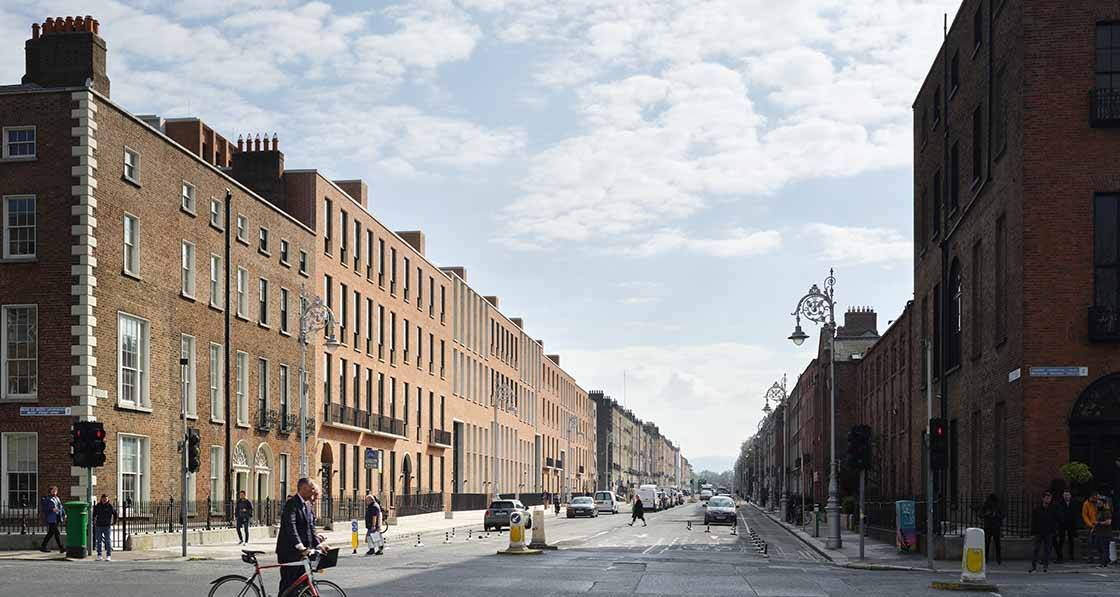
- Feature
- Posted
Adaptation sensation
Sometimes a building comes along that asks challenging questions. Chris Croly, building services engineering director of BDP, describes one such example – a building designed to tackle the specific energy profile of offices, while trialling an innovative, dynamically controlled approach to adaptive comfort.
Click here for project specs and suppliers
Building type: Large office block subdivided into two, totalling 39,000 m2 gross internal area
Key method: Adaptive comfort-based approach to cooling, heating and ventilation
Location: Dublin City
Standard: BREEAM Excellent
Energy use: 83 kWh/m2/yr*
* Total delivered energy use, based on the first five months of monitored usage.
The carbon intensity of electricity in Ireland has reduced by 50 per cent over the last 15 years and is on track to achieve an 80 per cent renewable energy content by 2030.
The Electrical Supply Board (ESB) is a semi state group that has contributed to this achievement. They have set a target of being completely carbon neutral by 2040, investing heavily in renewable generation and associated technology such as energy storage.
As an energy company working within this context, the redevelopment of their offices in Dublin’s Fitzwilliam Street presented an opportunity to invest in the advancement of sustainable office development.
The majority of new offices rely on either a LEED or BREEAM environmental certificate to demonstrate their environmental credentials. While these certificates can give the impression of a building that performs well in all environmental aspects, they often mask a monitored energy performance that differs little from offices constructed decades earlier. Modern office design requires a step change in approach to achieve genuine energy savings.
The Fitzwilliam project contains two next generation office buildings, the first of which is used as the ESB’s headquarter offices, and also serves as a research tool. It provides a treasure trove of new techniques and technologies that have been shown (through subsequent monitoring) to dramatically reduce energy usage in offices.
The second building includes many of the same techniques but is optimised for the commercial market. This was an important aspect of the project as the office market in Dublin invariably offers sealed, air conditioned buildings that struggle to achieve their energy aspirations. There was a need to introduce an alternative precedent and guide the market to low energy solutions.
The commercial office produced offers a new hybrid ventilation strategy that takes advantage of free cooling while offering comfort and air quality levels that exceed that of a typical air conditioned office. The market responded by showing a strong approval of the approach and placed a value on the building that notably exceeded the cost.
