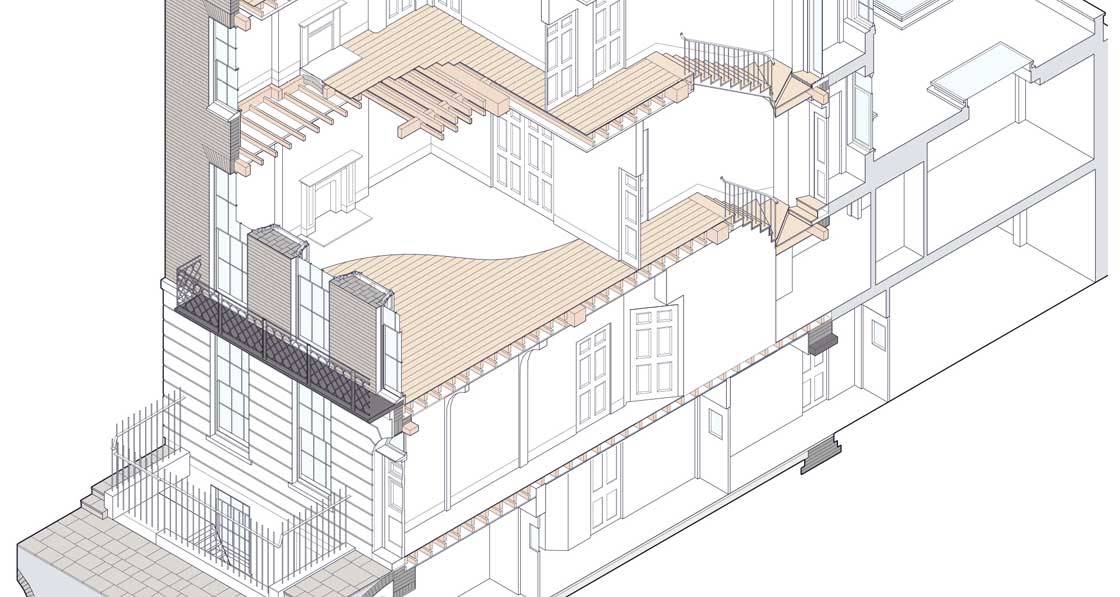
- Upgrade
- Posted
Historic London house gets near passive transformation
The default answer when you want to do pretty much anything to a listed building is ‘no’. The default assumption if you want to achieve the Enerphit standard for retrofit is ‘tackle everything’. So how on earth do you retrofit a listed building to within a whisker of the Enerphit standard — with the blessing of the conservation officer?
Click here for project specs and suppliers
This article was originally published in issue 20 of Passive House Plus magazine. Want immediate access to all back issues and exclusive extra content? Click here to subscribe for as little as €10, or click here to receive the next issue free of charge
Georgian Bloomsbury was developed in the early years of the 19th century. Fashionable then, the elegant and well-proportioned streets, with many long terraces still relatively intact, are still valued. The historic exteriors and interiors alike are fiercely protected by the planning system, and local authority conservation officers.
When Bob Prewett of Prewett Bizley Architects was approached for help with turning this five-storey Georgian house in Bloomsbury back from an office building into a family home, and an Enerphit-standard home at that, he knew it would not be straightforward. But he also believed that if they could achieve Enerphit, the passive house standard for retrofit, while retaining all the elegance and historic value of the building, then an important precedent would have been set.
While the clients were keen to reduce the energy consumption of the building for their own comfort — and out of responsibility to protect the planet — architect, client and their selected contractor Bow Tie were all as concerned as the conservation officers to tread lightly with the historic fabric. And this sensitivity shines through the project.
The first stage in any retrofit is to return the fabric to good condition, to ensure it is performing optimally in its own right, and to give a safe, dry basis for insulation and other energy-saving measures. So it was here. The disintegrating cement pointing (the external part of the mortar joints) was removed, and replaced with lime based mortar, to reduce water penetration from driving rain, and allow any moisture reaching the brickwork to dry out safely. The parapets were leaning slightly inwards, not throwing water effectively away from the façades, so they were partly rebuilt and given new copings.
