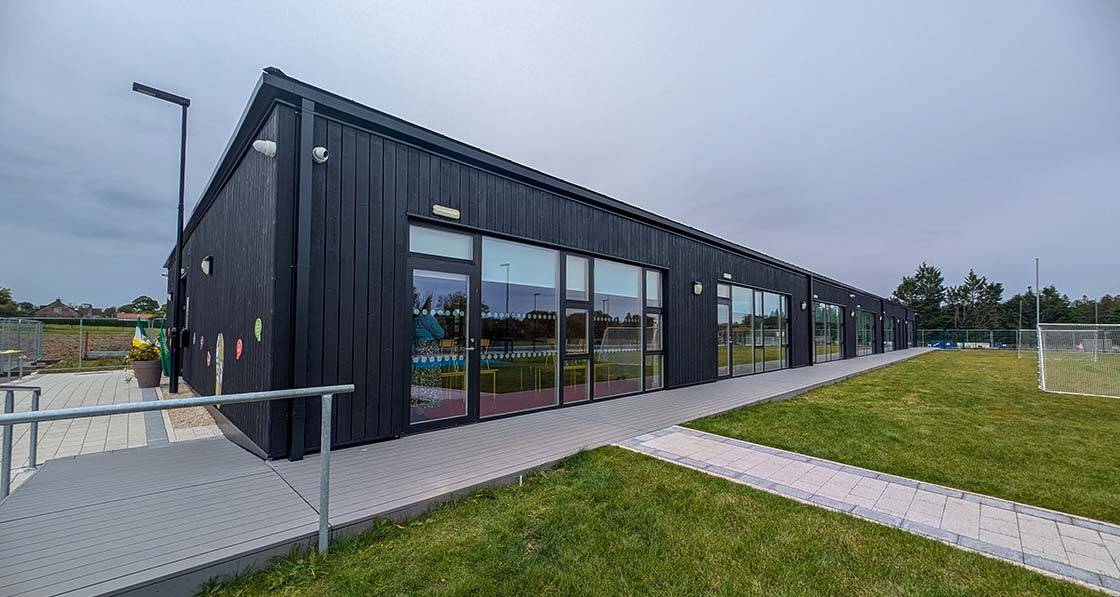
- Feature
- Posted
Pump up the volume
Forgive the 80s hip hop house reference in the headline, but the volume of the walls in this volumetric modular school building in Birr was literally pumped up – with recycled newspaper insulation. Built to passive house principles, it’s a story of one Roscommon manufacturer reimagining the role that offsite methods can play in the delivery of highly sustainable permanent accommodation for schools – while delivering exceptionally low embodied carbon results. Additional words - Jeff Colley
Click here for project specs and suppliers
Development type: 1,000 m2 class room building
Method: Timber frame volumetric modular building with bio-based insulation.
Location: Greenfield site, Birr, Co. Offaly.
Standard: Near passive, and ultra low embodied carbon (meets the RIAI 2030 Climate Challenge targets)
Heating cost: €91 per month estimated space heating cost – and set to fall once the PV array is installed.
See 'In detail' panel for more information.
Gaelscoil na Laochra, in Birr, Co Offaly, was borne out of a desire by the Department of Education to build a high performance low embodied carbon school using modular construction to meet their permanent building standards. The original idea was driven by a senior architect in the department, Niall Lowther.
Reference to “prefabricated” schools probably conjures visions of cold, unsightly cabins in school yards, but these days the word “prefabricated” has largely been expelled from the construction lexicon, replaced by fresher terms like modular, offsite, and the zeitgeisty but nebulous MMC (modern methods of construction).
And there is a new generation of offsite manufacturers delivering high quality, low carbon offsite structures that meet, or come close to, the passive house standard.
“We really have to figure out how to deliver low embodied carbon buildings, that was the primary driver for this," says Mick McDonnell, a senior architect at the Department of Education.
“We were focused on embodied carbon as the main improvement over traditional building.”
Roscommon-based Lidan was awarded the contract. The innovative offsite builder who have become known for delivering ultra low embodied carbon, all-timber, turnkey buildings – and even for using ground screws on some projects as an alternative to conventional concrete foundations.
