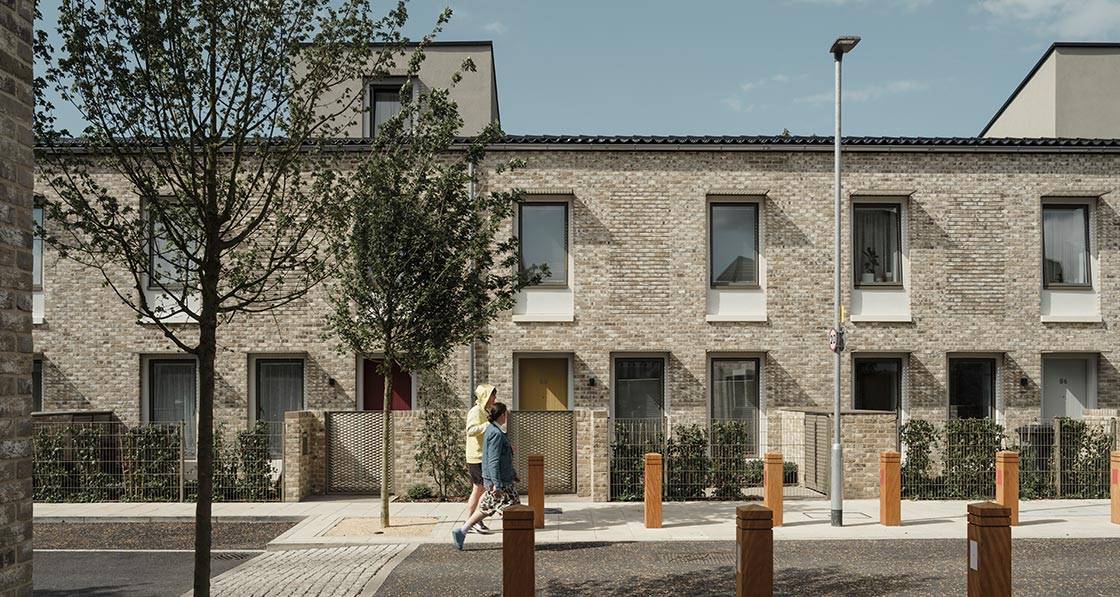
- New build
- Posted
Stirling Work - The passive social housing scheme that won British architecture’s top award
Early in October, Norwich City Council’s Goldsmith Street development become both the first passive house and the first social housing project to win the Stirling Prize, British architecture’s most coveted award, with the judges calling it “high-quality architecture in its purest, most environmentally and socially conscious form”. Leading building energy expert Dr Peter Rickaby visited the scheme for Passive House Plus to see this ground-breaking project for himself.
Local authority housing is at last being revived in the UK. For nearly four decades new developments in the social housing sector have been dominated by housing associations or ‘registered providers’ – ever larger, ever more corporate organisations, ever more exclusively focussed on unimaginative regulatory compliance, ever more wedded to procurement by design-and-build, despite its endless legacy of defects and poor performance. Against this backdrop, new local authority housing is blowing a breath of fresh air through the sector.
Nowhere is this more evident than in Norwich, where the city council has an extensive programme of new homes, is committed to quality and sustainability via the passive house standard (with over a thousand passive homes in its development programme) and is willing to innovate, experiment and challenge convention.
This article was originally published in issue 32 of Passive House Plus magazine. Want immediate access to all back issues and exclusive extra content? Click here to subscribe for as little as €10, or click here to receive the next issue free of charge
The combination of Norwich City Council’s sustainable community development policy and architects Mikhail Riches’ professional and technical skills has resulted in an outstanding new housing scheme that is not only passive house certified but has won British architecture’s top accolade – the Stirling Prize. It is fitting that, as we move towards net zero-carbon new housing, the Stirling Prize has been awarded to a social housing scheme for the first time.
The housing development at Goldsmith Street originated from a RIBA competition, for which Mikhail Riches submitted a passive solar design laid out in parallel east-west terraces arranged to admit low-angle winter sun to the homes, in order to benefit from solar heat gains, and to exclude the high-angle summer sun. Norwich City Council’s subsequent request to apply the passive house standard informed and focused the energy strategy for the resulting design.