Procurement process
This article was originally published in issue 44 of Passive House Plus magazine. Want immediate access to all back issues and exclusive extra content? Click here to subscribe for as little as €15, or click here to receive the next issue free of charge
A design competition was held to select the project architect and their overall approach to the building. The unusual step was taken of appointing the mechanical/electrical and sustainability consultant (BDP) in advance of the architectural appointment to ensure that sustainability formed a key element of the architectural competition. Grafton Architects were appointed in conjunction with O’Mahony Pike Architects with a scheme that had the potential to embrace hybrid ventilation.
While a design and build contract was used for the shell and core of the buildings, BDP were conscious that the design and build process by its nature rarely prioritises environmental innovation. For the commercial block it was also important that a future fit-out would not dilute the services design envisaged. The solution was to fully design the key fabric elements for both blocks and the core services within the commercial block prior to the design and build competition. PJH were then appointed as the design and build contractor to complete the shell and core construction.
The ESB offices were then fitted out by Walls Construction with Jones Engineering Group as services sub-contractors, and Aecom were the fit-out architect. BDP were retained as sustainability and mechanical/ electrical consultant, while also assisting with monitoring the design and build contract to ensure consistency of environmental approach at all stages.
The approach allowed BDP to invest in the buildings as a research project and fully develop the new strategies implemented in both buildings.
Passive design
Traditional office design norms such as the use of fully glazed facades were banned, and each element of design was required to reflect the principles of building physics to reduce the building’s demand for heat, cooling and lighting.
Hybrid ventilation
Modern offices often have a net cooling load throughout the year and external temperatures in Ireland are almost always lower than the internal temperatures required. This means that the tradition of sealing offices from their cooler external environment and then actively cooling them must end.
It can be tempting to think of a naturally ventilated office as the ultimate low energy solution, but the approach doesn’t allow heat recovery and often struggles to produce a comfortable and healthy environment.
A sealed air conditioned office guarantees precise internal conditions but is energy hungry and often produces a sterile environment that ultimately doesn’t deliver on health and comfort.
The new hybrid ventilation approach combined the best of all systems to achieve an enhanced level of air quality and an energy performance that has proven to be better than most naturally ventilated offices.
It was not possible to identify a clear precedent for this approach as tradition frowns on the use of opening windows in fully air conditioned buildings. In part due to a concern that the energy used to cool them will be lost through open windows, air conditioned offices are invariably designed as sealed buildings. This is a valid concern where fixed internal set point temperatures are used but the constraint has been overcome by adopting a new approach to adaptive comfort.
The human response to temperature is complex and adaptation occurs naturally in warmer weather. Following several days of warm weather, people become more comfortable at warmer temperatures and even start to feel cold if the internal temperature is held down artificially.
This building pioneers a new control solution that allows the peak comfort temperature to be influenced by external temperatures that have occurred in previous days and weeks, with a higher weighting given to the most recent weather conditions.
As the resulting internal temperature is almost never below the external temperature, staff are free to intuitively open windows to naturally improve both energy usage and comfort. It is hoped that the demonstration of this control method will offer an invaluable example for future reference.
Early monitoring results have demonstrated that the strategy is very effective and has produced a record breaking monitored cooling energy usage below 4.5 kWh/m2/yr. This figure includes the comms room and specialist facility cooling and the cooling in open plan office areas was close to zero, reaching only 4 W/m2 when external temperatures peaked at 29 C during the summer 2022 heat wave.
The combination of natural and mechanical strategies with a new fan control technique has also reduced fan energy by more than 85 per cent compared with a typical office. Air quality is continuously measured by both CO2 and VOC sensors and excellent air quality has been achieved.
Facade design
LEED and BREEAM certificates often mask a monitored energy performance that differs little from offices constructed decades earlier.
The glazing areas have been adjusted by location, considering the yearly simulations of sunlight falling on each window. In particular, glazing on the upper floors, which are more exposed, have a smaller area.
South and west-facing glazing is provided with solar control while solar gains are encouraged from the north and east. The key south façades are also provided with vertical external shading that is optimised to block solar gains in the afternoon.
Insulation and infiltration
Opaque elements have a U-value in the order of 0.15. The monitored building heating load is so close to zero that any increase in thermal performance would increase the embodied energy of materials used at a higher rate than the savings produced.
In most sealed offices, the level of air leakage achieved has become so small that it unwittingly increases the energy used by reducing natural cooling. It increases cooling loads more than it reduces heating loads.
