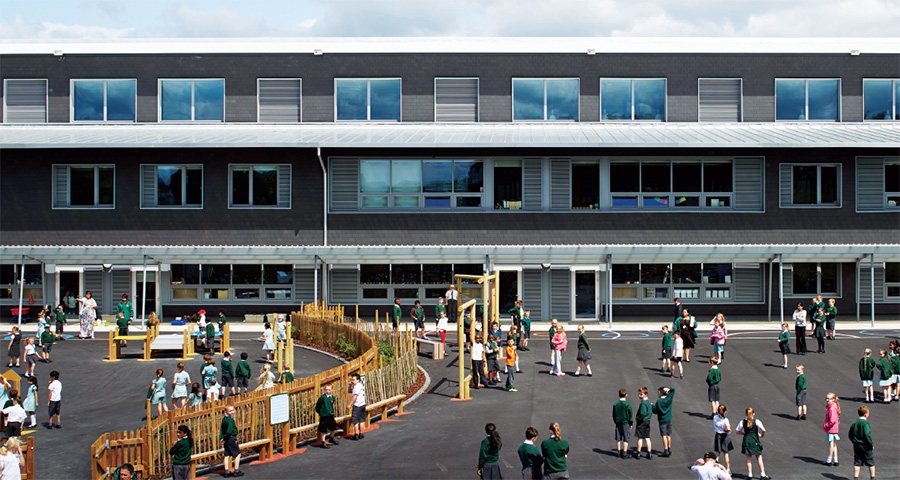
- New build
- Posted
Building a better passive school
The team behind a series of passive house schools in Wolverhampton have used the lessons learned from in-depth monitoring of the first two buildings to make the third even better — and cheaper to build.
Wilkinson School is the third passive house school built for Wolverhampton City Council by the same collaboration of architect, contractor, timber frame company (for two of the three), passive house consultants, and M&E consultants.
In 2011, the team completed their first two passive schools for Wolverhampton, Oak Meadow and Bushbury, even though they were restricted to a standard school budget. Feedback from the teaching staff at these schools has been good. The head teacher at Oak Meadow, for example, reported that staff felt children were “more alert and attentive ... due to the amount of daylight and fresh air.”
After the previous Wilkinson School building was destroyed by a catastrophic arson attack, the head, who had been impressed with the quality of the buildings at Bushbury and Oak Meadow, told Wolverhampton City Council she wanted the same for her students.
By this time the standard budget had been cut by 10%. But the same team was able to work together again, and could take advantage of what had been learned to date to deliver this latest school more quickly and efficiently – and at a lower capital cost. The one concession made by Wolverhampton was that, as energy use and emissions would be so low anyway, there was no need for the on-site renewables usually required by the council.
Wilkinson, like Oak Meadow and Bushbury before it, is a two-storey school: this makes passive house easier and cheaper to achieve (two-storeys are not unusual in larger primary schools, and leave the school more outdoors space).
As with their previous school designs, Architype incorporated some of the specialist teaching areas such as IT and cookery into the circulation space, enabling them to create the wide, daylit double-height ‘streets’ which contribute to the spacious feel inside.
Wilkinson uses the same basic construction method too: an externally insulated timber frame, set on a slab with insulation beneath, and has a similar approach to building services, with gas boilers and radiators providing the heating.
However, careful analysis of the performance of the first two schools enabled the team to identify some expensive features that were not really necessary, and the construction team (timber framers Cygnum and Thomas Vale Construction) was able to refine its approach to accommodate the needs of a passive house build more smoothly. This all contributed to a simpler and cheaper process.
Glazing design
The classic passive house tends to have large areas of south facing glazing, and Bushbury and Oak Meadow were no exception. Experience with these two builds enabled a more tailored glazing design for Wilkinson that saved money, and quite possibly improved comfort and performance too.
Typically in a passive building, internal heat gains provide about a third of the total heating. As schools are densely occupied compared to houses, body heat is a major contributor to internal gains.
However, the assumptions underlying school occupancy in the Passive House Planning Package (PHPP) relate more closely to German schools than British ones. Looking at a sample of schools, Nick Grant of Elemental Solutions calculated that British schoolchildren are squeezed into approximately half the space available to their German counterparts – so contribute twice as much body heat per square metre of classroom.
Compared to the PHPP “standard” school, this translates to a very handy additional 5-6 kWh/m2/yr of useful heat across the heating season – and a less welcome extra burden of unwanted gains when it's warm.