Inside however, most of the structure was in good condition. “There was a phenomenal amount of timber, it looked like shipbuilding,” Bob Prewett recalls. “There are effectively massive trees making the main beams with a six metre span from party wall to party wall, with cross joists notched into those, supporting the floors, with ceiling joists below.
And all the internal partition walls, everything, was made of timber.” Happily only a few small areas were rotten and needing repair.
Insulation strategy
Different parts of the building had different construction, different building physics challenges, and differing historic value, so the insulation strategies also varied. At the top (the old servants quarters) and bottom (basement) of the building, there was not much of historic interest remaining, so the challenges to overcome were mainly technical. The beautiful historic interiors were on the ground, first and second floors. They had retained their original marble fireplaces, ornate cornicing, and original woodwork, including shutters and shutter boxes.
Although the windows had been replaced in the Victorian era, they replicated the elegant sliding sashes of the Georgian originals.
The front and back façades at these levels had ‘false’ lath-and-plaster walls inside created by the original builders, to accommodate the depth of the shutter boxes without the need for an excessively thick brick wall (a lath is timber framework on which plaster is applied). This left a cavity behind the Georgian lath and plaster, which could be insulated without touching the interior decor.
One option considered was to blow cellulose into the cavity, but the blower might have put pressure on the old construction, and there were also concerns about exposing the cellulose to moisture risk from the exterior brick, says Bow Tie director Rafael Delimata.
The team opted to use vapour-open Icynene pour-formula. Delimata says this approach – which had been analysed in a monitoring and simulation study in a lath and plaster sandstone wall – worked well. Bow Tie find that the liquid formula fills even irregular cavities easily, and it greatly increased the airtightness of the walls.
So long as it is specified and installed with care, both Bob Prewett and Bow Tie believe Icynene foam to be a useful product.
Bow Tie have their own rig so they have full control over the installation. “Our team are fully trained to use it. We also inspect the substrate carefully, and check the U-values and carry out condensation risk analysis.” Delimata says. Stormdry repointing additives were mixed in to the lime mortar for repointing the elevations.
“We have not found a more environmentally friendly option for those jobs where really you cannot easily insulate any other way, and it is cost-effective,” says Delimata. The party walls also had to be insulated. Even a few degrees temperature difference in the adjoining space (for example if neighbours were absent) would add considerable heat loss, given that the party wall area is so large (around double the area of the façades). In the middle storeys the party walls had the same decorative woodwork and cornicing as the elevations, but no cavity. And as well as being insulated, these walls had to be made airtight.
Remarkably this was achieved within the 30-40mm depth made available by removing the existing plaster. The old brickwork was made airtight with a lime parge, and the walls were then lined with 20mm of Aerogel [an extremely high-performance synthetic insulant] on a 10mm magnesium oxide board, giving a U-value of around 0.23, then finally skimmed. It was a lot of Aerogel – and it isn’t cheap. As Delimata recalls, when the insulation arrived “it was the most expensive pallet ever!”
Basement, attic and roof
The basement was damp, “but we would never have got to the bottom of where it was coming from,” Bob Prewett says. So the basement walls were lined with a cavity drain tanking system (“probably overkill,” Prewett suspects). On top of this tanking membrane was a layer of Icynene, but given the proximity to damp, not the vapour open system, but instead the waterproof closed-cell formulation.
In the top storey (the former servants’ quarters) few historic details remained.
Internal insulation was with Pavadry wood fibre boards, which interlock in a tongue-andgroove system, with the joints taped for extra airtightness. “Pavadry is nice to use, it’s very robust and would withstand a lot of abuse,” Delimata notes. The ceiling was made airtight with OSB board, while 50mm of glassfibre in the attic was replaced with 300mm of cellulose, which has recently been checked and is very dry.