The passive solar approach was retained. Terraces of two-storey houses have been spaced to preserve solar access to the south-facing ground-floor spaces in every house, but a cleverly placed and oriented expanded metal brise-soleil over every south-facing window shades out the high-angle summer sun to reduce overheating.
‘An urban feel, and sense of community’
New local authority housing is blowing a breath of fresh air through the sector.
The blocks are spaced 14 m apart between fronts, and 14 m between backs (rather than the more conventional 22 m spacing) to increase the density (which is 82 dwellings per hectare) and promote an urban feel, and a sense of community. The terraces are terminated at each end by three-storey blocks of three flats each.
The details of the layout demonstrate the architects’ skill in defining private, semi-private, shared and public external spaces between the buildings. Every south-facing house has some protected front garden space on the street side. Every north-facing house and flat has a small sheltered external porch, and every flat has its own entrance door at street level – there are no internal ‘common parts’. Every house also has a private rear garden and every flat has a substantial balcony with a pierced brick balustrade for privacy.
A modest masterpiece
The judging panel for the 2019 Stirling Prize, which was chaired by leading architect Julia Barfield, said of the project:
“Goldsmith Street is a modest masterpiece. It is high-quality architecture in its purest, most environmentally and socially conscious form. Behind restrained creamy façades are impeccably-detailed, highly sustainable homes – an incredible achievement for a development of this scale. This is proper social housing, over ten years in the making, delivered by an ambitious and thoughtful council. These desirable, spacious, low-energy properties should be the norm for all council housing.”
Between the terraces are shared, sinuous, linear spaces (‘ginnels’), securely gated at each end, where neighbours meet, families gather, and children play in safety.
There is also a play area for small children, a wild flower meadow and a central landscaped space. Parking is provided on the street, and the streets connect (there are no cul-de-sacs or parking courts) but the design deters speed and fosters community.
Throughout, the hard and soft landscaping is impressive – surfaces for driving, parking, walking and playing are defined by high-quality materials differentiated by texture and colour. Front boundaries are simple metal and wire fences submerged by growing vines and shrubs. Rear gates and fences are boarded timber – just high enough to provide privacy but not so high as to intimidate or block daylight. Cheap but neatly detailed anodised expanded metal panels are used to screen bin stores and meter boxes.
Internally, two-bedroom, four-person houses are 90 m2; four-bedroom, six-person houses are 121 m2; and one-bedroom, two-person flats vary from 52 m2 to 64 m2 according to floor level. House layouts vary according to whether they are entered from the north or the south. In the houses, all rooms are daylit except for ground floor WCs; in the flats, the bathrooms are the only internal spaces without windows.
The houses have living areas and generous kitchens including dining spaces.
The flats have smaller kitchens, with combined living and dining spaces. All homes are bright and spacious, with high quality finishes and tall windows. Windows that are close to the street, or south facing, have internal timber shutters, and most residents have fitted blinds for privacy and to control glare.
Passive-grade timber frame
All homes are bright and spacious, with high quality finishes and tall windows.
The buildings are timber-framed, using panels manufactured off-site by passive house veterans Cygnum. Walls incorporate Warmcel recycled cellulose insulation within the panels and rigid insulation boards on the outsides. The front elevations of the houses, and the blocks of flats, are clad with light-coloured clay bricks; the rear elevations of the houses are simply rendered (a value engineering casualty), and the render is coloured to match the brickwork.
To achieve passive house insulation standards, the brick-clad walls are approximately 600 mm thick, including the cladding, and the rendered walls are approximately 500 mm thick, so windows have deep, insulated reveals, sills and soffits. Window openings, which are larger than the windows themselves, expose the rendered insulation layer externally as window surrounds, and have pre-cast concrete sills.
The windows themselves are triple glazed Idealcombi Futura+ composite units with powder-coated external sills.
The roofs are mostly shallow pitched (~30 degrees), facing north or south, with some steep pitched (~80 degrees) roofs on the larger houses and blocks of flats. All roofs are covered with shiny black glazed pantiles, with minimal eaves overhangs and clipped verges. The average tested airtightness of the building envelope for the development is 0.57 air changes per hour at 50 Pascals (see ‘In detail’ for more).
All homes have central heating systems consisting of gas-fired condensing boilers supplying heat to radiators, and hot water. Ventilation is provided by Paul passive house certified MVHR systems. Internal air quality is excellent, and residents report minimal use of the heating. For architectural reasons all flues and ventilation terminals are located on the rear elevations.
