- Passive Housing
- Posted
Rathdrum passive refurb
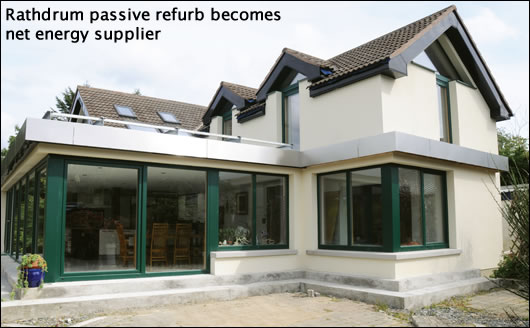
Randy Ralston and Mel Cronin aimed for the passive house standard with their upgrade, and though they didn’t quite get there they ended up with a house that produces more energy than it consumes, making it one of the country’s flagship green renovation projects.
In 2007, Randy Ralston and Mel Cronin bought a dormer bungalow in Rathdrum, Co Wicklow. While they'd loved to have built from scratch, they knew it would be difficult considering the restrictions many planning authorities place on non-locals looking to build new. So they decided to buy an existing house and renovate.
Refurbishment began soon after they bought the 35 year old house, which had seen better days. “When the wind blew you could feel it everywhere,” Randy says.
The couple had some clear goals in mind: an environmentally friendly house, low running costs, freedom from what Randy calls the "petroleum addiction loop", and to inspire others to go green. Naturally, they also wanted a comfortable and beautiful home.
The couple decided to completely remodel the inside of the house, turning its nine bedrooms into five, and bringing an angled conservatory into the main body of the house by constructing a new wall around its footprint. New timber frame sections were built in the conservatory, as well as in other areas where walls were knocked. But at 338 square metres the finished house's footprint remains largely the same as the original.
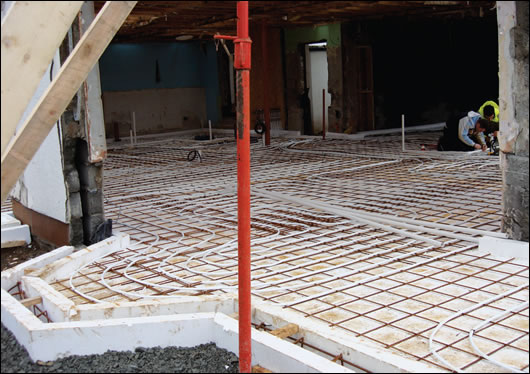
Underfloor heating pipes laid on the insulated foundation system developed by Viking House
"We used timber frame because it was cost-effective, renewable and locally produced," Randy says. "It was also faster, easier to work with, and had better thermal and vapour permeability properties than the alternatives." The couple chose locally grown pine for the timber frame, hired local labourers through Fás and managed the build themselves.
The timber frame wall build-up features 140mm and 90mm twin-wall studs filled with cellulose, with 15mm of taped and sealed OSB board inside and outside, 200mm of EPS insulation externally and a 100mm Rockwool-filled service cavity internally lined with Intello vapour check and Fermacell board. The walls have a U-value of 0.11 W/m2K.
The new flat roof in the conservatory has 150mm of EPS insulation under a fibreglass roof membrane, followed underneath by a plywood deck, nine inches of cellulose insulation, taped and sealed OSB board as the vapour control layer, and 100mm of Rockwool in the service cavity below — its U-value is 0.13 WW/m2K. Existing roof sections were renovated with 60mm of Gutex woodfibre board under the roof tiles, cellulose insulation between the rafters and a 100mm Rockwool-insulated service cavity underneath.
Rockwool was used to insulate the service cavities in the roof and timber frame sections throughout. This smart energy-efficient approach — where an airtight layer is installed inside the main timber frame, with a counter-battened insulated service cavity installed inside that — enables substantially reduced cold bridging and greater continuity of insulation. It prevents mechanical and electrical services from puncturing the airtight layer, reduces heat loss through infiltration, and reduces the risk of vapour from the room getting into the wall. The reduction of cold bridging — which would be caused by the timbers of the timber frame were it not for the protection of the additional service cavity insulation layer — not only reduces heat loss, but pushes the dew point out towards the exterior of the wall and reduces the risk of interstitial condensation and associated mould growth.