Airtightness/windows
The airtightness strategy was all internal: lime parge was used extensively, though in places this role was fulfilled by insulation (and taping) instead. To maintain airtightness upgrade the lime parge was allowed to dry slowly, to prevent cracking, before other layers were added. “This appears to have held very well,” Prewett says.
However there were also a lot of junctions to deal with, often complicated by additional structural penetration such as floor beams.
Parging up to the beams and taping was done where possible, but to fill some of the really inaccessible gaps, open-cell Icynene foam was used, to tackle heat loss and reduce air leakage.
Internal insulation around penetrating timbers is thought to be safe so long as the timbers are dry to begin with, the insulation around them is vapour open (to allow timbers to dry into the warm interior if needs be) and the U-values are not too onerous. “The walls were in fact pretty thick, and the insulation was a modest layer, this meant we were allowing a bit of warmth back into the wall, to keep the timbers warm. We didn’t go below about 0.3,” Prewett explains.
He adds: “The beauty of a tall terraced house is the excellent form factor. The exterior walls are quite a small proportion of the surface, which means you don’t need to get a very low U-value to achieve thermal performance of Enerphit or close to.” In the basement, the tanking membrane proved hard to make airtight, but once the foam insulation had been installed, the airtightness was much improved, Prewett says.
The original fireplaces also had to be made airtight, which was quite tricky, Prewett recalls. “The chimneys were filled with vermiculite. We grouted and sealed the marble chimney pieces and the cast iron surrounds, and parged the backs, which was fairly successful, even though the old brickwork is like a honeycomb, there are so many gaps in the mortar.”
“Achieving 1.1 air changes per hour, given the challenges, is quite remarkable and shows how airtight even challenging projects can be made, given a team who are committed and conscious of the issues.”
Historic windows
But the biggest issue faced by the team was obtaining listed building consent for the proposed alterations and in particular, for the secondary glazing system. It took over 18 months to get the go-ahead for this, which was a “huge headache” for the sequencing of the build. “It caused a lot of pain to the contractor.” Prewett says.
Eventually, and after repeated, slightly different applications, the conservation officers gave them the go-ahead — though not before the sash windows and boxes had been taken apart once to repair the windows, then reinstalled for inspection.
The secondary glazing is an evacuated double skin pane only 6.2mm thick, on extremely slender frames. The U-value of the glazing is quoted as 1.0, the figure used in the calculations, though in-situ testing of this system for Historic Scotland has suggested a marginally better U-value in reality, of between 0.6 and 0.8.
The whole system is fitted between the sash window and shutter box, so it is really inconspicuous. On the larger windows the secondary glazing is in sliding sashes mirroring the main windows; the smaller windows have casements.
Unfortunately, because the permission took so long to be granted, the build had to proceed with the possible end point of single glazing only, meaning designs and preparations were made for a supplementary heating system. The heat pump and low-temperature underfloor heating specified for the Enerphit-level fabric would not have been adequate in this scenario.
(above, from left) the timber frame extension to the rear under construction; the disintegrating cement pointing was removed, and replaced with lime based mortar to reduce water penetration from driving rain; the top storey was internally insulated with Pavadry wood fibre boards, with plasterboard outside this, while OSB to the ceiling above is taped for airtightness; ductwork for the MVHR systems, and airtightness taping around joints and junctions.
Delimata estimates these reversals and delays (including several extra visits from the airtightness tester) probably cost his firm around £5000, eating quite a chunk from their overall profit. “But we did feel we were doing something worth doing, showing that Georgian sash windows could be sensitively updated, to enable really high energy performance throughout.”
This was not just the icing on the cake. The new windows are crucial to the improved energy performance, making more of a difference to the heat loss than the wall insulation. “In these houses there is a very large glazed area, and single glazing has terrible performance, with a U-value of around five,” Prewett points out. “The windows are about 40% of the external surface area but accounted for half the heat loss — a huge amount.”