There is scope for solar photovoltaic (PV) panels to be added to the south-facing pitches, in the future, to bring the energy performance of the homes close to ‘net zero carbon’.
(above) Drone shots of the site on the west side of Norwich city, showing progress from the beginning of works to the completion of the build.
'Elegant, beautifully detailed'
Architecturally, the quality of Goldsmith Street derives from three features. First, the simple built form of parallel straight terraces of two-storey houses ‘book ended’ by the blocks of flats. The terraces are a local built form that integrates the development into the area. The flats not only increase the scale, presence and urban feel of the buildings but also define the individual terraces and subtly mark the entrances to the development, without in any way separating residents from their neighbours living in the houses.
The second feature is the traditional, almost Georgian, proportions of the elevations. Often when the form of a building is simple and repetitive it is the windows that provide the opportunities for architectural expression, for rhythm and proportion. Mikhail Riches have exploited this opportunity with architectural skill that is rarely seen in modern housing.
The visual enlargement of the window openings by exposing the insulated wall behind the brick cladding as window surrounds (especially below the windows) is inspired. The subtle ‘ghost window’ treatment of the panels of brickwork and render where there are no windows, in order to retain the rhythm, is clever and displays an architectural sense of humour.
The third feature is simply attention to detail. I have often remarked that the energy ‘performance gap’ in modern buildings is an attention to detail deficit, and that the passive house standard not only requires attention to detail but also identifies which details are important. At Goldsmith Street attention to detail has been applied not just to the performance of the buildings but to their construction, appearance and style. The thoroughness and consistency of the detailing helps to turn buildings of simple form into architecture.
It is to Norwich City Council’s credit that the Goldsmith Street development was procured traditionally, not by design-and-build.
The architects’ commission extended through the construction phase, enabling them to inspect progress and quality on site, uphold the importance of architectural features and attention to detail, and help the contractor RG Carter to cope with the demands of the passive house standard.
(above) Graphic showing how the shading design of the terraces is confi gured to allow in low angle winter sun, but to block out the high angle summer sun that is associated with overheating; 14 metre spacing between rows (as opposed to the conventional 22 metres) helps to create an urban feel.
It is often said that great architecture requires not only a skilled architect but also a committed client who shares the architect’s vision of what their project could be like and holds them to that vision. It is a credit to both Norwich City Council and Mikhail Riches that their strong, positive relationship has delivered this elegant, beautifully detailed, high-performance housing development that sets a standard for local authority housing in the future.
Goldsmith Street is a demonstration that energy performance can be combined with superb place-making, and that architectural quality and the passive house standard can go hand-in-hand, through rigorous, consistent attention to detail. Residents of Goldsmith Street declare themselves delighted with their new homes. During my visit one couple, residents of a flat, stated that their friends who have struggled to buy their own homes elsewhere are envious of the quality and comfort of the accommodation they have. It is difficult to think of a better recommendation than that.
1 Grey EPS around the foot of the buildings to prevent thermal bridging here; 2 bringing the Cygnum timber frame panels to site; 3 the panels, which feature a two-stud system, stacked on site prior to installation and insulation; 4 the timber frame structure going up for one of the terraces, with pro clima Intello airtightness membranes installed; 5 pump-filling the walls with Warmcel recycled cellulose insulation; 6 pro clima Solitex Plus breather membrane installed on the roof with battens externally, prior to installation of the clay pan tiles.
Passive house for your water system
By Toby Cambray, Greengauge
The space heating and hot water at Goldsmith Street are delivered by combi boilers, with a small number of radiators, and carefully optimised hot water distribution.
“We designed the hot water layouts using the principles in the AECB water standards, which are completely brilliant and really under-rated,” says Sally Godber of passive house consultants WARM. “They are like passive house for your water system. The key is to calculate everything and keep dead-legs to a minimum in both length and diameter, which reduces distribution losses. These losses impact both energy consumption and overheating, so it’s a massive win.”
“For future projects there are some things we might change; primarily we need to consider less carbon intense options for hot water heating.”
Ventilation is via a Paul MVHR unit in each dwelling. The design was carefully developed so most homes have a very simple, repetitive layout which means the quality of installation (particularly key for insulating ductwork) is dependable. This was coordinated in 3D with specialist technical support from the Green Building Store, who supplied the Paul systems. “The design manages to conceal all services in a pretty tight design, so the very accurate model proved very useful on site,” says Adam Lane of Greengauge.
