- Design Approaches
- Posted
Zero waste
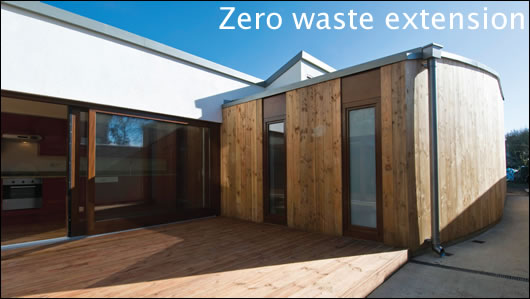
Upgrading and extending a semi-detached house on a tight site in Limerick required ingenuity from architect Patti O’Neill. John Hearne describes a design approach defined by a commitment to avoid the waste of space, sunlight, and the unsustainable use of materials.
Architect Patti O’Neill’s house extension in Limerick city expresses a design philosophy centred on zero waste. She has taken a range of natural, low embodied energy materials and created a living space that blends smoothly into the suburban landscape. Careful modelling and minute attention to form, orientation and layout make optimum use of solar gain, thereby reducing reliance on renewables to generate heat.
“The zero waste concept originates in efforts to reduce defects in the Japanese manufacturing industry,” O’Neill explains. “They force attention onto the lifecycle of products which encompasses design, waste reduction, reuse and recycling. Approximately 40% of waste generated globally originates from construction and demolition of buildings.” In the Limerick extension, O’Neill specified natural, recycled and recyclable materials, including sheep wool insulation, wood fibre insulation board, timber, GGBS concrete, a sedum roof and passive ventilation. Using a breathable wall construction, she minimised both U-values and cold bridges to produce a well insulated external envelope.
O’Neill points out that vernacular architecture was all about the spaces between buildings – a central courtyard enclosed by dwelling house and outbuildings. Her extension echoes this approach. The 70m2 structure comprises a galley kitchen, living room and corridor leading to a bathroom and bedroom, which form a courtyard of 20m2 and terrace to the garden of 10m2. The existing one-storey garage and utility room were removed, allowing separate access to the garden, and restoring the original volume and beauty of the 1930s two-storey house.
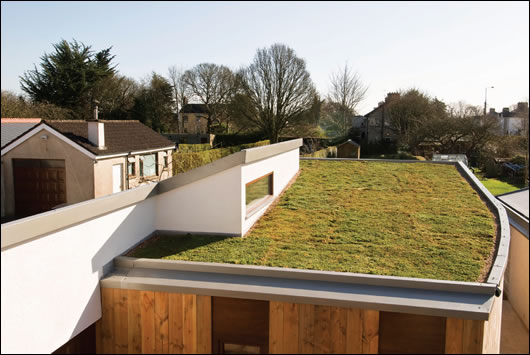
The sedum roof sits on the western side of the extension and is flanked on the eastern side by a pitched roof rising from east to west
In marked contrast to the double height extensions on neighbouring houses, O’Neill chose instead to push the single-storey extension into the long, narrow garden, and laid out the space to maximise natural heating and lighting solutions. The living room and bedroom sit side by side at the rear of the extension, with extensive glass facades to make full use of the southerly aspect. The living room leads directly into the galley kitchen which forms the eastern flank of the exterior courtyard, then continues on into the body of the main house. Ingeniously, the bedroom roof is precisely engineered to ensure that even on the shortest day of the year, southern sun reaches into the courtyard, and from there is dispersed into the old house through the large sliding glass doors. Achieving the right slope required 3D sunlight studies to determine the optimal angles to catch both winter and summer sun. In addition, O’Neill had to carefully manipulate the internal layout of the extension.
The living and bedroom spaces were situated to the rear of the extension, and the short corridor and bathroom to the front, thereby giving the necessary slope to allow the sun access into the courtyard throughout the year. While the interior floor levels of the main house and the extension are continuous, the bedroom is raised by two steps to create a steeper angle for the roof. Consistent with her overall design philosophy, this approach also allowed O’Neill to follow the contours of the site, thereby minimizing excavation work and allowing the structure to sit more comfortably in the landscape. Further careful planning on the roof itself – which is sedum – was also required. The upstand enclosing the sedum had to be set back and reduced to ensure there was no obstacle to the winter sun’s access to the courtyard.