Two MVHR systems were installed by Bow Tie, one in the attic serving the upstairs bedrooms, and the other in a service riser at the back of the dwelling, to minimise the need for duct penetrations through the historic structure. “Heating is by air source heat pump and we also installed solar thermal panels, as the client was very particular about not using gas,” Delimata says.
Most of the work, including the services installation, was carried out by the contractor’s in-house multi-skilled team, rather than an army of sub-contractors. Bob Prewett believes this played an important part of the success of the project: “Most of the crew are multi-skilled, which means they understand each others’ roles, and know what the other processes are going to need, and they can join in to help catch up if one element is behind, rather than wait around, meaning work can be streamlined. It’s a real team approach,” he says.
“Rafael was there most days for the best part of a year,” Prewett adds. “You just do need that level of supervision and coordination.”
Performance
Calculating the energy performance before and after the retrofit suggests that while the heat demand of the unimproved fabric would have been around 180 kWh/m2/yr, retrofit will have slashed this by nearly 90% to 20 kWh/m2/yr.
Although this is within the limits set for Enerphit, the airtightness is slightly over the Enerphit target of one air change per hour, so the building doesn’t qualify for certification. Nonetheless, the level of energy efficiency and comfort achieved, alongside the preservation and restoration of a listed historic fabric, is outstanding.
The occupants were able to get a vivid demonstration of the impact of one aspect of the retrofit. “Because we had to wait so long for permission to add secondary glazing, the clients moved in before it was installed. It was late autumn when it finally went in, and suddenly the whole room became comfortable, instead of having one cold side. And the whole room became instantly quiet,” Prewett recalls.
“The window treatment was expensive but had a huge impact. The effect of the windows on the energy consumption, comfort and acoustics of the house is palpable when you are there.”
“So far we have just set up sensors to monitor internal air quality and electrical use. Initial review indicates good stable temperature and humidity levels, as well as low CO2 levels. The energy consumption for the first year is a bit over prediction — this may have had something to do with there still being builders on site here, plus an empty property next door for some of that time.”
At around £1.2million the job was certainly an expensive one, but the energy works did not account for the lion’s share, by any means. “A lot of the work would have had to be done anyway to achieve such a great restoration of the interiors. There were also a number of new items and fittings that cost a lot. In the end the energy efficiency work was probably only a third of the budget,” Prewett says.
Is it time to update our approach to historic buildings?
Overall the whole team is very proud of the quality of the conservation. But as Bob Prewett says, the problem with listed buildings is that “the default answer to touching anything is ‘no’”. Energy upgrades of listed buildings can be done badly of course, but to outlaw everything as default is immensely unhelpful, he believes.
“Listed buildings can contribute to carbon reduction without being spoiled. Given that many listed buildings are in the possession of people with the means to carry out this type of retrofit, it is a pity that they are usually blocked from doing so by very conservative planning views and a culture of do nothing.”
Yet with this retrofit, while achieving one of the best-ever fabric performance levels for a listed building, the conservation officer was so delighted with the outcome they wanted to take photos, as Delimata recalls, “to show other people how it should be done”.
Perhaps these photos should be shared far and wide amongst the conservation officer community, to make them just a little less frightened of allowing the owners of listed buildings to protect the future. As this retrofit shows, it doesn’t have to mean you lose the past.
Selected project details
Architect: Prewett Bizley Architects
Interior designer: Emily Bizley Interior Design
Passive house design: Prewett Bizley
Contractor: Bow Tie Construction Ltd
Quantity surveyor: Mark Hammond
Structural engineer: Studio Park
Wood fibre insulation: Natural Building Technologies
Lime plaster: Lime Green
Blown cellulose insulation: Warmcel
Aerogel MgO board: Thermablok
Sprayed insulation (open and closed cell): London Insulation
Airtightness products: Ecological Building Systems
Ground floor & flat roof insulation: Kingspan Insulation UK
Windows & doors: Selectaglaze, Double Good
Parquet flooring: Luxury Wood Flooring
Solar thermal & air source heat pump: Chelmer Heating
Wall paints: Keim
MVHR: Paul, supplied by Green Building Store
LED downlighters: Photonstar
External blinds: Reflex-Rol UK
Aluminium rainwater goods, external railings and other sundry metalwork: Brian Cherry
Additional info
Building type: Four-storey over basement, 1820s terraced townhouse with 20th/21st century extension at the rear.