Lidan Designs were appointed to deliver a new 1,000 m2 school building for Gaeilscoil na Laochra in Birr, Co Offaly – but the building posed challenges for a modular, offsite builder. The Department of Education's typical standard for new school buildings is a floor-to-ceiling height of 3.15 metres, which presents challenges of transporting modules taller than this by road.
However, Lidan set about aiming for the 3.15 m target, but it required delivering the 8 m x 4 m modules on low loaders, so as not to hit any overhead bridges on the road between Roscommon and Birr. Lidan manufactured the modules in their Roscommon factory, but a bespoke approach was also required to build and deliver the school’s large open-plan rooms, such as the 70 square metre library, and the 100 square metre shared activity space.
“The ability to do the wide open-plan rooms meant that two walls needed to be omitted from some boxes, and in some cases three walls, prior to transportation," says Dan O'Brien of Lidan. "This in addition to the eight metre room spans required some specific structural engineering in terms of beams, and true to our sustainability strategy this was all done in timber.”
This added to the complexity on site. “The materials are more substantial, the modular units are much heavier, the transport and lifting is way more complex,” O’Brien says. At 1,000 square metres, it illustrates the increasing complexity of the challenges that skilled modular builders are willing to take on, and deliver, in Ireland.
-
The 1,000 m2 school building was built in Lidan’s factory in Roscommon in 8 m x 4 m modules and transported to site on lowloaders The 1,000 m2 school building was built in Lidan’s factory in Roscommon in 8 m x 4 m modules and transported to site on lowloaders
-
Each module was then craned into place on precast concrete ground beams. Each module was then craned into place on precast concrete ground beams.
-
Each module was then craned into place on precast concrete ground beams. Each module was then craned into place on precast concrete ground beams.
https://mail.passivehouseplus.co.uk/magazine/feature/pump-up-the-volume#sigProIdddb545ca13
The use of timber construction and a combination of cellulose and wood-fibre insulation also meant wider, thicker modules than if synthetic materials were used, but true to form, Lidan specified timber throughout – and took this philosophy to an obsessive level.
For a start, the entire structure is timber frame, with I-joists in the roof and floor, and glulam for structural beams. Lidan had won a national innovation award in 2020 on the use of glulams in structural widespan modular buildings. Recycled paper in the form of Isocell cellulose is the primary insulation, with Gutex woodfibre forming an additional external layer of insulation for the walls and flat roof.
Most of the structural timber was of Irish origin (the glulam came from mainland Europe), and all of it was FSC-certified. The building was then clad externally with charred Siberian larch from MTS in Bray, with metal fixings from Rothoblass, and the larch was even fixed in place using a low carbon innovation: wooden nails. Lidan believe this may be the first time that wooden nails were used on a project of this scale in Ireland.
Our school is extremely comfortable and it makes for an exceptional learning and working environment.
With attention shifting to the circular economy, innovations like this may be destined to move from obscurity to centre stage for one very far-sighted reason: when the building reaches its eventual end of life, timber nails will make it far simpler to reuse the timbers.
The modules were almost entirely finished in the factory. "You had an open-plan room, five or six boxes with two sides missing, going down the road fully finished – including all electrics, all plumbing - and skim finish plastered,” O’Brien says.
This obsessive focus on timber paid off in the building achieving an exemplary embodied carbon score: 488.2 kg CO2/m2, comfortably beating the RIAI 2030 Climate Challenge target of 540 kg CO2e/m2 for school buildings in spite of the heady duty concrete foundations, which were outside of Lidan’s remit.
Apart from Lidan’s core system there were other neat sustainable touches in the finishes too: a standing seam metal roof, installed by hand, which is fully recyclable, and floors finished with Forbo Marmoleum, an all-natural alternative to linoleum, which is made from flaxseed oil, wood flour, pine resins and jute.
The building performs exceptionally well when it comes to energy performance. PHPP calculations at design stage showed that the building’s heat load was meeting the passive house target of 10 W/m2 – albeit factoring in a Passive House Institute-certified heat recovery ventilation system which wasn’t used in the end.
