and design for ‘installability’ and ‘fixability’. Peter Warm advises: “Design the installation very carefully, leaving enough space for insulation, and make it accessible in case you have to go back and re-fit the insulation if it turns out to be poorly done.”
After all this careful design there will, of course, still be gains from hot water distribution during the summer – these have to be taken account in the summer comfort calculations in PHPP, allowed for in the cooling provision, and in the calculations to ensure overheating limits are not breached.
Primary energy
Passive house sets a strict limit on primary energy, and all system losses have to be added in to the total. Distribution losses inside a building reduce the need for space heat in the winter, but for times of year when heating is not needed, these losses have to be added in.
With careful services design, it ought to be possible to get these heat loads low enough to be manageable both in terms of overheating risk and primary energy demand, says Alan Clarke.
However, losses outside the building may be outside the passive house designers’ control. At present, if a passive house development connects to an externally run heat grid, the primary energy entered in PHPP is derived using set loss factors for transmission and for the primary energy use by the plant.
However, the Passive House Institute recognises that this is not necessarily a good reflection of reality, and is exploring ways to make the calculation more realistic. They note however that it is very difficult, if not impossible, to get performance information (even information about lengths of heat mains) from third party district heating companies.
Can district heating deliver low bills?
While this wasted energy may not (currently) cause problems to the designer aiming for passive house certification, it still has to be paid for, and can potentially cause problems for the occupants. Contrary to a lot of the claims, district heating in existing (non-passive house) developments isn’t always cheap, as an online discussion reveals.
One contributor reports: “The first bill I got said ‘You’ve used 0kWh of heat’ and asked me for £70. No mention was made of these charges by the housing association before people moved in, and they claim there’s nothing they can do about it. We can’t change supplier because the current supplier has a monopoly.”
Another states: “My non-profit landlord (housing association) [promised us] bills of around £per week when we first moved in to our Code Level 5 eco houses.
“My hot water tariff is currently 11p/kWh… I obtained their gas bill recently and was shocked to see they are paying 3p/kWh for gas. They turn this into hot water and charge 11p/kWh to us. .. If you look at the tariffs, it’s actually cheaper to use electric heaters in the winter as they cost half the price to run.
“When I question them about the high cost, all I hear is that all they are charging is what it is costing them and they insist they make no profit”
As mentioned above, as well as charging for fuel, a third party district heating scheme will have to recoup the capital investment. In Casey Cole’s report on the Danish district heating system at Lystrup, he calculated that the capital cost of extending an existing network to the new houses was about £6,400 per house.
At the Cloughjordan eco village in Tipperary, Ireland, a biomass district heating system formed a central part of the plan to live communally, sustainably and with minimal fossil fuels.
The system was sized and installed for 130 homes, but only 55 houses have so far been built, effectively making the system oversized at present. Duncan Martin explains: “The high fixed costs for maintenance and insurance don’t go down because half the capacity isn’t being used – and the heat lost into the ground doesn’t go down either.”
What is worse, much specialist low carbon plant actually becomes less efficient when running below capacity – in some cases even having to cut out and hand over to backup boilers.
If occupants face a high fixed charge for connection to district heating – because the external losses and plant costs remain unchanged, despite their very low energy consumption, their bills will not after all be low. Increasing the per unit cost of energy, and reducing the fixed costs, might make the scheme fairer to low-energy housing, but as Duncan Martin at Cloughjordan warns: “Folk start switching — for example, using an electric shower. Then heat sales fall, so prices have to be raised again to balance the books, and the whole thing starts to spiral down the plug-hole.”
This is a worry for district heating suppliers. If they can’t sell enough heat for a high enough price, they will lose money. Passive house might end up quite unpopular with district heating suppliers as a result of the ultra low heat demand. Everyone needs to be very clear at the earliest stages what the demand will be, and how the pricing will be structured.
A paper published as part of a series of investigations into European district heating systems sets it out plainly: “With third-party district heating, the low heat demand of passive house building effectively reduces the all-important energy density that is so helpful to the efficient and profitable running of district heating.”