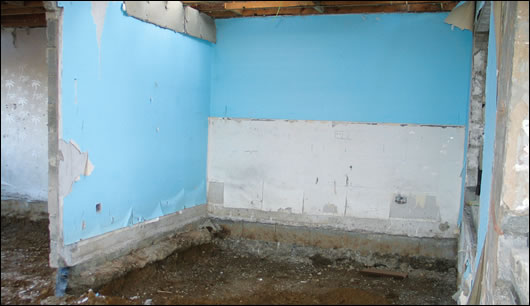
The shell of the building after it was gutted, with the sub-floor removed to enable the insulated foundation system to be installed
OSB board for the project was supplied by Smartply. The company is owned by Coillte — all its timber is sourced from Irish forests, and the company has full FSC chain of custody certification.
The house’s existing cavity walls were pump-filled with bonded-bead and externally insulated with 200mm of EPS, then lined internally with Intello vapour check, followed by Fermacell board. Their U-value is 0.14 W/m2K. All floors throughout the house are insulated with 300mm of EPS and and have a U-value of 0.12 W/m2K.
New triple-glazed Internorm windows — supplied by Ecoglaze — replaced single glazing throughout. Both the Edition and Edition 4 models were specified — the latter includes a controllable blind between the triple-glazing and a fourth separate outer pane. Both models are timber alu-clad with argon fill. The Edition units have a U-value of 0.86 W/m2K overall, while the Edition 4 has an overall U-value of 0.8 W/m2K with the blinds rolled and 0.7 W/m2K unrolled.
Randy and Mel chose triple-glazed roof windows too — timber-aluclad, krypton-filled units from Polish manufacturer Fakro, with an overall U-value of 0.94 W/m2K. Tallaght-based Tradecraft supplied the Fakro units, and the company's Ray Clarke says that while the firm initially just planned to supply the windows, they later went on site to do further airtightness sealing when Randy and Mel told him they were going for the passive house standard.
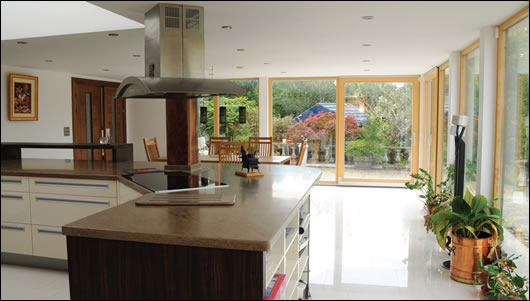
The finished open plan kitchen with energy-efficient Berbel extract hood which removes grease and recirculates warm air
Passive goals
“We started off just wanting to do the best job we could based on our objectives and within u our budget," Randy says. "It wasn't until about one-third of the way into the project that we realised what we were actually doing was building a passive house. Although that was not originally our goal, once we saw how close we were to it we held fast to it until the end.”
"It's true we did get a bit carried away with ourselves when we realised that actually going full passive seemed within our grasp," he continues. "At one point we completely downed tools and spent two weeks with a team of six people doing nothing but searching for and sealing air leaks using the blower door, air pens, smoke machines and even incense."
Trying to get the house down to passive airtightness standards involved some novel approaches. "We invented ways of sealing the recessed lighting using silicone rings, and used gargantuan amounts of fireproof acoustic mastic," Randy says. "We even had representatives from the various airtightness materials manufacturers visit the site during that time to advise us how we could improve and they could offer nothing, saying we were doing ‘everything right’”.
The house hasn't quite made the passive house standard though — while the U-values all meet the mark, the airtightness result of 0.92 air changes per hour (ACH) at 50 pascals narrowly misses the Passive House Institute's standard of 0.6 ACH.