Elemental Solutions realised they could reduce the amount of solar gain from south glazing without endangering the heat demand ceiling of 15kWh/m2/yr, because these additional gains would make up the difference. Reducing the amount of south glazing would in turn reduce unwanted gains in warm weather – and save money. It could even improve daylighting, as tall windows need deep (wide) shades – which in turn reduce sky view, and therefore daylight.
The snag of course is that such a building would show up as needing over 15kWh/m2/yr of added heat in PHPP, because of the software's lower heat gain assumptions. However, Elemental Solutions wrote to the Passive House Institute explaining the case, who agreed they could use a more realistic figure based on UK school occupancy levels.
Thus, one of the main differences between the glazing at Wilkinson School and its predecessors is that the classroom windows here generally stop at around desk height, rather than dropping to the floor. This is simpler, cheaper – and gives more useful space.
Even with reduced areas of south-facing glazing, any building is at risk of overheating in hot weather without good purge ventilation. While MVHR running on summer bypass can remove quite a bit of heat, wide-open windows can do more, and the strategy in all Architype’s passive buildings is to provide generous natural ventilation for this.
Nevertheless, some of the south-facing classrooms in the team’s first two passive schools became a bit warm – at 25C it was nothing drastic, but staff found it uncomfortable. As well as the floor-to-ceiling glazing, there were also some difficulties getting the windows to open.
The foundation sits on 250mm of high density Jablite Jabfloor rigid EPS insulation consisting of two staggered layers; the airtight layer consists of Medite Smartply OSB3 with careful taping at junctions and between panels; wrapped glulam ends visible through structural zone
Some low-level windows were so large they had to be mechanically operated, and the opening had to be restricted to avoid any possibility of fingers becoming trapped. Meanwhile the highlevel ventilation in the curtain walling did not perform perfectly either. Curtain walls, although they look lovely, present some practical problems. “This was a big lesson we learned as architects,” says architect Lee Fordham of Architype.
The openings were also very close to the ceiling, restricting airflow. And the lack of frames in the curtain walling caused problems with the actuator siting, leading to cables getting caught in the windows.
With Wilkinson, these lessons were learned. The building has windows built conventionally into the walls: quicker to install, easier to make airtight – and a lot cheaper. “The way we have framed the windows looks very nice, we are very pleased with the elevations,” Lee Fordham says.
A similar change was made to the daylighting for the spacious double-height circulation spaces. Instead of continuous “curtain roof” glazing, Wilkinson has simple skylights, as Alan Clarke of Elemental Solutions explains. “Upwardsfacing glazing lets in most sun when the sun is highest, but solar gains are least welcome. So now we have individual skylights just sized for daylight. There is less overheating, a big cost saving, and no leaks.”
Service penetrations in the timber frame waiting for ductwork; a site inspection by passive house consultant Nick Grant; a windtightness detail
After the experience with the first two schools, says Lee Fordham, “we realised that the occupants were better at controlling their comfort than the BMS was. BMS is not always in tune with user needs; it can also be distracting when it keeps opening and closing the same window, making a buzzing noise each time.” At Wilkinson the smaller, lighter, low-level windows are all manually operated.
Instead of relying on the BMS to control purge ventilation, Wilkinson has secure night vents. These are inward-opening casements that can be opened to 90 degrees and fixed back out of the way, for the full benefit of the cool air. Many are at low level so can be manually operated
Heating and hot water
With heat loads as small as they are in passive buildings, Elemental Solutions are inclined to offer simple advice. Running costs and emissions will be low whatever the heat source, so it makes sense to go for a system that is familiar, reliable, and inexpensive – hence the use of simple gas boilers and radiators, with local control via thermostatic valves, for all three of the schools.
The team took advantage of the BMS monitoring information from the first two schools to refine their design decisions at Wilkinson. The systems specified for the earlier schools – two boilers, and two large radiators per classroom – were much larger than needed. At Wilkinson the heating system supplies one modest radiator per room, saving money and freeing up wall space.
Not only are the radiators smaller and fewer. Unusually for a school, there is only one boiler. Alan Clarke explains: “The school is so wellinsulated that the boiler is no longer ‘mission critical’ — the school can stay open even if it breaks down. Other schools not only have to have much larger boilers, they need multiple boilers in case one fails.”
Monitoring at Bushbury and Oak Meadow also enabled a simpler hot water design. There, the majority of the heat used by the hot water system turned out to be disappearing as circulation losses. At Wilkinson it was decided to use a dispersed system instead, with small electric heaters supplying just four or five rooms apiece, via small bore pipework, to minimise losses.
