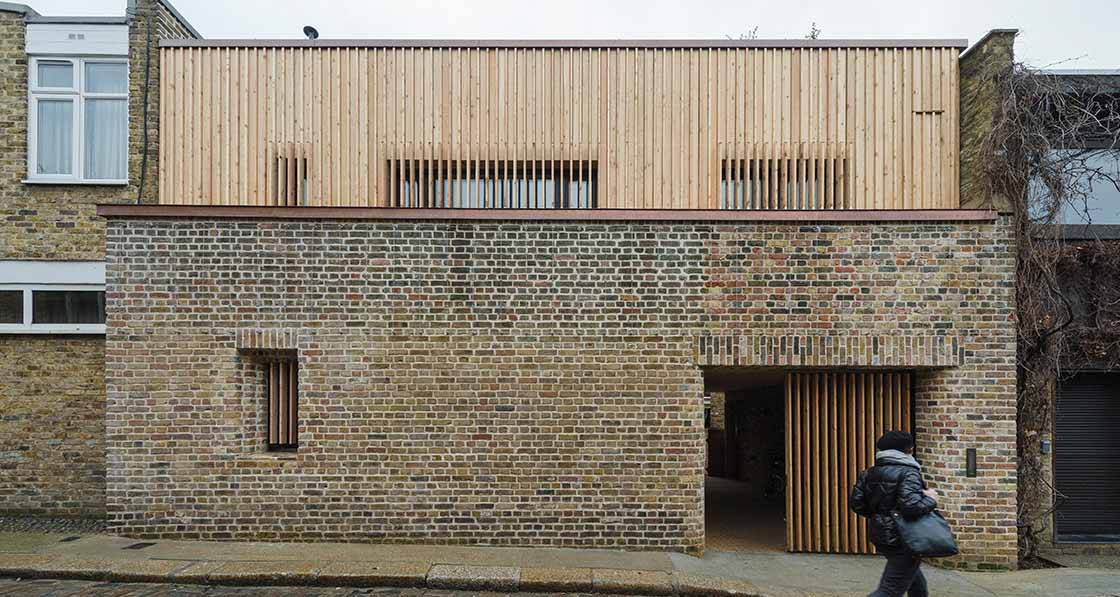
- New build
- Posted
Legendary engineer builds engine-less home
With this stunning, award-winning passive house in Camden, the legendary engineer Max Fordham — together with bere:architects & Bow Tie Construction — has produced a simple and beautiful urban home with no wet heating system that draws on his lifetime of work applying the principles of simplicity, practicality and replicability to the design of building services.
Click here for project specs and suppliers
Building: Infill mews passive house 145 sqm
Completed: February 2019
Location: Camden, London
Standard: Passive house (certification pending)
£21.66 per month for space heating costs (estimate)
£23.50 per month for hot water (estimate)
What kind of house would one of Europe’s leading heating engineers build? If you are Max Fordham then you build a passive house, but one that also takes into account decades of both practical engineering work and environmental thinking.
Fordham, who founded Max Fordham LLP in 1966, having worked in engineering since 1958, has been described by CIBSE Journal as “Britain’s most influential services engineer” and is one of the earliest advocates of sustainable building design. At school— the educationally experimental Dartington Hall in Devon — Fordham was on track to become an engineer, but says his interest later began to wane.
“I was interested in physics so that I would learn the science behind engineering, and I was in a school that was an arty school. So then when I went to university I was bored by engineers and interested in architects,” he says.
This was because of a step change in architecture at the time, and one of those who Fordham met was Leslie Martin, one of the architects behind the Royal Festival Hall. “At Cambridge I met the first architect who wasn’t an artist, he was a designer of buildings,” Fordham says of Martin.
Now retired and in his eighties, though still busy, Fordham recently sought to build a new home for himself. Located in Camden Mews in London, the finished house is a three-storey blockwork-built terrace, in-filling between two existing houses. Just before going to print, it picked up two RIBA London Awards, including the sustainability award for 2019.