The fabric standards are all in the region of typical passive house specs: U-values of 0.13 for the roof and floor, and 0.15 for the walls, and thermally broken triple glazed windows with a glazing U-value of 0.53.
An airtightness test by 2eva.ie revealed the finished school also hit the passive house airtightness target of 0.6, with all airtightness membranes pre-installed in the factory. Because airtight buildings can take longer to dry out, the Lidan team even used a waterless skim to reduce the amount of moisture internally.
The overall heating demand of the building is so low that Lidan opted to install direct electric radiators for space heating – which can be pre-fitted in the factory – rather than heat pumps, with a domestic hot water heat pump to meet the hot water requirement.
In an ordinary building the decision to opt for direct electric heating at a time of high electricity prices might be ill-advised – with each kilowatt of electricity generating only a kilowatt of heat, as opposed to a heat pump, which could deliver three to five times that return.
But this building has a couple of things in its favour to mitigate the risks of high costs. There's the combination of excellent airtightness, high levels of insulation, triple glazing and heat recovery ventilation to dramatically reduce heat loss. There’s the fact that primary schools are only occupied during school days, and only for part of the day – with a boost of free “kiddiewatts” from metabolic heat loss starting each day when the children enter the building.
While no formal energy monitoring is taking place yet, school principal Niamh Ui Chléirigh says the radiators have seen little use.
“We switched them off altogether in march,” she says. “One of the teacher's asked to switch them on last week [in October] because it was a chilly morning. There was no sun that day, and her room is at the back of the building where there's less sun. It was on for a maximum of two hours, because it got too hot.”
There are two heaters per classroom, Ui Chléirigh says, “but there's only ever one on. They're set to 20 to 21C, and they turn off when they reach temperature. They were used in February, when it was colder.”
The heat demand is reduced further by a heat recovery ventilation system, comprising 14 Daikin enthalpy recovery ventilation units.
While these cross flow units don’t recover as much sensible heat as the counterflow heat recovery units that more commonly appear in these pages, they do recover latent heat, meaning some of the humidity from the extract air is passed to the supply air.
“As a consequence,” says Tony O’Connor of consulting engineers TEM Engineering & Management, they “can provide a level of humidity control without sophisticated controls being required”.
The large ducts are exposed throughout the ceiling, and the system was designed to deliver up to 10 litres per occupant per second. McDonnell says the department is also keeping an eye on the risk of overheating in schools.
“It’s something we’ve always considered, and we need to ensure that the design teams who work with us fully understand and mitigate that risk.”
According to Niamh Ui Chléirigh, overheating has not been a problem here, bar some minor teething problems while the occupants figured out how to operate the new building.
“Some of the classrooms got quite warm in May and June,” she says. “So we had to refigure out how to use the summer bypass on the ventilation systems, and that brought the temperatures down to acceptable levels.”
A 16kW solar photovoltaic array is set to be installed on the roof, to bring the building’s BER up from an A3 to A1 rating. An analysis for this article by solar PV expert Tim Cooper suggested a tailored solution to maximise solar contribution to meet the winter electrical load.
“If the array was located along the top of the southeast facing wall, the winter output would be circa 40 per cent higher than on the roof – also meaning no tampering with the roof and no need for aluminium support frame. The modules can be mounted on a simple wooden frame fixed to the external wall. They would also reduce solar gain during the summer. Fixed in this way a 16kWp system will generate 1,760kWh from November to February,” says Cooper, “most of which will be used on site.”
The turnaround of the project was speedy. Work in the factory started in January 2023, work on the greenfield site began in July 2023, Lidan went to site in October during storm Babet and the building was complete in December of that year. The school community moved in during February 2024.
Dan O’Brien of Lidan says that, in terms of time, 80 per cent of the build was completed offsite, but in terms of the value of the project, 92 per cent of it was premanufactured value (PMV), finished in Lidan’s Roscommon factory.
McDonnell is eager to see the department carry out more pilot projects like this on innovative and sustainable methods of construction. “The state has a duty to be a leader when it comes to sustainability,” he says. “I would be keen to see more post occupancy evaluations of these projects too.