During the night in winter, when it is important to prevent heat from escaping there is a benefit to having an airtight structure but later in the day, even in very cold weather, offices need to be cooled. Cracking open the high-level motorised windows encourages useful air transfer without causing draughts. This is implemented automatically whenever there is a net cooling load in the building.
Monitored heating energy demand has been less than 7 kWh/m2/yr. and roughly 25 per cent of that energy has been provided by recovering waste heat from cooling processes.
Ventilation
The building is set around a series of planted courtyards with all office areas having access to external spaces, natural light, and ventilation. Because the courtyards are set back from the street, they allow natural ventilation with less traffic noise and improved air quality.
Low level manual openings are provided for staff and motorised openings are provided at high level to reduce draughts and allows warm air out above head height. The automated windows have multiple functions including cracking open in cold weather, opening fully in warm weather, and providing night cooling. The high-level openings can also be manually overridden by staff.
An often-ignored constraint of opening windows is that in warm weather, blinds are pulled over the openings to prevent glare, blocking the free flow of air. Solid window sections were used to prevent this contradiction. The openings are also protected by external shading which takes the form of vertical fins that do not restrict airflow.
Exposed mass
A strip of 1.5 m of exposed mass is used at the perimeter, raising the glazing level and projecting daylight deeper into the plan. Deeper plan areas are reserved for tea stations as they have less need for natural ventilation and daylight. In these spaces an open timber grid ceiling is used. This allows the concrete to be thermally visible while still providing the visual benefits of a ceiling.
During the day, the concrete absorbs heat and at night it is released and removed by natural cooling.
A 70 per cent GGBS content was used in the foundations and 50 per cent for the structure resulting in a reduction of 7,200 tonnes of CO2 (160 kg/m2).
ACTIVE SYSTEMS
Fresh air
Office air is traditionally supplied continuously for all staff, irrespective of how many people are in the building, even to empty meeting rooms and canteens.
In this case fresh air is only supplied at the rate required and reduces automatically as windows are opened. The air control system includes a number of innovations including the lowering of fan pressures in addition to volume with load. This rarely understood technique produces dramatic savings in fan energy, particularly during low load conditions.
Typically, in office buildings, a constant supply air temperature is used at all times which wastes both heat and cooling energy, and fails to take full advantage of free cooling. A number of innovative new control strategies are under test in the offices including a self-learning strategy which adjusts the level of free cooling provided based on the net loads.
Open breakout spaces are used for informal meetings which limits the use of more closely controlled meeting rooms.
Heating and cooling
The building is a zero local pollution building with no fossil fuel connections, even for cooking. The operational carbon impact of the building will approach zero along with the national grid.
Air source heat pumps are used to generate heating, cooling and recover heat when simultaneous loads occur.
Cooling is provided from several sources:
- 100 per cent of the hot water for showers, hand washing, catering etc., is provided by a heat pump that recovers heat from the cooling system, offering cooling as a by-product.
- Free cooling is provided by a 4.8 km closed loop ground collector.
- Cooling is recovered from any live heating demands in the building.
- A phase change store is used to transfer cooling loads to the night when there is less demand on the electrical grid.
The phase change material used for the energy store is an advanced product which is similar to ice but changes phase at 10 C. This product is not in common use and is under test in this building. It has characteristics that differ from ice which are not widely understood.
In winter an office has a net heating load in the morning and a net cooling load in the afternoon. The phase change material stores the cooling potential from the morning for use as free cooling later in the day.
The fan coils used for heating and cooling only have one coil which reduces fan energy. This is achieved by using an innovative six port valve that switches each coil between heating and cooling mode. This technique reduces capital and running costs, and embodied energy.
A glycol free system is used which reduces chemical consumption but also improves the heat transfer properties of the water used.
Environmental assessment methods
During the design process the ESB hosted a workshop with the IGBC to compare BREEAM, LEED and the German DGNB environmental assessment methods. The purpose was to study the different approaches used but also to incorporate the best concepts from each method. An assessor was invited from each organisation to review the building and offer suggestions that could be incorporated into the design. The three methods were very similar, but the DGNB method was the most flexible of the methods reviewed. The method also encouraged the team to consider how the building could be designed for increased adaptability in the future.
The building was formally assessed under the BREEAM method and achieved an Excellent rating, but priority was given to actual environmental performance rather than the certification result in the few cases where conflicts occurred.
Water
A ground water well is used to provide local water for flushing and irrigation.
Monitoring and reporting
There is limited detailed energy data available for modern offices. The ESB offices are fitted with an extensive metering package and BDP are monitoring and tuning the building’s performance and post occupancy evaluation process.