A certain frugality informs the design: there are no en-suite bathrooms and no heating system, relying instead on heat recovery ventilation. The simplicity of the house’s architecture also reflects Fordham’s own engineering philosophy of keeping things simple and practical.
There is also a clear focus on accessibility: it is possible to live entirely on the ground floor, for example, while cork flooring provides some safety against falls.
Fordham’s house, though not yet certified, is a passive house. This is interesting because Fordham has in the past been seen as a critic of the passive house standard. But he says that coming to the principles that informed his own house followed a logical process.
“David Levitt [the architect] and I combined to design a little block of around 50 flats that we thought would be pretty efficient, but before you know where you are you find yourself designing for a low ventilation rate so that the heat loss is minimised—and the insulation of components is more or less straightforward,” he says.
“But making it airtight is not straightforward and so you are trying to design a building where the ventilation needs to be limited. Then you have to have a mechanical ventilation system with heat recovery.”
This was the Caspar (City-centre Apartments for Single People at Affordable Rents) development in Leeds for the Joseph Rowntree Housing Trust, finished in 2000, and it was not a happy experience, though for structural reasons rather than anything energy-related.
A report by structural engineers Arup later found that the building — constructed with a prefabricated system from Japan — had a two per cent chance of collapsing in exceptionally high winds, and it was ultimately evacuated and demolished.
But Fordham’s approach of increased airtightness, adding mechanical heat recovery ventilation and attempting to eliminate the need for heating — principles at the very heart of the passive house standard — was vindicated through experience. And despite the structural issues at Caspar, the project did provide data and reported experience from occupants.
“We had three years’ worth of fuel bills in 50 flats, so there was a decent statistical group showing that, basically, the buildings needed no heat,” says Fordham.
“The heat loss from the flats on a freezing, overcast day was 300 watts. But then the electric use for the refrigeration and all the things that electricity does for the industrial revolution, all of those things, communications, cooking, are producing 300 watts. That’s the electricity bill for the flats. Then when you add to that that people go to sleep at night: two people sleeping for eight hours at night produce another 100 watts.”
“That, I think is a recipe for making housing…that doesn’t need any [space] heating at all. These would help to decarbonise the nation,” he says.
According to Fordham, ventilation—a lack of understanding of it and crude techniques resulting in overventilation—are the source of the worst excesses of the building industry.
Bow Tie Construction built mechanised test versions of the shutters using Lego.
“Ventilation is certainly the big problem in the industry,” he says. “In particular, once you’ve solved the ventilation problem you’ve got a building that doesn’t really need any heating. What’s happening a lot with passive houses we’re seeing built is that people are demanding things like underfloor heating.”
Fordham believes there is a reluctance to challenge the idea that space heating is an essential component of any house.
“I think it’s a conservatism: people are afraid, but it’s [passive house] then being adopted and people are adding underfloor heating to the brief. That’s the worst kind of heating to have, in a way, because if you have a thermally heavy [passive] building it doesn’t actually need any heating. So, if you don’t need any heating, you’d better not put in a heating system that is difficult to control and slow to control. It may look very luxurious and nice, but you can’t really turn it off. It’s just wasting heat.”
Fordham’s own house, he says, proves the point: with a properly designed and built house, a conventional space heating system is no longer required. He hopes that this becomes more widely understood. “I hope we can get this message out to one-off builders, to councils and to the Barratt Homes of this world,” he says.
1 The Isoquick insulated raft foundation system helps to eliminate any thermal bridges; 2 50% GGBS in the concrete helped to reduce CO2 emissions in the floor slab; 3 construction of new lightweight concrete block walls just inside the neighbouring party wall; 4 to keep the wall construction thinner at the party wall, Kingspan Kooltherm rigid board was used externally for insulation here; 5 however the walls of the main facades were insulated with Steico I-joists packed with Rockwool Flexi mineral wool insulation and 6 finished externally with a Steico black breathable board, which was then clad externally with Austrian larch.