But more than anything, he loves the look and feel of the building. “It’s got a burnt larch exterior, it looks lovely, it feels lovely. It’s nice to know that not only is the building delivering on all of its technical goals, but it’s a really nice environment for the kids. Just because it’s MMC doesn’t mean you have to give up on aesthetics and materials.”
Niamh Ui Chléirigh agrees. “Our new school building is amazing,” she says.
“It is bright, colourful and cosy. The triple glazed, full length windows keep the school warm and allow an abundance of daylight into the classrooms. The technology in the heating and ventilation system allows us to regulate the temperature at the touch of a button or by using the app on our phones. The school is extremely comfortable and it makes for an exceptional learning and working environment. The school now has a wonderful home where pupils can learn and develop the skills they need for the 21st century in a beautiful state of the art building.”
Low embodied carbon, against the odds
This article was originally published in issue 48 of Passive House Plus magazine. Want immediate access to all back issues and exclusive extra content? Click here to subscribe for as little as €15, or click here to receive the next issue free of charge
A report by leading whole life carbon consultant John Butler assessed the building’s embodied carbon against the RIAI 2030 schools target of 540 kg CO2e/m2 of gross internal area (GIA) – covering the emissions from cradle to grave. The foundations and spoil removal alone add up to 184.7 kg CO2e/m2 – over a third of the RIAI target. Lidan’s challenge was to add a fully finished, high performance building – with highly insulated floors, walls and roofs, triple glazing, internal and external finishes including a standing seam aluminium roof, building services including MVHR, electric heaters, hot water heat pump, a large PV array and fitted furniture, and keep the score as low as possible. The overall score achieved was 488.2 kg CO2e/m2 GIA.
What's in a cradle-to-grave life cycle assessment?
Cradle-to-grave building life cycle assessments divide a building up into modules covering three phases of its life, as follows:
Module A: the emissions released by the point the building is completed, through the manufacture of building materials, transporting them to site, and the construction process itself.
Module B: the emissions predicted to be released during the building’s use, due to maintenance, repair and replacement of components. Operational energy and water use comes into this phase too, but organisations like the RIAI, RIBA and LETI don’t include it in the cradle-to-grave totals – they’re reported separately instead.
Module C: the emissions predicted to be released when the building reaches its end of life, through demolition and disposal of materials. This includes landfilling, incineration or recycling of materials.
There is also another phase – Module D, which we describe as the graverobber phase. It covers benefits from potential reuse of materials in other applications, and other benefits outside the boundary of the LCA calculation.
To prevent potential future emissions reductions being netted off against emissions released within the building’s life, Module D figures are not counted in most embodied carbon targets, but can be reported separately.
What was the main cause of this result? To attempt to answer that, Butler modelled the effect of the same building being constructed conventionally, with cavity wall construction and PIR boards in the cavity and roof. For this article, we re-ran the calculation stripped back to only include the foundations and floor build up, external wall build-up, and roof systems.
The external finish of the walls was included, but the floor finish and roof finish were also omitted, as were the windows and external doors. The figures were then worked out for three scenarios:
- The Lidan fabric, as built
- As built, without the concrete foundations
- A cavity wall build alternative
On a cradle-to-grave basis, the Lidan build system for this school – including piled concrete foundations – comes in 25.7 per cent lower than the cavity wall alternative. Take away the foundations from Lidan’s build, and it’s 68.5 per cent lower.
Of course, this is not to say that Lidan buildings don’t require foundations – except in cases where buildings are delivered to pre-existing foundations. But the company has experience of working with lower carbon alternatives to strip foundations – up to and including ground screws – and is exploring other foundation options to substantially reduce concrete use overall, and integrate low embodied carbon materials into the mix.
The sequestered CO2 emissions are noteworthy too. Even in spite of the concrete foundations, the as-built school has almost as much CO2 stored in the Lidan building fabric as was released into the atmosphere by the point of practical completion. If we exclude the foundations, the stored CO2 is almost double that which was released by this stage, due to the high reliance on timber, cellulose, wood fibre and wood panel products in the build.
As Passive House Plus has previously reported, rules on building life cycle assessment mean that the CO2 emissions stored in certain building materials cannot be netted off against the emissions released into the atmosphere from building materials production, transport to site, the construction process, repair, replacement and maintenance, and end of life disposal. There is good reason for this.