It is hoped that the insights produced by this building will inspire future offices to achieve a step change in energy performance and in particular, it is hoped that it will bring about an end to the age of the sealed, air conditioned office.
ARCHITECT’S STATEMENT:
Grafton Architects
A naturally ventilated office may seem the ultimate low energy solution, but it doesn’t allow heat recovery and often struggles to produce a comfortable, healthy environment.
In 2009 the ESB organised an international design competition to find an architectural team to design a world‐class office building. Grafton Architects & OMP Architects were successful in their entry to create a building that satisfied the needs of the ESB as well as the citizens of Dublin on this important and historic streetscape.
Located at the centre of the Dublin’s Georgian Mile and between the 18th century grandeur of Merrion and Fitzwilliam Squares, the challenge for Grafton Architects was to find a way to create a modern office building that could comfortably sit amongst the restrained elegance of the sur rounding Georgian context.
To begin this process, we set about analysing the built fabric of the Georgian streetscape including its rhythm of windows and doors, its hierarchy of floors, its gently stepping parapet lines, chimneys and threshold of railings bridge and basement, which bring light down to lower level. These elements form the essence of the Georgian streetscape, they represent the fundamental machinery of Georgian architecture. The proposal works within this vocabulary, this language of building, in a contemporary way, to make a building sensitive to its surroundings and representative of its own time.
The new building continues the Georgian streetscape and parapet height of a four‐storey brick wall to Fitzwilliam Street Lower. This edge is crafted with a load bearing, masonry brick wall that has been designed and detailed to harmonise with the existing load bearing brickwork of the street.
The façade to Fitzwilliam St is designed to feel familiar and new at the same time. It feels familiar because it relates to the gracious brick walls of the existing street, which is repetitive and cohesive, where each house is slightly different from the next. It feels new because it is similar but not the same, with new elements subtly introduced to accommodate new uses and new ways of building. The materials used have been carefully chosen to be both sympathetic (brick and Wicklow granite) as well as innovative (thermally broken stepped steel windows).
To James’s Street East, a strong and vibrant streetscape is proposed to provide order and clarity of form. Brick gables face James’s Street East and these blocks open and set back to create courtyards, connections, and sunken gardens spaces. These new forms release a lavish landscape proposal to the street and frame vistas through the scheme from the street.
The design is entwined with a sustainable agenda to deliver a healthy and energy efficient design for its occupants, where a high-quality work environment is provided, delivering flexible and adaptable floor plates, naturally ventilated spaces within a building made with high quality robust materials and workmanship that knits into the city fabric and will stand the test of time.
Fitzwilliam Street facade
The wall to Fitzwilliam Street is composed of two solid brick walls built in a composite manner. The outer wall is a self-supporting brick wall to the street while the inner wall is a loadbearing brick wall that supports the concrete superstructure. A thermally insulated cavity separates these two constructions.
The brick used is a large (240 x 115 x 73 mm) custom made brick from Gillrath brickworks in Germany. This overall construction measures 800 mm in width and rises to approximately 21 metres from the lower lightwell. Both walls are built in Flemish bond with lime bedding and pointing.
The use of load bearing masonry with lime bedding allows for a wall free from mastic filled movement joints. Although building joints are provided every 15 linear metres there are no joints required over the 21 m height of the wall.
The loadbearing structure of brick piers stack from level to level, there are no concrete columns or steel frames embedded in the structure. The slab has exposed concrete coffers bearing onto the brick structure and varies in depth from 150 mm to 250 mm. All elements that require structural support, such as the staggered steel frame windows, granite surrounds, copings and gates are all fixed to the inner brickwork and are cantilevered over the external wall allowing for independent movement between the inner and outer parts of the wall. The windows are finished internally with a solid oak liner which splays to allow additional light from the west.
The windows to Fitzwilliam Street are a thermally broken steel window system. A ventilation flap is incorporated at the step in the window section. The window openings in the outer brick wall are lined with a feathered reveal of lime mortar. Masonry flat arches are used to form the window openings in the wall. Larger openings make use of precast concrete elements built into the wall as loadbearing lintols. Leinster granite is used extensively on the Fitzwilliam Street Façade, for the cills, steps, kerbs, parapets, railing base and colonnade linings. The street side wall of the lower lightwell is lined in glazed bricks to reflect daylight into the lower ground level and courtyards.