This article was originally published in issue 30 of Passive House Plus magazine. Want immediate access to all back issues and exclusive extra content? Click here to subscribe for as little as €10, or click here to receive the next issue free of charge
Fordham only moved into his own new house in February, so he has not yet experienced a full winter. He is confident, though, that he will not need space heating even in the depths of the season; perhaps just a sweater. (He did use a small 2kW electric heater, however, to heat up the three-bedroom house at the outset, finished, as it was, in winter).
Now, at the time of writing three months later, Fordham is starting to gather information from the house, both in terms of data and his own lived experience.
“I’m just getting some feedback on the energy use. It’s very interesting: the top has the most glass and is getting the heat. It’s very cosy. The ground floor tends to need a little heat so I’ve just written a note that says that we need to increase the internal air flow. “It’s very exciting getting some real feedback,” he says.
Design for life
Alex Whitcroft, co-director at bere:architects, says that working with Fordham there was a clear direction driven by his ideas.
“It was about focussing on this idea of a building metabolism, a balanced system,” he said. “Max is definitely an engineer at heart.”
Fordham’s decision to go with a passive house was not a Damascene conversion so much as his arriving at the logic of the standard through this own thinking, including, crucially, about replicability.
“It’s interesting; one of the most interesting things is that Max is, quite rightly, known to be a critic of passive house. At the same time Max is an environmentalist and an environmental engineer. Like Wolfgang [Feist], he’s very practical about performance and the science,” says Whitcroft.
1 Douglas fir joists to underside of roof with Smartply ProPassiv airtight OSB above; 2 construction of internal studwork with pro clima Intello vapour control membrane behind; 3 Schöck thermally broken connectors used to support 2nd floor planters; 4 construction of the Bauder roofing system with 160mm Bauder PIR insulation under a 3mm bitumen layer; 5 installation of the Paul Novus heat recovery ventilation system and 6 rigid insulated Lindab ventilation ductwork; 7 & 8 construction and installation of the innovative window shutters, which are both insulated and automated, and designed to prevent unwanted heat loss on winter nights as well as providing solar shading; 9 Max Fordham looking on while builder Rafael Delimata examines the Lego test motor for the shutters.
Fordham has long stressed that the industry should be able to deliver sustainable performance in a way that is simple and replicable. “Although this is a one-off home and although it’s on a very difficult site it is not just a one-off exemplar, it’s replicable, and replicable with building materials available in the UK,” Whitcroft says of the block-built house.
Bere’s founder and co-director Justin Bere, one of Britain’s leading passive house designers, had known Fordham for some years, but never worked with him before. Indeed, Fordham was an admirer of an experimental eco house Bere built for himself in the early 2000s, and their conversations set Bere off on a journey that was to change his practice forever.
“At the time Max got in touch I had half built my own house and was really trying to do everything in Brenda and Robert Cale’s ‘autonomous house’ concept. I also worked on a school [that had been] built in 1968 that had really bad air quality, and Max told me I needed heat recovery ventilation. “That…set me off on the journey that led to passive house. Another time in the office he said, ‘What you’re doing, with HRV and triple glazing and so on, is passive house, have you heard of it?’ I said ‘no’ and went over to the conference in Germany and was amazed by what I saw,” says Bere.
“Max then worked on Caspar, which was demolished for structural reasons, but he designed HRV into that. A little bit like Wolfgang Feist, Max was pioneering HRV.”
As for Fordham’s own house, Bere says that it makes some important statements—and not in the sense of showy architecture. “It’s a really important project in terms of making architects, non-passive house architects, move forward. They can’t say ‘Max Fordham wouldn’t design a passive house’ anymore.”
“Throughout his career he has, in his own way, developed his own version of passive house. He was on the same wavelength but didn’t know about it, and in this he brought together what he was doing and what the Passive House Institute was doing, saying: ‘Were both on the same mission to fight for the planet’.”
Fordham was also happy to borrow an idea from Bere’s home.
With a properly designed and built house, space heating is no longer required.
“He loved the technology of the [automated, indoor] shading blinds. That works really brilliantly and my [elderly] mother can use them. I think Max recognised technical and inventive thinking like his own.
“Max’s point was that Georgian houses or Victorian houses have window-wall, window-wall arrangements, and shutters that worked quite well, and we should do an interpretation of that.”