One of the least obvious but most challenging aspects of a project like this is the coordination of the utilities. “The architects challenged us to avoid having meter boxes scattered everywhere,” says Hannah Jones of Greengauge.
“This is much easier said than done, because the normal approach has developed from a combination of safety features and ease of installation and meter reading. It was hard work to do something diff erent, but the result is no white boxes cluttering the façade.”
WARM and Greengauge worked together on the building services design; WARM led the mechanical design whilst Greengauge undertook the electrical design, BIM modelling and design of the utilities.
Making 105 building envelopes airtight
As with any passive house project, airtightness was one of the major challenges at Goldsmith Street, where there were 105 different building envelopes to be air-sealed and tested. Leading Irish manufacturer Cygnum Building Offsite supplied the timber frame for the job. And while the firm has extensive experience working on large passive house buildings in the UK, the company’s managing director John Desmond told Passive House Pus that a project like Goldsmith Street, where building fabric detailing is multiplied over 105 units, presented a different type of challenge.
“While it doesn’t bring the major structural challenges, it does bring its own operational challenges,” he says. “This project was built to a pretty ambitious and challenging build programme. We started works on site on 17 June and completed all the blocks, bar one, by that Christmas. At any one time we had three to four crews on site with different tasks.”
“The first crew erected the structural framework of the building — the internal leaf of the external walls, the mid floor, and the roof structure. That was followed on by a team erecting the external timber frame leaf, then a third team finishing off the airtightness detailing. Finally, we had a crew fitting the Warmcel insulation. We sent about four articulated lorry loads of timber frame to site every week.”
Cygnum were responsible for ensuring the airtightness of the timber frame up until the installation of the windows and building services. Three air tests were carried out on each dwelling: the first when Cygnum completed their installation, the second after building services and windows were fitted, and the third on practical completion.
All the houses were tested individually: the best final result was 0.39 air changes per hour, the worst was 0.63 (the backstop for passive houses being 0.649). The development was passive house certified terraceby- terrace, with an average overall score for the whole development of 0.57.
Desmond says that a collaborative spirit was key to the success of the project. “Everyone needed to be moving in the one direction, and that was very much an overriding characteristic of this job.”
Selected project details
Developer: Norwich City Council
Architect: Mikhail Riches
Contractor: RG Carter
Timber frame: Cygnum Building Offsite
Landscape architects: BBUK Landscape Architecture
Clerk of Works: Enhabit
Passive house consultant: WARM
Building services design: Greengauge & WARM
Passive house certification: Etude
Structural engineer: Rossi Long
Quantity surveyor: Hamson Barron Smith
Windows & doors: Idealcombi
External insulation: Permarock
Cellulose insulation: Warmcel, via PYC Group
PIR: Celotex
Floor insulation system: Forterra
Thermal blocks: Foamglas/Thermalite
Perimeter subfloor insulation: Jablite
Airtightness products: Ecological Building Systems, via Green Building Store
OSB: Medite SmartPly
MVHR: Paul, via Green Building Store
Gas boilers: Vaillant
Radiators: Stelrad
In detail
Building type: Social housing scheme of 45 houses & 60 flats, all timber frame. Floor area from 51 m2 to 121 m2.
Location: Goldsmith Street, Norwich
Site size: 1.2809 ha
Net density: 82 dwellings/ha
Completion date: 2019 (all residents had moved in by June)
Budget: £14.5m / £1,875 per m2 (the latter figure excludes professional fees)
Passive house certification: Certified (passive house classic) (PHPP information below is for one terrace of 11 dwellings. The development was certified terrace by terrace)
Space heating demand (PHPP): 13 kWh/m2/yr
Heat load (PHPP): 10 W/m2
Primary energy demand (PHPP): 115 kWh/m2/yr
Heat loss form factor (PHPP): Terrace form factor ranges from 2.66 to 2.85
Overheating (PHPP): 4.8% of year above 25C
Airtightness (at 50 Pascals): 0.57 air changes per hour. This is the average for all blocks. The airtightness test was carried out home-by-home and then an area weighted average used. Each home passed the air test individually as well. The worst score was 0.63 ACH, the best 0.39 ACH.