Courtyard facades
The courtyard facades are constructed from Techrete precast concrete panels and canopies with a grit blast finish. The panels are composed of white cement concrete with a granite aggregate. There are two different types of grit blast finish, one rougher than the other. In terms of support, the panels at lower lev-els are stacked whereas on the upper floors they are corbelled off the concrete super-structure.
The plan geometry of the panels varies depending on the orientation of the facade, with the south facing facades having deeper fins to assist with solar control. The openness of the panels varies from the roof to lower ground floor, with the solid to glass ratio reducing as the building descends, allowing for additional light penetration to the lower levels.
A high-performance aluminium window system is used throughout the non- Fitzwilliam St facades. The system has a custom profile fin to the front and rear perimeters that act as closers to the cavity on both sides. Each 3 m bay is composed of a large fixed window, a solid side hung vent and an upper BMS actuated top hung vent.
Superstructure
The design and build process by its nature rarely prioritises environmental innovation.
The superstructure of the building - which was the overall winner and building category winner at the 2022 Irish Concrete Society Awards - is an exposed concrete frame with suspended flat slab floors. The use of GGBS was maximised in the project, with 70 per cent GGBS being used in the lower floors and 50 per cent GGBS in the upper floors.
A series of concrete Vierendeel trusses allow for larger overhangs and clear spaces. The column structure charges orientation as the structure descends, allowing for the increase in window dimension and light to the lower levels. At level 04 structural transfer beams accommodate a change in block width at this point from an 18 metres floor depth to 15 metres above. Precast concrete soffits are cast as permanent formwork with cast in lighting and thermally isolated. Chilled slabs are incorporated into all roofs, these are inhabited with various soil depths and biodiverse roof finishes, bees, and solar panels.
Selected project details
Client: ESB - Electrical Supply Board Ireland
Architects: Grafton Architects / O’Mahony Pike Architects
Sustainability consultants: BDP
Conservation architects: Shaffrey Associate Architects
Structural/civil engineers: O’Connor Sutton Cronin
Landscape architects: Bernard Seymour Landscape Architects
Mechanical/electrical consultants: BDP / Axiseng
Quantity surveyors: Linesight
Planning consultants: Tom Phillips & Associates
Fire consultants: MSA
Acoustic consultants: AWN Consulting Ltd
Façade consultants: Buro Happold
DAC consultants: Maurice Johnson & Partners
Project management: Lafferty
Health and safety: Arup
Ecology: Scott Cawley Ltd.
Main contractor: PJ Hegarty & Sons
Mechanical contractor: Leo Lynch
Electrical contractor: Designer Group
Airtightness testers: Building Envelope Technologies
Thermal bridging modelling: Passivate
BREEAM (D&B): Eslar
Precast subcontractor: Techrete IRL
Windows subcontractor: Gunn Lennon Fabrications
Brick supplier: Janinhoff Klinker Manufaktur / Gillrath Ziegel & Klinkerwerk GmbH & Co. KG
Steel window fabricator/supplier: MHB / The KCC Group
Granite Supplier: RyanStone
Metalwork: OMC Technologies Ltd
Specialist pointing Contractor: Oldstone Conservation Ltd
Superstructure concrete frame: Admore Group
Landscaping subcontractor: Peter O’Brien & Sons Landscaping Ltd
Roof: Crown Roofing Limited / Bauder Flat Roofs
Automatic opening vents: Alucraft Ltd t/a William Cox
Tiles: Aston Crean Ireland
Fire doors and timber panels: Burke Joinery Limited
Partitions: Castle Group
Lifts: Kone (Ireland) Ltd
Precast Stairs: O’Reilly Concrete
Terrazzo: P J Ryan Terrazzo & Mosaic Spe
Screed: Floor Screed Ireland
Insulation: U-Value Insulation
Green roof: Crown Roofing Ltd
Architects and quantity surveyors: Aecom
Sustainability and BREEAM consultants: BDP
Mechanical/electrical and civil/ structural consultants: BDP
Audio visual: Hamilton Robson
Project management: Lafferty
Catering: QA design
Main contractor: Walls
Mechanical/electrical contractor: Jones Engineering Group
Air handling units: Systemair (ESB side) and Flakt Woods (Block A)
Air source heat pumps: Daikin (ESB side) and EICL (Block A)
Zero GWP transfer heat pump: Daikin
Phase change material: (Crystalair PCM)
Hot water heat pump (water-to water): Climaveneta via Flakt Woods
Grilles and diffusers: Entropic
Low energy kitchen canopies: Entropic (automatic cooking sensors and UV filtration to allow heat recovery)
Underfloor heating: FLV
Window actuators: Smoke Management Systems Ltd
6 port valves: Belemo Automation
Meeting room heat recovery unit: Flakt Woods
Fan coils (very low fan power units – also unusual as designed for single coils): Versatile.