At Fordham’s home the blinds are automated and, uniquely, insulated. They automatically close at dusk in winter to prevent unwanted heat loss but can also be used to block out solar gain in summer and provide privacy. During construction, the team from builders Bow Tie Construction built mechanised test versions of the shutter motors using Lego. They even considered using Lego motors for the final version, but there were concerns about its durability.
Building the future
Site constraints—the mews being very narrow—and the desire to retain a historic street wall dating from 1850 caused practical difficulties during the construction phase, and increased costs.
But the process of building a passive house is always smoothed by having a contractor who understands the concept. Bere and Fordham put the project out to a negotiated tender, which was won by Bow Tie Construction, who specialise in passive house building.
Founded in 2012, Bow Tie has always had a focus on green construction but shifted from a primary focus on materials to a primary focus on passive house design over the years.
“Passive house is a still a challenge,” says managing director Rafael Delimata. “We definitely see a bigger shift in volume of passive houses being sold. Ours have typically been one-offs but it’s very interesting: we’re talking to developers who are interested and trying to educate them.”
The sentiment will no doubt please Fordham. “So [now] we’re looking at volume construction. We’re talking to one gentleman in west London who wants to do a small development and wants to go with passive house due to air quality and noise reduction.”
Asked what he would like to see change in the industry, Delimata says that practical measures can be taken, such as moving toward more negotiated tenders rather than traditional ones, facilitating a more collaborative approach between architects and builders.
Also, he says, expert builders can lead architects. “Yesterday I spoke to an architect who said to me ‘I don’t want to have to learn all this [in advance]. I want you to show me.”
“One really interesting thing that comes to mind is that we try to specialise in passive house but [some] architects look at the costs and see us as too expensive or unapproachable. We’d like to see more co-operation between builders like us and architects.”
Selected project details
Client: Max Fordham
Architects: bere:architects
Passive house consultant: Max Fordham LLP in consultation w/ Passive House Institute
Energy rating assessment: Max Fordham LLP
M&E engineer: Max Fordham LLP
Structural engineer: Price & Myers
Main contractor: Bow Tie Construction
Insulated automated shutters: Bow Tie Construction
External insulation: Rockwool
between Steico fins with Steico Black sheathing board
Party wall insulation: Kingspan
Green Roof: Bauder
Windows & doors: Bayer Schreinerei
Roof windows: Fakro
Airtightness products: pro clima, via Ecological Building Systems
Wood fibre insulation: Natural Building Technologies
OSB board: Smartply
Thermal breaks: Schöck / Foamglas / Forterra
GGBS: Hanson Regen
Steico joists: Ecomerchant
Building boards: Fermacell
Cork flooring: The Cork Flooring Company
Air source heat pump & buffer tank: Daikin
Solar PV: LG
Heat recovery ventilation: Paul, via Green Building Store
Ductwork: Lindab
Controls system: Loxone
External paving: Wienerberger
Airtightness tester: Aldas
In detail
Building type: New 145 sqm infill terrace home
Location: Camden Mews, London
Completion date: February 2019
Budget: Private
Passive house certification: Pending
Space heating demand (PHPP): 13.4 kWh/m2/yr
Heat load (PHPP): 8 kWh/m2/yr
Primary energy demand (PHPP): 105 kWh/m2/yr
Primary energy renewable demand (PHPP): 48 kWh/m2/yr
Hot water demand (PHPP): 14.5 kWh/m2/yr
Heat loss form factor (PHPP): 3.33
Overheating (PHPP): 9% (excludes automated insulated window shutters)
Airtightness (n50 at 50 Pascals): 0.38 ACH
Energy performance certificate (EPC): B 83
Energy bills: Estimated cost of £22.60 per month for space heating & £23.50 per month for hot water based on PHPP energy demand calculations & estimated average UK electricity price of 14p per kWh (exclusive of standing charges).