Viewed from the upstairs bedrooms, the sedum roof provides a connection with the long, narrow garden beyond, O’Neill explains. The sedum sits on the western side of the extension and is flanked on the eastern side by a pitched roof rising from east to west. The idea here, O’Neill explains, was to provide a window at high level in the living room, which will allow western light into the space throughout the year, again reducing the necessity for artificial lighting. The combination of roofs in a tight footprint was, she acknowledges, an engineering challenge. Making it work required close collaboration between designer and engineer. Visually, the effect is striking. “There is geometric play between the two volumes,” says O’Neill. “The long, angled, cold roof that connects to the timber clad grass roof. It embraces it almost, so they are two separate volumes but they interact, they’re interlinked.”
Having designed the building, O’Neill set about drawing up a spec from scratch. It was a process that she quickly found fed back into design again. Designating natural materials led directly to a breathable wall construction. “At that point I realised my ambition that I had achieved with the design, now I wanted the same level with the materials. I wanted to use natural materials and I didn’t want to cause waste. I didn’t want to use membranes.”
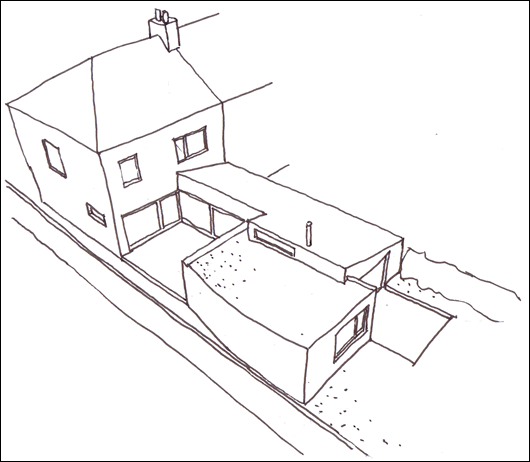
The super-structure is timber frame, filled with sheep’s wool and clad in wood-fibre board from renewable resources, forming a breathable wall system which allows for a natural regulation of moisture. “Having learned all about breathability, I’ve become a big advocate of that approach. Airtight membranes for me are like living in a plastic bag.” The wall build-up allows water vapour to pass from the interior to the exterior, but makes it difficult for vapour to make the return journey. “The least permeable materials – like the racking board – are on the inside. That will stop vapour from coming in but it does allow it to diffuse out through it.” O’Neill doesn’t anticipate any loss in thermal performance through the absence of an airtight layer. She believes that breathable wall construction is particularly suited to Irish conditions. “It addresses the whole condensation issue. Ireland is a saturated vapour country. There is so much moisture in the air that we need to deal with it instead of blocking it out with paints or concrete or vapour-impermeable materials.”
The 100% sheep wool insulation comes from Sheepwool Insulation in Co. Wicklow. Fully natural and biodegradable, sheep wool is a hygroscopic material, meaning it can absorb and release moisture without reducing its thermal efficiency. It’s also an easy product to work with and doesn’t support combustion. The wood fibre board used in the project is the timber frame Pavaclad system from Econstruction Products in Dublin. Pavaclad systems use Pavatex wood fibre boards over the outside of the frame in a continuous layer, with the racking board on the inside of the structure. Econstruction’s timber frame Diffutherm System was also used where the timber frame required a render finish. The Diffutherm system also uses Pavatex woodfibre boards, which are then overlaid with a mineral-based, thin render.
Of the two extension roofs, one is of cold construction, while the sedum roof is warm. The waterproofing membrane under the sedum is Sintofoil TPO/FPA, composed of a polymer base which excludes chlorine, lead or other heavy metals, and is totally recyclable. “If I had to use a plastic for the roof membrane, then it had to be the most ecological one that there is,” says O’Neill. The Sintofoil TPO/FPA was supplied by Moy Materials and installed by Grange Roofing.