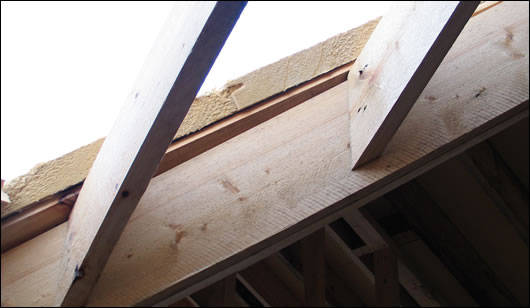
Existing roof sections were renovated with 60mm of Gutex woodfibre board under the roof tiles
Other factors put the house at a disadvantage too — it has a large exposed surface area relative to its volume, and the orientation isn't ideal either. Overall the house's energy consumption, as calculated by the Passive House Planning Package (PHPP), is 17.9 kWh/m2/yr — superb u for a refurb, but outside the Passive House Institute requirement of 15 Kwh/m2/yr.
“There’s a huge amount of exposed surface area relative to volume,” says Archie O’Donnell, energy consultant on the project. The passive house standard calculates heat demand per unit of floor area — the more exposed surface relative to that, the higher the heat demand will be.
Archie says it’ll be difficult to improve the airtightness further. “A lot of that is down to the shape factor, and the fact it’s a renovation,” he says. “In general if you go for passive you need to have about a 10% margin of error because things change on site.”
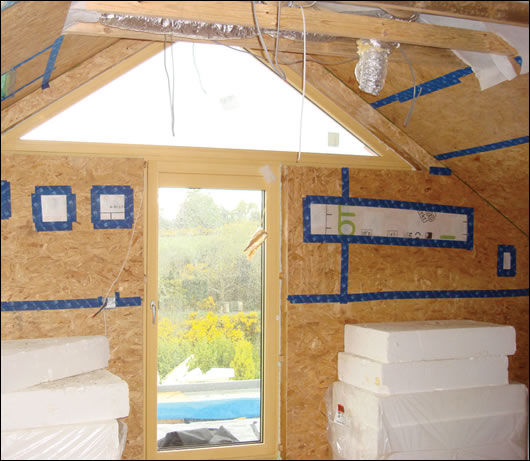
Pro Clima Intello membrane is used to seal the holes
But O’Donnell points out that the essential aim of the passive house standard is to deliver an energy efficient, comfortable house with good air quality — getting close is usually enough to achieve those goals, even if the exact standard isn’t reached.
“They just saw it as a challenge and they wanted to aim for passive,” O’Donnell says of Randy and Mel. “I think they wanted to push the boundaries…they’re quite tenacious, if you put a challenge in front of them they will want to excel in that.”
For Randy, failing to meet the passive house standard was evidence that it’s unrealistic for renovation. "To my knowledge, there are only two or three other residential renovations in the entire world that have met this standard,” he says. “What good is a standard that cannot be met? It would be of much more benefit to the planet and global society to set achievable standards with regard to the energy efficiency of buildings, particularly renovations.”
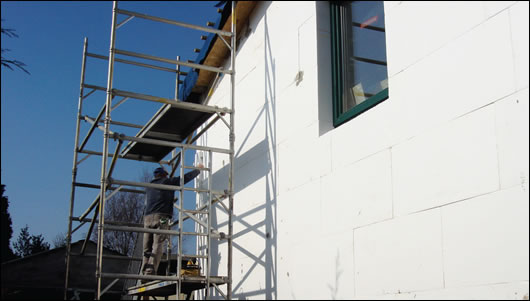
The whole house was insulated externally with EPS
Renewable power
Of course the couple’s ambitions went far beyond the building envelope, and the house is largely heated and powered by renewables. A wind turbine and a solar PV array provide much of its electricity.
Energy consultant Archie O’Donnell analysed the feasibility of the site for both wind and PV using a software programme called Retscreen. “The results were inconclusive as to the financial feasibility of solar PV and micro wind,” O’Donnell’s report says. “But the sensitivity analysis tools were able to give us assurance that the installation would at least be cost neutral over the installation lifetime. This eliminated the risk to the homeowners, whose reasons for installing the technologies went beyond financial considerations.”