Thermal bridging: Structure entirely within thermal envelope, except for ground piles & 3 columns in the entrance passage, which are thermally isolated with Foamglas Perinsul & a collar of 400mm insulation respectively. Schöck thermally broken connectors used to support 2nd floor planters. Insulation in warm roofs continuous with insulated parapets. Window frames externally over-insulated. Overall thermal bridging Y-value: 0.27 W/m2K
Ground floor: 11mm click-lock floating cork flooring followed beneath by acoustic floor underlay, self-levelling screed, 50% GGBS in-situ concrete, RIW Structureseal clay sheet with taped joints cast into concrete, 400mm Isoquick XPS insulation, 160mm Cordek Cellcore HX void former, 50mm rough GGBS in-situ concrete blinding. U-value: 0.016 W/m2K
Walls (typical exterior wall): Austrian larch cladding (angled to shed water) followed inside by 25mm ventilated air gap, 22mm Steico Universal black breathable sheathing board, 260mm Rockwool Flexi mineral wool insulated batts between 240mm x 60mm Steico Wall SW60 I-joists, 100mm lightweight concrete blockwork, pro clima Intello vapour control membrane, 100mm NBT Pavatex Pavaflex wood fibre insulation, 100 x 50mm horizontal timber battens, 12.5mm Fermacell wall board, 1mm plaster skim coat, zero VOC paint. U-value: 0.11 W/m2K
Main roof: PV array on mounting system, followed beneath by 80-150mm soil / growing medium seeded with native meadow plants, Terram 1000 geotextile membrane, 40mm Bauder DSE40 reservoir board, Bauder PE separating foil, 5mm Bauder bitumen capping sheet, 3mm Bauder bitumen underlayer, 160mm Bauder PIR insulation, 2.5mm Bauder bitumen vapour barrier, 18mm Structural plywood deck, 12mm Medite SmartPly ProPassiv airtight OSB with all joints taped, 100mm wood fibre insulation between 250x75mm Douglas fir joists, 12.5mm high density Fermacell board. U-value: 0.12 W/m2K
First floor green roof: 80-150mm soil / growing medium planted with native meadow plants followed beneath by Terram 1000 geotextile membrane, 40mm Bauder DSE40 reservoir board, 2 x Bauder Versicell 20 drainage board, Bauder PE separating foil, Bauder bitumen capping sheet, Bauder bitumen underlayer, 240mm Bauder PIR insulation, Bauder bitumen vapour barrier, 200mm GGBS insitu reinforced concrete slab, 15mm render and finish plaster. Windows & external doors: Bayer Ökotherm passive house certified aluminium-clad timber windows. Sealed with Pro Clima Tescon No.1 and Contega tapes. Overall U-value: 0.63 W/m2K
Roof windows: Fakro FTT U8 Thermo passive house certified quadruple glazed skylights. Overall U-value: 0.76 W/m2K Heating system: Electric heater battery in MVHR supply duct for space heating. Daikin Altherma 2-stage air source heat pump with integrated domestic hot water tank, designed to run at about 2pm each day. A two-stage heat pump over the course of a year is more efficient at heating DHW. 2 refrigeration circuits: one goes to the outdoor compressor, one inside. The second circuit takes heat at circa 45C or so and boosts it to 65C.
Ventilation: Paul Novus 300 mechanical ventilation with heat recovery system, passive house certified heat recovery 93%. Rigid Lindab ducting throughout.
Water: All fittings with very low-flow restrictors. All roofs have significant restrictors on the outlets to attenuate rainwater.
Electricity: LG solar PV array with total installed capacity of 5.11kW, estimated annual generation of 4024kW.
Green materials: All concrete 50% GGBS. All timber FSC with chain of custody & European spruce plywood. All finishes zero VOC. Natural & rapidly renewable materials used wherever possible (woodfibre insulation, timber, etc).
Image gallery
-
First floor plan course First floor plan course
-
Ground floor plan course Ground floor plan course
-
Second floor plan course Second floor plan course
-
Sough facade details Sough facade details
-
Isometric south Isometric south
https://mail.passivehouseplus.co.uk/magazine/new-build/legendary-engineer-builds-engine-less-home#sigProId04f18b8768