-
The ground floor The ground floor
-
The third floor The third floor
-
The fifth floor The fifth floor
-
The roof top The roof top
-
A mass model of the building A mass model of the building
https://mail.passivehouseplus.co.uk/magazine/feature/adaptation-sensation#sigProId9192f2e2dd
In detail
Building type: Large office block subdivided into two distinct offices, with a 22,343 m2 gross internal area block occupied by the ESB, and a 16,577 m2 commercial block.
Location: Fitzwilliam Street, Dublin
Completion date: February 2022
Budget: Approx. €150 m.
Environmental assessment method: BREEAM Excellent
The LEED, WELL and DNGB methods were also used to inform the design. The building was used as a case study as part of an IGBC study of assessment methods.
Space heating demand: 7.7 kWh/m2/yr by detailed dynamic thermal simulation. Initial monitoring results imply the figure is realistic. Note that the majority of this heat is provided by recovered heat.
Heat load: 15 W/m2 by detailed dynamic thermal simulation. Initial monitoring results imply the figure is realistic.
Primary energy demand: 67.7 kWh/m2/yr using SBEM.
150 kWh/m2/yr using dynamic simulations. The building operates 24/7, 365 days per year, and contains some functions that are not directly related to the building so typical office benchmarks must be used with caution.
It is too early for monitoring results to give an accurate indication of performance, but initial usage implies a value between the figures above.
Overheating: 0 per cent overheating from dynamic simulations.
The building embraces adaptive comfort and internal temperature limits are a complex function of external temperature. The traditional overheating criteria do not apply and a new dynamic, adaptive response is used.
The building is capable of achieving a set internal temperature, but it is allowed to adapt dynamically in the interest of both reducing energy and improving comfort.
Number of occupants: The ESB building can support up to 1,650 staff but actual numbers will typically be lower.
Energy performance coefficient (EPC): 0.83
Carbon performance coefficient (CPC): 0.84
Note that SBEM is not capable of considering many of the energy saving techniques used so the results from SBEM have limited meaning. The above EPC and CPC figures are relative to the 2017 version of Part L where the building was only required to comply with the previous version due to the date at which planning was achieved. It was however important to exceed the requirement of future Building Regulations at the time of design.
BER: A3 67.7 kWh/m2/yr.
Measured energy consumption: The operating time has not been long enough to establish accurate energy usage metrics.
At this stage data is only available for five months. The data implies a usage of approximately 83 kWh/m2/yr.
Airtightness: 2.5 m3/m2/yr
Thermal bridging: Passivate were employed to calculate thermal bridging results for all key details.
Energy bills (measured or estimated): No bills available.
Ground floor: Piled foundation with a U-value of 0.15 W/m2K. As there is a basement car park the ridged insulation is applied to the underside of the soffit. The ground slab and foundations contained 70 per cent GGBS.
Walls: A mix of walls is used from the solid brick historic façade to the precast concrete walls (with 50 per cent GGBS). The average wall U-value was in the order of 0.15 W/m2K
Roof: Concrete slab (50 per cent GGBS) with ridged insulation to 0.16 W/m2K
Windows: A mix of windows with an average U-value of 1.2 W/m2K.
Consideration was given to the use of triple glazing and it was shown that using it would result in a net increase in energy usage both from an embodied energy and a cooling perspective. The heating energy requirement is close to zero with the current design and that heat comes almost entirely from recovered cooling so there is no heat to save.
Heating system: A complex system of heat pumps. A Turbocor transfer heat pump is used to transfer loads between cooling and heating sides and an air source heat pump us used for net loads. The transfer heat pump can also operate in ground source mode. Hot water is provided by a water-to-water heat pump that recovers heat from cooling loads.
Ventilation: Hybrid ventilation. The main units are provided by Systemair in Block B and Flakt in Block A. The units are set up in an innovative variable volume variable pressure mode. The heat recovery wheel is a total recovery wheel (it can recover moisture in winter).
Water: Low flow fittings throughout including showers with a flow of less than 8l/min. Waterless urinals. Ground water and rainwater recovery.
Electricity: 30 kW PV system.
Green materials: 70 per cent GGBS in the foundations and 50 per cent in the structure. A full life cycle assessment was carried out on the fit out which would be one of the first office projects to use the method.