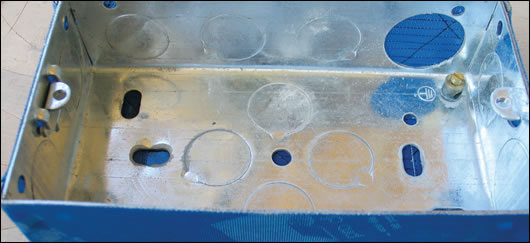
An electrics box wrapped with airtightness membrane
Coolpower supplied the PV panels for the house. The array features 14 Sanyo HIT PV panels — about 2.9kW in total. Coolpower's Tim Cooper explains that HIT panels consist of thin monocrystalline wafer cells with additional ultra-thin amorphous PV technology between cells in areas that would otherwise be empty, maximising the area of the panels that generate power. This allows the panels to capture the scattered indirect light that is abundant in Ireland’s many overcast, cloudy days.
He says that Randy and Mel’s project was ideal as Coolpower was brought in to design the PV system from the start, rather than retrofitting it after the fact. "They clearly wanted the best system we could provide them with at the time," Cooper says of the couple.
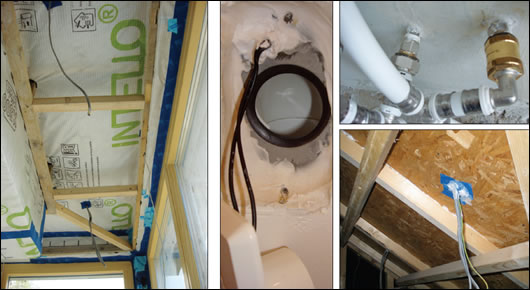
(left to right) Pro Clima tapes and Intello membrane in the flat roof of the new open plan kitchen/dining area; a portal for the BEAM central vacuum system with mastic sealing; piping penetrations sealed with mastic; electrical wire penetrations sealed with airitghtness tape and mastic (bottom)
Coolpower also installed their Emma (Energy and Microgenerator Manager) device at the house. A small unit that sits alongside the existing ESB meter, Emma’s basic function is to automatically adjust the amount of power delivered to heating and cooling devices such as electric immersion heaters, underfloor heating systems, electric storage heaters, electric space heaters, kettles, fridges, freezers and battery chargers. It was designed before the introduction of feed-in tariffs here, when excess electricity produced by microgenerators would otherwise have been exported to the u grid for no financial return — Emma allowed users to direct it to storage devices to make use of the power instead.
The technology enables microgenerators to prioritise where their power goes — for example, whether it goes to an immersion, an electric space heater, a heat pump, other storage device or to the grid. If dynamic tariffs that change frequently based on demand are introduced in future as expected, Emma will allow users to store or export excess electricity based on real-time prices.
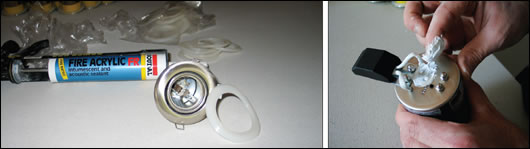
For maximum airtightness, downlighters were sealed with both rubber seals (left) and mastic (right)
"The aspect of Emma control that is creating the most interest at the moment is its ability to control electric import, export where microgenerators are installed, and thermal storage in a very large number of residential buildings in real time," Cooper says. "This provides network operators with the ability to match demand to output in real time and to store surplus energy in thermal storage devices close to or at the point of demand. This makes it possible to greatly increase the number of and capacity of microgenerators connected to the grid without the need to upgrade existing networks. We’re selling most of our Emma units overseas at the moment because of restrictions applying to microgeneration in Ireland. The recent decision by ESB to increase the permitted size of domestic micro-generators to 50kW is expected to result in increased sales of Emma technology in Ireland."