Energy performance certificate (EPC): Generally, in the range of B82 to B87.
Measured energy consumption: Not yet available.
Energy bills (measured or estimated): We estimate annual space heating only bills of approximately €31, €55 and €74 respectively for the three sizes of dwellings based on PHPP space heating demand, gas price of 4.3p per kWh (confusedaboutenergy.co.uk, includes VAT) & boiler efficiency of 90%.
Ground floor: 75 mm screed followed beneath by 225 mm PIR and then 150 mm
Jetfloor EPS. U-value: 0.081 W/m2K
Walls: Cygnum timber frame featuring Protect TF200 membrane externally, followed inside by 9 mm OSB and then twin-stud system featuring 38x67 mm external ‘fin’ wall & 38x89 mm internal structural stud, comprising total insulation depth of 380 mm, which was fi lled with Warmcel. Followed inside by 9 mm OSB, pro clima Intello membrane services zone & plasterboard internally. Walls finished externally with brickwork & ventilated cavity (U-value: 0.110 W/ m2K) or 140 mm Permarock external insulation (U-value: 0.083 W/m2K)
Roof: Gloss black clay pan tiles externally, followed inside by 44 x 50 mm ventilation battens, pro clima Solitex breather membrane, 12 mm Medite sheathing, 400 mm I-joist fully filled with Warmcel, 9 mm OSB sheathing, pro clima Intello Plus membrane, services zone of 44 x 46 mm battens, plasterboard internally. U-value: 0.097 W/m2K
Windows & external doors: Idealcombi
Future+ triple glazed timber frame alu-clad windows with overall reference unit U-value of 0.74 W/m2K
Heating: Vaillant EcoTEC Plus 825 combi gas boilers to each house, providing space heating & hot water. Space heating distributed via low temperature radiator system with TRVs, linked back to one central thermostat.
Ventilation: Paul Novus 300 MVHR systems to houses and some ground floor flats, Paul Novus 200 MVHR to other flats with Paul electric heating batter to intake. Passive house certified heat recovery efficiency of 93-94% & 91% respectively.
Image gallery
-
059AD00001 059AD00001
-
GoldsmithStreet_Axo_Landscape GoldsmithStreet_Axo_Landscape
-
GoldsmithStreet_House-Types_2 GoldsmithStreet_House-Types_2
-
GoldsmithStreet_House-Types_2_Axo_Flatbloc GoldsmithStreet_House-Types_2_Axo_Flatbloc
-
GoldsmithStreet_House-types-1 GoldsmithStreet_House-types-1
-
GoldsmithStreet_X-(31)-618-TYPE-A_C---FF-SOUTH-FACING-WINDOW-JAMB-DETAILS GoldsmithStreet_X-(31)-618-TYPE-A_C---FF-SOUTH-FACING-WINDOW-JAMB-DETAILS
-
GoldsmithStreet_X-(31)-619-TYPE-A_C---FF-SOUTH-FACING-WINDOW-HEAD_CILL-DETAILS GoldsmithStreet_X-(31)-619-TYPE-A_C---FF-SOUTH-FACING-WINDOW-HEAD_CILL-DETAILS
-
Location plan with north point 1 to 1000 Location plan with north point 1 to 1000
-
Location plan Location plan
-
Mikhail-Riches---Goldsmith-Street-1 Mikhail-Riches---Goldsmith-Street-1
-
Mikhail-Riches---Goldsmith-Street-2 Mikhail-Riches---Goldsmith-Street-2
-
Mikhail-Riches---Goldsmith-Street-3 Mikhail-Riches---Goldsmith-Street-3
-
Mikhail-Riches---Goldsmith-Street-4 Mikhail-Riches---Goldsmith-Street-4
-
Mikhail-Riches---Goldsmith-Street-5 Mikhail-Riches---Goldsmith-Street-5
-
Mikhail-Riches---Goldsmith-Street-6 Mikhail-Riches---Goldsmith-Street-6
-
Safe-Play-Concept-Image Safe-Play-Concept-Image
-
Site-wide-section Site-wide-section
-
Street Elevation Street Elevation
https://mail.passivehouseplus.co.uk/magazine/new-build/stirling-work-the-passive-social-housing-scheme-that-won-british-architecture-s-top-award#sigProIde847b51597