Location: Bloomsbury, London
Budget: £1.2m
Before: 180 kWh/m2/yr
After: 20 kWh/m2/yr
HEAT LOAD (PHPP)
Before: 163 W/m2
After: 17 W/m2
PRIMARY ENERGY DEMAND (PHPP)
Before: Not modelled
After: 114 kWh/m2/yr
AIRTIGHTNESS (AT 50 PASCALS)
Before: >10 air changes per hour
After: 1.1 air changes per hour
BASEMENT FLOOR
Before: Carpet over cement screed over a concrete slab. U-value: 2 W/m2K
After: Tiles on 75mm screed with integrated UFH, on 75mm XPS, on tanking, on 50mm XPS, on existing concrete slab. U-value: 0.23 W/m2K
ORIGINAL WALLS
Before: London stock brick, with plastered walls (some plastered linings were mounted on stud work fixed to brick internally.) Approximate U-value: varied from 1.2 to 1.8 W/m2K, depending on wall thickness.
After: Lower ground floor wall: taped OSB on studs on lime page, with vapour closed spray-foam insulation between. U-value: 0.27 W/m2K
Mid floors: Existing lath and plaster lining on studs with vapour open poured insulation between. U-value: 0.22 W/m2K
Top floor: Plasterboard on battens over taped wood-fibre insulation boards, fixed to lime-parged faced. U-value: 0.3 W/m2K
Party walls: Lime plaster on MgO board faced Aerogel, fixed to lime parged walls. U-value: 0.23 W/m2K
EXTENSION WALLS
Before: Brick with poor tanking system and dry lined. Approximate U-value: 2 W/m2K
After: Taped OSB on studs with vapour open sprayed insulation between. U-value: 0.27 W/m2K
Lime rendered wood-fibre insulation boards applied to a timber frame with mineral wool insulation between. U-value: 0.1 W/m2K
MAIN HOUSE ROOF
Before: Slate tiles on roofing felt over double pitched timber rafters. 50mm of glass wool between ceiling joists (below vented double pitched roof). U-value: 1.2 W/m2K
After: Slate tiles and roofing felt repairs. 300mm cellulose between and above ceiling joists. OSB installed to underside of existing ceiling joists. All joints and junctions taped with Pro Clima tapes. U-value: 0.12 W/m2K
SPACE HEATING SYSTEM
Before: 30 kW gas boiler.
After: Wet under floor heating to all spaces excluding third floor, which uses low temperature radiators. Supplied by buffer tank connected to one air source heat pump.
HOT WATER
Before: Commercial - local electrically heated hot water in WCs.
After: Solar panels connected to a 500 litre hot water tank and air source heat pump.
VENTILATION
Before: No active ventilation system. Reliant on infiltration, chimney and opening of windows for air changes.
After: Two Paul Novus 300 MVHR systems.
Effective heat recovery efficiency of 93%
Image gallery
-
Bloomsbury House Bloomsbury House
-
Bloomsbury House heat demand Bloomsbury House heat demand
-
Bloomsbury House page 1 Bloomsbury House page 1
-
Bloomsbury House page 2 Bloomsbury House page 2
-
Bloomsbury House page 3 Bloomsbury House page 3
-
Bloomsbury House page 4 Bloomsbury House page 4
-
Bloomsbury House page 5 Bloomsbury House page 5
-
Bloomsbury House page 6 Bloomsbury House page 6
-
Bloomsbury House page 7 Bloomsbury House page 7
https://mail.passivehouseplus.co.uk/magazine/upgrade/historic-london-house-gets-near-passive-transformation#sigProId6703c7faca