"The current [Emma units] are really nice because they give you more sophisticated control over the temperature of hot water," Cooper adds. This extra control means water can be a heated to just the right temperature, and in the right location in the house, to maximise efficiency.
Waterford-based Sunstream Energy supplied Randy and Mel’s wind turbine, a Skystream 3.7, which is manufactured in the US by Southwest Windpower. The turbine is rated at 2.4 KW in wind speeds of 12 metres per second (m/s), which is equivalent to 27mph. With no battery, it’s designed to connect directly into a household distribution board and operates automatically, with its output either consumed by the household or exported to the national grid. Up to 19c per kWh is currently available for microgeneration. “ESB Customer Supply pays 9 cents per kWh for exported electricity in single annual payments, which is less than the 14 cents per kWh they are currently charging customers,” Randy explains. “There is an additional 10 cents per kWh incentive paid by ESB Networks to members of the microgeneration scheme – however this is only for the first 3,000 kWh exported annually and is valid only for five years. In October the ESB is going to raise the rate it charges its customers for electricity, but the amount it pays to microgenerators will not rise.”
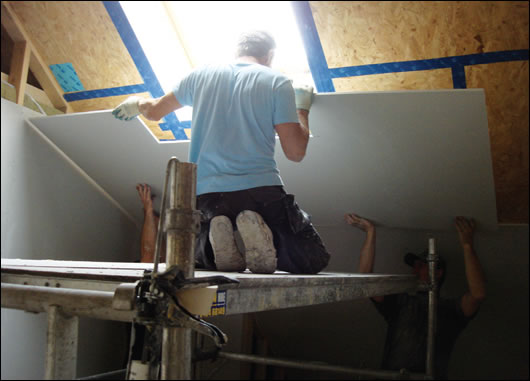
The inside of the build-up being finished with Fermacell board
The turbine starts producing electricity at a wind speed of 3.5 m/s (8mph), with full output achieved at 12 m/s (27mph). “It is designed and certified to operate for 20 years with minimal maintenance requirements,” says Sunstream Energy’s Gene Hourihane. He says the turbine should produce between 2,500 and 5,000 kWh per annum on suitable sites — equivalent to displacing up to 60 tonnes of CO2 per annum.
“Our ESB smart meter only got installed about six months ago,” Randy says. ”Before that, the grid received whatever excess we generated for free. It's sad that the Irish government has set such a low standard of payment compensation for microgenerators like ourselves. A high rate of payment for microgeneration would encourage many more people to adopt renewables and quickly bring Ireland into a strong position regarding CO2 emission targets. It would also send a message to the world that we are serious about the environment.”
Heating design
The solar PV and turbine will help power a heat pump, one of the house’s main heat sources. The Emmeti air-to-water heat pump has a COP of up to 4.49 based on Eurovent conditions (water temperature 30/35C, air temperature 7/6C). "If the temperature of the tank drops below the set flow temperature, which is weather compensated, the heat pump will get called on,” explains Cormac McHugh of C-MC Energy, who supplied most of the heating equipment in the house. But the heat pump is essentially a backup. “The heat pump is something that shouldn’t be frequently called upon according to their system design,” McHugh says.
Solar thermal features too — an array of 120 solar evacuated tubes, comprising approximately 20 metres squared. "It's designed to take care of 70% of domestic hot water requirements along with considerable underfloor heating contribution," McHugh adds.
Both the solar thermal panels and the heat pump heat water in an Akvaterm 2000 litre hot water tank, also supplied by C-MC Energy. “This was a bespoke tank manufactured specifically for this job,” McHugh says. “The tank will harness energy from solar thermal, heat pump, and excess energy from the PV and the wind turbine, distributing this energy to the domestic hot water and underfloor heating.”
The tank is insulated with 100mm of high density polyurethane high density foam, with a U-value of 0.22 W/m2K and a heat loss factor of less than one degree in 24hours, McHugh says. It has three coils — one vertical coil in the lower section of the tank for solar thermal energy, plus one vertical coil in the lower section and one horizontal in the upper section for heat on demand domestic hot water. McHugh says all coils are rated at 90kW. The tank also features a baffle plate internally to optimise stratification.