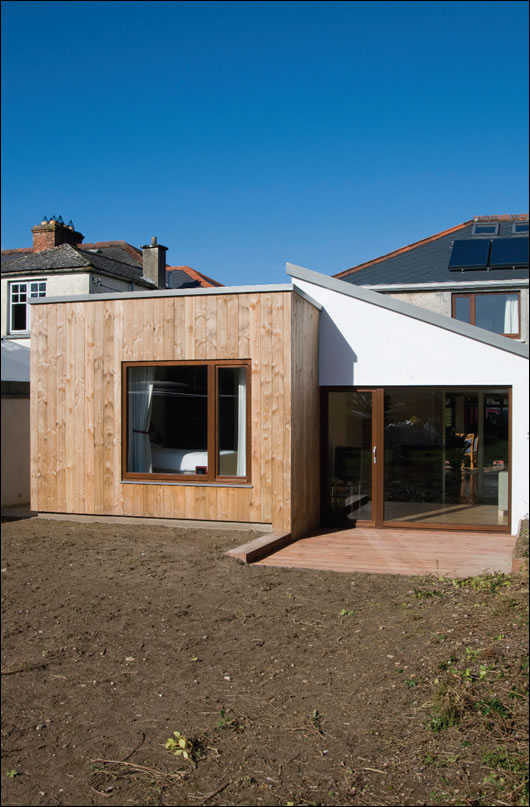
The living room and bedroom at the rear of the extension have extensive glass facades to make full use of the southerly aspect
The windows were provided by Youghal Glass in Nenagh. Custom built by the company’s Polish partners, they are manufactured from certified hardwood, and incorporate soft-coat low-e glass, a warm-edge spacer bar, and provide a whole unit U-value of 1.3 W/m2K. The very large sliding doors accessing the courtyard on two sides – from both galley kitchen and from the existing house – presented another engineering challenge. In order to preserve the clean flow of light from old house to new structure, O’Neill asked that the sliding doors meet at the corner of the court yard without any post.
A service cavity incorporated into the wall build-up houses electrical and plumbing services, while all sockets are located on external walls. The idea here was to preserve the acoustic envelope. “The living room is acoustically reinforced with SoundBloc plasterboard on either side,” says O’Neill. “It was important for me that if someone is watching TV, that someone else might be sleeping. That has been a disaster in Irish buildings. So I was anxious not to cut that acoustic layer. By not having any cables or light switches on those surfaces, we eliminated the possibility of any sound getting through. In the living room, we put cables under the floor, and fitted the TV outlets in both corners in the floor itself too, again to make sure sound can’t be transmitted through the walls.”
In keeping with the zero waste concept, O’Neill specified a foam glass gravel substructure. A by-product of the glass recycling industry, sourcing issues prevented its use in the project. Instead, the structural slab was built from reinforced GGBS concrete. This is produced from a recycled industrial by-product of steel manufacture.
Ventilation solutions were also provided by Econstruction Products. “Intellivent is a standalone vent that’s used in wet rooms,” Peter Woodcock of Econstruction Products explains. “It automatically detects moisture levels so it kicks in when it needs to. It’s demand controlled.” The house also features a Fresh 99H demand-controlled vent. “This is a passive wall vent,” says Woodcock. “It’s got a humidity sensitive mechanism inside it. When humidity levels rise within the room, the vent opens, and then when the humidity level drops, it closes without any electrical or mechanical intervention.” In keeping with the high standard of natural materials and insulation, a natural gas boiler with a warm water collection tank were installed and connected to solar panels. The ground floor level has a new Junckers FSC chain-of-custody certified solid oak wood floor throughout with underfloor heating in the new part. Junckers boast carbon neutral manufacturing facilities in Denmark. The company operates a wood-fired CHP plant to which the company’s residual wood – sawdust, wood chips, saw-cut log ends and other residual wood from the production – is supplied. As a high value and durable product, it’s reasonable to assume that the solid oak flooring is likely to be salvaged when the building reaches its end of life.
Client Jer Horan says that the house has been transformed by the extension. “It was a very cold house, now it’s much warmer, and there’s light everywhere, even when the weather is bad.” He’s also noticed a drop in heating bills since moving back in. Patti O’Neil emphasises the importance of designing the space to suit the personality of whoever will live in it. “In the end the client needs to live there, so I have to interpret their personality, their needs.”