Marko Cosic of CoHeat however, says that to an extent this is the system designers’ own fault, and stems from systems being oversized and operated at excessively high temperatures: “We love passive houses – they give nice flat heat load profiles throughout the season so network utilisation is excellent. Because the space heat peaks are so low you don’t need the high flow temperatures that cause such problems.”
Cosic also believes that charging tenants for the initial capital cost of the system through their energy bills is unreasonable; it should be seen as part of the capital cost of the development. “The connection charge should be included in the price of the property and paid by the owner,” he says.
“In social housing, the model we propose is that the landlord pays for the initial capital costs out of the equivalent budget for boiler installation, and the fixed operating costs from the equivalent budget for boiler maintenance and replacement. The tenant should be paying the marginal costs – i.e. actually using the heat.
Is there an alternative?
As Bill Watts points out, the standard of CHP installation has been so poor that, “it would have been better to save the several hundreds of millions of pounds investment and use a £10 electric fan heater plugged into a 13 amp socket using grid electricity.”16
With district heating at its worst, this would even be true in a conventionally designed home — though obviously the electricity would still be expensive. But in a passive house apartment, it would actually be very cheap. The form factor is so favourable, and space heat demand so low, that direct electric heating is feasible within the primary energy limit, according to Peter Warm.
Hot water poses a bit more of a challenge, as in passive dwellings hot water energy demand is higher than space heat, and direct electric heating of water pushes past the primary energy limit. However a heat pump sized for supplying hot water would use a lot less energy, and Warm believes the technology is worth exploring: “Exhaust air heat pumps are getting a lot better and can be as quiet as a fridge. They don’t rely only on heat from the exhaust air but also draw it in from outside, so they no longer lead to over-ventilation and chilling the way the early models did.”
Warm is not a fan of communal heating in passive house: “Communal fossil fuel systems can work for old buildings, listed buildings... but in a modern passive house I feel it’s wasteful, and the buildings are always too hot.” In Warm’s view, the drive for communal heating risks distorting decision-making about low energy building, which is having to bend around in the service of a particular system, rather than simply pick what works best for the buildings. “The tail is wagging the dog,” he feels.
With his experience of purchasing and running district heating plant for low heat loads, Duncan Martin of Cloughjordan Eco Village can see that capital intensive energy systems and high-specification low energy housing aren’t necessarily natural bedfellows. “The extra investment of passive house when you have to pay the standing charge for district heating, and the heat is cheap, makes it a bit questionable whether it is worth it.”
And looking at it the other way, now that passive house is becoming more widespread and familiar, Duncan Martin wonders whether for a similar eco-community, district heating would still be a logical choice.
Yet it is still low carbon heat that attracts the financial inducements, in subsidies such as the Renewable Heat Incentive. And it is even suggested that with district heating, there is less justification for the refinements in energy saving delivered by passive house, as “low carbon heat” is supposedly a simpler or cheaper way to decarbonise.
Mechanical ventilation with heat recovery [MVHR] in particular has been singled out as a more expensive form of carbon abatement than district heating. In one of the case studies looked at by Innovate, the consulting engineer stated that “one of the other reasons for using MEV [mechanical extract ventilation] rather than MVHR was to concentrate on maximising efficiency from the district heating network.” Yet the district heating system on this development had so many issues with the plant that it ended up using more fuel than individual condensing boilers would — in fact in the early stages of the scheme, the amount was double.
There are many questions about the current reliability of “low carbon” heat and its true carbon footprint.17 One can question too whether major new sources will really materialise in future.18 By contrast, with passive house, the technology to slash carbon and energy use is available now.
Passive house is not just about saving energy; it is, equally, about healthy and comfortable living conditions. The need to satisfy a desire for the potential benefits of low carbon heat should not be allowed to detract from the actual benefits passive house offers to occupants.
Losses of 60% make no kind of sense in a world where energy is precious — low carbon energy, especially so. Even losses of 30% only make sense if there is a reliable source of genuinely low carbon heat that simply cannot be operated closer to the customers’ buildings.
As designs, technologies and installation standards are refined, district and communal heating may one day serve low energy housing as easily, simply and efficiently as the simple condensing gas boiler — and may even be able to offer carbon savings. In the meantime, it might be a mistake to let the tail wag the dog.