“We have one controller for the complete system, controlling the solar thermal, the heat pump and the weather compensation for underfloor heating, thus optimising performance of all individual components,” McHugh says. “The controller can be accessed online remotely, and can data log the performance of individual components.”
“The heat requirements on that house should be minimal, as this is the reason for building to passive standards,” he adds. ‘We worked with Randy and Mel to supply components that will u easily and efficiently satisfy this requirement with minimal running costs.”
Each room in the house has a separate underfloor heating loop, and there’s a thermostat in each room too, as well as a master control for the whole house, all allowing for control over each room. The couple also installed a Supra airtight wood burning stove, but they haven’t used it yet — they’re worried it could overheat the house.
There’s no backup boiler though. ”The traditionalists had no confidence at all in what we were doing,” Randy says. “I can't tell you how many 'experts' we talked to who insisted we were crazy not to have to have a boiler as a 'back up' in case the renewables didn't work as we planned.”
But the early signs are that the system is performing. “We went through one of the coldest winters on record, with deep snow all around – in fantastic comfort. But because all the different systems were not fully integrated and tuned until recently, we won't know the actual performance for another year or two. But so far, it's looking very good.”
But there is one small caveat. "We sized the evacuated tube array so that we would have enough radiant heat for most of the winter," Randy says. "While this works as intended, we regret having so much surplus hot water in the summer. The array shuts down before 10am because it's already at temperature. It seems wasteful and we wish there was something productive that could be done with the excess."
The house also features an MTD ERV 500 heat recovery ventilation system, with a heat exchange efficiency of up to 85% according to the independent SAP Appendix Q database. Randy and Mel chose to install a Beam central vacuum system too.
Rainwater harvesting
They also specified a Wisy rainwater harvesting system, supplied by Rainharvesting Ireland. The rainwater is first filtered by a vortex filter that removes leaf debris and other large particles. The second stage is settlement in the rainwater tank, where heavy particles sink to the bottom and lighter organic matter floats on top. Heavier particles accumulate at around 1 to 2mm per year to form a "beneficial biological layer", explains Rainharvesting Ireland’s Johnny Coyle. A multisiphon overflow unit is designed to skim floating particles from the surface when the tank overflows.
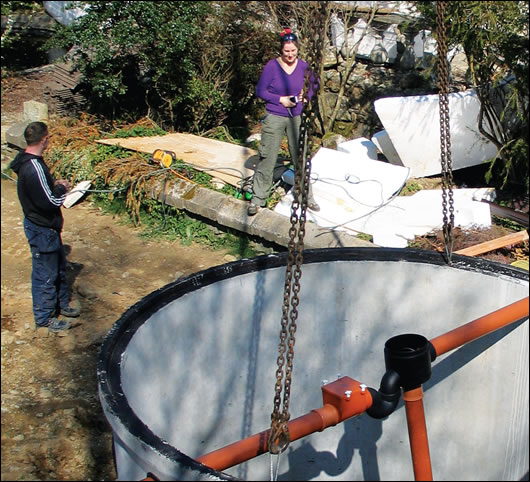
The Wisy rainwater harvesting tank was installed underground at the site
Water is extracted from the cleanest part of the tank, just below the surface, with a floating filter — this ensures the water is filtered to 220 microns before entering the pump, helping to protect the pump and clean the water at the same time. Water quality is maintained by the removal of organic matter and by the action of incoming water, which introduces oxygen.
Once it's pumped in to the house, water passes through a series of fine cartridge filters that bring it down to five microns. A Wedeco Aquada UV disinfection system then provides final treatment. In total the system provides rainwater to four showers, two baths, five toilets and eight sinks in Randy and Mel’s house, as well as to one cold water connection to the washing machine.