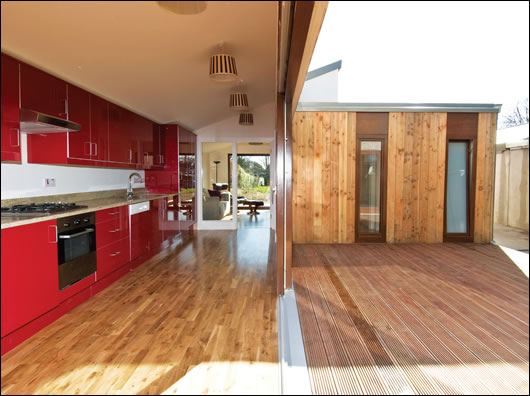
The galley kitchen is at the front of the extension and forms the western flank of the courtyard, leading into the living room
After leaving college, O’Neill spent six years researching and writing Placing Architecture, an artistic study on the connectivity of landscape and architecture. She’s now applying the philosophy developed during this project and through her commercial experience to create an architecture fully sensitised to the environment in which the building exists. A suburban extension, squeezed into a very tight space offers particular challenges to this approach. “One of the difficulties was the width of the property,” says O’Neill. “It’s quite narrow. So how do you get two rooms into it? That was just managed by also having a 1.2 metre opening to the side, so now there’s a complete connection along the side of the building, front to rear.” She emphasises that despite the challenges, it’s still possible to remain faithful to this design philosophy. “The rooms work with the contours and with the orientation, so this approach can be taken into the house in the way we live…It uses the land, the orientation and the sun in the design process.
“I thought it was important to emphasise that not everything is done through technology. So much can be done through design. You can have a really good, in tune house which is economic in its construction and in its running.”
Panels
External walls of the sedum roof extension are of timber frame construction (150mm timber stud) insulated with sheep wool, 11mm OSB3 Medite Smartply on the inside and 60mm wood fibre soft board Pavatherm Plus insulation on the outside. Douglas fir T&G on 15mm marine ply on battens provides a rain screen on the exterior, with a plasterboard finish to the inside with skimcoat.
External walls of the pitched roof extension consist of 150mm timber stud with sheep wool, 11mm OSB3 smartply on the inside and wood fibre board on the outside, with NBT’s timber frame Diffutherm System and a plasterboard finish to the inside with skim coat. Overall wall U-value: 0.21 W/m2K
Internal walls consist of a 90mm timber stud insulated with sheep wool, with 11mm OSB to either side, finished with SoundBloc 15mm plasterboard, with skimcoat.
Pitched (cold) roof build-up: Sintofoil TPO/FPA membrane, 2 x 12 OSB marine ply, 50mm counter-batten, 60mm wood fibre board, 150mm x 45mm timber rafters, 150mm sheep wool insulation, plasterboard. U-value: 0.2 W/m2K
Warm roof build-up: Sedum root zone mix, extensive roof garden set Diadem 150, Sintofoil TPO/FPA membrane, 2 x 12mm marine ply, 80mm wood fibre board, vapour membrane, 18mm marine ply, 125 x 45mm timber rafter, plasterboard. The U-value according to building regulations for flat roofs is 0.22 W/m2K. However, it is anticipated that the sedum roof will produce a substantial improvement in thermal performance.
Selected project details
Client: Jer Horan
Architect: Patti O'Neill
Civil / structural engineer: Peter Silke
Main contractor: Killuragh Brothers Ltd.
Wood fibre insulation & ventilation: Econstruction Products
Wool insulation: Sheepwool Insulation Ltd
Roof insulation: Killuragh Brothers Ltd.
OSB: Smartply
Windows and doors: Youghal Glass
Sedum roof: Grange Roofing
Flooring: Junckers
Related items
-
Steeply sustainable - Low carbon passive design wonder on impossible Cork site
-
Focus on whole build systems, not products - NBT
-
International - Issue 29
-
Passive Wexford bungalow with a hint of the exotic
-
The House of Tomorrow, 1933
-
1948: The Dover Sun House
-
The dazzling Dalkey home with a hidden agenda
-
Mayo passive house makes you forget the weather
-
A1 passive house overcomes tight Cork City site
-
Norfolk straw-bale cottage aims for passive
-
Time to move beyond the architecture of the oil age
-
West Cork passive house raises design bar