Plants provide an important function in absorbing CO2, and if those plants are harvested and the bulk of that CO2 remains stored in the resultant products which prevents the CO2 entering the atmosphere for 20, 50, or a hundred years or more, it buys us time in the climate fight.
But netting those figures off against emissions released from polluting products risks creating the impression that those emissions haven’t occurred, or are not an issue. For this reason, targets like net zero emissions are inherently problematic. It’s much better to count the emissions released, and separately count the emissions stored in materials.
With increasingly accurate data emerging on emissions from current construction product manufacturing, transport and construction processes, the emissions released by the point of delivery can be proven with a high degree of confidence.
While these “sequestered” emissions are calculated and accounted for – and considered as benefits for as long as they remain in the building – they’re effectively considered to be released into the atmosphere at the building’s end of life. The rationale is that, even if materials containing stored CO2 are eventually reused in another building, the benefit of those stored emissions would pass out of the calculation for the original building, and into the calculation of the next use.
The treatment of end of life disposal has become a little more complicated since the advent of a new embodied carbon calculation standard, the RICS Whole Life Carbon Assessment for the Built Environment standard (WLCA), 2nd Edition, which came into force in July 2024. But the treatment of sequestered CO2 is essentially the same.
With Butler’s calculations on the whole building – including not just the Lidan fabric, but all elements – the sequestered total rises somewhat, due to stored CO2 in the internal doors, wood within the timber alu windows, internal partitions and some finishes.
But this is dwarfed by an increase in emissions from a number of sources, including the standing seam roof, windows, finishes, electric radiators and ventilation systems, among others.
Building LCA involves a heady combination of logging what has been done, and trying to make informed predictions about what will happen decades into the future – over an assumed 50 year lifespan for buildings in the EU, and 60 years in the UK. These lifespans are sometimes described instead as reference study periods.
To produce a cradle-to-grave figure, it’s necessary to set an estimate of building life. 50 or 60 years may seem pessimistically short for many building types, but using a set period does allow fair comparisons to be made between buildings.
With increasingly accurate data emerging on emissions from current construction product manufacturing, transport and construction processes, the emissions released by the point of delivery can be proven with a high degree of confidence. But the picture gets murkier after this, because looking forward involves making a number of assumptions. Two of the biggest such assumptions are around future manufacturing and waste disposal.
The original RICS guidance on embodied carbon took a punitively precautionary approach in these regards, and assumed that if a component is replaced in, say, 15 or 25 years, the replacement would have the same manufacturing emissions as the original component, and the old part would be disposed of in line with current waste disposal practice.
In addition to this “status quo” scenario, the 2nd edition of RICS includes a decarbonised scenario – meaning it is possible to assume that product manufacturing and disposal will have decarbonised to some extent over time.
By definition the projected decarbonisation scenarios do not apply to the construction phase, as we can instead use current data to provide more accurate figures here. They only apply to the use phase and end of life phases, and take into account projected decarbonisation in the manufacture of replacement materials, and cleaner construction waste disposal when the building reaches its end of life.
As it stands the “decarbonised” scenarios have not been added to the RIAI, RIBA and LETI targets, so when we talk about RIAI 2030 Climate Challenge targets above, the projected emissions for the use and end of life phase are likely to be punitively high.
Reflecting changes introduced in the new RICS standard, Butler carried out two versions of the calculation, based on a non-decarbonised and decarbonised scenario. The non-decarbonised scenario represents a very much worst-case situation, whereby national and global energy use and manufacturing does not decarbonise at all in the future. End of life demolition, removal of materials, and replacement of building elements across the lifespan are assumed to carry the same embodied carbon impact as they do today.
The decarbonised scenario assumes that energy use and manufacturing will continue to decarbonise over time.
Under the decarbonised scenario, end of life demolition, removal of materials and replacement of building elements across the lifespan are assumed to have a lower carbon impact than they do now.