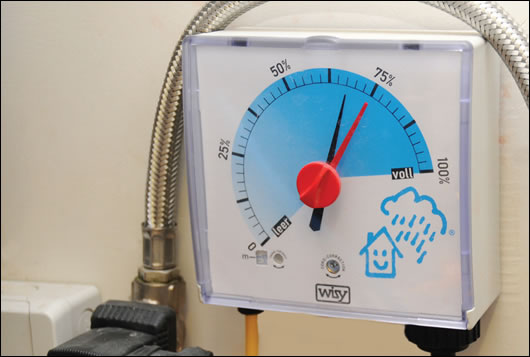
A meter for the Rainwater tank shows how full it is
Lessons learned
Having managed the project with Mel, Randy learned a lot about self-build, and how to build green. ‘We thought we were going to save money by avoiding what seemed at the time like steep architect fees if we just built it ourselves,” he says. “Wrong. An experienced architect's fully detailed construction drawings would have been a very good investment saving us from sometimes having to redo things two or three times to get them right.”
“About halfway through the build we instituted mandatory inter-disciplinary site meetings first thing every morning for everyone who would be working that day,” he continues. “Everything worked better after that. For a project like this, every person needs to understand the bigger vision of what is trying to be achieved and understand how their role fits into it. It's cliché but true that a chain is only as strong as its weakest link and the analogy suits very well for this build.”
His advice for others attempting a serious green building or renovation job? “Use genuinely experienced people with good reputations and personally follow up references thoroughly by interviewing previous clients in detail. The financial dynamics of the property market are different now but some things never change,” he says. He points out that just because the building market has taken a green turn doesn’t mean everyone in it is committed to quality. ”The cowboys are still here only now they're all wearing green hats.”
A provisional BER assessment states the house “achieves in excess of an A1 rating” — and showed it producing more energy than it consumes. The BER result also indicates the dwelling has a negative Carbon Dioxide Emissions Rate (CDER). The couple have changed the spec slightly since then, but Randy says it’s only been improved. They’re planning to have another provisional BER assessment done soon, but they will need to collect a year’s worth of electrical and microgeneration data before the result is finalised. Randy and Mel might not have ended up with a certified passive house, but if the final BER shows their home producing more energy than it consumes, they’ll have got an active one instead.
Randy & Mel can be contacted for advice or consultation at This email address is being protected from spambots. You need JavaScript enabled to view it. or at 087 687 5354.
Selected project details
Clients: Randy Ralston & Mel Cronin
Architectural & passive house consultant: Archie O’Donnell
BER assessment: Energy Matters
M&E: Robert Hassey Electrical Ltd
External insulation: Aerobord
Service cavity insulation: Rockwool
Cavity wall insulation: Warmfill
Blown cellulose insulation: Ecocel
Insulated foundation system: Viking House
Windows & doors: Ecoglaze Ireland
Roof windows: Tradecraft
Airtightness products and Gutex insulation: Ecological Building Systems
OSB board: Medite Smartply
Solar evacuated tubes, air-source heat pump, buffer tank: C-MC Energy
Rainwater harvesting: Rainharvesting Ireland
Wind turbine: Sunstream Energy
Solar PV & Emma controller: Coolpower
Heat recovery ventilation: MTD Solutions
- Articles
- Passive Housing
- Rathrum passive refurb
- Net Energy supplier
- timber frame
- Rockwool
- cellulose insulation
- Internorm
- Intelle Membrame
Related items
-
Up to 11
-
It's a lovely house to live in now
-
We Build Eco flat pack timber frame partnership gathers pace
-
Podcast: what we've learned from 20 years in green building mags
-
Mass timber masterwork
-
AECB conference to showcase timber innovation
-
Heart of oak
-
Welsh social housing to embrace passive house, timber & life cycle assessment
-
Cambridge chooses passive house comfort for Kings’ College students
-
Pitch perfect - Beguiling Dundee passive house puts wood into woodland
-
Above the curve - Limerick passive house showcases precision timber engineering
-
COP26 house to showcase fabric first, low carbon build methods