Ventilation
For background ventilation, because the number of people in the building is so predictable, it was not necessary to cater for all eventualities.
Thus rather than the standard approach of providing air changes to each room to match the maximum number of occupants it might contain (ie, basing supply on floor area), it was possible to subdivide the building into fewer zones, and supply air in at one end, cascade it through, and extract at the other, as the same number of occupants will always be somewhere in the cascade. This greatly reduces the amount of ductwork required, compared with supplying and extracting from each room separately.
For the school hall, occupancy varies widely (from no-one to the whole school community), so here a CO2 sensor is used. When the hall is in use, air is brought in through the wall from the internal 'street'. When everyone is in the hall, the air arriving into the 'street' from the classrooms is fresh, because the classrooms are empty – thus there is no need for a separate supply from the main unit.
Initially the plan was to ventilate the schools naturally (ie by window-opening) in summer, with no MVHR. However, as Lee Fordham explains, although you can turn the heating off in summer with no problem, people need to be told to switch to natural ventilation when the MVHR shuts off.
In practice, continuing to run the ventilation but on summer bypass is simpler: good ventilation is assured, and occupants can still use natural ventilation for additional comfort, which they don’t need telling to do. “This is worth the little bit of extra energy used,” Lee Fordham believes.
Monitoring and occupant feedback on electricity use at the first two schools proved invaluable too. Here the lighting had supposedly been controlled by BMS, but in practice this left lights on when they weren’t needed, with no way to turn them off. For Wilkinson, lighting controls were mostly ditched, along with the expense.
Easier construction
The construction system for all three schools has been developed by Architype and their construction colleagues. It wraps a continuous ‘duvet’ layer of insulation around the outside of the frame and under the floor.
As Lee Fordham explains: “To create a continuous layer of insulation the solid concrete floor floats over 250mm EPS. The load is spread evenly through the EPS, rather on the same principle as snowshoes, so this causes no structural problem.
“By contrast you can’t get the same continuity with external insulation if you have a suspended floor, as you have to insulate above the floor structure.”
Although Oak Meadow and Bushbury schools had freestanding glulam structures entirely inside the thermal envelope, with the reduced budget at Wilkinson School this would have cost too much, as Mark Smith of Cygnum explains. Instead, there is a load-bearing stud wall in the first (inner) 140mm of the 340mm insulated space. The outer 200mm is created by Larsen trusses, and the full thickness is insulated with blown cellulose insulation. Onsite assembly means less timber needs to be used in the outer section, minimising thermal bridging in the all-important 'duvet' layer.
Inside, the team has built on the experience of maintaining airtightness in the first two schools and the continuous OSB airtight layer is prioritised, ensuring it has as few joints as possible.
Previously, internal floors and load-bearing internal walls were notched into the frame, as part of the strategy to ensure the building does not collapse if one part is damaged. However, this means the airtight layer had to lap around the outside edges of the floor and walls, introducing three extra corners, meaning a lot of joints and a lot of tape. As Mark Smith explains: “We now use a different structural strategy to deal with disproportionate collapse, and keep the airtightness layer as a flat plane.”
Cygnum has embraced this approach, and now supplies drawings with all the airtight lines carefully marked in. Mark Smith says: “Some coloured lines on a boring section really make a difference. It makes it much easier for everyone to understand how the building works.”
The experience of the previous builds using the same system has enabled the team to come up with other apparently small refinements that nonetheless make life a lot easier on site.
For example, contractor Thomas Vale has perfected the way it tapes the windows – eliminating hundreds of pin-sized potential holes; and the way the walls are now prepared to receive the roof makes subsequent taping of the air barrier between them much more straightforward.
How is the school working?
The formal monitoring and soft landings process at Wilkinson School is due to begin in September 2014, so the feedback is only informal as yet. Monitoring that has taken place suggests that temperatures are stable. More importantly, the occupants are comfortable. According to head Tina Gibbon: “The school feels very airy, and it’s very quiet. It’s warm in winter, but it also performed very effectively in the recent hot weather.”
Building, then studying, a series of passive schools has enabled a lot of streamlining, and seems to offer the much-hoped-for reductions in the passive house cost premium. Critical to these savings, however, was the close teamwork and full buy-in from all parties. “It would have been impossible without the continuity of the main firms involved,” Lee Fordham believes.
Everyone gained from putting aside “the way we’ve always done it” and responding to the specific requirements of passive house. But just as valuable, everyone – and the budget too – gained from identifying and omitting the expensive and complex features that passive house manages perfectly well without.