Selected project details
Client: The Department of Education
Main contractor/volumetric modular builder: Lidan
Project architect: AXIS Architecture
Consulting engineer/energy consultant: TEM Engineering & Management DAC
Civil / structural engineer (foundation): Malachi Cullen Consulting Engineers
Civil / structural engineer: MMOS Engineers
Embodied carbon consultant: John Butler Sustainable Building Consultancy
Mechanical contractor: Frank Roche Air-Conditioning LTD
Electrical contractor: Lidan
Airtightness tester/consultant: 2Eva
Fasteners and connectors: Rothoblaas
Cellulose insulation, tapes and membranes: Isocell
Wood fibre insulation: Ecological Building Systems
Airtightness products: Isocell
Windows and doors: Rationel
Internal doors and glazing: Loughnanes Joinery
Cladding supplier: MTS
Fit-out: Lidan
Fitted classroom furniture, coathooks, wet areas: Western Postform
Flooring: Forbo, via MJ Flooring
Roofing: Lidan
Drainage, paving and landscaping: Vision Contracting
Insurance: Gateway Insurances
Electrical radiators and lighting: Kellihers / CT Electric
Mechnical ventilation supplier: Daikin, via Frank Roche Air-Conditioning LTD
Access control doors: Colemans Electrics
Sanitaryware: Chadwicks
Project overview
Building type: 1,000 m2 permanent school, built using a volumetric modular timber frame system.
Site type & location: Greenfield site, Birr. Co. Offaly
Completion date: January 2024
Budget: Not disclosed
Passive house status: Designed to passive house principles. Not certified.
Space heating demand: 22 kWh/m2/yr (provisional, calculated in PHPP)
Heat load: 10.4 W/m2 (provisional, calculated in PHPP) Overheating: 0 per cent above 25C (provisional, calculated in PHPP)
Number of occupants: 4 Classrooms + 1 fully equipped special educational needs base. Maximum capacity c.100 pupils.
Energy performance coefficient (EPC): 0.33
Carbon performance coefficient (CPC): 0.26
Non domestic BER: Draft: A1, with a score of 0.16, and 11 kWh/m2/yr, pending the PV array installation. Embodied carbon (Cradle to grave total): 488.2 kg CO2e/m2 GIA
Heating bills: Calculated at €1,095/yr (or €91/month) based on information from the school principal, including a Flogas 24 hour rate of 24.79C per kWh, assuming 16 radiators running for four hours per day from November to February. This figure may drop substantially when the 16 kWp PV array is installed, subject to a winter sun-oriented design, to reflect the potential for PV to assist a building with a use and load profile unusually well matched to winter sun.
Airtightness: 0.64 ACH at 50 Pa
Ground floor build up: (Inside to out) Forbo Marmoleum flooring; plywood; OSB; airtight membrane; I-joist insulated with Isocell cellulose insulation; Smartply OSB3; breather membrane; treated lath ground floor, Cemrock baseboard on precast concrete ground beams. U-value: 0.125 W/m2K Walls build up: (Inside to out) Plasterboard; service void; Finsa Vapourstop racking board; mm timber frame insulated with Isocell cellulose insulation; Smartply OSB3; Gutex Multitherm; breather membrane; ventilated cavity; charred Siberian larch cladding. U-value: 0.155 W/m2K
Flat roof build up: (Inside to out) Plasterboard; service void; Finsa Vapourstop racking board; I-joist insulated with Isocell cellulose insulation; OSB3 ; windtight breather membrane; a truss to create a fall and ventilated cavity; tongue and groove OSB; breather membrane; metal standing seam roof. U-value: 0.125 W/m2K
Windows and external doors: Rationel Auraplus timber aluclad windows and doors. Ug-value: 0.53 W/ m2K. Whole window U-value: 0.79 W/m2K
Heating System: WLS1000 iLifestyle WI-FI 1000 W6 digital oil electric radiators, and domestic hot water heat pump.
Ventilation: 14 X Daikin Vam-J enthalpy recovery ventilation units to cover classrooms, library and resource area, quiet space, multi-purpose room, multi activity area, shared activity space, special education teacher spaces and supporting teacher spaces.
Electricity: 16Kw PV solar array to be installed.
Sustainable materials: Isocell woodfibre external insulation; timber frame using C16, FSC timber.