Selected project details
Client: Wolverhampton City Council
Architects: Architype
Project manager: Carillion
Principal contractor: Thomas Vale Construction
Timber frame: Cygnum
Passive house consultants: Elemental Solutions & Alan Clarke
Mechanical & electrical engineers: E3
Structural engineers: Price and Myers
Landscape architects: Coe Design
Airtightness products: Pro Clima/Siga
Cellulose insulation contractor: PYC Insulation
Windows/doors/curtain walls: Raico & Gutmann, via Pacegrade Joinery
Rooflights: DVS Ltd
Roof joists: Steico
Building boards: Fermacell
OSB: Smartply
Sheathing boards: SIG Insulation
Cladding: H&H Alloys
Ceilings: Troldekt
Quantity surveyor: Smith Thomas Consult (since
acquired by Ward Williams Associates)
MVHR: Swegon
Condensing boiler: Remeha
Additional info
Building type: two-storey school, 2610 sqm gross internal floor area, timber frame with Corten steel and Wienerburger Corium brick façade.
Location:Bilston, Wolverhampton, United Kingdom
Completion date: February 2014
Budget: £5.05m (construction cost)
Passive house certification: pending
Space heating demand (PHPP): 11kWh/m2/yr
Heat load (PHPP): 9 W/m2
Primary energy demand (PHPP): 111kWh/m2/yr
Airtightness (at 50 Pascals): 0.34ach
Energy performance certificate (EPC): A25
Ground floor: various floor finishes on 300mm power floated concrete slab, on low permeability gas membrane, on 250mm high density (Jablite Jabfloor) rigid EPS insulation consisting of two staggered layers. U-value: 0.064
Walls: 12.5mm Fermacell boards internally, followed outside by 38mm service zone, 18mm OSB-3 taped at joints (airtightness line), Cygnum timber frame consisting of: 140mm structural zone with cellulose insulation (Warmcel 500), 200mm insulation zone with fully-filled Warmcel 500, 15mm T&G Bitroc sheathing boards, butt joints taped (wind-tightness line, ventilation zone comprising timber battens (minimum 50mm), external cladding. U-value: 0.13
Flat roof: 12.5mm Fermacell boards internally, followed above by 18mm OSB 3 taped at joints (airtightness line), and Cygnum timber-frame consisting of: 250mm roof joists (TJI, Steico), 18mm OSB, 250mm insulation, Sarnafil single ply membrane. U-value: 0.1 W/m2K Pitched roof: 12.5mm Fermacell boards internally, followed above by, 18mm OSB 3 taped at joints (airtightness line), and Cygnum timber frame consisting of: 350mm Roof joists (TJI, Steico) fully filled with Warmcel 500, 12mm timber vent, Pro Clima Solitex Plus membrane (wind-tightness line), 89mm ventilation zone, 18mm WBP plywood, Kalzip aluminium profile roofing with membrane. U-value: 0.1
Windows: Gutmann Mira Therm 08 tripleglazed aluminium-clad spruce windows, with argon filling and Swisspacer bar. Uf-value: 0.77; Ug-value: 0.54
Curtain wall: Raico Therm+ H-I triple-glazed aluminium clad timber frames, with argon filling and Swisspacer bar. Uf-value: 0.8; Ug-value: 0.54
External doors: Gutmann S80+ HW tripleglazed aluminium thermally broken and thermally insulated frames, with argon filling and Swisspacer bar. Uf-value: 1.8; Ug-value: 0.54
Roof lights: 3 x LAMILUX UK Ltd CI System Glass Element FEenergysave skylights. Passive House Institute certified system with warm edge spacer bar, triple layered seal system & thermally broken frame. U-value: 0.84
Heating system: Remeha Quinta Pro QP90 (rated output 84kW) condensing natural gas fired boiler and radiators. Gross efficiency at 50C Flow, 30C Return is 104.1% (net 93.8%). Hot water is provided by a number of local electric water heaters to minimise distribution and storage heat losses. Microbore copper pipework is used for final pipework to keep hot water deadleg volumes to a minimum.
Ventilation
Main school: Swegon Gold 50 supply and extract air handling unit with rotary wheel heat exchanger. Heat recovery temperature efficiency 82%.
Kitchen: Swegon Gold 12 supply and extract air handling unit with run-around coil heat exchanger. Heat recovery temperature efficiency 57%.
Green materials: Fermacell boards, Warmcel cellulose insulation, Bitroc boards, Troldekt panels.